2023 Quality Trends in Manufacturing to Watch
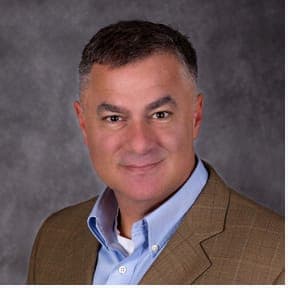
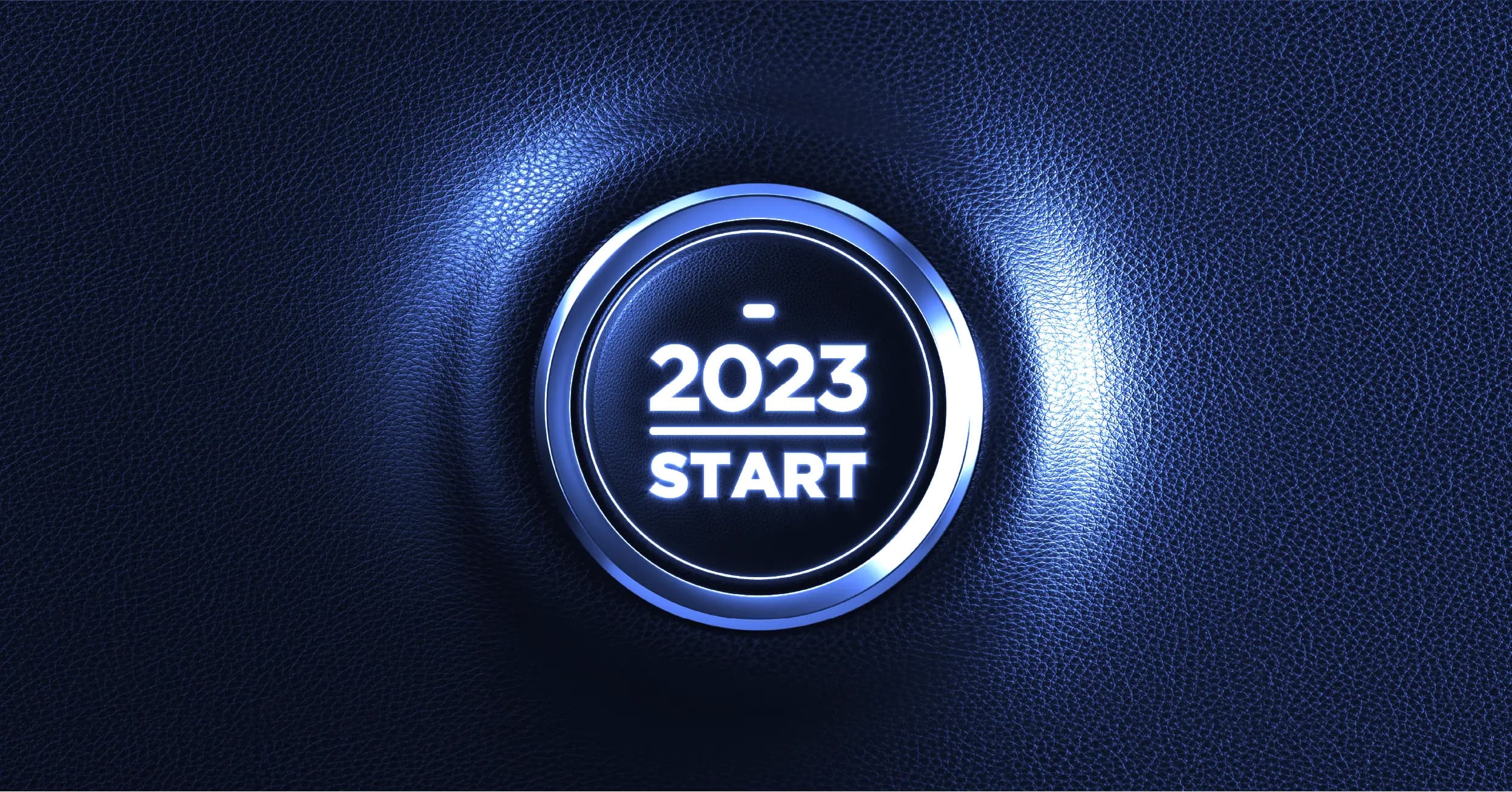
Since 2020, manufacturers have faced several disruptions that have forced many changes in how plants operate. From supply chain slowdowns to worker shortages, not to mention the potential of a recession on the horizon, there’s no question that 2023 will also bring its fair share of challenges.
However, with challenge comes an opportunity for forward-thinking companies that take steps now to mitigate their risks. Today we’re examining five important quality trends in manufacturing to watch in 2023, and how taking proactive steps to improve quality can help companies beat expectations and thrive in the coming year.
Download a free case study to learn how Valeo Wipers reduced quality costs by 50% with EASE’s digital layered process audit software
1. Getting EV Suppliers Up to Speed on Quality
One of the biggest trends to watch this year is how manufacturers address quality with electric vehicle (EV) suppliers new to the automotive industry and IATF 16949. The problem is that EV suppliers have little experience with the process audits required under the standard that act as a key safeguard of product safety. Many OEMs also require suppliers to conduct layered process audits (LPAs), meaning that their tier II suppliers should also be performing these checks.
So how do manufacturers get their supply base to use LPAs to ensure they’re holding processes in place? The first step is to make sure you update your supplier survey to ask if suppliers are conducting LPAs. Manufacturers may even want to go a step further and ask about LPA metrics to ensure that suppliers aren’t just doing them, but actually using them effectively.
2. Connecting the Workforce to Mitigate the Impact of Worker Shortages
According to recent U.S. Bureau of Labor Services (BLS) data, there are currently 746,000 unfilled positions in manufacturing. Finding skilled workers is an ongoing issue faced by the industry, a trend expected to continue for years to come.
In the past, many companies had a sink-or-swim training philosophy that involved replacing workers if they didn’t pick up the needed skills quickly. Today, companies can no longer just replace workers, nor can they afford to lose them when people quit due to insufficient training.
To that end, manufacturers must do a better job of preparing employees to be successful and making them feel safe and valued. More than just beefing up training, conducting frequent check-ins such as with LPAs is critical to showing that management cares about:
- Operators having what they need to do their jobs well
- Following safety protocols and eliminating hazards
- Getting feedback from operators and providing recognition for good work
As we see continue to see manufacturers work to build a more connected frontline workforce, technology is becoming more important than ever to retaining skilled operators. This includes access to training and documentation on the plant floor, the ability to collaborate in real-time with colleagues across the plant or even in another location entirely, and instant visibility into output metrics to let operators know that they are “winning the day.” If manufacturers are not providing these digital resources to their frontline workers, then those operators are likely to seek other opportunities.
3. Shifting Manufacturing Out of China
Where China was once the workshop of the world, today we’re seeing a decided shift in manufacturing to places like Vietnam, Mexico, Turkey, and the Czech Republic. Multiple factors play into this shift, from the higher cost of transportation to Covid restrictions in China.
The implication for manufacturers is that as they identify new suppliers, they need to understand the strength of those suppliers’ quality systems. To that end, companies should conduct a new supplier audit or another assessment system to evaluate suppliers before working with them. The bottom line: manufacturers can either be proactive in determining up front which suppliers meet requirements or be reactive and deal with problems later from unqualified suppliers. Again, looking at key performance indicators (KPIs) around a supplier’s LPA program provides important insight into how the supplier is holding processes in place.
4. Using Software to Link FMEAs and Control Plans
New customer-specific requirements (CSRs) from Ford and General Motors (GM) state that manufacturers must use software to link failure mode and effects analysis (FMEA) to the control plan.
The change stems from the issue that failure modes and controls identified in FMEAs weren’t getting transferred to control plans. Not closing the loop in this manner then creates the opportunity for preventable quality escapes.
The important takeaway here is that the same old manual systems aren’t going to cut it anymore when it comes to competing for OEM business. It’s not enough to simply do an FMEA (or LPAs, for that matter). Instead, OEMs are raising the bar and requiring documentation that you’re not just doing these activities, but doing them in a way that ensures quality.
5. Reducing Scrap to Address High Material Costs
In 2023, improving quality will be crucial for manufacturers to cope with both rising costs and a limited supply of materials. These pressures mean that scrapping parts is more expensive than ever, and not just because the material itself costs more. The bigger problem is that you can’t just replace the parts you scrapped, meaning you may not be able to fill customer orders.
Given these challenges, reducing scrap must be a top priority for companies. Doing so can have a significant impact on profitability, with the potential to save large companies millions. Compared with inspections of finished parts, proactive strategies like layered process auditing helps reduce production defects and scrap, providing a cost-effective method for mitigating the impact of limited material supplies.
Many challenges are on the horizon for manufacturers this year amid the economic headwinds facing the global economy. Strengthening quality processes—and ensuring they are held in place—will be key to weathering the inevitable bumps in the road and helping companies thrive in 2023.