Auditing What Matters: Why Variation Is Key
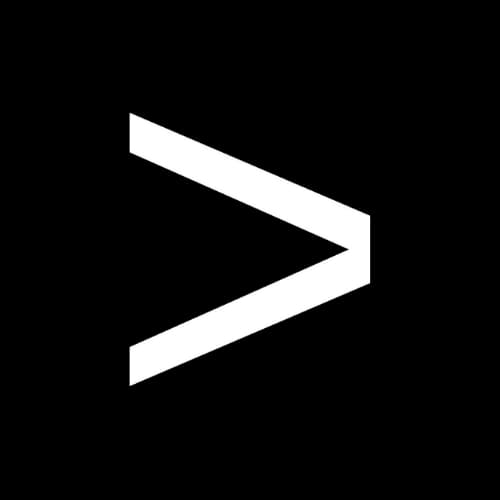
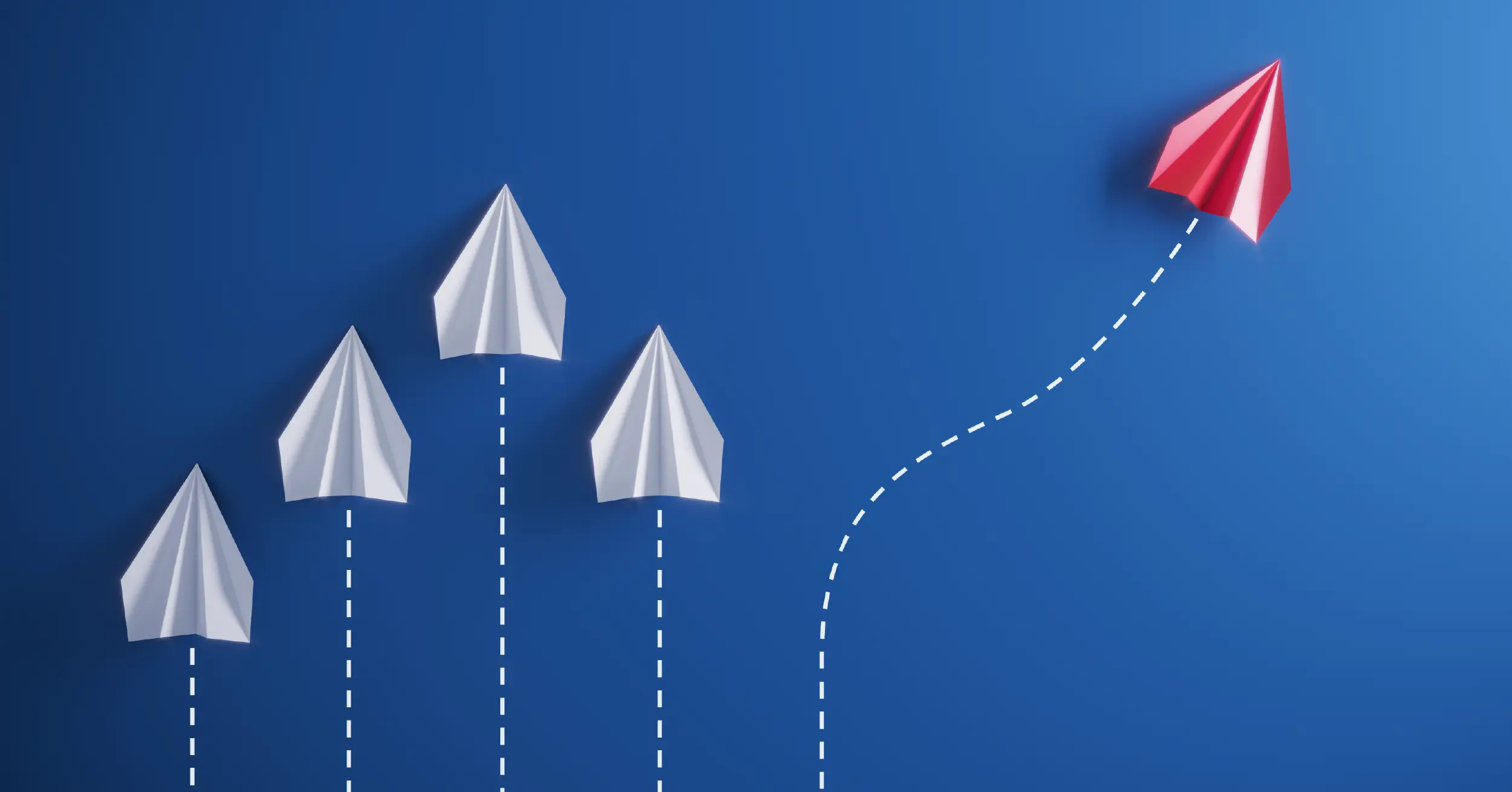
Imagine you’re conducting layered process audits and you see the following two questions on your checklist:
- Is the poka-yoke device bolted to the machine?
- Does the operator clear the extra plastic from the part before removing it from the mold?
While both questions address process inputs important to reducing defects, only the second question addresses an input that’s likely to vary over time. Variation is key when selecting elements to verify with layered process audits, helping you get the most valuable information in a short amount of time.
Today we’re looking at why it’s so important to focus on variation when writing layered process audit (LPA) questions. We also explore some practical examples, the role of the 6Ms and how LPA software can help you check inputs at the desired frequency.
Download your free Ultimate Guide to Layered Process Audits for more LPA question best practices, examples and tips
Why Variation Matters
When it comes to choosing an input to verify with an LPA question, there are several aspects to consider:
- Is it high value? Checking paperwork or forms is a waste of time when you only have ten minutes to complete an audit.
- Can you design a yes or no question around the input with clear evidence of conformance? Auditors need to be able to easily check whether the process is in or out of conformance.
- Is the process element something that can vary over time? An input may be high value and easy to check, but if it never changes you don’t need an LPA question to check it.
Asking questions about process elements that don’t vary over time tends to frustrate auditors and operators, hurting buy-in for your LPA program. If people don’t think the questions have value, they’re more likely to check out and simply pencil whip the audit.
Just as important, LPAs are designed to be frequent, and to achieve that you must be able to complete them quickly. That means only having about ten questions on each checklist. With so few questions included on each audit, each one needs to have maximum impact. Verifying elements that don’t vary is a waste of time and a lost opportunity to catch another problem that could lead to product defects.
So how do you know whether an element varies over time? One simple way to find out is by asking the operator. Soliciting operator feedback can provide valuable insight into which questions are likely to hit home, and which ones are likely to provide little value.
Using the 6Ms to Drive Variation to Zero
A great place to start when building your LPA question library is the 6Ms of process control. Based on an Ishikawa or fishbone diagram, the 6Ms are used to categorize process inputs that, where variation exists, can lead to quality problems. The 6Ms are:
- Man (People): Variation in how an individual employee does their job, or variation among how different workers perform an operation, can lead to problems.
- Machine: Changes in equipment operation such as those due to normal wear and tear can lead to defects.
- Method: Variation in methods should only occur if you are using separate sets of work instructions to produce similar parts for different customers. Most LPA questions won’t focus on Method because there shouldn’t be variation in documented methods.
- Mother Nature (Environment): Environmental conditions such as high humidity or high temperatures are a crucial source of variation, since they can impact equipment performance as well as stability of materials.
- Material: Examples of material-related variation would be if a raw material was labeled incorrectly, the wrong parts were brought to the work area or if there’s an issue with supplier quality.
Getting the Frequency Right
There are certain situations where asking a question daily on an LPA would be too much, yet not asking it at all also represents a risk. The above instance of the poka-yoke device being bolted to the machine is one such example.
Asking this daily or even weekly is likely too frequent, especially if you’ve never had a problem with it in the past. However, let’s say you installed the device as part of a corrective action to prevent upside-down assembly. As such, this might be something you want to check periodically to make sure it’s still working.
Instead of including it on a daily checklist, however, you might add it to a pool of low frequency questions, so that it’s checked once every 45 days. The way you do this is by creating a custom tag in your question library, randomizing checklists to rotate in just one low frequency question per audit. LPA software like EASE makes this simple, also allowing you to create tags for each of the 6Ms to ensure broad coverage of known risks.
While it may be tempting to throw anything and everything into your LPA question library, discretion is critical. By focusing on elements likely to vary—and dialing down the frequency of questions that don’t—you can ensure you’re getting the most value from these fast, frequent audits.