The 5S of Lean Manufacturing Principles
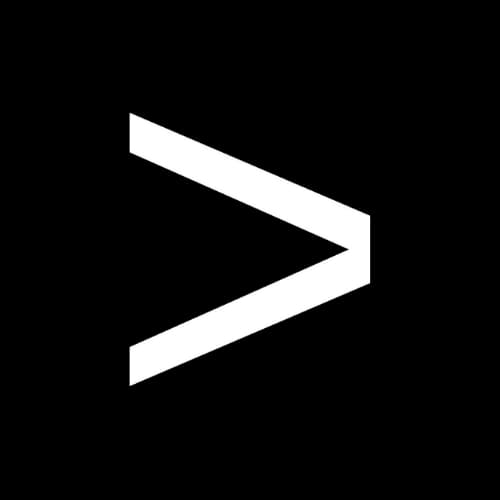
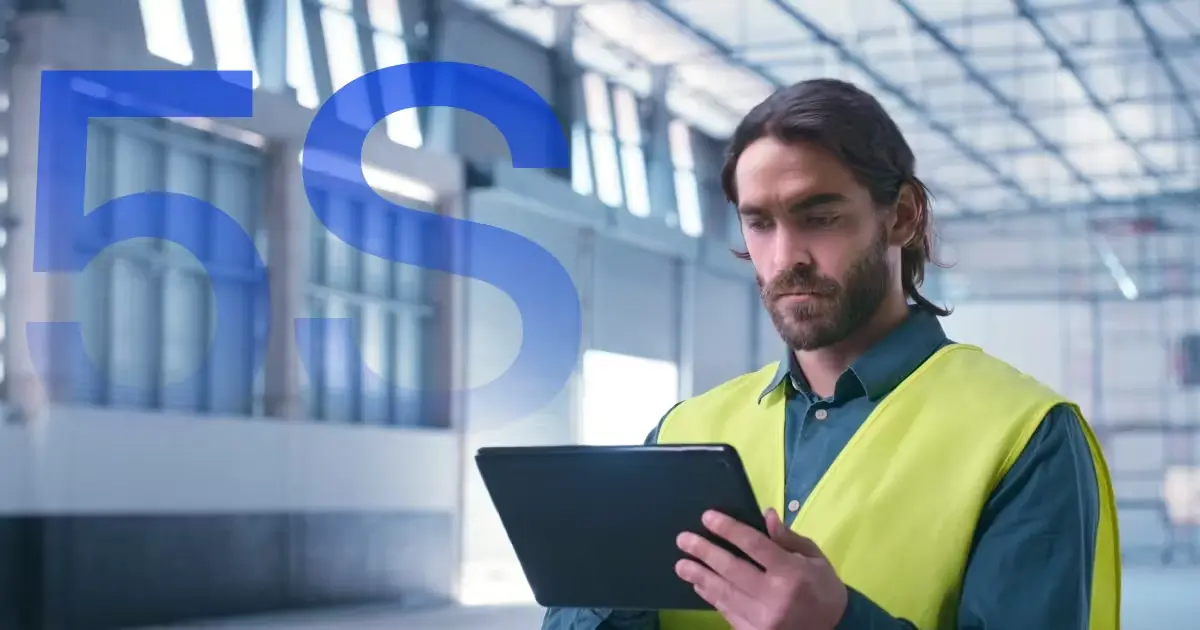
When the Toyota Production System (TPS) was introduced in post-World War II Japan, the world had little idea how it would fundamentally reshape manufacturing. In subsequent decades, TPS concepts spread worldwide to become what is now known as Lean Manufacturing.
The guiding principle of Lean: trimming the so-called “fat”—that is, anything that doesn’t add value—is the key to streamlining operations and ensuring customer satisfaction.
5S lean manufacturing methodology is a core Lean tool built around the idea that an orderly work environment is essential to efficiency and productivity. Today, 5S is prevalent in industries spanning automotive manufacturing, pharmaceuticals, medical devices and more.
In this guide, we provide an overview of 5S of Lean manufacturing, exploring concepts such as:
- How and why to implement 5S of Lean manufacturing
- How to perform 5S audits
- Considerations for your 5S checklists and how software can simplify plant floor audits
Learn How to Use Layered Process Audits to Close the Loop on Safety
What Is 5S Methodology in Lean Manufacturing?
5S is a Lean methodology focused on keeping the workspace clean and organized, with the goal of creating an orderly work environment that promotes efficiency, productivity and safety. The 5S’s originate from five Japanese words:
- Seiri – sort
- Seiton – straighten
- Seisou – shine
- Seiketsu – standardize
- Shitsuke – sustain
Read 33 Sample Questions for Your 5S Checklist
Sort (Seiri)
Step one of the 5S process is seiri, or sort, which involves looking at every item in the workstation and removing anything unnecessary from the production process. The goal: keep only what is needed and remove anything that doesn’t add value.
Why is this important? By decluttering the workspace, plants can streamline their processes by reducing the time spent looking for tools and materials. It also creates more space in the plant for moving about or other production work, further improving productivity while creating a more pleasant work environment.
Here, you want to assess each item in the work area based on:
- Necessity
- Frequency of use
- Condition
Start by identifying all necessary items that will stay in the work area, and returning all items that belong in other work areas. Items that aren’t used frequently—or those you’re not sure if you’ll need—should be red-tagged and placed in a separate holding area. After a period of time, if these materials aren’t used, they can be relocated or disposed of permanently.
Straighten or Set in Order (Seiton)
Seiton roughly translates to straighten or set in order, and involves organizing what remains after sorting so that everything has a designated place and is easily accessible. A well-organized workspace improves efficiency and ergonomics by reducing excess motion, while also boosting productivity and minimizing the risk of errors.
In this step, workstation design is key, ensuring frequently used items are close to the point of use. In addition, plants should look to:
- Group similar items by category and store them in appropriate containers whenever possible to reduce clutter
- Using labeling, color-coding and signage to make tools and materials easy to find and retrieve
- Adding visual tools such as shadow boards that show the correct location for tools, so operators can easily identify when critical items are missing
Shine (Seisou)
The third step of 5S starts with a cleanup campaign covering all workstation tools, equipment and surfaces, as well as performing regularly scheduled equipment maintenance and inspection. Keeping equipment and workstations clean helps prevent machine breakdowns and downtime while extending the life of equipment. A clean workspace also reduces the risk of defects and contamination, making it easier to spot impending problems, such as leaky equipment, before they impact the process.
In this step, you’ll need to create cleaning and maintenance schedules with clearly defined tasks and inspection checklists to ensure tasks are performed at defined intervals. As you engage your team in cleaning up workstations, you’ll want to pay special attention to:
- Any evidence of leaks or spills
- Debris where it shouldn’t be in or around machines
- Overall condition of equipment and tool wear
This process is an ideal time to investigate whether any equipment is in need of repair, and whether tools are in good working order.
Standardize (Seiketsu)
Standardize or seiketsu refers to developing documented procedures for making the improvements of the first three S’s a repeatable process rather than a one-time event. This involves:
- Developing standard operating procedures (SOPs) for organizing, cleaning and maintenance tasks
- Determining the frequency needed for each task and establishing a schedule for them
- Use schedules to create daily, weekly and monthly checklists organized by role and shift
- Using visual aids such as diagrams to make 5S procedures easy to follow
- Building kits for tasks such as cleaning so that all necessary supplies are at hand
- Training employees on 5S procedures
By standardizing your 5S practices, they eventually become a habit for your team, and in turn part of your overall culture where everyone has a sense of pride and ownership in the workplace.
Sustain (Shitsuke)
Sustain or shitsuke is centered on maintaining 5S practices over the long term and continuously improving them. Essential elements of this step include:
- Checking off 5S schedules to ensure all assigned tasks are completed
- Performing regular plant floor audits to reinforce 5S practices and provide guidance where needed
- Providing ongoing training and education to reinforce 5S practices with practical demonstrations
- Inviting employees to contribute their ideas on implementing or improving 5S
Recognizing team members for their efforts is also essential to building a culture of engagement where people can see that their contribution makes a difference to quality.
The 6th S: Safety
Some manufacturers have expanded 5S to include a sixth S: safety. The 6S methodology, also called 5S + safety, focuses on identifying hazards and preventive controls to ensure a safe working environment.
As you create your 5S procedures, think about ways to use 5S principles to reduce risks to workers. Examples include:
- Ensuring ergonomic design of workstations to reduce repetitive use injuries—one of the most common types of workplace injuries
- Creating clearly marked paths for equipment such as forklifts
- Posting signage on hazardous machines or adding safeguards such as light curtains to guard operators from equipment
Read 5 Benefits of Implementing 5S Audits at Your Plant
Benefits of Adopting 5S Lean in Your Plant
Implementing 5S in your plant can deliver many benefits, creating a safe, efficient and productive work environment that facilitates continuous improvement and quality culture. Below, we take a closer look at some of the benefits that manufacturers can achieve with a robust 5S program.
Reducing the 8 Wastes of Lean
To see how 5S can positively impact your organization by reducing waste, it’s helpful to understand what is called the eight wastes of Lean. Toyota production chief Taiichi Ohno first described the seven wastes, to which an eighth waste has since been added:
- Transportation
- Inventory
- Motion
- Waiting
- Overproduction
- Overprocessing
- Defects
- Skills
5S addresses several of these wastes, including:
- Motion: Excess motions can be reduced through workstation design and organization
- Waiting: Having clearly marked locations for items helps prevent errors and reduces the time spent looking for tools and materials, increasing productivity overall.
- Defects: A clean, organized work area helps prevent errors and mix-ups, while helping proactively identify equipment issues that can cause defects
Promoting Continuous Improvement and Quality Culture
5S lean thinking help drive continuous improvement and support a culture of quality in a multitude of ways
One of these is by opening up more space on the plant floor that can be used more efficiently for production. When people spend less time dealing with problems related to workstation cleanliness, disorganization and equipment issues, there is also naturally more time to improve your processes.
A core concept of 5S is that everyone in the organization is involved, from top managers down to operators. When operators are responsible for keeping their stations neat and tidy—and when this is part of their daily habit—they become more invested in quality and gain a sense of pride in their contribution to the plant. This supports a culture of quality by involving the entire team in daily practices that help prevent errors and defects while delivering higher quality products.
Creating a Positive Work Environment
When you walk into your plant, what is your first impression? Recognizing that nobody wants to work in a dirty, cluttered environment, management should prioritize 5S implementation as a way to improve the experience and wellbeing of workers.
Consider, for example, the following:
- When the workspace is tidy, operators can focus on their work with fewer distractions, creating a calmer, less stressful environment
- Workers are less frustrated having to sift through clutter to find tools and materials
- A clean plant is more pleasant to work in and gives the team pride in their workplace
- When there are fewer equipment breakdowns and process disruptions, things go smoother and there is less frustration among teams overall
Improving Safety
Committing to following 5S principles can provide a much-needed boost to safety in the workplace, including by:
- Clearing out space for larger walkways and aisles to minimize tripping hazards
- Removing excess tools and materials such as sharp objects in drawers that can cause injuries
- Eliminating leaks or spills that may create slip and fall hazards
- Ensuring equipment is maintained properly to mitigate machine hazards
- Reducing the risk of ergonomic injuries from improperly laid out work areas where employees have to reach or twist for commonly used tools and materials
Boosting Quality Metrics
Companies that implement and sustain a Lean 5S system can build a foundation for improved quality metrics, including in areas such as:
- Reducing defect rates
- Lowering cost of poor quality (CoPQ)
- Improving equipment availability and performance rate
Combined improvements in availability, performance and quality also add up to increased overall equipment effectiveness (OEE), helping plants maximize both productivity and profitability.
How to Conduct 5S Audits
Plant floor audits are critical to success with 5S programs. Some organizations choose to conduct periodic 5S audits, while others incorporate 5S questions into other plant floor audit programs such as layered process audits (LPAs). This strategy often makes sense when supervisors don’t have time to complete separate audits for LPA, 5S or safety.
5S audits should be conducted at the beginning of the shift rather than the end. The reason: if you wait until the end, you’ve wasted an entire shift before identifying the problem, increasing quality and safety risks.
Two particular areas to focus on in 5S audits are missing items and labeling issues. With 5S audits, it’s easier to identify a cluttered workspace with too many items than it is to determine if a basic tool is missing. This is where shadow boards come in, making it simple to identify during an audit if there’s anything critical missing.
Labeling issues are also a concern. This gets back to seiton, or set in order—if you want the operator to retrieve the correct parts in an assembly, those parts all need to be labeled correctly and located in their designated place.
Examples of 5S Audit Questions
As you write your 5S audit checklists, it’s important to keep in mind that checking paperwork is not the goal. Rather, you want to ask high-value questions that allow you to verify 5S compliance and easily identify issues. Below we include some sample questions for each element of 5S to help you get started.
Sort
- Are all materials off the floor?
- Are walkways clear?
- Is the workstation free of clutter?
- Are infrequently used items stored in a separate area or red-tagged?
Set in Order
- Are all tools accounted for on the work cell’s shadow board?
- Are parts clearly and correctly labeled?
- Are parts needing rework stored separately and red-tagged?
- Are aisles clearly marked?
Shine
- Are work surfaces free of dirt and grease?
- Is the machine clean and in good working order?
- Has the operator completed their autonomous maintenance tasks?
- Are labels and other visuals clear and in good condition?
- Are cleaning materials available and clearly labeled?
Standardize
- Have red-tagged tools and parts been reviewed according to the date on the tag?
- Can the operator describe the process for their (daily, weekly) maintenance or cleaning tasks?
- Are visual management tools up-to-date?
Sustain
- Has the operator been trained in 5S?
- Have the most recent 5S findings been corrected?
- Are the most recent corrections still in place?
- Are 5S checks performed according to the schedule?
Safety
- Is the work area free of spills or slick spots?
- Are all heavy items stored down below where they can’t fall on workers?
- Are pathways and emergency exits free of obstructions?
- Is the operator wearing the required personal protective equipment (PPE)?
How to Simplify Your 5S Audits
Using EASE plant floor audit software, manufacturers can create a library of 5S questions that can be randomized into any audit checklist. This allows you, for instance, to create a short 10-question checklist that includes questions on safety, 5S and process conformance—an ideal solution for companies already conducting other high frequency audits such as layered process audits.
Plants can also use software to:
- Schedule and manage audits with just a few clicks, and get immediate reports on findings
- Incorporate photos into audit questions for easy verification of conformance to 5S standards
- Assign corrections, track their completion and escalate issues to managers when people don’t complete audits or corrections
- Log ad-hoc observations such as safety hazards encountered in the plant
How One Automotive Supplier Streamlined 5S Audits
Global vehicle interior manufacturer Eissmann deployed EASE plant floor audit software to help manage its layered process audits mandated under IATF 16949 certification and customer-specific requirements. The company uses layered process audits to proactively address quality issues, but its paper-and-spreadsheet system was extremely time-consuming while getting in the way of visibility.
These quick daily audits incorporate elements of process conformance, 5S, safety and maintenance, but with the spreadsheet-based system, updating checklists would take hours each week. Even changing a single question meant updating 20 documents, from formatting and images to distributing new process-specific checklists at each production line.
The plant chose EASE because of its flexibility and user-friendly interface, as well as the ability to randomize different question types in a single audit. By digitizing plant floor audits, the quality team can now:
- Rotate checklist items drawn from a library of audit questions (5S, process quality, maintenance and safety)
- Add visual standards to questions to streamline audits and make it easy to verify compliance
- Gain instant insights into where nonconformances are happening in the plant
- Assign, track and escalate corrections to ensure problems are resolved efficiently
A well-developed 5S program is foundational to success with Lean, creating a work environment that’s ready for safe, efficient, high-quality work. As with any quality strategy, however, consistency is paramount. Conduct a one-time cleanup campaign, and you’ll surely find yourself back at square one in no time.
Instead, plants must put in place processes to sustain their 5S program over time with an efficient checklist, leading to higher levels of quality and productivity while creating a workplace in which every employee can take pride.