3 Signs Your Company Is Ready for a Layered Process Audit Program

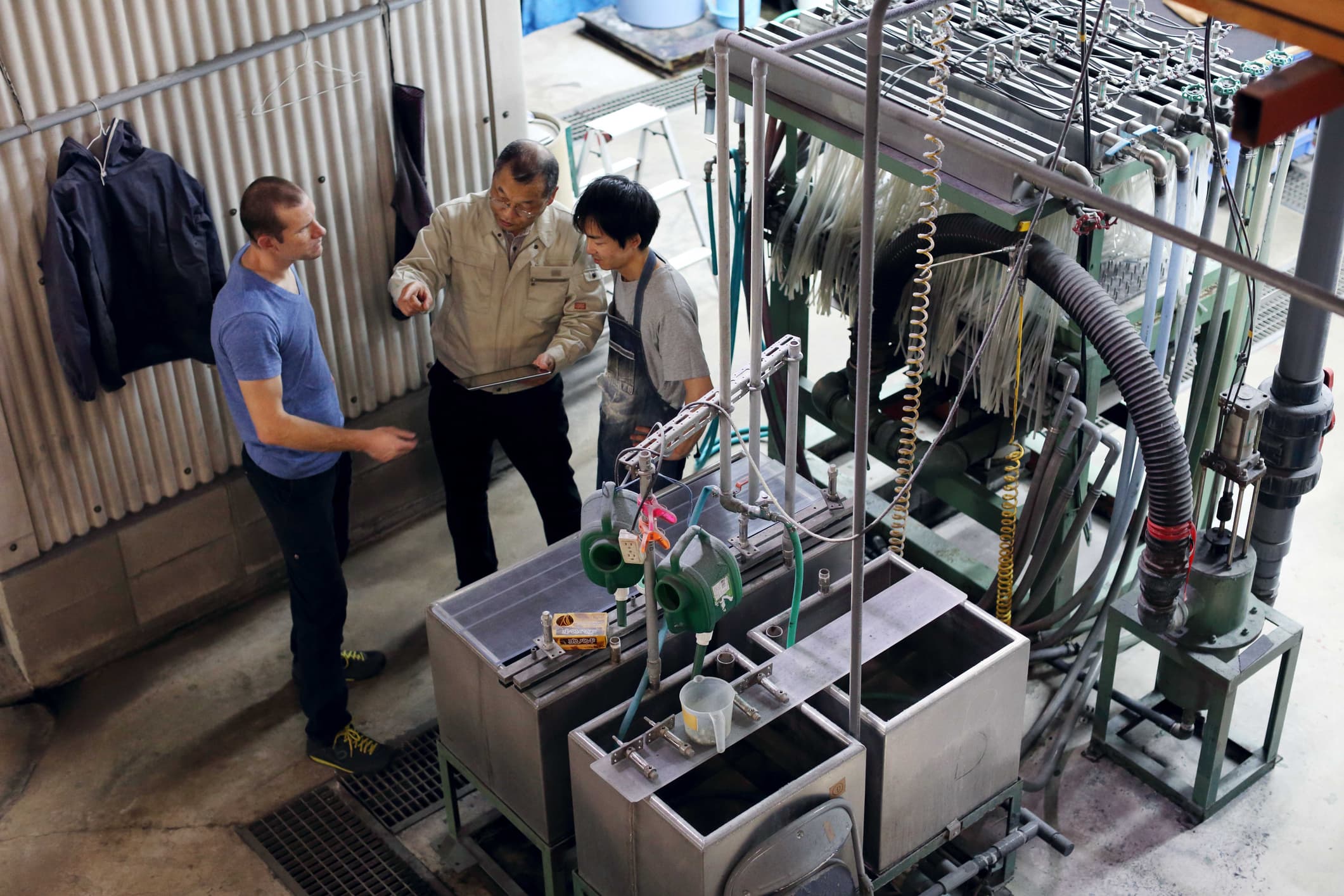
Layered process audits (LPAs) are a powerful strategy for helping auto and aerospace suppliers achieve their quality goals. At the same time, LPAs are also one of the most involved types of audits.
In an LPA program, different layers of the organization participate in daily checks of processes known to impact product quality. These checks catch process errors upstream, reducing variation to minimize scrap, rework and customer returns.
Because of the high frequency of audits, companies often find it difficult to leverage the full potential of LPA programs. How do you know if you’re ready for LPAs? It all depends on your motivation, leadership engagement and a willingness to automate your processes. Let’s look at these elements more in depth.
1. You’re Implementing LPAs for the Right Reasons
One of the most important requirements for implementing an LPA program is the desire to foster a quality culture. Some organizations only do it to satisfy a customer requirement, which ultimately limits their results. Experts estimate over 80% of quality improvement comes from quality culture, making internal motivation essential to getting the most from LPAs.
Even if you’re just starting on your quality journey, implementing an automated LPA system can help you build a culture of quality through:
- Improved communication: LPAs provide daily opportunities for operators and management to share feedback, observations and ideas for improvement.
- Process standardization: LPAs ensure operators are following the same processes every time, which is the key to reducing variation and product defects.
- Leadership engagement: LPAs involve all layers of management, from team leads to executives. Their increased presence on the shop floor provides fresh perspective and lends credibility to your quality efforts.
- Quality ownership: When operators get recognition for their contributions to quality, they are more likely to proactively identify quality issues in the future.
2. Management Is Ready to Jump In
Management buy-in and support are some of the most important elements of a successful LPA program. And it’s not just initial enthusiasm or allocating resources for systems to support your LPA program. These things are important, but leadership must also have the discipline to stay involved throughout the process by:
- Conducting their share of audits according to the audit plan
- Prioritizing the program and regularly reviewing results
- Regularly updating checklist questions based on known problems or high-risk issues identified in process failure modes and effects analysis (PFMEA) reports
- Working to develop leading indicators from LPA programs
By definition, LPAs involve all layers of management and are not something you can simply delegate to the quality manager. LPAs take quality out of its departmental silo, making it a daily focus of all departments.
3. You’re Prepared to Automate Your Processes
If you want your LPAs to work efficiently, you have to be ready to move on from paper checklists and spreadsheet-based audit tracking. LPA programs call for 2,000 or more audits per year for a facility of 100 workers, something that’s difficult to do when you’re relying on manual scheduling and tracking.
From what we’ve seen, organizations that use email, paper checklists and spreadsheets typically complete only about 10% of scheduled audits. Pencil-whipping is a big problem in many of these companies, with auditors automatically passing every item just to finish the audit. Paper-based methods also create lag time between data collection and analysis, making it difficult to intervene before problems occur.
Automated LPA software reduces the administrative overhead associated with LPAs by as much as 85%, allowing you to:
- Schedule recurring audits for 50 people in less than 10 minutes
- Send automatic reminders when it’s time for team members to conduct audits, as well as notify supervisors when they’re overdue
- Quickly close out non-conformances, or assign corrective actions as needed
- Rotate questions and auditors to prevent pencil-whipping
- Get instant visibility into actionable results and findings
Some people might think you already need a well-established quality culture to be successful with LPAs, given their level of complexity. But the truth is, even a company with the most basic quality management system can benefit from LPAs. All you need is the right motivation, authentic management commitment and an efficient way to manage your program.