6 Ways Layered Process Audits Add to the Bottom Line
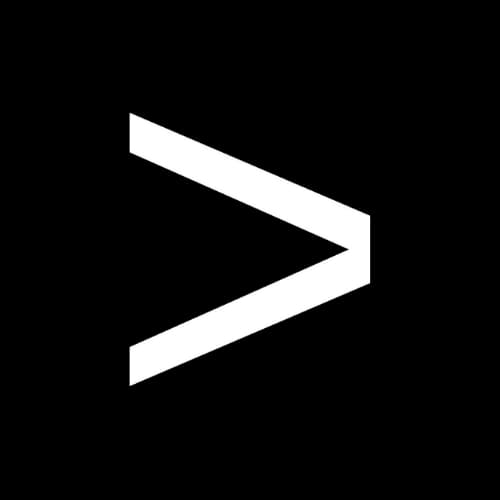
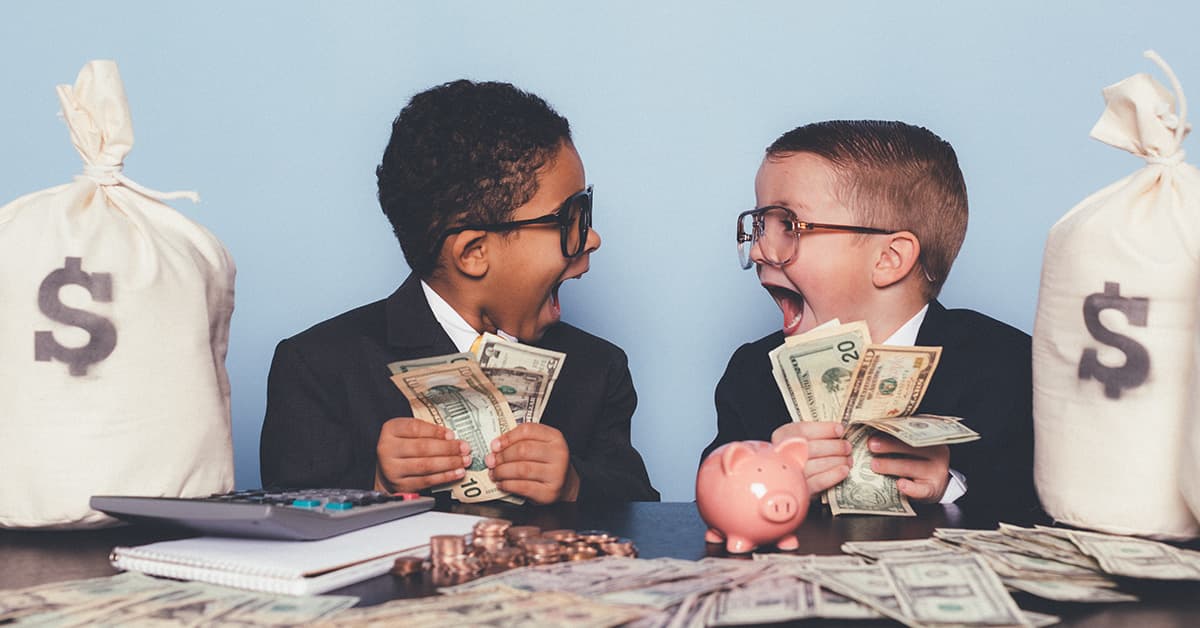
Layered process audits (LPAs) are a cost-effective way to reduce quality and safety costs, providing daily process checks to minimize defects and incidents.
Considering the cost of a single quality or safety failure, implementing layered process audits might seem like a no-brainer. However, organizations may hesitate due to the logistics of setting up an LPA program, leaving many wondering whether it’s worth the investment.
In today’s post, we look at six ways that LPAs add to the bottom line, highlighting how plants can leverage the power of prevention to drive down quality costs. We also examine how digital LPAs streamline the process so you can focus on what the data is telling you rather than the administrative complexity of managing frequent audits.
1. Lower Scrap
Reducing scrap is more important than ever in the context of today’s current supply chain challenges. In fact, according to the American Productivity and Quality Center, the cost of scrap and rework is estimated at over $2 million annually for a company with $100 million in revenue.
With proper execution, LPAs have the potential to significantly reduce scrap costs. That’s because these plant floor checks identify sources of variation early in the manufacturing process, pushing down production defects that have a direct impact on scrap costs.
Manufacturers have been able to reduce defects by 50% or more with digital LPAs, using software to automatically schedule audits, build randomized checklists and report on findings.
See how a Fortune 500 automotive supplier reduced PPM by 73% with EASE in our free Automotive Case Study
2. Reduced Corrective Action Costs
LPAs reduce corrective action costs by catching defects earlier when they are easier to contain and less expensive to fix. The result is better prevention and early detection of problems, helping to limit complaints and associated costs.
For example, an LPA can identify when an operator isn’t using the right temperature setting on a machine, a problem that might not be detected until complaints start rolling in. Early detection of this process variation means the quality team can quarantine affected product and keep it out of the hands of customers, also limiting the number of bad parts manufactured.
The 1-10-100 Rule tells us that every dollar spent on preventing a problems saves 10 dollars in correction costs and 100 dollars in failure costs. Line stoppage fees from original equipment manufacturers (OEMs) can run as much as $10,000 per minute in the automotive industry, highlighting the critical role of prevention.
3. Less Equipment Downtime
Unplanned downtime has a direct impact on the bottom line, for instance in the automotive industry where stopping production costs a staggering $22,000 per minute. LPAs performed at the start of each shift can help identify equipment issues before a machine goes down, limiting the potential for downtime by verifying key items such as:
- Machine settings
- Operator compliance with standard work processes
- Whether a work station is set up correctly with the right tools and materials
4. Increased Productivity
LPAs can help reduce equipment downtime, scrap and time spent on corrective action. Ultimately, these all add up to increased productivity and profitability.
The key here is that, instead of spending valuable time and resources on products that get returned, those resources are going into viable products that generate a profit. Proactively preventing defects also increases production capacity and process efficiency, enabling more sales that add to company revenue.
5. Fewer Safety Incidents
Reducing safety incidents is key to limiting workers’ compensation costs as well as costs associated with lost productivity. According to the National Safety Council, the average cost of a medically consulted workplace injury was $44,000 in 2020. By incorporating safety-related questions into daily plant floor checks, companies can minimize costly injuries that can be life-altering for employees.
Safety also plays a key role in employee satisfaction, which has an important yet indirect effect on corporate profits. According to research in Applied Ergonomics, employee perception of safety is directly linked to employee engagement and turnover rate. Verifying safety processes on the plant floor shows a genuine commitment to safety, helping reduce high turnover costs at a time when the Great Resignation has teams stretched thinner than ever.
6. Higher Customer Retention
A general rule of thumb is that it costs five times more to get a new customer than it does to keep an existing one. Improved customer satisfaction is a direct result of LPAs, adding profits to the bottom line by reducing customer acquisition costs and making existing customers more likely to order more.
A digital LPA platform in particular can make a strong impression when customers visit the plant, allowing you to quickly pull up audit data without having to sift through paper. Plants can also show customers where new LPA questions have been added in response to complaints, demonstrating they are holding the gains of corrective action.
LPAs represent a cost-effective strategy for minimizing production defects and related costs that eat away at profits. Digital LPAs minimize the complexity of these audits with automated scheduling, reporting and issue mitigation, shifting the focus from paperwork to what’s actually happening on the plant floor. The result is lower quality and safety costs, including hidden opportunity costs associated with customer and employee retention.