7 LPA Mistakes to Fix Before Your Next Customer Audit Checklist
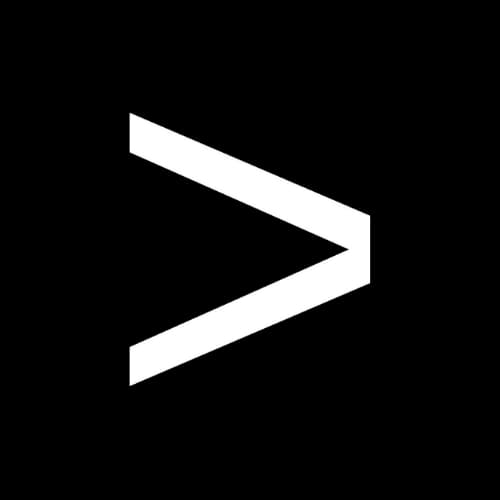
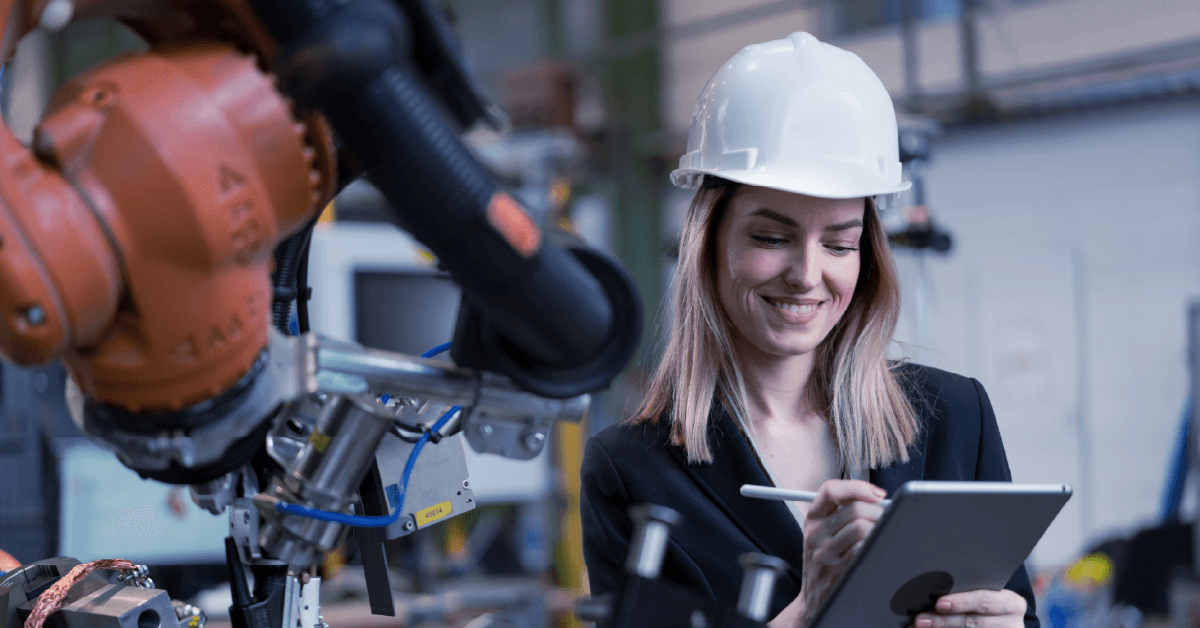
When a customer asks to see your layered process audit (LPA) documentation, will you be ready?
For many manufacturers, the answer is no. Instead of having proof of an effective LPA process, they’re left scrambling for data that show low audit compliance and few actual results. Unfortunately, poor LPA processes are enough to fail a customer audit, which could put your key contracts at risk.
Make sure this doesn’t happen to you by taking a deeper look at your LPA practices from the customer’s perspective. To help you get there, we’ve put together a checklist of 7 critical LPA mistakes to fix before your customer knocks on your door.
1. Lack of Management Participation
One common problem with LPAs is low management participation.
Plant managers and other layer 3 auditors should conduct monthly audits. Quarterly audits simply aren’t enough, sending a clear signal that you don’t have the right commitment to LPAs.
2. Low Audit Completion Rates
Compliance with scheduled audits is a major problem in many LPA programs, particularly those that rely on paper-based or spreadsheet-based tracking.
Strategies for increasing audit completion rates:
- Get management on board to increase accountability
- Send email reminders to auditors that link to checklists
- Notify supervisors of missed audits
3. Inadequate Reporting
If a customer asks to see your LPA results and your checklists are just stuffed in the back of a drawer, you’re going to have problems.
Instead, you should compile and report on findings immediately, using Pareto charts to identify your most significant issues.
4. Poor Follow-Up
Customers want to see you taking action on non-conformances identified during audits. Make sure you:
- Record on-the-spot corrective actions during audits
- Assign corrective actions during or immediately after audits
- Link action plans to failed items for closed-loop tracking
5. Not Addressing Previous Problems
During an audit, a customer may ask how your LPA program addresses previous quality problems. Best practices call for periodically adding questions based on:
- Customer complaints
- Internal defects
- Process failure mode and effects analysis (PFMEA) reports
- Warranty issues
6. Pencil-Whipped Data
When auditors are just rushing to “check the box” on audits, you can’t trust the resulting data. Improve audit integrity by:
- Randomizing questions within checklists
- Rotating items from your question library in your checklists
- Take a closer look at audits that are completed in a very short amount of time
7. Generic Questions
Many manufacturers use the same checklist for every single work area, which tells customers you’re just going through the motions.
Instead, each work area should have LPA checklists customized to the specific process or procedure being verified.
How Automating LPAs Can Help You Pass Your Next Customer Audit
An automated LPA platform solves many common LPA mistakes, helping you:
- Increase audit completion rates with email reminders
- Email links to online checklists users can complete on a mobile device
- Record corrective actions and assign corrective actions during mobile audits
- Access LPA data instantly to spot trends and problems
- Customize checklists for each work area
- Rotate and randomize questions to improve data integrity
- Add new questions to your library to address emerging risks and verify corrective actions are working