The Complete 5S Manufacturing Checklist
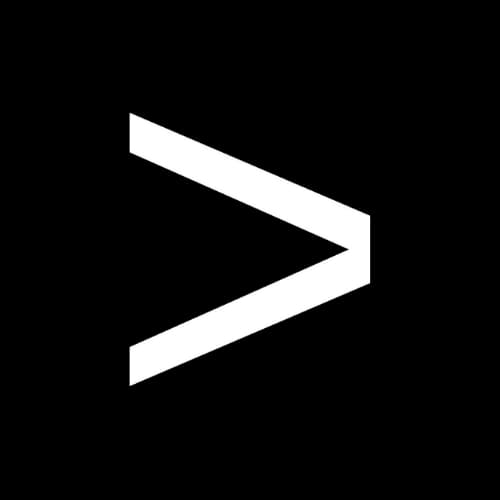
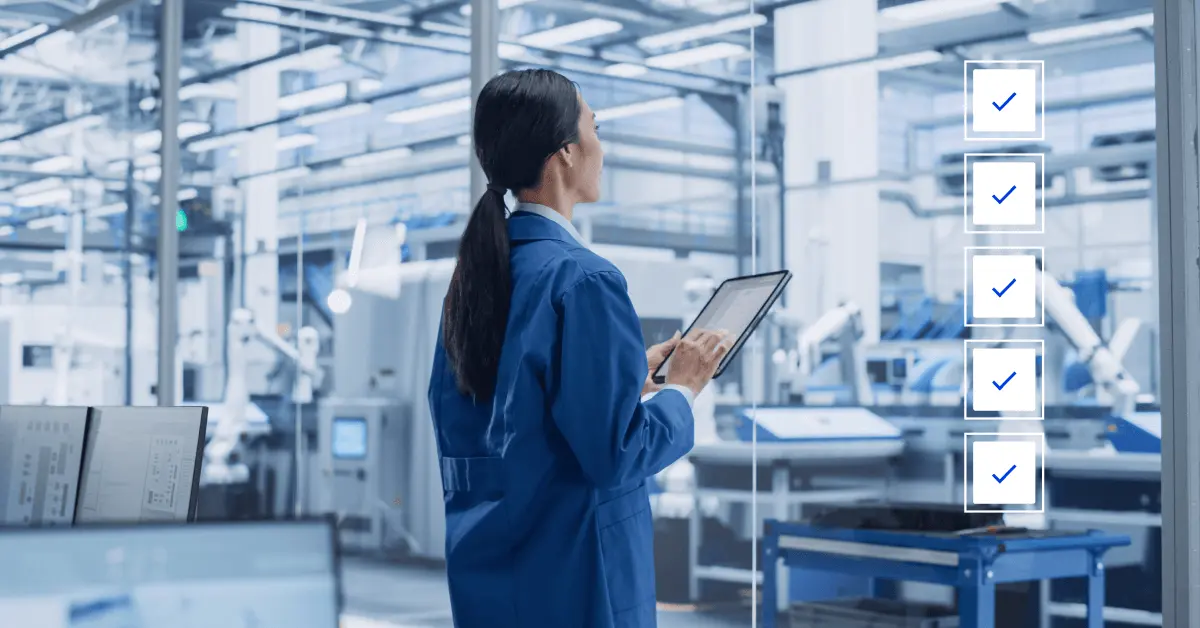
Lean is a well-known concept in manufacturing that prioritizes streamlined, efficient processes to reduce waste, and 5S is a well-known approach to become lean. 5S is often used in conjunction with Gemba walks by area supervisors and plant managers to create and maintain an orderly, more efficient work environment.
While implementing 5S on the plant floor can feel intimidating, there are many practical action items that are fairly straightforward to put into place. The 5S manufacturing checklist below will help you identify what you need to focus on and the steps needed to make your space tidy, efficient, and optimized for productivity.
But first, let’s quickly review the objectives of 5S and why so many companies embrace it in their lean manufacturing journey.
What Is 5S?
As mentioned, 5S is a lean methodology that aims to keep a workstation optimized for efficient production. It originated in Japan in the post-World War II era, and was developed by the Toyota Motor Company as part of its Toyota Production System (TPS). 5S is based on five actions:
- Seiri (or Sort)
- Seiton (or Straighten)
- Seisou (or Shine)
- Seiketsu (or Standardize)
- Shitsuke (or Sustain)
Seiri (or Sort)
Keep only the necessary equipment at the workstation and remove anything that is unnecessary. By reducing clutter, you reduce the time people spend looking for tools and materials. Items that aren’t used frequently—or at all—should be red-tagged and moved to a storage area.
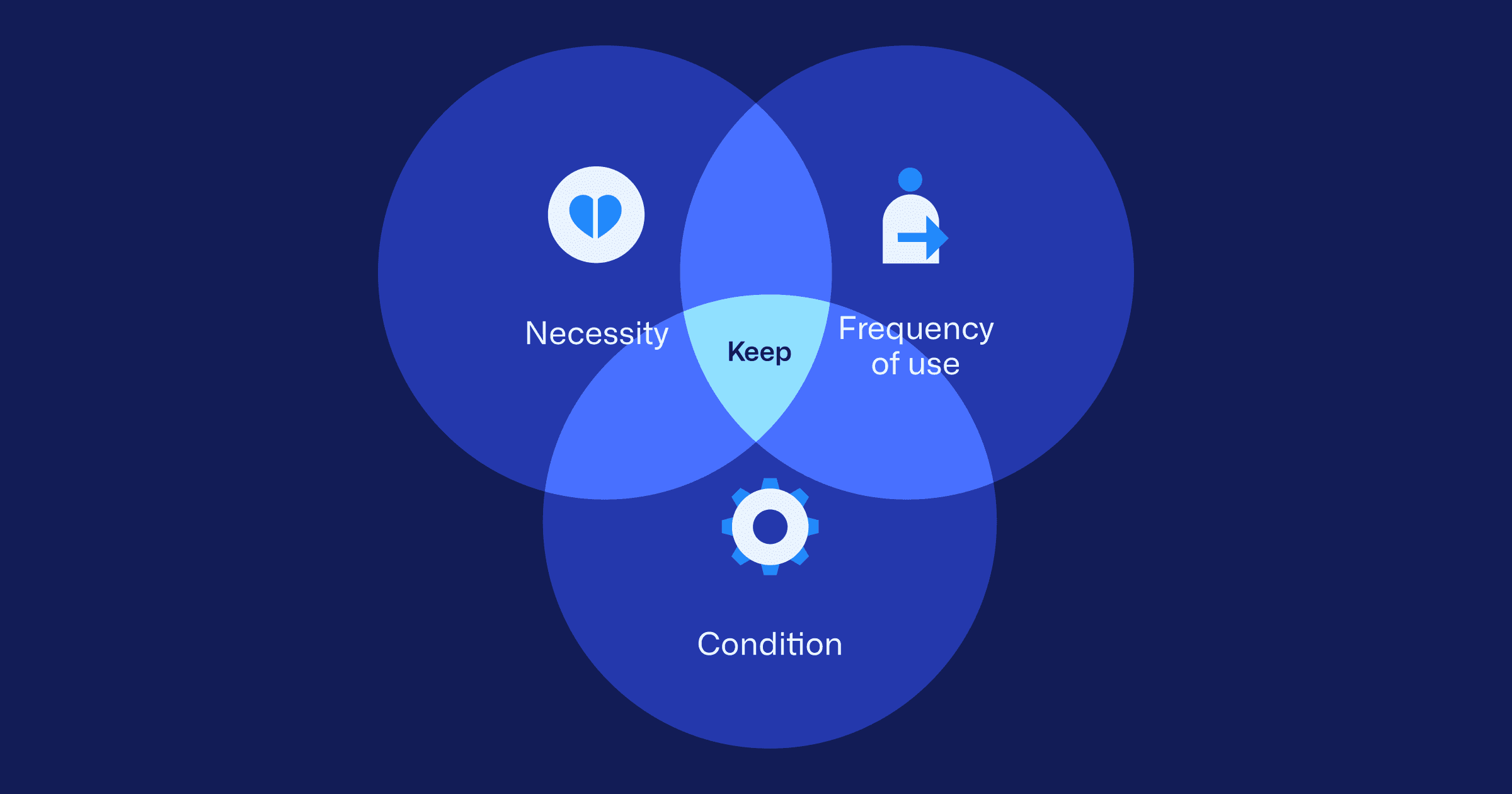
Seiton (or Straighten)
Once the unnecessary and redundant items have been removed, the remaining tools and materials should be set in order. To organize them, you should:
- Create categories and group tools within them
- Tag, label, and color-code them for easy identification and retrieval
- Create visual tools to map their locations so it’s obvious when they are missing
Seisou (or Shine)
Regular maintenance and cleaning of the workstation and equipment help prevent unplanned breakdowns and downtime. Cleanliness reduces the chances of contamination or defects. It also makes it easy to detect leaks and weaknesses before they affect the production process, contributing to continuous improvement.
Seiketsu (or Standardize)
If the processes are consistently the same for everyone, inefficiencies are reduced. Use standard operating procedures (SOPs), visual aids, checklists, and on-the-job training to integrate the first three Ss into the daily routines of your workplace.
Shitsuke (or Sustain)
Maintaining 5S practices over the long term requires work. You need regular 5S audits, training, and team involvement to achieve this. You also need to encourage employee contributions and recognize their efforts to create more engagement and establish 5S as a long-term habit in the work area.
Get our customizable 5S audit template and supercharge your lean initiatives.
The Successful 5S Manufacturing Checklist
While we’ve shared these 33 sample questions to create your own 5S checklist for manufacturing, here’s a version that categorizes, according to each S, specific actions to be performed on the plant floor.
Sort (Seiri): Eliminate Unnecessary Items
- Ensure only the raw materials, tools, or equipment that are essential for current production processes are in the workspace.
- Remove any obsolete parts, materials, or tools that are taking up space in workstations or storage areas.
- Consolidate similar items to eliminate waste and reduce redundancy in your work area.
- Remove or replace defective or damaged items.
- Create a defined process for disposing of unneeded materials or scrapping unusable parts.
- Optimize inventory levels so no excess materials are being stored unnecessarily.
- Remove clutter for production efficiency and safety.
- Identify seasonal or project-specific items that can be stored offsite when they aren’t being used.
Set in Order (Seiton): Organize for Manufacturing Efficiency
- Store tools and materials as close as possible to their point of use.
- Design the production line layout to minimize movement, transport waste, and improve ergonomic efficiency.
- Organize tools, molds, or fixtures for quick retrieval during changeovers.
- Clearly mark and label storage locations for materials, tools, and finished products.
- Prepare appropriate racks, bins, or shelves for materials to prevent clutter on the plant floor.
- Ensure that commonly used items are easily accessible and that infrequently used items are stored elsewhere.
- Organize conveyors, forklifts, or other transport systems so they aren’t causing bottlenecks.
- Ensure spare parts or maintenance tools are available when needed without overstocking.
Shine (Seiso): Clean and Inspect for Manufacturing
- Clean machines and equipment regularly to prevent debris buildup that could cause defects.
- Include inspections for wear, leaks, or damage to machines in your cleaning routines.
- Ensure lubrication points, filters, and other maintenance areas are free of dirt and grime.
- Store and clean hazardous materials like oils, solvents, or waste safely.
- Clean tools and workstations after every shift to ensure readiness for the next team.
- Create a clear process for reporting and addressing cleanliness-related issues.
- Integrate cleaning routines with preventive maintenance schedules.
- Place cleaning supplies where they are needed most.
Standardize (Seiketsu): Document Procedures for Manufacturing
- Clearly document operating procedures (SOPs) for machine setup, operation, and maintenance to support continuous improvement.
- Create SOPs for handling raw materials, finished goods, and work-in-progress items to streamline the audit process.
- Visually mark workstations and production areas for proper tool and material placement.
- Provide employees access to schedules for machine cleaning, maintenance, and safety checks.
- Make sure standard practices are consistent across all shifts to ensure uniform product quality.
- Use color-coded labels or floor markings to guide workflow and storage
- Create a schedule for 5S procedures to be reviewed and updated to reflect changes in production methods.
- Train employees on how to follow and improve these standardized practices.
Sustain (Shitsuke): Maintain and Continuously Improve in Manufacturing
- Integrate 5S practices into daily production meetings or shift change discussions.
- Define how to measure the effectiveness of 5S practices (e.g., downtime, defects, lead time).
- Have supervisors or team leaders conduct regular 5S audits.
- Create visual boards or dashboards that track 5S progress for the team.
- Give employees time and resources to suggest improvements to 5S processes.
- Provide ongoing 5S training that includes practical demonstrations of manufacturing tasks.
- Create processes to ensure employees take ownership of their roles in maintaining 5S practices.
- Recognize and reward team members for exceptional adherence to 5S principles.
- Create and identify actions to address areas where 5S compliance is lacking.
- Incorporate new equipment, tools, or processes into existing 5S standards.
- Identify opportunities to use automation or technology to sustain 5S practices.
5S Audits That Do the Job Right
Just like you have a manufacturing process audit to ensure that the production follows a standardized process, you also need 5S audits that check whether your team is truly adhering to 5S principles. This periodic review tells you whether your 5S implementation was successful, whether it needs continuous improvement, and more, so you can streamline and optimize your manufacturing operations.