3 Quality Tools to Quickly Reduce Defects and Costs
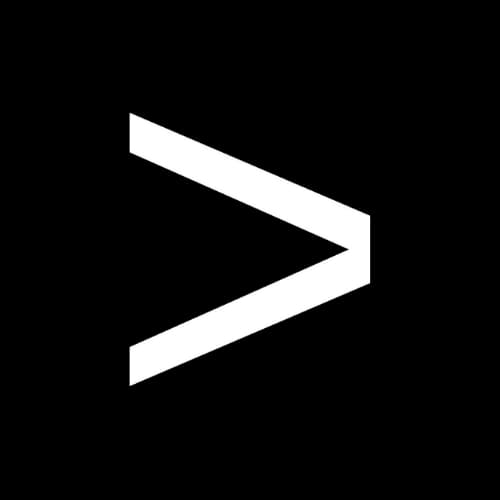
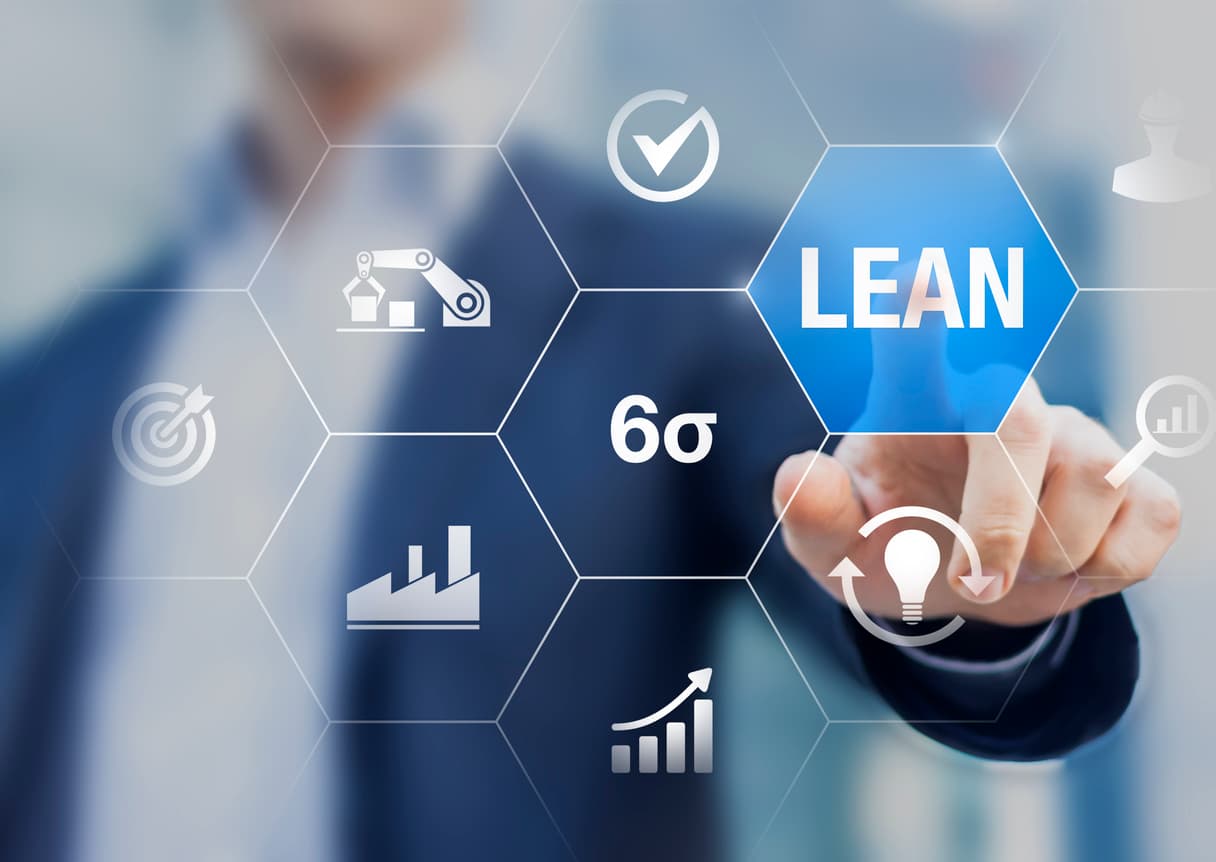
It’s an open secret that many automotive and aerospace manufacturers have unacceptably high defects and costs. And where defects are on the rise, quality costs aren’t far behind.
Even one defect could mean recalling an entire batch, a problem that can cost thousands of dollars per minute if it means a line stoppage for a customer. In extreme cases, a customer’s entire plant might have to shut down, with the full cost billed to you.
So how can you quickly make a dent in defects and costs if you’re looking at a burning platform situation? As you formulate your strategy, consider how Pareto charts, failure modes and effects analysis (FMEA) and high-frequency audits can help you get results faster.
1. Pareto Charts
One of the easiest ways to identify your plant’s biggest problems is with Pareto charts. A classic tool for visualizing the relative significance of various factors, a Pareto chart consists of a bar graph and a line graph. The bars are arranged from left to right in decreasing frequency or cost, with the line corresponding to the cumulative percent represented by each.
Pareto charts get their name from Pareto’s Law, more commonly known as the 80/20 rule, which states that 20% of inputs account for 80% of results. In essence, Pareto charts help you pull out that small set of causes that make up 80% of costs. For example, you might see a disproportionate number of defects in a particular component, department or process, helping you prioritize problem-solving for maximum impact.
The trick is to make sure your buckets are neither too broad nor too narrow. If they are too broad, it’s hard to pinpoint causes. If they’re too narrow, the charts become hard to understand, especially when sharing them with leadership to get buy-in for proposed improvements.
2. Failure Modes and Effects Analysis (FMEA)
The American Society for Quality defines failure modes and effects analysis (FMEA) as “a step-by-step approach for identifying all possible failures in a design, a manufacturing or assembly process, or a product or service.”
If you’re new to FMEAs, they essentially boil down to:
- Listing the possible ways a product or process might fail, and the potential consequences of each failure
- Rating the severity (S), likelihood of occurrence (O) and detection capabilities for existing controls (D)
- Multiplying S x O x D to come up with a risk priority number (RPN), providing a quantitative measure of which risks need attention first
Organizations often use FMEAs during product or process design, then file them away and forget about them. Proactive organizations treat FMEAs as dynamic documents, comparing them against failed products or processes to add new controls and make the tool even more robust. These actions reduce risks upstream of manufacturing, translating into bigger results than simply focusing on detecting or correcting defects.
3. Layered Process Audits
The final tool for reducing defects and costs is high-frequency auditing, a best practice for driving quality improvements. An example would be implementing a layered process audit (LPA) program, which involves all layers of personnel in verifying high-risk processes.
Instead of focusing on finished products, LPAs identify where people aren’t following standardized processes—one of the most common causes of variation and defects. Automotive and aerospace manufacturers have reported drastic reductions in internal PPM, customer complaints and overdue corrective actions as fast as six months after implementing LPAs.
LPAs can be difficult to manage with spreadsheets and paper checklists, taking anywhere from several months to a year to implement depending on the size of the facility. A cloud-based LPA platform can be operational much faster, providing:
- Automated scheduling, reminders and notification of supervisors when audits are overdue
- Instant data analysis and generation of Pareto charts and other reports to enable faster action
- Mobile audit and corrective action tools to eliminate data entry and close the loop on shop floor problems
- The ability to easily add questions based on items like FMEA results and corrective actions, rather than manually recalling and redistributing hard copies of process audit checklists
The fact that all levels of the organization are engaged in audits is a big part of driving LPA results. For automotive and aerospace manufacturers, it helps take quality out of its silo, making quality visible to everyone and laying a foundation for a culture of quality.
It’s important to recognize that quality transformations don’t happen overnight. A manufacturing plant is a large ship to turn around, and it’s a task that takes organization-wide discipline. With the right tools—and leadership making a visible commitment of time and resources—organizations can target faster reductions in defects than might otherwise be possible.
…………………………….
We’re reshaping the world of archaic paper-based processes like layered process audits (LPAs), 5s, HSE, internal audits and corrective actions through our intuitive mobile application, Beacon Quality. Designed to meet the quality and compliance challenges of the automotive and aerospace industries, Beacon Quality is helping manufacturers bring mobility to the shop floor; create a culture of quality, integrity, & transparency; and obtain real-time insights.