5 Ways Paper-Based Audit Programs Block Quality Improvements
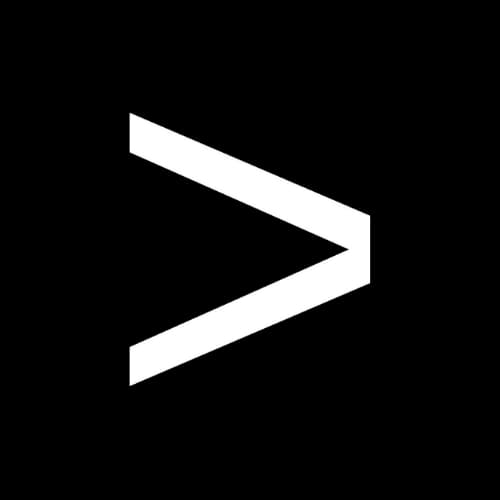
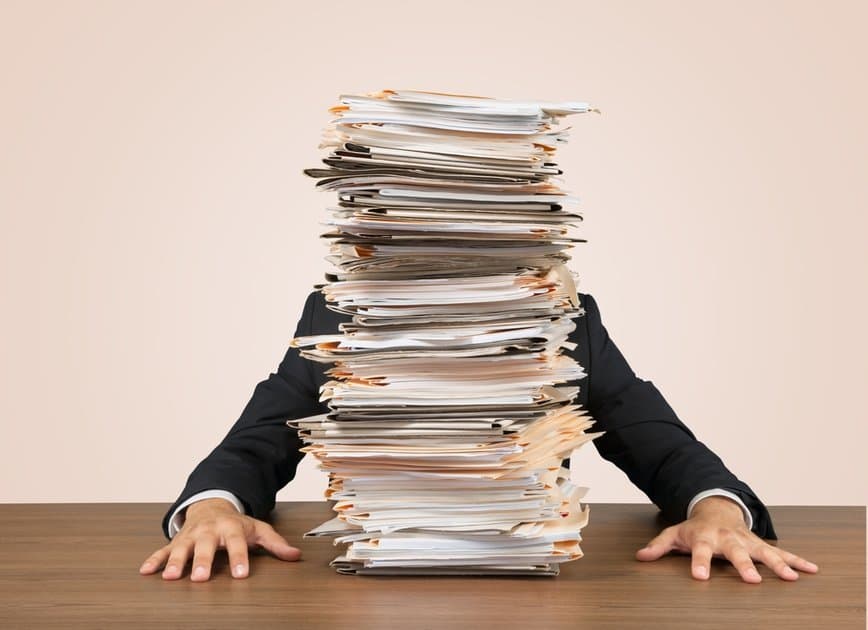
For decades, audit management has centered on paper checklists, with tracking moving to Excel spreadsheets in more recent years. Despite growing adoption of cloud-based manufacturing software, many auto suppliers still rely on paper checklists and spreadsheets to manage audit programs.
There’s a big problem with this approach, however, it doesn’t improve quality – at least not in any sustainable way. In fact, it often adds more costs to quality management – costs that many experts estimate total as much as 20% of revenue for the average company.
In an era of increasing competition among automakers and their suppliers, organizations can’t afford letting these costs stay this high. Part of the problem is that paper-based checklists are inefficient and ineffective for scheduling, data analysis and building a quality culture overall.
1. Inefficient Scheduling
Companies that use manual methods and spreadsheets are at a serious disadvantage when it comes to scheduling for continuous audit approaches such as a layered process audit (LPA) program.
LPAs provide frequent checks of critical processes, engaging the entire organization from operators to top management. Supervisors and team leads conduct audits as often as every shift, while middle management, site leaders and executives perform them at weekly or monthly intervals.
This type of approach increases visibility into high-risk processes identified from sources such as:
- Process failure modes and effects analyses (PFMEAs)
- Customer surveys
- Defects and rejections
A true LPA program involves thousands of audits annually, but our experience shows suppliers that use manual audit tracking only complete about 10% of them. It raises the issue of whether a paper-based system is an LPA system at all, given that LPAs are by definition a high-frequency process.
2. Disjointed Data Management
A paper-based LPA program requires someone to take a paper checklist back to the office and enter results by hand. Hours of manual data entry later, you might have an Excel spreadsheet of items requiring further data analysis.
Not surprisingly, many companies aren’t doing this at all, instead filing away checklists for weeks or months until a customer or third-party audit. This approach runs totally counter to the purpose of audits in general, and LPAs in particular. LPAs have the power to generate predictive insights, but only if you analyze the data while it’s still actionable.
As a result, leading automakers we’ve talked to report growing dissatisfaction with companies that rely on paper-based LPA systems. It’s why suppliers on probation often move to automated systems, helping improve data management and restore their reputation with the manufacturer.
3. Collaboration Roadblocks
Collaboration is another important area where traditional approaches to audit management block improvements in quality. Common problems include issues such as:
- Lack of leadership engagement: It can be difficult to get upper management involved in the audit process. When leadership isn’t a visible presence on the shop floor, your commitment to quality is less credible.
- Siloed functions: Traditional audit programs make quality its own department, rather than something that everyone is responsible for.
- Communication deficiencies: Sporadic, low frequency audits provide few opportunities for people to interact and get feedback. More than 50% of workers report lack of communication as a major barrier to leadership effectiveness, according to a Harris/Interact poll.
4. Poor Data Integrity
Data integrity is a major problem for suppliers struggling to meet customer requirements and demonstrate a high level of quality. Data integrity issues that often result from paper-based or spreadsheet-based audit systems include:
- Pencil-whipping, where auditors automatically pass each item to complete the audit faster.
- Buddy passing when people let their friends slide, a problem solved with LPA programs that keep auditors rotating.
- Overlooked defects that happen when people perform audits on autopilot, which often occurs when the same people are checking the same items over and over.
Audit management software can help with data integrity issues, providing randomized questions and time tracking to see when people are rushing audits.
5. Missed Detection Opportunities
All in all, these audit management issues add up to one big problem, and that’s missed opportunities to catch defects before they reach the customer. The purpose of audits is to prevent problems, and yet the very structure of traditional audit programs stands in the way of this.
LPA programs, when implemented properly, significantly increase the number of checks and interactions among team members. Think of your audit system as being like a sieve for filtering out defects. When you make the mesh smaller by increasing the frequency and plugging the gaps, you prevent issues from becoming customer problems.
Automated LPA software helps you do just that, streamlining scheduling, collaboration and data analysis for detailed, actionable information on quality trends. Ultimately, it’s these capabilities that pave the way for quality culture, also reducing scrap, rework and the customer complaints that threaten your reputation.