13 Popular Layered Process Audit Questions Answered
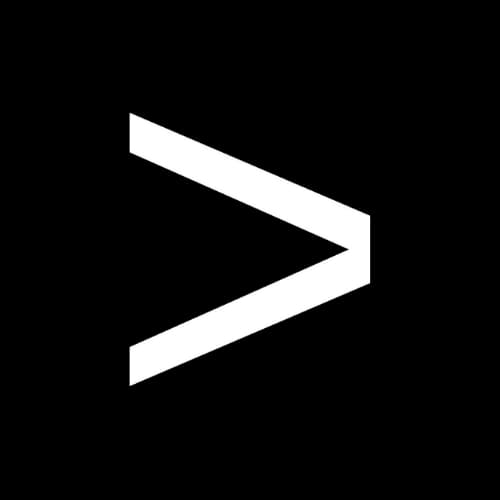
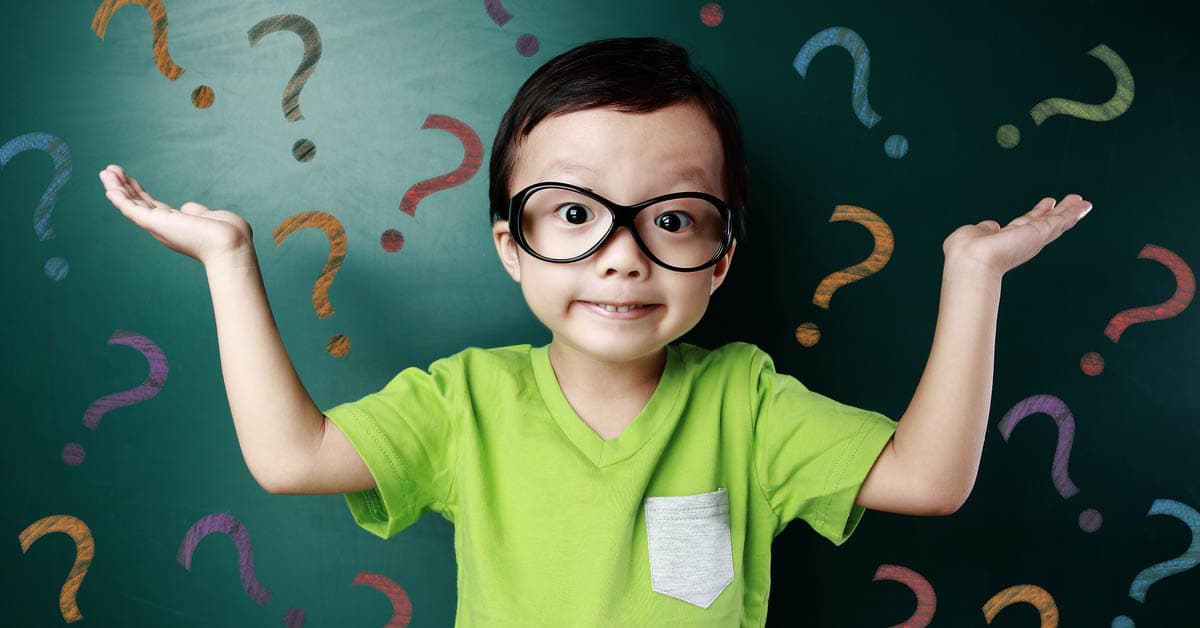
If you are currently conducting layered process audits (LPAs) you know that when done right, investing time upfront in prevention avoids costly and time-consuming downstream quality issues that impact customer satisfaction.
That’s why it makes sense to check in annually on your LPA program and reassess obstacles to success and best practices for achieving better results.
Ease ran a webinar in conjunction with The Luminous Group recently where we provided a framework for an annual LPA checkup. Attendees surfaced some great layered process audit question and challenges that have wide applicability to other manufacturers. In this post, our LPA experts answer a selection of those questions.
Watch the OnDemand Webinar Reduce Reoccurring Defects with an LPA Checkup
Q. Is Craftsmanship a Process Input or are you Checking an Output?
In manufacturing, craftsmanship is one of a number of process inputs to achieve a desired output. For LPA check sheets and questions, it’s preferable to check process inputs: e.g. settings, tooling used, operator craftsmanship in order to prevent defects.
Q. How Do you Connect LPAs to a Turtle Diagram?
Process inputs that have been determined with even the slightest variation should be on an LPA since they can result in a high probability of creating a non-conformity. These are typically manual assembly related processes. Not all process inputs need to be audited on a daily basis – which is the fundamental goal of LPAs.
For example, on the ‘Material’ leg of a Fishbone Diagram, the chemistry of the incoming material does not need to be on an LPA. Typically, the supplier quality team would audit these processes for incoming material. Fundamentally, the questions incorporated into a layered process audit should be based on risk.
Q. How Many Questions Should be Included in a Standard LPA?
A typical layered process audit should contain approximately 10 questions. There is not a set standard but remember that LPAs are designed to be high-frequency audits that take no longer than 10-15 minutes so keep this in mind as you design them. LPAs are auditing the recipe (inputs) of the process in real-time to ensure the process is followed to create desired, conforming products (outputs).
LPAs can become too long if non-quality related questions are added to them that are unnecessary. When LPAs become too long with process inputs, then break them up by operation, shift or frequency. Additionally, if you use LPA software like EASE, you can consider randomizing questions at a set frequency to incorporate more questions but asking them on a slightly less frequent basis.
Q. Can you use LPAs to Review Competency?
LPAs are verifications of the process, including people and operator craftsmanship and technique. While it might be easy to check if an operator was trained, what’s more important in an LPA is are they performing the job as required at the time of the audit. Therefore, LPAs should be focused and detailed at high-risk process steps to look for nonconforming variation in how an operator performs the task or the job.
Repeated failure to perform the process correctly by the same operator should raise questions but consider the 5 Whys technique as a way to evaluate what the root cause of the issue is. It could certainly be operator competency, but it could also be training, out of date work instructions or perhaps the process itself is too complicated and needs simplifying.
Q. Do you Recommend that the LPA Questionnaires be Different for Each Layer?
Absolutely not. The same audit should be used at every level of the organization. This removes variation from the LPA process and holds all levels accountable to thoroughly complete their checks. The only exception is that higher levels of management, who audit less frequently, might and should have additional questions. These additional questions are usually general system level checks.
Q. Our Open Issues List Has Ballooned to 100s of Issues, What Should We Do?
If open issues balloon and there is an organizational failure to address issues in a timely manner, it is time to refocus operations and leadership. We suggest perfecting the process in a smaller, model area but putting available resources in that small part of your plant. Clarify the inputs and processes and hold the gain there.
Once the desired output is achieved, you can extend the approach across horizontally to other operations. However, take time to be sure that everyone is following the practices developed from the model area. The model area is the “lighthouse” for the expansion. In other words, if people in the expansion areas do not respond or take it seriously or have doubts, you could take them to the model area and demonstrate it works. The model area project must be truly supported by the highest level of leadership in the facility, just the quality department.
Q. Can you Comment on LPAs versus the Toyota/Lean Approach?
There is no contrast or difference between LPAs and the Toyota/Lean Approach. Toyota Production Systems (TPS) educate leaders on the forgetfulness curve. What they mean by that is if operators or leadership are not reminded on a frequent basis of what is important, human nature will typically forget and only remember when there is a crisis. Constructed and executed correctly, LPAs address forgetfulness too, reminding people what is most important (holding process element inputs in place).
Q. Could the LPA be Used for Quality Internal Audits, Kind of Layer 3, Maybe?
Yes, if you make them a controlled document and a part of the internal controls. This would provide structure and ensure accountability. Also, using LPAs in this way would bring leadership attention to non-conformities found in previous QMS internal audits; again, paying attention to what’s important.
Q. How can we Sell the Value of Layered Process Audits to Everyone: Operators, Auditors, Leaders?
The best way to do this is to promote the ability to give instant, positive feedback/recognition when you catch people doing something right. This is a key aspect! Yes, we need to catch people doing something wrong too, but if the process is healthy, this will be minimal. If your LPA process is healthy, when you arrive to do an LPA at a particular operation, people will show you the correct process immediately.
Another approach is to post the results visually along with dashboards, showing compliance to schedule a mitigation of any nonconformances. Reviewing the previous day’s LPA results at each shift meeting can also help sell the value and importance of LPAs.
Q. Where’s the Best Place to Get Sample Layered Process Audit Questions?
You’ll find sample questions in The Luminous Group’s training materials, Ease’s Ultimate Guide to Layered Process Audits as well as our Layered Process Audit Checklist Template. There is not a bank of best practice questions for a given manufacturing technology because every plant, and every process, and every line – even every shift could have their unique risks. Transplanted questions could be a good starting point but they are typically ineffective and eat away at the potential health of an LPA system.
Q. Do you Have any Advice on Preventing LPA Auditors from Pencil Whipping Their Audits?
Pencil-whipping, or just clicking through an audit, is not likely to happen in a healthy LPA system. Why? Someone else will be checking the same elements after you. Also, if it’s a high-risk process (assuming you have questions that are meaningful for that process) if a problem occurs, who wants to be the last person checking that didn’t do the verification?
That said, by keeping the auditing time between 5 and 15 minutes you can ensure it’s not a large time-burden on auditors. You can also see where you have exceptionally short audit times as strong indicators that pencil whipping occurred. If you use a digital LPA solution such as EASE, you can have auditors use their device camera to capture and timestamp a conforming or non-conforming situation.
Q. Should LPAs be Focused Primarily on the Production Area? Or are They Appropriate for Other Processes Such as Maintenance, Tooling Warehousing etc.?
Production is usually the focus of LPAs because that’s where variation is very prevalent and severities (customer issues and scrap) are very high. But certainly, you can use LPAs anywhere you have processes and requirements that might benefit from LPAs including maintenance, tooling, warehousing etc.
Q. Management is Asking, “What is the Positive Impact of Performing LPAs Such as Cost Savings?” Do you Have a Recommendation About how to get This Information?
LPAs reduce non-conformities leaving the process as waste – scrap, customer returns, and warranty claims. The key here is to attach a proper execution of an LPA to a specific defect and track performance of that defect only. That will be an initial LPA Key Performance Indicator (KPI).
Posting the defect “run chart” at the specific operation also has an effect on the continued support of maintaining that process input by the operations team. This convinces all involved that the process has value. Ease also has a White Paper: Calculating the ROI of Layered Process Audits that covers this in more detail.