5 Things Quality Leaders Must Prioritize in 2021
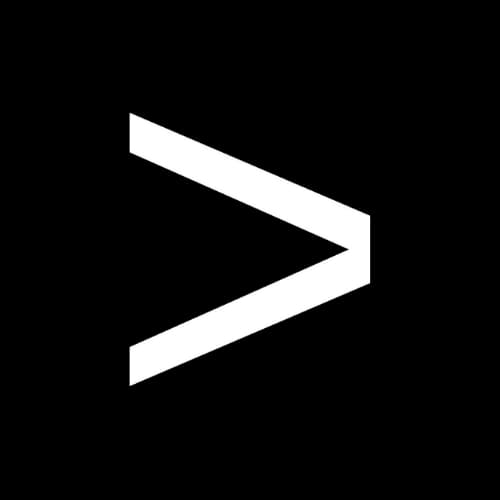
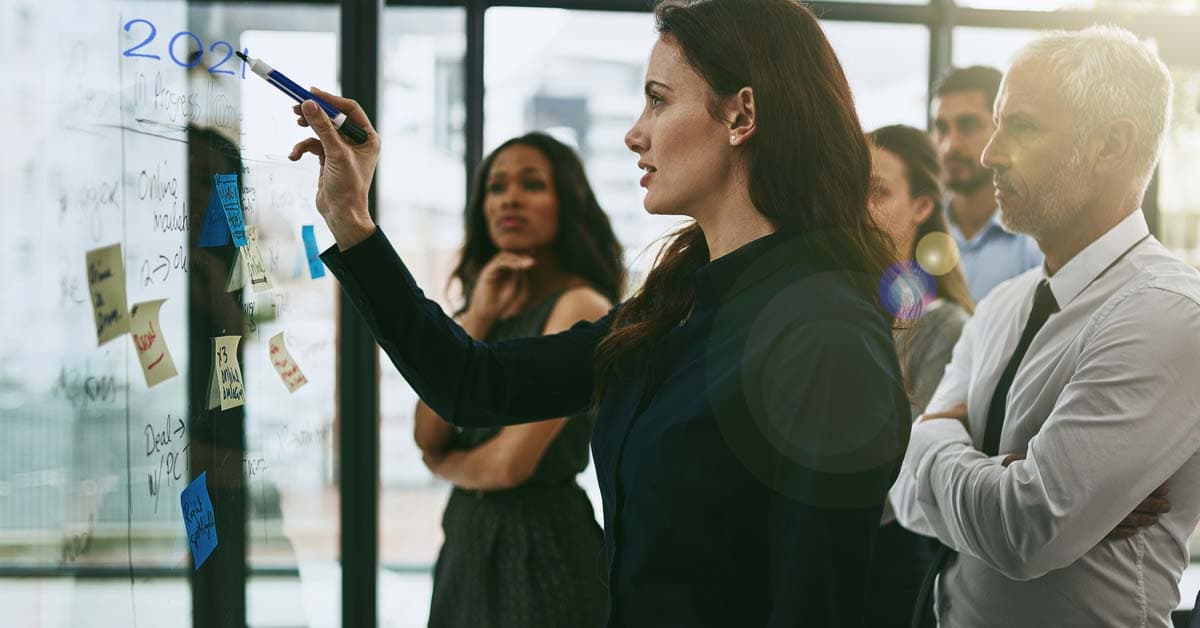
Reuters reports that in November, U.S. manufacturing expanded faster than any time in the past six years. However, production levels are still below pre-pandemic figures, and the recovery has been slow.
These trends combined with growing optimism over COVID-19 vaccines create a mixed picture for manufacturing, and it’s unclear how 2021 will play out.
In any scenario, quality has a large part to play in determining which companies come out strong and which ones will struggle. As we enter the new year, we’re examining what quality leaders must prioritize, and how to meet the challenges to build a stronger, better manufacturing organization overall.
1. COVID-19 Safety
As the pandemic wears on, employee safety remains the number one priority that quality leaders must focus on. Beyond the sizable personal impacts of COVID-19 on workers and their families, manufacturers must also keep in mind the impacts on productivity and potential liabilities and costs.
The General Duty Clause of the Occupational Safety and Health Act of 1970 states that employers are required to provide a workplace “free from recognized hazards that are causing or are likely to cause death or serious physical harm.” The U.S. Occupational Safety and Health Administration (OSHA) has begun enforcing this standard with regards to COVID-19 precautions, handing out more than $3 million in fines so far according to the agency.
It’s also worth noting that, at this time, the latest round of pandemic relief does not include liability protections for employers, underscoring the importance of frequent checks to reduce COVID-19 business risks.
2. Digital Transformation
The second major priority for quality leaders in 2021 should be digital transformation, especially in light of pandemic-related staffing shortages and potential changes in demand.
McKinsey notes that Industry 4.0 adoption is becoming a critical differentiator between “technology haves and have nots.” Accelerating digital transformation is making some companies more resilient to fluctuating market conditions, while those who sit on the sidelines only stand to fall further behind.
One strategy the consulting giant points out is implementing what they call “quick-win solutions” such as technology to ensure safe distancing on the plant floor. Technology like mobile audit software is one example, allowing companies to verify compliance with safety protocols while also reducing defects.
3. Addressing the Talent Gap
A 2018 Deloitte report projected the manufacturing skills gap could put $2.5 trillion in manufacturing GDP at risk through 2028, making addressing the shortage a key priority in the coming year. What’s more, the ability to implement new technologies such as Industry 4.0 relies on having the skilled workers to run the equipment.
Interestingly, while the manufacturing sector has seen recent job losses, many positions still remain unfilled due to the skills shortage. How can quality professionals have an impact on solving this industry challenge? Strategies to consider include:
- Improving compensation packages
- Offering additional training, professional development and promotion opportunities
- Investing in upskilling workers to drive digital transformation
- Incorporating modern technologies to make careers in quality more attractive to the next generation of manufacturing professionals
4. Improving Operational Efficiency
As the manufacturing industry continues to reel from the economic impacts of the pandemic, reducing operational costs will remain a top concern for many organizations. Improving operational efficiency is the key to doing more with less, ensuring companies don’t lose their hard-won gains through indiscriminate cuts that put key goals at risk.
In any manufacturing plant, a hidden factory exists that continually works against standardization, quality and efficiency. A commitment to uncovering hidden factory elements such as undocumented process steps and versioning errors through ongoing verification can improve transparency.
Again, it’s an area where digital technologies can help raise visibility, both in terms of identifying problems and highlighting how quality contributes to overall productivity. Adopting automated technologies such as EASE cloud-based mobile audit software can provide visibility and rapid scaling without major capital investments.
5. Ensuring Quality in the Face of Change
2020 was a turbulent year, and if there’s one thing that’s for sure about 2021 is that it will involve change. Changes in products, changes in how people work together and even potential changes in the trajectory of the manufacturing industry as a whole.
Amid all this change, manufacturers will be faced with the central challenge of maintaining a high level of quality. Product safety and customer satisfaction are as important as ever in the new normal, with the stakes so much higher as companies compete for a smaller piece of the pie.
Managing new products, fewer staff and increased distancing will become a critical capability. Tools like layered process audits (LPAs) can help keep a finger on the pulse of quality while achieving production targets.
All things considered, quality professionals have a crucial role in how the manufacturing industry continues its comeback. By focusing on strategies such as digital transformation, safety, operational efficiency and closing the talent gap, companies can continue to make strides and set a course for operational excellence in 2021.