5 Ways to Get More from Your Mobile Audit Software
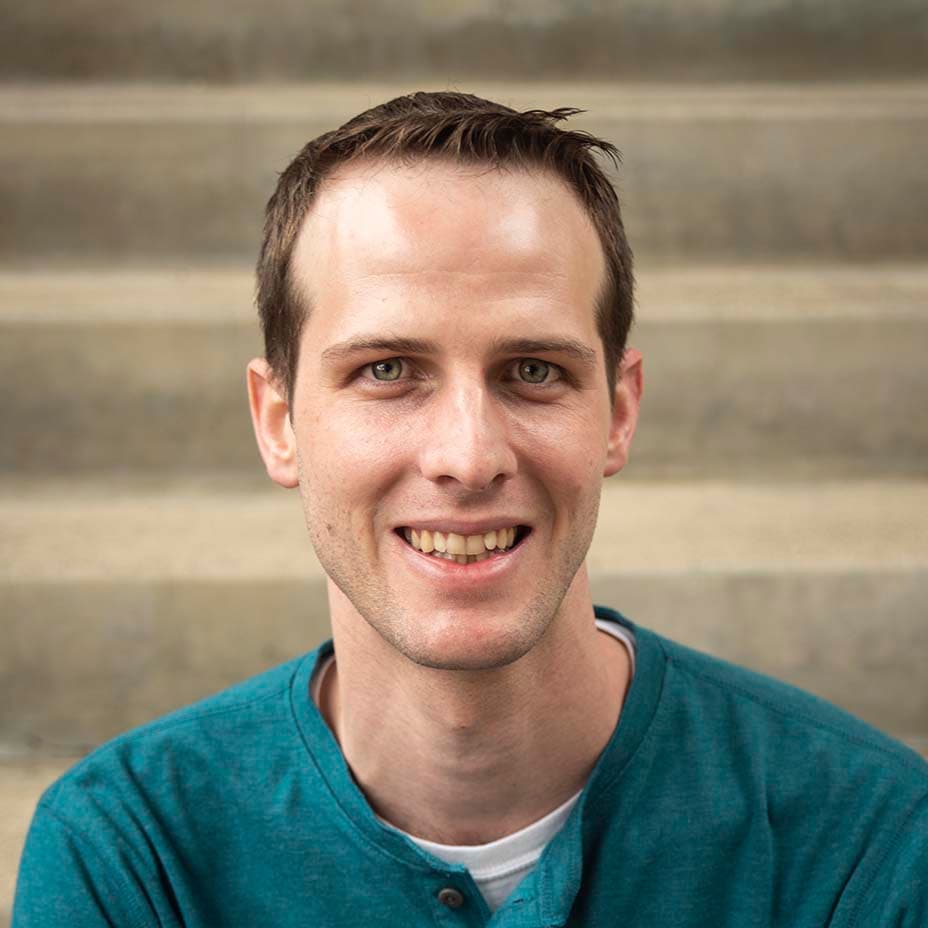
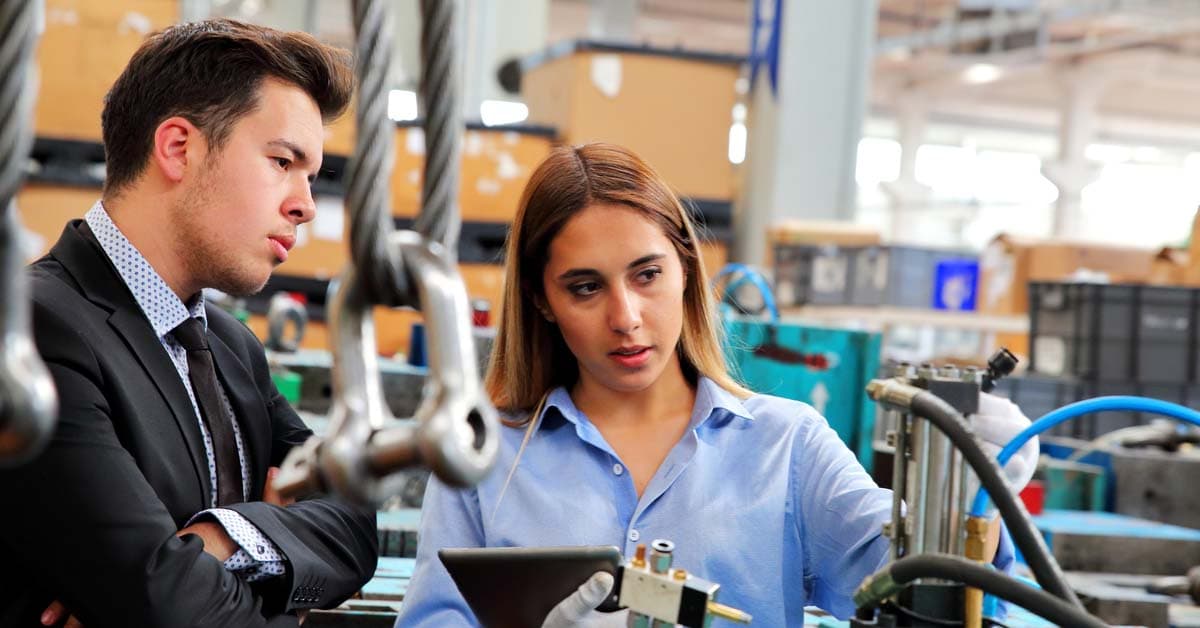
If you’re already using mobile audit software, you may have implemented it to get away from inefficient processes like paper checklists and manual data entry.
But once you’ve got the basics down, how can you be sure you’re getting the maximum value from your investment?
Today we look at how to get more from your mobile audit software, from your data to your question library to improving the audit process. Included are industry best practices as well as user tips to help you root out defects at the source and see what’s really happening on the plant floor.
Get more industry best practices, strategies and tips in our free Ultimate Guide to Layered Process Audits eBook
1. Look Deeper into Your Data
Having customizable dashboards to keep audit data front and center makes it simple to see how your audits are going throughout the facility and track mitigations. If users can generate and share links to dashboards with others or directly to plant floor monitors, you can communicate key metrics and areas of focus even more clearly.
Some examples of metrics manufacturers typically track are:
- Audit completion rates
- On-time audit completion
- Audit pass rates
- Overdue corrective actions
In addition to tracking these data points, companies can get more from their audit data through advanced reporting by:
- Segmenting data in different ways to identify priorities, problems and possible solutions
- Integrating with statistical analysis tools that provide mean, standard deviation, linear regression analysis and even chi-squared tests for improved problem-solving
- Tracking leading metrics that show where problems are likely to occur
- Linking audit data to business intelligence tools for functions such as predictive analysis
2. Write Better Audit Questions
Strong audit questions are the secret to successful audits. Ways to leverage your audit management platform to get better information include:
- Creating specific questions for a group, process or set of equipment investigate specific problems or risks
- Incorporating photos into audit questions to clearly show what is acceptable (or what is not)
- Randomizing audit checklists to prevent pencil-whipping and provide broad coverage of standards
Teams should also periodically review their question library and perform an LPA checkup to update questions and identify any that may be confusing. Clarity is critical. If an auditor doesn’t know what to look for, then the answer itself will be uncertain. And ultimately, that will skew your data.
3. Eliminate the Hidden Factory
The hidden factory refers to processes people are using that are undocumented, often working against quality. Hidden factory processes cost facilities millions or more every year, with the American Society for Quality reporting up to 40% of revenue lost on quality costs in some companies.
Tribal knowledge, where operators have found shortcuts or better ways of doing things, is one example of the hidden factory in action. In these situations, standard processes either don’t exist or aren’t followed correctly.
In some cases, these undocumented processes should be incorporated into standard protocols. In others, they should be eliminated.
So how can you use your mobile audit software to identify these issues? Here you’ll want to focus on:
- Designing questions to focus on how operators perform certain procedures
- Adding checks by multiple individuals (such as with layered process audits) to increase the chances of identifying variation
- Analyzing failed audit questions for patterns to see where standard processes need to be created or updated
4. Find Recurring Issues
One manufacturer has devised a unique method for using the EASE platform to find and fix systemic issues before they cause problems that impact the customer.
The process is relatively simple:
- Questions are tagged by category (e.g., equipment, process and material)
- A separate tag is created for focus questions that are looked at every day
- When a question fails during an audit, its tag gets switched to a focus question for four weeks
What this means is that if a question fails on a piece of equipment, plant leaders are asking the same question of all identical equipment. That allows them to distinguish one-off problems from those affecting multiple areas, helping them fix problems before they impact a large volume of products.
5. Reduce Pencil Whipping
Over time, it’s natural for people to rush through audits. This is especially true if your plant used paper checklists in the past, since repetitive work can often lead people to just check the box.
However, you can use your audit platform to create controls to help you prevent pencil whipping, including:
- Tracking audit times to help you make sure auditors aren’t just running through questions. For example, if you see an audit took just a minute to complete, then that could indicate pencil whipping
- Setting up dummy questions to check if auditors are paying attention. One manufacturer uses the question “Is Daisy Duck Mickey Mouse’s girlfriend?”
- Requiring photos of the observed station during the audit to make sure that the auditor actually visited their assigned station
Getting better data and larger improvements from your audit program may seem difficult, but even small changes can lead to big results. Whether it’s incorporating the industry best practices or user innovations discussed here, or something else unique to your facility, the key is engagement.
Leave the system to languish, and your data won’t be as valuable. Use it to refine your process, and you’ll be able to maximize the value of your audit program.