Audit Questions to Ask Now to Reduce Coronavirus Risk in the Workplace
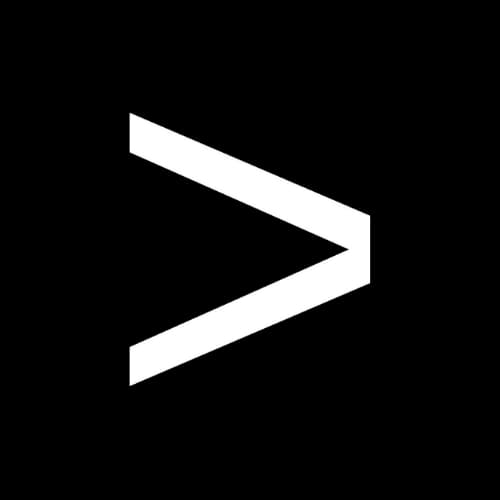
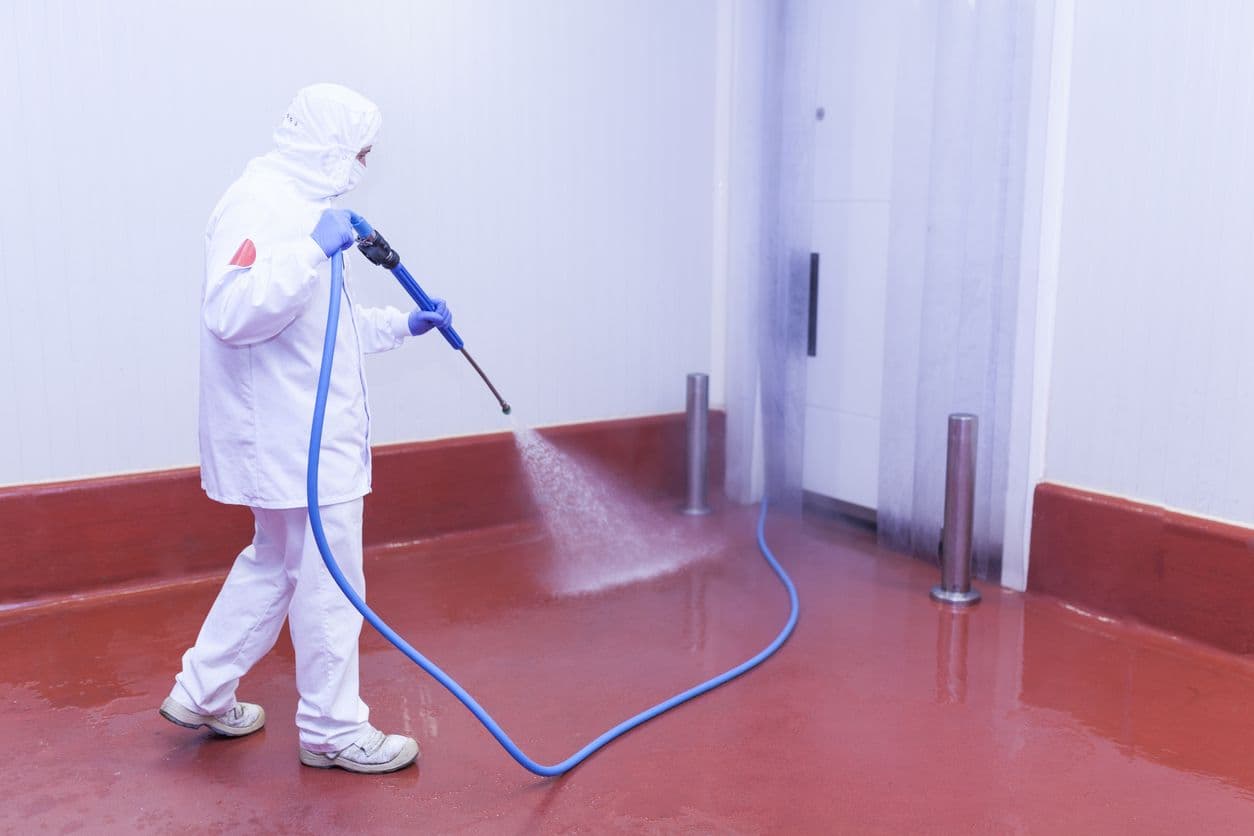
In the rapidly developing coronavirus crisis, it’s clear that manufacturers of all kinds will have to make big changes.
While some automotive manufacturing is shutting down, other companies like medical device manufacturers are ramping up production to keep critical supply chains functioning during this difficult time.
Amid the heartbreaking shutdown of Ford, GM and Fiat Chrysler, personal protective equipment (PPE) and medical device manufacturing is growing, with 3M ramping up manufacturing to provide more N95 masks and other supplies.
For manufacturers continuing operations, conducting periodic audits to ensure people follow safe and sanitary practices can help save lives. Whether using layered process audits (LPAs), safety audits or 5S audits, you’ll want to consider adding the following questions to your checklists or question library (for those with an automated platform). We also go over how to make audits themselves safer to reduce the risk of spreading the virus.
Protective Clothing
Manufacturers like Premio Foods are fighting COVID-19 with expanded sanitization efforts and increasing the frequency of protective clothing and glove changes, also using audits to verify that employees follow the new standards.
If your facility makes changes to protective clothing policies, you may want to add questions such as:
- Are workers changing out protective clothing and gloves according to enhanced standards?
- Are operators washing hands and sanitizing gloves at the required frequency?
- Do operators know how often they should change out protective clothing, wash hands and sanitize gloves?
- If your safety standards require safety glasses, are operators wearing them?
Equipment and Work Stations
Keeping manufacturing equipment and work stations clean and sanitized is essential to protecting workers and product safety. Questions to ask here include:
- Are work stations sufficiently separated to keep people a minimum of 6 feet apart?
- Are work stations free of clutter and debris so they can be cleaned regularly?
- Has the operator sanitized their equipment or station according to the frequency set out in new or existing standards?
- If you have enhanced cleaning standards or frequencies, can the operator describe how and how often they should be cleaning?
- Are the required sanitizing supplies (e.g. wipes, cleaning solution, etc.) available at the work station?
- Are operators using separate equipment? If not, is the equipment cleaned and disinfected between uses?
Shared Spaces
Communal spaces such as break rooms and bathrooms are key places where pathogens can spread among individuals. Questions you can add to safety walkthroughs to protect workers include:
- Are high-use surfaces like counters, workstations, keyboards, handrails, phones and doorknobs in common spaces sanitized frequently?
- Is seating spread at least six feet apart to maintain spacing?
- Are people congregating in areas like breakrooms or lunch areas?
- Are tissues, hand sanitizer, sanitizing wipes and no-touch disposal receptacles available?
- Are soap and water readily available and bathrooms wiped frequently?
- Are cleaners being used on the list of EPA-approved disinfectants for coronavirus?
People
People’s behavior is a key determinant of COVID-19 transmission. To reduce that risk, you can encourage people follow best practices by adding questions such as:
- Are any employees visibly sick or exhibiting symptoms?
- Are people generally staying six feet or more apart?
- Do employees avoid handshaking and follow coughing and sneezing etiquette?
- Are employees following handwashing protocols and recommended frequencies?
- Do people know which symptoms to watch for and report?
- Do people know when to stay at home?
For more information, the U.S. Occupational Safety and Health Administration offers a PDF guide with detailed recommendations on preparing workplaces for COVID-19. The Centers for Disease Control (CDC) also offers guidance for businesses on reducing coronavirus risks. Learn more about the layered process audit checklist PDF on our dedicated page.
Keeping Audits Safe
Audits themselves may need to change to minimize the risk of spreading COVID-19. For one thing, auditors must be sure to maintain at least six feet of space when conducting audits. Organizations can also consider how to conduct contactless audits, relying on observation and minimizing face-to-face interactions whenever possible. Finally, if you perform mobile audits using a shared device such as a tablet, auditors should be sure to sanitize the device before and after each audit.
Many manufacturing organizations have already shut down as a result of coronavirus, and more will undoubtedly undergo big changes. For those continuing to run to provide essential supplies, adding daily checks of the items discussed here can help keep workers safer.