Turning Corrective Actions Into One-Point Lessons: Benefits and Pitfalls
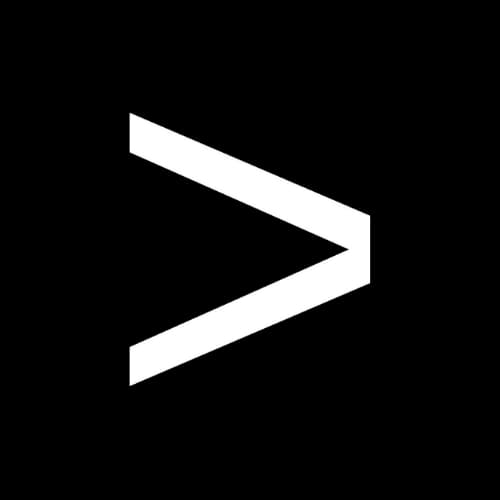
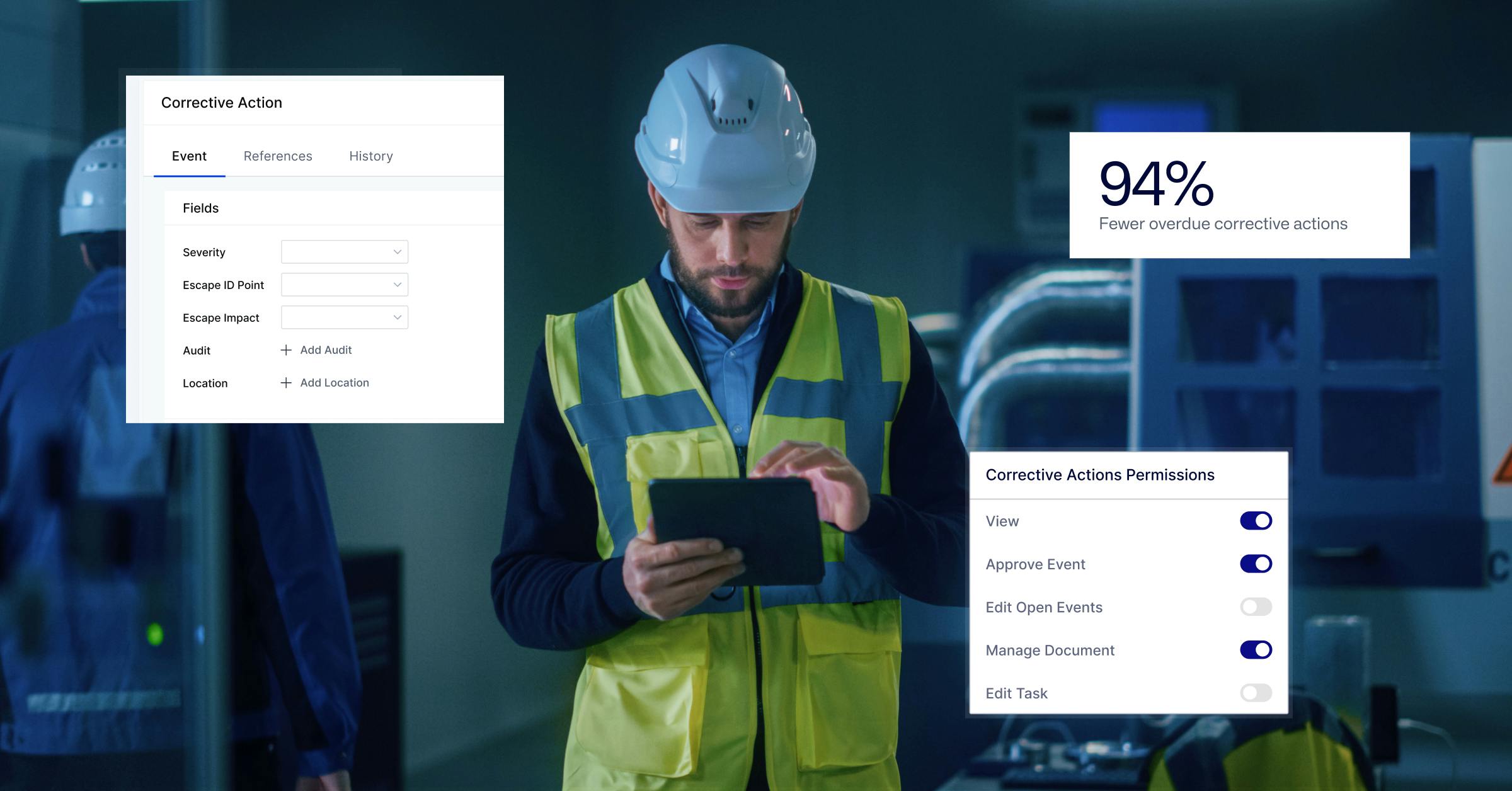
One-point lessons are a Lean tool that provide quick summaries of key learnings that highlight the importance of a specific procedure or work step. Some manufacturers use them to distill the results of corrective action into bite-sized information to promote continuous improvement.
After a workplace safety incident, for instance, a one-point lesson might focus on reminding employees to wear a respirator in a work area where noxious reagents are mixed. While this approach can raise awareness of safety, it doesn’t replace training on how to wear a respirator and what to check to make sure it’s in working condition.
This example underscores the usefulness as well as the limitations of turning corrective actions into one-point lessons. In this article, we explore this in more detail, including the one thing manufacturers really need to ensure corrective actions are held in place.
Download your free Root Cause Analysis 101 Guidebook for an overview of common root cause analysis tools used to drive corrective action
What Are One-Point Lessons?
One-point lessons or one-minute lessons are tools used in manufacturing to call awareness to important safety or quality issues. They summarize the results of problem-solving activities into a short, one-page format with prominent visuals that describe specific operator practices. Teams often use one-point lessons at pre-shift meetings and team lead meetings to share and reinforce lessons learned.
Using Connected Worker Software to Share One-Point Lessons
Connected worker software can be an ideal tool for centralizing one-point lessons and making them available to operators at work stations. Providing on-the-spot access to one-point lessons can be helpful to employees in several situations, for instance as a quick reference when:
- Executing a modified task
- Troubleshooting a process
- Performing autonomous maintenance
What One-Point Lessons Are Not
It’s essential to note that one-point lessons do not replace work instructions or training and competency testing. They typically call awareness to why a practice is important, without providing detailed specifics on how to do it correctly.
For example, let’s say you have a complaint that’s traced back to a failure to measure pH on a certain tank once each shift. The one-minute lesson may say why it’s critical to measure the pH using a specific piece of equipment and report it each shift. Here a one-point lesson can’t replace the need to know:
- How to use the equipment
- How to do the pH testing
- How to interpret the test correctly
Process Changes Demand More than One-Point Lessons
While one-point lessons are most useful for safety and 5S items, they are least effective when it comes to process changes. That’s because process changes tend to be the most complex, making it difficult to cover the most important parts in a one-point or one-minute lesson.
Instead of trying to hold corrective actions in place with one-point lessons, manufacturers should instead focus on preventing backsliding with layered process audits (LPAs).
These daily checks provide frequent reinforcement of process changes, verifying in person that operators know not just why a new procedure is required, but also how, specifically, it must be done. In this way, LPAs also help verify training effectiveness and operator competency.
LPA software makes it easier by allowing plants to:
- Add new questions to digital checklists detailing the what, why and how of process changes
- Add photos to checklist questions so auditors can quickly assess conformance
- Rotate different questions within checklists to ensure periodic checks of corrective action implementation
- Define custom failure modes to better assess the root cause of nonconformances
One-point lessons are a powerful tool for driving awareness of changes that result from corrective action. In weekly meetings, for instance, having leaders prepare one-point lessons on safety is a best practice that does far more to promote a culture of safety than “safety first” slogans.
That said, more rigorous verification is needed for when process changes take place. LPAs provide that higher level of verification, engaging operators in the details of changes to truly hold continuous improvement in place.