14 Examples of Quality Metrics in Manufacturing for Product Quality Assurance (QA)
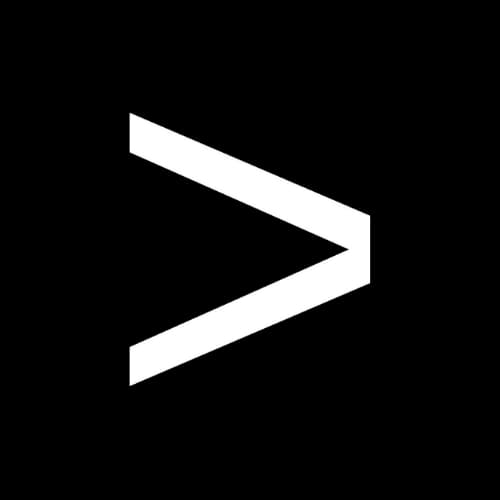
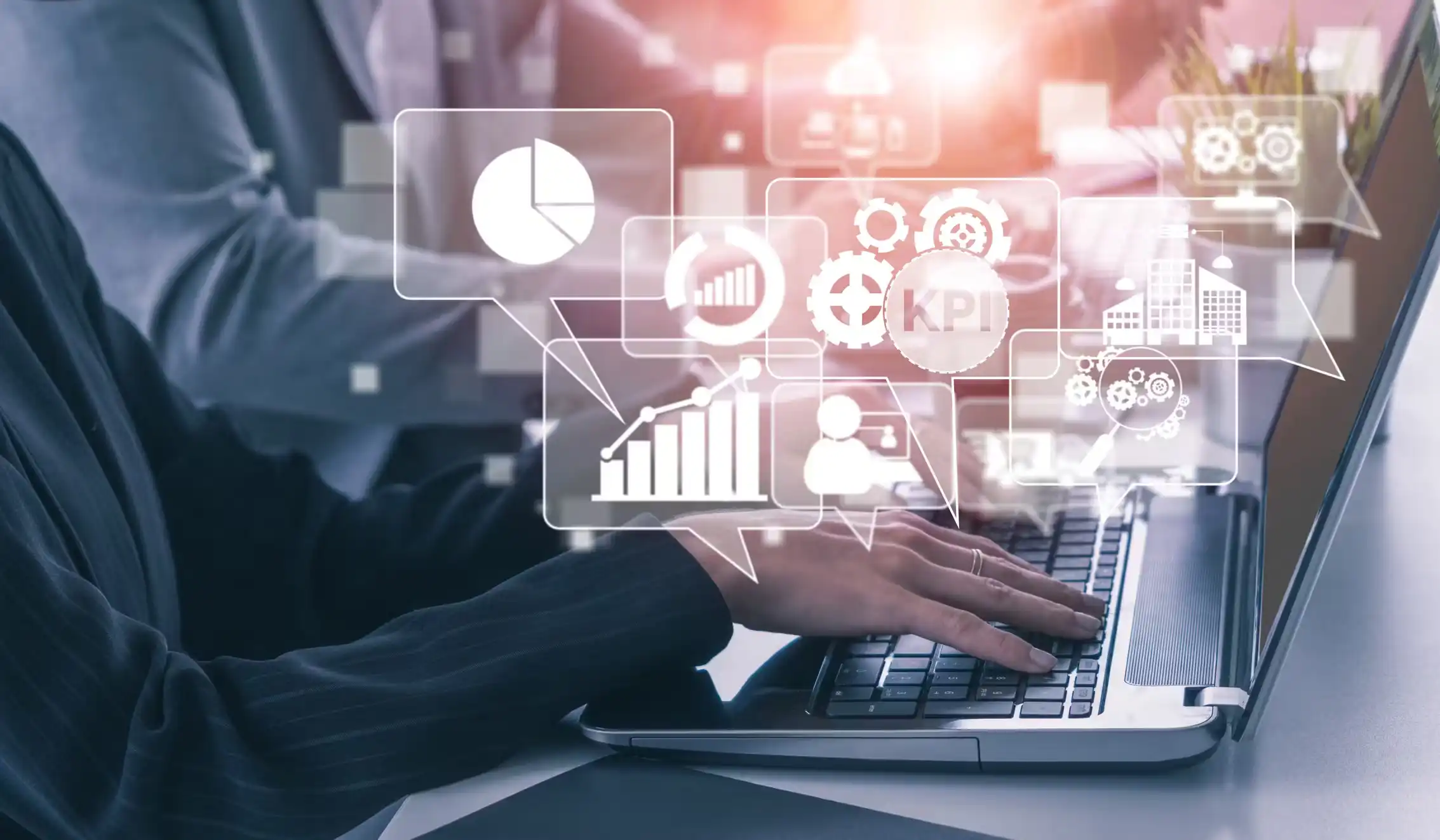
As the saying goes, what gets measured gets managed. That’s just as true for quality control, where you must measure quality metrics for quality management. However, sometimes it’s hard to know which quality assurance metrics are the most important.
This post gives a brief summary of the types of metrics and a high-level overview of 14 quality metrics examples every top executive should consider monitoring, depending on your specific goals and improvement needs.
Selecting the right ones will help you improve the quality of your products and services. They will help reduce the number of defects to improve stakeholder satisfaction, bringing your quality standards to meet and exceed market expectations.
Read the latest quality trends in manufacturing.
Types of Quality Metrics
Understanding the types of product quality metrics is important for effectively monitoring and improving manufacturing processes. They can be broadly categorized into four key areas, with each serving a specific purpose. When aligned with industry best practices, they ensure overall quality and operational efficiency.
Process Metrics focus on the efficiency of your production lines. Metrics like yield, throughput, and cycle time help identify bottlenecks and assess the performance of individual processes.
Product Metrics measure the quality of the final output and customer satisfaction. Common examples include defect rates, scrap rates, and customer complaints, which directly reflect how well the product meets standards and customer expectations.
Maintenance Metrics offer insights into equipment performance, ensuring reliable operations. Metrics such as downtime and the ratio of planned versus unplanned maintenance help prevent disruptions that could impact quality.
Supplier Quality Metrics track the quality of materials and components, while metrics like incoming quality and supplier defect rates help maintain a high standard of inputs, reducing rework and defects downstream.
Additionally, performance metrics are vital in supporting and complementing these categories by ensuring operational efficiency. By categorizing your metrics, you can focus on the areas most critical to your goals, creating a comprehensive view of your quality performance while driving continuous improvement.
Examples of Quality Metrics and KPIs, and How to Use Them
When it comes to achieving operational excellence and delivering high-quality products, tracking the right quality metrics—or Key Performance Indicators (KPIs)—is essential. These key metrics are used to assess an organization’s services and processes, helping to uncover areas that need improvement and prevent defective outcomes.
From cost of poor quality to customer satisfaction rates, metrics help ensure quality, enhance overall efficiency, and support improvement efforts. Whether you’re focused on manufacturing equipment or project management, understanding ways to measure and evaluate metrics like test coverage, percentage of goods, and work-in-process is critical for creating products that meet market demands.
By using these quality metrics to improve outcomes, organizations can make informed decisions and maintain their competitive edge.
1. Cost of Quality
The Cost of Quality (CoQ) stands out as a crucial metric that warrants close monitoring, as it is often overlooked in data sources tracking quality issues. It encompasses both the expenses incurred due to poor quality and the investments made to ensure high quality.
The following formula for CoQ was developed by the American Society of Quality (ASQ):
COPQ includes internal and external failures, such as:
- Internal COPQ, like scrap, rework, and re-inspection
- External COPQ, when defects reach the customer, including adverse event reporting, warranty, corrections and removals, product liability, and loss of brand reputation
COGQ is comprised of what you spend to create conforming products, including:
- Appraisal costs like inspection and testing, quality audits, and calibration
- Prevention costs like statistical process control (SPC), quality planning, and training
How to Use It:
- Prioritize Improvements: Analyze CoQ data to identify whether prevention costs (e.g., training, audits) are lower than the costs of defects (e.g., rework, warranty claims). Focus on increasing prevention activities to lower overall CoQ
- Set Benchmarks: Use CoQ to establish cost-saving targets for internal and external stakeholders
- Track Trends: Monitor CoQ over time to evaluate the ROI of quality improvement programs
Read how to reduce manufacturing costs.
2. Defects
Calculating defect rate
There are a couple of ways to look at defects that tend to confuse people:
- Defective parts per million (DPPM): Interchangeably called parts per million (PPM) or defects per million (DPM), you can calculate DPPM with the following formula:

- Defects per million opportunities (DPMO): This metric proves particularly valuable in examining defects within subassemblies, where there could be numerous chances for failure. Calculate DPMO with the following formula:
- Improve Manufacturing Processes: Use DPMO to identify specific stages in production where defects frequently occur and to address root causes
- Monitor Supplier Quality: Compare defect rates to identify and replace underperforming vendors
- Enhance Training Programs: Focus employee training efforts on processes or areas with the highest defect rates
3. Customer Complaints and Returns
Ensuring customer satisfaction
Closely monitoring customer issues is the only way to systematically prevent them. Figures to help you track customer-related issues include:
- Complaints, rejects, or returns over a specific period
- Number resolved during a specific period
- Average taken to resolve customer complaints
- Warranty costs
How to Use It:
- Boost Customer Satisfaction: Use complaints and return data to identify recurring product issues and take corrective action to resolve them
- Reduce Warranty Costs: Focus on common complaints or defects that lead to costly warranty claims
- Drive Product Development: Incorporate feedback from complaints into future product designs to better meet customer needs
Get Our Free Ebook on Quality Cost
4. Scrap
Scrap rate is the percentage of materials sent to production that never become part of finished products. You’ll want to keep a close eye on total scrap
costs.
Scrap to include in your calculations include vendor scrap, internal scrap, and internal setup scrap. Manufacturers usually have their own internal ways of calculating scrap; for example, some companies would not include setup scrap, so it’s important to check with your company on what to include.
An easy way to calculate scrap is:
- Reduce Material Waste: Identify and address the processes responsible for the highest scrap rates
- Improve Supplier Selection: Work with suppliers to ensure incoming materials meet quality specifications, reducing scrap due to poor inputs
- Monitor Environmental Impact: Use scrap rate data to support sustainability initiatives by reducing wasted materials
5. Yield
Yield is a metric used to measure process or plant effectiveness. Beyond total yield, consider monitoring first-pass yield (FPY): the percentage of products manufactured correctly the first time through without rework.
For example:
- 200 units enter A and 150 leave. The FPY for process A is 150/200 = .75
- 150 units go into B and 145 units leave. The FPY for process B is 145/150 = .97
- 145 units go into C and 130 leave. The FPY for C is 130/145 = .89
- 130 units got into D and 129 leave. The FPY for D is 129/130 = .99

How to Use It:
- Optimize Production Efficiency: Track FPY for each stage of production to pinpoint inefficiencies and prioritize corrective actions
- Measure Process Reliability: Use yield rates to assess whether new equipment or process changes improve output consistency
- Identify Hidden Costs: High rework rates may indicate low FPY, which increases labor and operational costs
6. Overall Equipment Effectiveness (OEE)
Overall Equipment Effectiveness (OEE) is an important measure of productivity and efficiency, calculated in simple terms as availability multiplied by performance and quality. Here’s a more detailed look at each of those component metrics:

How to Use It:
- Maximize Machine Utilization: Identify machines with low OEE and develop maintenance or upgrade plans
- Improve Scheduling: Use OEE data to create schedules that minimize downtime and maximize availability
- Track Performance Over Time: Monitor OEE as a leading indicator of process improvements or potential failures
Read how to streamline manufacturing processes.
7. Throughput
Throughput is the quantity of goods produced over a given period. You can measure throughput:
- Per machine
- Per product line
- For the entire plant

How to Use It:
- Analyze Bottlenecks: Use throughput data to identify the slowest points in the production line and optimize them to increase output
- Set Realistic Production Goals: Base targets on historical throughput data to avoid overloading teams or machines
- Measure ROI: Use changes in throughput to evaluate the success of investments in new equipment or process improvements
8. Supplier Quality Metrics
Suppliers have a huge impact on quality costs. Metrics to track here include:
- Supplier defect rate: Percentage of materials from suppliers not meeting quality specifications
- Supplier chargebacks: Total charged to suppliers for cost of non-conforming materials (possibly including late delivery and payroll costs)
- Incoming supplier quality: Percentage of materials received meeting quality requirements
Learn More About The Cost of Quality
9. Delivery Metrics
There are two crucial metrics you should be measuring with regards to delivery from a customer satisfaction and efficiency perspective:
- On-time delivery (OTD) is calculated as the percentage of units delivered within the OTD window.
- Perfect order metric (POM) or fill rate is the percentage of orders that arrive complete, on time, damage-free and with a correct invoice.
It’s harder to achieve a good POM considering that each component of this metric gets multiplied together:
How to Use It:
- Improve On-Time Delivery: Use OTD data to identify delays caused by specific processes, suppliers, or logistical inefficiencies and implement corrective actions
- Enhance Customer Experience: Work on perfecting order metrics (POM) to improve customer satisfaction by ensuring timely and error-free deliveries
10. Internal Timing Efficiency Metrics
A number of metrics provide insight into how efficiently your facility runs in terms of timing. A few basics include:
- Manufacturing Cycle Time: How much time it takes from order to production to finished goods
Throughput time = Process time + Inspection time + move time + Queue time - Changeover Time: How much time it takes to switch a line to another product, which can last anywhere from a few minutes to several weeks
- Change order cycle time: Average time to execute change orders from documentation through production
- New product introduction (NPI) rate: Average time to introduce a new product to market
11. Capacity Utilization Rate
Capacity utilization is the percentage of total output capacity used at any given point. This KPI can help with strategic planning and is also an indicator of market demand.
- Strategic Planning: Use capacity utilization rates to identify whether your facility is operating near maximum efficiency. If rates are consistently low, this could indicate excess capacity that can be repurposed or downsized
- Plan for Expansion: High utilization rates approaching 100% suggest the need for additional equipment, labor, or facility expansion to meet growing demand
- Balance Workloads: Monitor utilization across departments or production lines to ensure workloads are evenly distributed, avoiding bottlenecks or overburdening specific areas
- Forecast Demand Trends: Use historical capacity data to anticipate seasonal fluctuations or market demand changes, and adjust production schedules accordingly
12. Schedule Realization
This metric tells you how often your plant reaches production targets over a given period of time. A simple calculation is orders completed by the scheduled date divided by a total number of orders.
- Monitor Production Efficiency: Track schedule realization to evaluate how well your production team adheres to planned timelines. A low rate may indicate inefficiencies, resource constraints, or overly ambitious scheduling
- Set Realistic Targets: Analyze historical data to set achievable production schedules, improving both employee satisfaction and operational reliability
- Identify Bottlenecks: A low schedule realization rate can highlight areas where delays are common, such as material shortages, equipment downtime, or inefficient workflows
- Customer Commitment: Use schedule realization as a benchmark for meeting delivery promises. A high realization rate correlates with improved customer satisfaction and reduced penalties for missed deadlines
Continuous Improvement: Combine schedule realization data with other metrics (e.g., OTD and capacity utilization) to refine processes and improve overall plant performance
13. Audit Metrics
Audit metrics are another leading indicator to monitor, especially if you’re using high-frequency layered process audits to reduce defects.
Which audit metrics should executives track? On a high level, you’ll want to look at:
- On-time audit completion rate
- Number of non-compliances per area
- Percentage of non-compliances receiving follow-up via mitigation or corrective action
How to Use It:
- Ensure Compliance: Use audit completion rates to ensure all critical areas are monitored regularly
- Track Improvements: Monitor reductions in non-compliances over time as a measure of process effectiveness
- Identify High-Risk Areas: Use audit findings to focus resources on departments or processes with recurring issues
14. Maintenance Metrics
Maintenance metrics serve as vital leading indicators for quality, offering an early alert system for potential quality concerns. Key leading metrics to track in this regard include:
- On-time completion of scheduled maintenance
- Ratio of planned maintenance activities completed to unplanned emergency maintenance
- Downtime as a percentage of total operating time
It’s essential to monitor a mix of leading and lagging indicators. While lagging indicators tell you the results you’re achieving, leading indicators let you step in early to make adjustments before things go off the rails.
How to Use It:
- Prevent Equipment Failures: Use metrics like downtime percentage and maintenance completion rates to ensure equipment reliability
- Optimize Maintenance Schedules: Prioritize preventive maintenance for equipment with high repair costs or frequent breakdowns
- Reduce Costs: Track planned versus unplanned maintenance to shift more work toward planned activities, reducing emergency repair
How to Implement Quality Metrics
Implementing quality metrics is a foundational step in ensuring the importance of quality across your organization. These metrics are critical to assess the quality of products, processes, and even software development efforts. Here’s how to get started:
Define Foundational Objectives
Establish clear goals for your metrics to use as benchmarks; for example, reducing defects by 10% or improving QA functions to enhance software quality.
Choose Relevant Metrics
Metrics to assess performance should align with your objectives. Metrics include qualitative and quantitative options like defect rates, number of tests, and measurements of performance.
Incorporate Tools and Technology
Use software tools to evaluate and automate data collection, especially within software and end-to-end manufacturing environments. These tools make it easier to analyze trends and identify areas needing improvement, often through visualizations like graphs.
Establish Baselines and Targets
Based on the number of existing quality processes, define realistic goals to improve outcomes, e.g., increasing market share by enhancing product reliability.
Monitor and Refine
Regularly evaluate progress using metrics and adjust strategies to ensure ongoing improvement of quality processes.
By focusing on foundational metrics and aligning them with strategic goals, organizations can improve outcomes, strengthen QA functions, and drive operational excellence.
And really, that’s what monitoring KPIs is all about—and what your customers expect to see you doing. Learn more about key manufacturing quality metrics.