Manufacturing Process Audits: Benefits, FAQs and Improvement Strategies
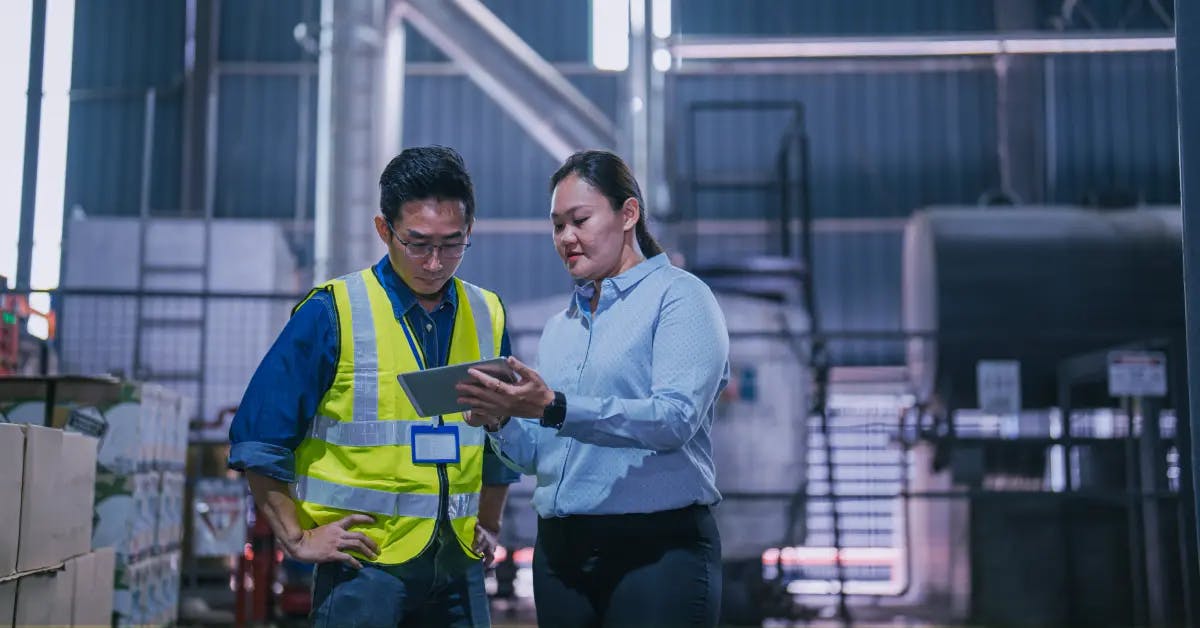
They say that what you don’t know can’t hurt you, but in manufacturing, it’s the very things you don’t see that can cause the biggest problems.
Like when an operator fails to affix bolts on a vehicle assembly with the right torque, leading to a breakdown in the field. Or when you experience reduced machine cycle time due to degraded tooling condition that impacts overall equipment effectiveness (OEE), resulting in lost productivity.
These scenarios highlight the fundamental role of manufacturing process audits in maintaining standards to ensure quality and process reliability. This article explores the basics of manufacturing process audits, including:
- The difference between product audits and process audits
- Why process audits are critical to quality
- How to create process audit checklists for effective quality control and to ensure adherence to each special process.
- How to get more from process audits with layered auditing and digital apps
Download a free eBook on Cost of Quality: The Hidden Truth About Your Ultimate Quality Metric
What Are Manufacturing Process Audits?
Process audits are used to verify that standardized work is being followed, systematically reducing risk by verifying key process inputs such as:
- Whether operators are following work instructions
- Machine settings and condition
- Effectiveness of process controls such as work instructions and error-proofing devices
- Conformance to safety protocols
- Measurement techniques and tools, such as gauge calibration
By identifying process non-conformances, manufacturers can proactively identify sources of variation and implement corrective action before it causes defects.
Product Audits vs. Process Audits
Product audits and process audits are both integral parts of the quality process, however, they differ in their scope, aim and output:
- Process audits focus on manufacturing inputs, while product audits focus on the characteristics of completed products
- Process audits look at how things are done, whereas product audits look at what is produced
- Process audits prevent defects, while product audits only detect existing defects
In essence, process audits look upstream from the point of manufacture to ensure the process itself is stable and consistent. Conversely, product audits are rear-facing, verifying that products that have already been manufactured meet established quality criteria.
However, as we’ll see below, product audits alone only verify this on a surface level, leaving manufacturers open to quality risks that can have serious implications.
Benefits of Manufacturing Process Audits
Process audits act as a backstop for ensuring processes are running as intended, which helps avoid hidden factory issues that drive up quality costs, defects and compliance issues. Below we explore some of the top benefits of process audits in more detail, from defect prevention to improving quality culture.
Preventing Defects Upstream
Process audits are vital to quality because they prevent defects at the source, as opposed to relying on final inspection to catch defects. This is important because oftentimes, inspection can’t always detect a defect, such as if a product component hasn’t been heated to the right temperature.
For example, a process audit might include a question to verify that operators heat a specific product component to 120 degrees. Looking at the heating device, you might discover it’s only configured to 110 degrees—an error that might not be noticed at all until the part fails in the field.
Variation in manufacturing processes is a top cause of product defects. Process audits are designed to identify that variation, bringing the process under control to deliver a safer, more consistent product.
Facilitating Root Cause Analysis
Process audits provide valuable data to inform root cause analysis and accelerate problem-solving. Then, the audit reports inform manufacturing quality control about opportunities for improvement and adherence to standards. For instance, let’s say your plant has seen an increased rate of scrap in recent months, and you want to investigate.
Process audits can help identify work cells that have recently demonstrated a high rate of process failures, which could be contributing to higher scrap overall.
Getting Eyes on the Process
Process audits provide a critical opportunity for direct observation of processes, which can reveal issues that wouldn’t be identified otherwise. That’s because data alone doesn’t always provide a complete picture when it comes to identifying quality issues, nor is quality something that can be done just behind a desk.
It’s essential that you also “go to the Gemba,” or the place where work is actually performed.
Imagine you’re performing a process audit and you notice an operator manually bending a tab back on a part, a step not found anywhere on the work instructions. When you ask why, the operator reports that this makes the part fit better.
The problem is that because it’s not captured in the work instructions, this step may not be performed when someone else works at this station. Either there’s an upstream issue that needs to be addressed, or the step needs to be captured on the official work instructions. Either way, this type of insight is only available through direct observation.
Embrace problem solving with our comprehensive guide to root cause analysis!
Reinforcing Standards and Training
Humans are creatures of habit. Anytime standards or requirements change, it’s essential to go back and make sure those changes have been implemented on the plant floor. This ensures people aren’t using workarounds or shortcuts that could cause issues later, or that they haven’t reverted to old methods over time.
Furthermore, process audits allow teams to highlight the most important elements of standards that operators should be aware of. A good checklist question will explain why that element is important, reinforcing the value of adhering to standard operating procedures (SOPs).
Demonstrating Leadership Commitment
If you’re not performing process audits regularly, it sends the message that you’re not really invested in quality control or in ensuring that every process is being followed to avoid rework and ensure customer satisfaction. Compare this to a manufacturing floor where leaders are a visible presence, checking in frequently to observe processes. Which situation demonstrates that leaders actually care about quality?
Process audits show people that you care not just about how they are doing things, but also that:
- Processes and procedures themselves are effective
- Operators have what they need to get the job done right
- The plant floor is safe for work and free of hazards
- Problems are taken seriously and are fixed in a timely manner
When people see their leaders are truly invested in quality and safety, they are more careful about their work. Where leaders aren’t present, people are more likely to think management doesn’t care and are thus more likely to be careless themselves.
Creating a Culture of Quality
Quality culture is defined as a set of shared beliefs, attitudes, and actions relating to quality control, emphasizing the continuous improvement and customer satisfaction emphasis of ISO 9001. So how do process audits play a role in creating a culture of quality?
They make quality a habit by making leaders responsible for performing checks and through operators knowing that management will be checking what they are doing.
The entire team can see that quality is truly valued, and not just something the company is willing to sacrifice for the sake of hitting production quotas.
Process audits engage people in discussions about quality, focusing on why particular steps are important to quality and safety.
When team members see the results, they can see that their efforts have a direct impact on quality, helping ensure buy-in for process audits and other quality initiatives.
All in all, process audits contribute to greater effectiveness and team engagement, so that everyone is pulling in the same direction—and can be proud of the resulting improvements.
Creating Manufacturing Process Audit Checklists
As you start building your manufacturing process audit checklists, one useful place to start is with the 6Ms of process control. The 6Ms are also the focal point of the fishbone or Ishikawa diagram used in manufacturing problem-solving.
The 6Ms represent different categories of process inputs where manufacturers must eliminate variation to keep processes stable. These categories are:
- Man (people): Does the operator follow each step of the procedure as defined in standard work instructions? Are they wearing the required personal protective equipment (PPE)?
- Machine: Are machine settings correct? Is the machine up-to-date on required maintenance?
- Method: Variation in methods shouldn’t occur if you’re using a documented procedure. If you’re producing similar parts for different customers, however, it’s worth verifying that operators are using the correct method.
- Mother nature (environment): Are environmental conditions such as temperature and humidity within standard? If you’re working with polymer pellets, for instance, high humidity can affect the drying process.
- Material: Do materials meet quality standards? For example, you might look at whether certain materials are within their expiration date, or verify certain quality elements of materials from suppliers with a history of problems.
- Measurement: Are measurement tools used as described in the standard? Are measurement tools such as gauges calibrated and in good condition?
Process audit questions can cover both quality and safety standards. Ultimately, standards form the basis for your questions, as without documented standards there is nothing to verify against.
A Simple Strategy for Writing Your Questions
Process audit questions should focus on high-value operations, such as procedure steps that are critical to quality or are associated with previous quality issues. Each question should cover three key elements: what, how and why.
- What: Can the operator explain the process or step? Here your goal is to assess whether the operator understands the process element you’re verifying.
- How: Can the operator demonstrate the process or step as defined in the standard work instructions? This part should include evaluation criteria, citing any relevant standards.
- Why: Can the operator describe why this process or step is important? Asking this question reinforces the value of following SOPs.
If you’re using process audits as part of a layered process audit program, which we discuss later, you’ll want to format these as yes or no questions. This allows you to cover more questions in a short audit format, while also making it easier to quickly spot areas of non-conformance.
Process Audit Question Do’s and Don’ts
As you write your questions, the best practices outlined in the table below will help you get the most value from your process audits.
Do | Don’t |
Be specific | Use subjective terms like “correctly” and “properly” |
Solicit frontline input on key process elements to verify | Leave operators out of the question-writing process |
Create process-specific checklists | Use generic checklists across the plant |
Address process inputs | Examine finished products |
Ask questions that get to the root of whether operators understand and are following standards | Check paperwork, such as by asking if work instructions are posted and forms filled out |
Write questions in plain language | Ask questions that require technical expertise to answer |
The last item is especially important for companies using layered process audits, since auditors may not be experts on the process in question.
Find out what are Layered Process Audits and how they can revolutionize your manufacturing processes!
How Layered Auditing Makes Process Audits More Effective
Layered process audits (LPAs) are a powerful type of process audit that manufacturers have used to achieve significant reductions in defects and quality costs. LPAs support Lean manufacturing principles with ongoing verification of mission-critical processes to foster continuous improvement.
What makes these audits unique is that they involve multiple layers of management in conducting quick, 10-minute checks, allowing plants to:
- Increase the frequency of checks, conducting them daily or even on each shift
- Generate a higher volume of process audit data to better identify trends and risks
- Catch items that might otherwise be missed by involving multiple people in checking the same processes
- Reduce risk by covering a broader range of standards with fast, frequent audits
- Improve quality culture by showing frontline workers that management cares enough to visit the plant floor daily to discuss quality and solicit feedback
Layered Process Audits in Automotive Manufacturing
Layered process audits are a requirement for suppliers to automotive OEMs like General Motors (GM) and Stellantis, and are strongly recommended by others. As part of these manufacturers’ customer-specific requirements (CSRs), suppliers must implement layered process audits to achieve IATF 16949 certification.
The Automotive Industry Action Group (AIAG) CQI-8 Layered Process Audit Guideline details industry standards for creating and sustaining an effective layered process audit program. It is an essential reference and starting point for any automotive manufacturer looking to implement layered process audits, but can also used by manufacturers in other industries.
Limitations of Traditional Audit Methods
Traditional audits using pen-and-paper, Kamishibai boards and spreadsheet tracking present significant limitations for manufacturers looking to maximize the value of their auditing efforts. Chief among these are:
- Poor visibility into process issues: Having to manually enter checklist data creates lag time between audit completion and reporting. This, in turn, delays identification of process issues, trends and root cause analysis.
- Administrative Burden: Scheduling audits, generating checklists and entering findings often means teams spend more time on paperwork than using the data to drive continuous improvement.
- Low Audit Completion Rates: Especially for layered process audits, manual audit tracking often leads to low audit completion rates, allowing quality problems to grow unnoticed.
- Poor Coverage of Standards: Because of the effort required to create and update checklists, teams often use generic checklists across the entire plant. This provides less meaningful data and limits coverage of standards, while also increasing the risk of pencil-whipping.
How to Get More from Process Audits with Digital Apps
Process audit software like EASE can help plants get better results from the time and effort invested in their audit programs. Advantages over manual tracking methods include:
- Simplified administration: Automated scheduling, reminders and management alerts boost completion rates to generate more data to uncover process issues.
- Instant reporting: Sleek mobile apps make it easy to complete audits on a mobile device, with results immediately available so teams can identify and address problems faster.
- Closed-loop issue management: When auditors identify a non-conformance, they can assign tasks to responsible parties with due dates and escalations to speed up the resolution of issues.
- Detailed insights: Dynamic question libraries with customizable tags make it easy to add, rotate and randomize questions for process-specific checklists incorporating multiple question types (e.g., 5S, safety, etc). Conditional questions and custom failure modes also provide more detail on process failures to improve root cause analysis.
- Robust documentation: Process audit software makes it easy to demonstrate compliance with customer requirements, ensure audit readiness and streamline standard certification.
Real-World Results
Leading manufacturers have used digital process audit software to achieve breakthrough results in their process audit programs, for example:
- 50% reduction in quality costs
- 50% reduction in defects
- 73% reduction in internal PPM
The common denominator in all of these success stories was a desire to address inherent inefficiencies of traditional audits—and a commitment to preventing quality escapes.
Product audits are an important part of the quality process, but they only reveal part of the picture. Without process audits to identify non-conformances upstream, you’re only baling water out of a sinking boat, rather than actually plugging the leaks. A digital audit and inspection app can help close the gap, so you can create a closed-loop process that tracks process non-conformances from identification through resolution.