5 Main Components of Good Manufacturing Practice (GMP)
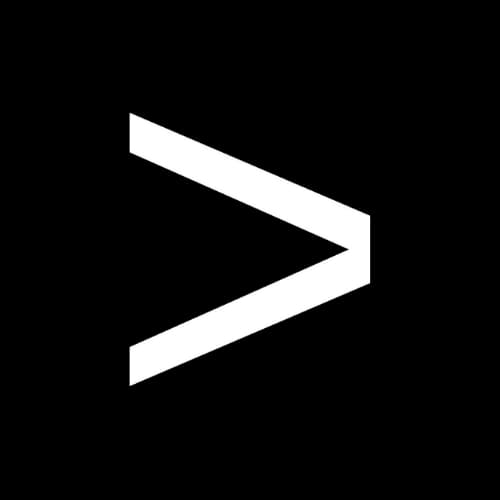
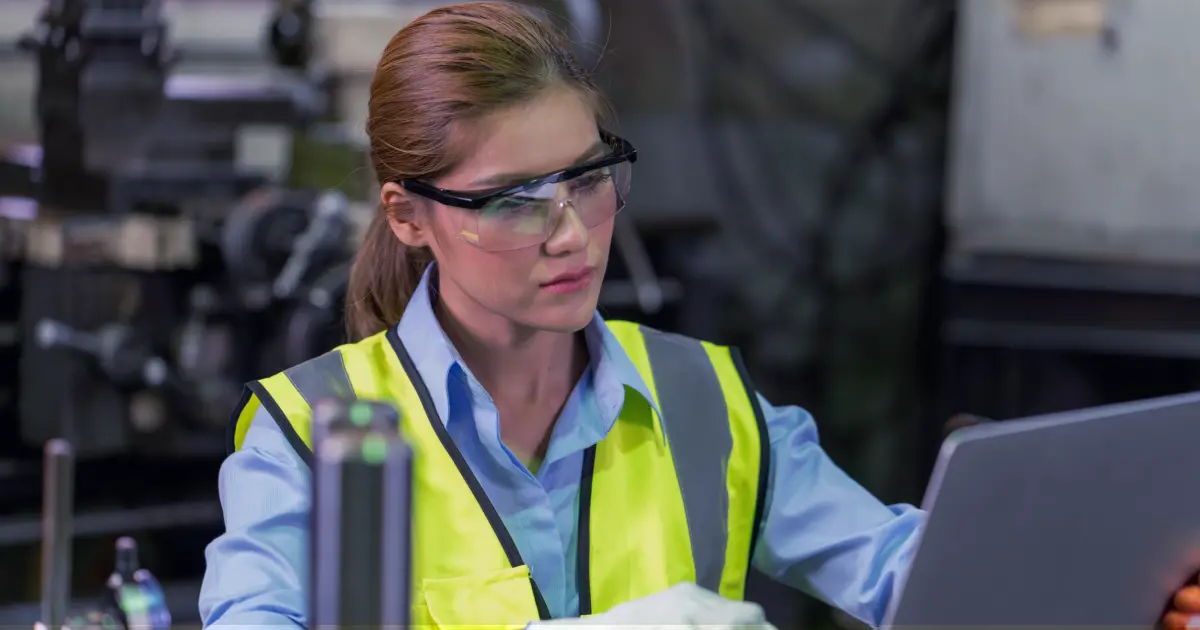
U.S. Food and Drug Administration (FDA) inspections are on the rise again post-pandemic, with the agency conducting nearly 400 domestic inspections in FY 2022, focusing on quality assurance and adherence to quality standards. Good manufacturing practice (GMP) violations are a common thread in warning letters and 483 observations posted online, making GMP compliance a top priority for regulated companies. Therefore, understanding the 5 main components of good manufacturing practice is crucial for maintaining compliance and ensuring product safety in today’s regulatory environment.
GMP refers to a set of processes and procedures that ensure product quality and safety. The FDA requires food and pharmaceutical manufacturers to comply with GMP, also called current good manufacturing practice (cGMP). These regulations are spread across several parts of the Code of Federal Regulations, covering a multitude of individual requirements that can be distilled into 5 main components.
Adhering to the 5 main components of good manufacturing practice can help any manufacturer improve their operations by reducing waste and preventing mistakes that lead to recalls. Let’s take a closer look at each of the components, often referred to as the 5 P’s.
Download your free Root Cause Analysis guidebook for expert tips on top root cause analysis tools
1. People
At the heart of the 5 main components of good manufacturing practice are people. GMP requirements here focus on making sure your people are knowledgeable, skilled and competent in their roles.
Comprehensive training in GMP ensures everybody on your team understands the principles of GMP, such as necessary material handling, sanitation and hygiene practices.
GMP training courses play a crucial role, but it’s also important to recognize the critical role of process and skills verifications. Without having a staff fully trained in GMP—and people checking in periodically that they understand and follow GMP principles—your efforts at adhering to GMP will be wasted.
2. Premises
Premises refer to your facilities where manufacturing takes place. GMP regulations require that manufacturing facilities and equipment are designed, constructed and maintained in a way that minimizes the risk of contamination and quality issues. Sanitation is paramount and goes beyond cleaning practices to encompass how well facilities and equipment are maintained.
In the food industry, for example, facilities must be inspected regularly to identify potential water leaks and places insects or rodents can get into the building. The largest criminal sentence ever in a U.S. food safety case occurred when eight people died and hundreds became sick from salmonella poisoning caused by rodent droppings in peanut butter.
In pharmaceutical manufacturing, cleanroom environments require close control over temperature, humidity and air quality to protect product quality. Condensate dripping from a single exposed pipe, for instance, can introduce contamination into the process.
3. Products
The quality of incoming materials has an enormous impact on the quality and safety of finished products. From a GMP perspective, manufacturers must follow a master formula for products without deviation, as well as follow a strict testing program to guarantee ingredient quality.
For any manufacturer, supplier quality issues present a major risk that should be accounted for within the quality process, including through:
- Supplier qualification processes and requirements
- Conducting supplier audits
- Ongoing monitoring of supplier performance and adherence to quality standards for raw material procurement.
Take, for example, a supplier with a record of previous quality issues. When switching suppliers isn’t an option, increasing inspection frequency and sampling resolution of incoming material inspections can provide a proactive way to detect problems.
4. Processes
In GMP, all processes must be validated and formally documented, with safeguards in place to verify that your team follows those processes and avoids cross-contamination. FDA as well as international standards organizations like ISO require manufacturers to have documented processes covering their operations, quality systems, and best practices for ensuring adherence to quality standards. Remember that in the eyes of regulators, if you didn’t document it, it never happened.
It’s also important to know that you must not only say what you’ll do, but also verify that you do what you say. Verification strategies such as layered process audits provide that added level of security, so that process documentation isn’t just meaningless paperwork but a reflection of best practices and quality assurance.
5. Procedures
Processes are a series of activities to deliver an outcome, while procedures refer to work instructions and standard operating procedures (SOPs) that describe a single activity or task. Standard operating procedures (SOPs) are a crucial component of GMP that provide that added level of security, ensuring manufacturing processes meet quality standards. Again, documentation and verification are both key. Procedures such as SOPs should be evaluated on an annual basis at minimum, as well as anytime you:
- Receive a product complaint
- Use problem-solving tools like 8D or 5 Whys for root cause analysis
- Make changes to products or processes
- Install new equipment in your facility
GMP compliance is an essential tool for not just reducing costs and risks, but also for protecting your company’s reputation and even building a competitive advantage. Training and documentation go a long way toward GMP compliance, with process audits acting as a guardrail to demonstrate your team is adhering to 5 GMP principles.
Read more about ISO quality management principles.