2024 Manufacturing Technology Trends
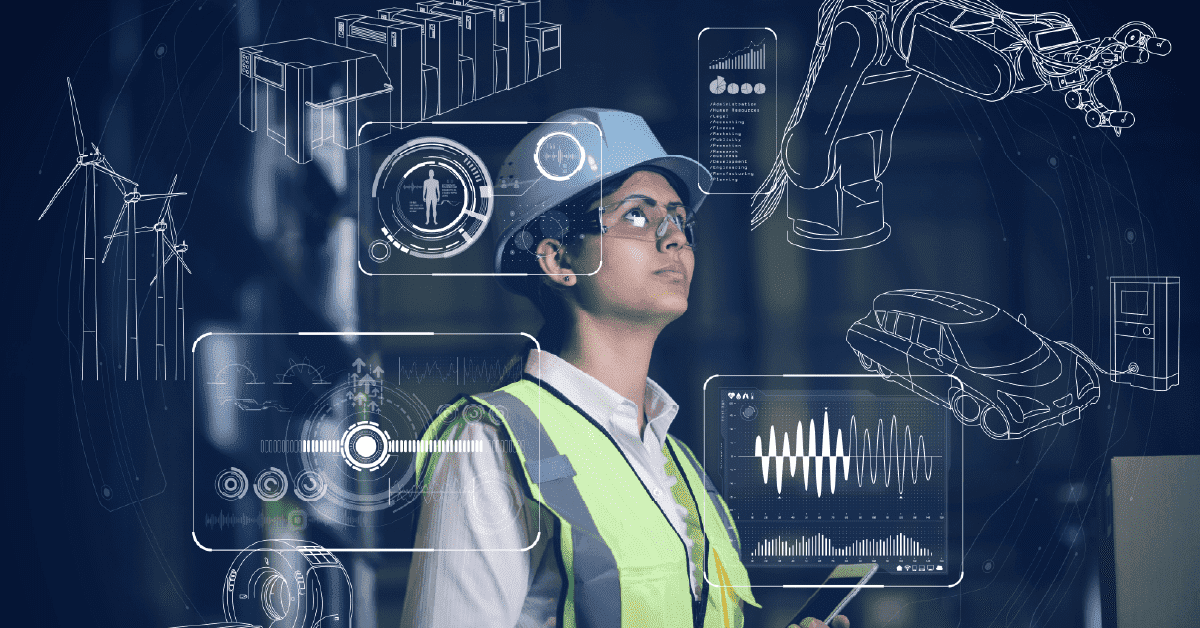
When the Toyota Way was first introduced, one primary goal was to support production through enhanced communication. The Andon light, for example, revolutionized how information was passed between workers at different levels by flashing colored lights to signal departmental support.
This system was beautifully simple, easy to implement and changed the culture from hiding problems to exposing them to support the overall health of the plant. In this way, it shifted the focus away from individual mistakes to problem-solving as a team.
2024 manufacturing technology trends reveal a similar revolution underway, as Industry 4.0 tools gain traction in helping meet the challenges of today’s industrial landscape. Here we discuss some of the most significant trends and how they’re reshaping the future of manufacturing.
Download a free eBook to learn How and Why Digital Safety Inspections Help Manufacturers Work Safer
Connected Worker Adoption Sees Rapid Growth
Connected workforce solutions are quickly emerging as a key solution for addressing a wide range of manufacturing challenges. According to LNS Research, the number of companies with no plans to implement connected worker solutions has shrunk by half since 2020, now representing just 16% of manufacturers.
Just as telling, a full 43% of what LNS Research calls future of industrial work (FOIW) leaders are now using digital tools to connect their workforce, compared with just 20% of FOIW followers.
Connected worker solutions will be critical to tackling the ongoing shortage of skilled workers, giving operators:
- Real-time access to information, procedure checklists and troubleshooting guides to accelerate training
- Remote support from engineering or management to reduce bottlenecks and downtime
- Machine alerts guided by internet of things (IoT) sensors and live production data to minimize defects and equipment issues
- The ability to log issues they see on the plant floor to resolve them faster with fewer resources
AI and Analytics Take Off
Artificial intelligence (AI) in manufacturing is set to explode in coming years. According to Market Research Future, the market for AI in manufacturing was worth just $2.45 billion. In 2030, it’s expected to exceed $53 billion.
Predictive maintenance is one of the top use cases for AI in manufacturing. Using AI combined with IoT sensors, companies can achieve higher productivity, quality and safety with:
- Deep analysis of data on equipment performance and normal operating conditions to identify anomalies that precede machine failure
- Detailed insights into the optimal timing of maintenance and specific needs
- Actionable data for planning maintenance activities to minimize downtime and costs, compared with scheduled or reactive maintenance
- The ability to prevent breakdowns, extend equipment lifespan and strategically plan replacement
AI also has a range of other use cases in manufacturing, from optimizing supply chain operations to energy management, process optimization, quality control and more. IoT sensors combined with AI, for example, can detect defects and help determine when products meet requirements or whether the manufacturer needs to stop the production line.
Additive Manufacturing Becomes a Disruptive Force
Additive manufacturing or 3D printing is another fast-growing disruptive force in manufacturing as this emerging technology becomes less expensive and thus more accessible. Additive manufacturing is forecast to grow 20% annually in coming years, according to Precedence Research, with automotive manufacturing accounting for the largest amount of market share at 20%.
While plastics initially dominated the 3D printing scene, new market growth has been spurred by additive manufacturing that uses metal materials. By 2030, Statista predicts companies will be able to use 3D printing to move beyond prototyping to mass production, eliminating the need for welding and cutting machines.
Other benefits include the ability to:
- Quickly create highly customized products with intricate designs, including customized tooling and jigs
- Reduce waste compared with manufacturing techniques that involve cutting away excess material
- Produce parts on demand to reduce inventories and promote more agile manufacturing processes
- Create lightweight but strong components ideal that improve fuel efficiency and performance, which is ideal for aerospace and automotive products
Remote Audits Become the New Normal
While remote audits initially seemed a temporary measure to deal with pandemic-related shutdowns, they’ve quickly become the new normal. Leading registrars like BSI and Bureau Veritas, for example, now offer remote auditing as part of their ISO certification processes.
Remote auditing provides several advantages over traditional onsite audits, including:
- Fewer onsite audit hours
- Reduced costs, including for travel time and expenses
- Less disruption to manufacturing operations
Providing a more streamlined process overall, remote auditing hinges on one key factor: the ability to provide auditors with documentation electronically. Widespread adoption of digital quality tools has made this increasingly easy. For instance, a digital audit and inspection platform allows teams to quickly compile and share data to demonstrate compliance with internal audit requirements of ISO 9001 and other standards.
Similar to how Lean management tools revolutionized manufacturing, 2024 trends signal a new era in improved collaboration and manufacturing efficiency. As Industry 4.0 becomes the dominating force in manufacturing, companies that embrace change stand to make huge gains. More than just advancing their technological capabilities, these companies are redefining how plants work and succeed as a team.