33 Sample Questions for Your 5S Checklist
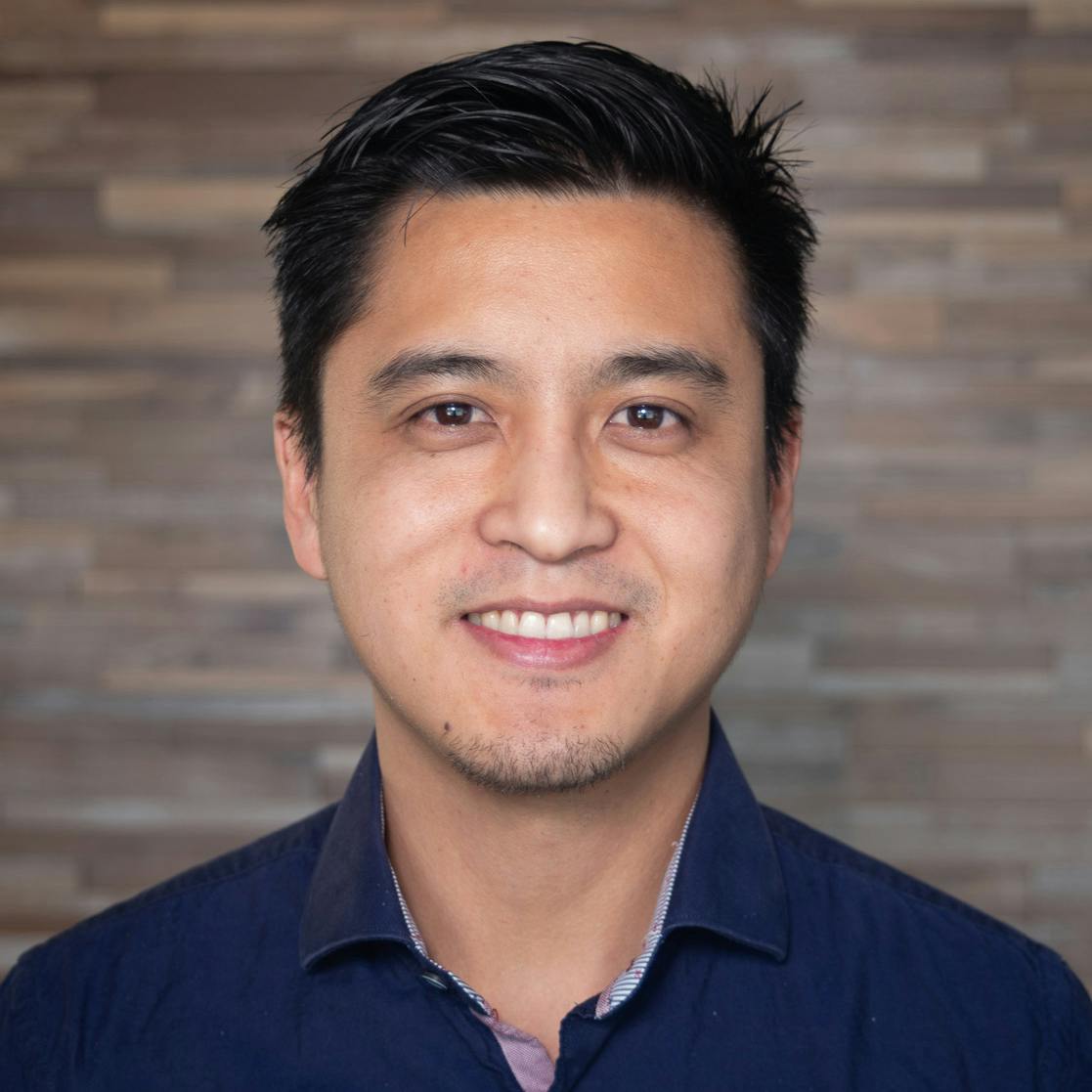
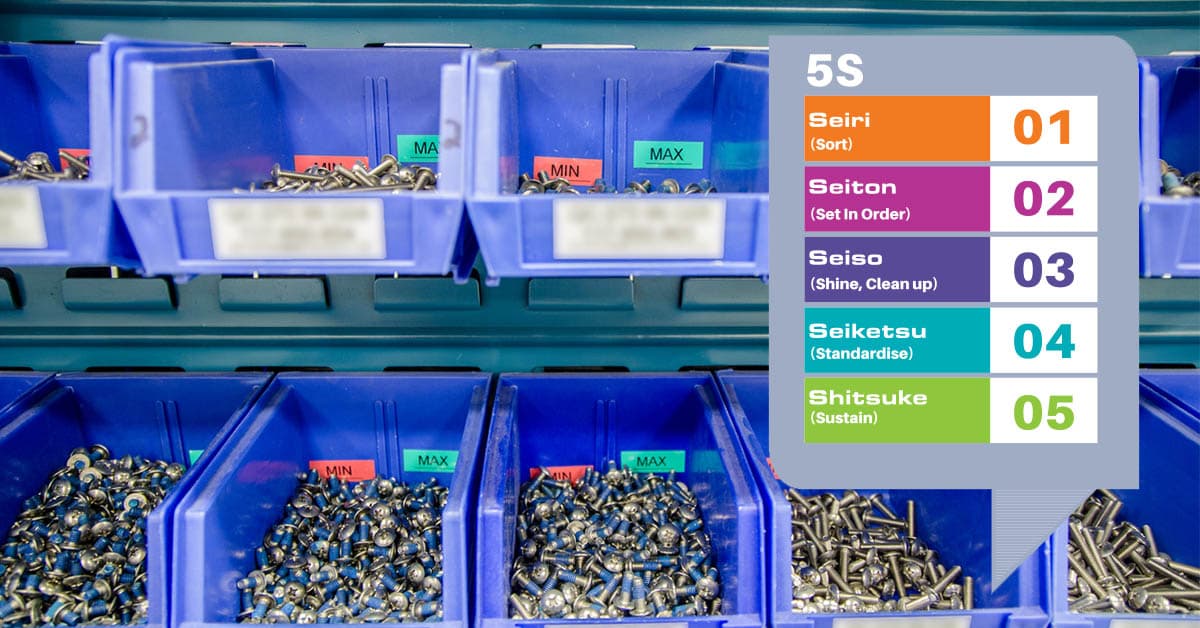
The American Society for Quality (ASQ) defines 5S as “a methodology that results in a workplace that is clean, uncluttered, safe, and well organized to help reduce waste and optimize productivity.”
Rooted in Lean manufacturing, 5S is all about creating an environment conducive to quality and safety.
If you’re new to 5S, you may wonder what types of questions to include in your 5S checklist. Let’s take a look at some sample questions from each category, and how to incorporate questions into your larger audit program to simplify your 5S efforts.
Seiri: Sort
The Japanese term seiri loosely translates to sort. Seiri refers to separating essential tools, parts and instructions or documentation from anything that’s unnecessary or obsolete at the workstation. This step is typically one of the most straightforward, making it a good place to start on your 5S journey.
Some questions you might include here on your 5S checklist include:
- Are all tools in the work area currently in use?
- Are all tools or parts off the floor?
- Are all posted work instructions, notes and drawing currently in use?
- Are workstations and walkways clear of unnecessary items and clutter?
- Are occasionally used items stored separately?
- Is the station clear of safety hazards such as spills or unlabeled chemicals?
Seiton: Set in Order
When it comes to seiton, it’s helpful to remember the old adage, “A place for everything, and everything in its place.” To achieve this goal, consider including questions such as:
- Are tools, equipment and supplies organized in separate locations and bins?
- Are materials and tools clearly labeled?
- Are parts that need reworking set aside in a separate location?
- Are minimum and maximum quantity limits clearly indicated?
- Are items not in use put away?
- Are aisles and work areas clearly delineated?
Seiso: Shine
This step focuses on ensuring workplace cleanliness. Potential 5S checklist questions in this area include:
- Are surfaces clear of dirt, oil and grease?
- Is equipment clean?
- Are cleaning supplies ?
- Are labels and other visual markers clean and intact?
- Are light fixtures clear of dust and dirt?
- Is the area free of evidence of pests?
Seiketsu: Standardize
While the previous steps are more straightforward, achieving a high level of 5S compliance for the final two can be a little trickier. Questions here may integrate elements of previous categories, for example:
- Is there a standard cleaning procedure?
- Can the operator describe and demonstrate all steps of the standard work instruction?
- Is there a standard procedure for verifying process adherence?
- Are visual management systems updated and in use?
- Is the schedule for 5S checks being followed?
Shitsuke: Sustain
The cornerstone of continuous improvement is the ability to sustain any gains you make. Without this key element, you’re only treading water—or worse, backsliding as previous problems recur.
5S questions here should focus on items like:
- Has the operator received 5S training?
- Have all of last week’s 5S findings been corrected?
- Are last week’s corrections still in place?
- Have daily 5S checks been performed every day this week?
Digital 5S Audit Checklists
For companies that conduct 5S audits in addition to other audits like quality system and layered process audits (LPAs), mobile audit management software can streamline the process.
Advantages of using a digital platform like EASE to centralize audit management include the ability to:
- Cover multiple audit types (e.g., 5S, safety, LPAs) in the same checklist with question tagging and randomization
- Conduct mobile audits via smartphone or tablet without having to manage or update paper checklists
- Get instant visibility into findings to identify and correct problems faster
- Spot trends before they lead to quality or safety issues
- Add questions to ensure you’re sustaining the gains made through previous fixes
One issue to consider if you’re using a digital 5S audit system is how to word questions. For example, you might want to standardize questions such that a ‘no’ answer is a non-conformance that requires follow-up, as we have worded them here. An alternative to a pass/fail system would be a rating approach based on the total number of problems identified, something that’s common with a 5S audit system.
5S is a powerful Lean manufacturing approach to improving safety, quality and efficiency on the plant floor. Similar to other strategies, however, effectiveness depends on ongoing verification and writing good questions.
As you sort, organize, and clean, the ability to standardize and sustain checks will determine whether your team treats 5S as a one-off quality project or truly a way of life. An automated audit solution can help ensure it’s the latter, acting as a catalyst for standardization and sustained improvement that everyone from CEO to front-line operator can see.