27 Key Manufacturing Quality Metrics Your Plant Needs to Implement Now
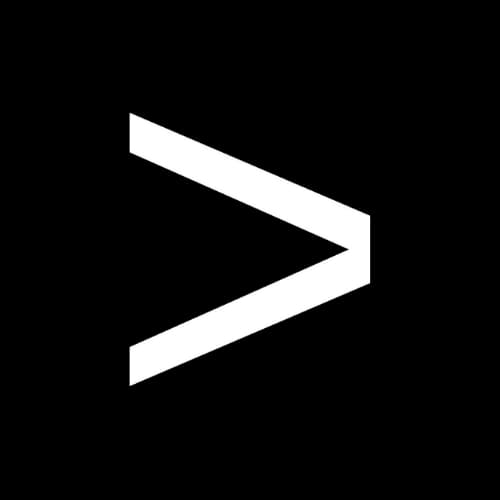

You’ve heard it before: What gets measured gets done. Part of planning to reach an objective is measuring what must be improved in order to move forward—in a word, metrics. Metrics give companies a way to define success and a path toward achieving their goals.
Quality Standards
Plant managers and owners strive to ensure that their plants comply with quality standards. One of the best ways to achieve this is to use metrics.
Employing an array of key metrics can help assure that plant personnel identifies details that ultimately make up the objective and meet the standards quality owners and managers require. Having definite measurements, targets, and planned actions (the first three parts of the SMART mnemonic: Specific, Measurable, Actionable, Realistic, Time-Based) helps achieve the high standards managers and owners set while recognizing that goals that are too lofty often can lead to worker discouragement.
Research over the past few years by MESA (Manufacturing Enterprise Solutions Association) has helped determine the most important metrics that improve safety, efficiency, customer satisfaction, and profits.
Each metric includes multiple components that can assist you in addressing the complexities of the current manufacturing arena. Continuity is required in order to obtain sustainable improvements; the process is ongoing and time-based.
The following list contains a summary of the MESA research that can guide your plant’s efforts in measuring what matters most:
1. Safety
- Reportable safety and health incidents
- Reportable work-area incidents
- Noncompliant incidents per year
2. Cost Reduction and Increasing Profits
- Total cost of manufacturing for every unit (not including materials)
- The cost of manufacturing (aka percentage of revenue)
- Operating profit (net)
- Revenue per employee—how much revenue the plant generates divided by its total number of employees
- Contribution ratio—to calculate this ratio, divide the profit margin the plant generates into a specific unit or production volume
- Return on assets—to determine this financial performance indicator, divide the net income from the plant by the value of the plants fixed assets and working capital
- Cost of energy per unit—the cost of the energy the plant uses to produce a product (or quantity of product)
- Cash to cash time—the duration of time from when the owner(s) purchased the plant’s inventory and when they receive the cash from the sale of the products that the plant utilized to produce the products
- EBITDA (Earnings Before Interest, Taxes, Depreciation, and Amortization)—the plant’s earnings before subtracting any interest, taxes, depreciation, or amortization from any expenses or income
- Perfect order, on schedule delivery, order fill rate—the percentage of times customers received perfect goods, on time, as specified
3. Innovation and Flexibility
- New product—how fast the plant can introduce a new product, includes design, development, and manufacturing changeover
- Product change—how fast the plant can implement a change or changes to an existing product
4. Quality Improvements
- Yield—the number of products the plant manufactures correctly the first time with no reworking
- Customer returns—how often customers return products (or request returns)
- Suppliers—a measure of the useable materials from suppliers
5. Efficiency
- The amount of production throughput—per machine, product line, or the entire plant
- How much of the facility the company utilizes at a point in time
- OEE (Overall Equipment Effectiveness)—this is the product of Availability X Performance X Quality for a piece of equipment or for a production line
- Schedule realization—how many times the plant reached a targeted production level for a given period of time
6. Response to Customer Needs and Requests
- Delivering product to the customer on time
- Manufacturing time—from releasing the order to final production
- Change—switching from one customer product to another
7. Inventory Reduction
To determine the best use of materials, divide the price the company charges for the finished product by the average of the inventory materials the plant uses to produce the product.
8. Maintenance Reduction
- Percentage of planned versus emergency maintenance
- Down time versus operating time
Prove to yourself that metrics works by implementing a consistent, documented program. Do the footwork of measuring the details and publishing the results. Then move forward with confidence and power to achieve the quality standards that your plant is capable of achieving. Attaining those worthy goals gives management and workers alike a sense of fulfillment and confidence to move toward even greater achievements in the future.