8 Documents You Should be Using to Create LPA Questions
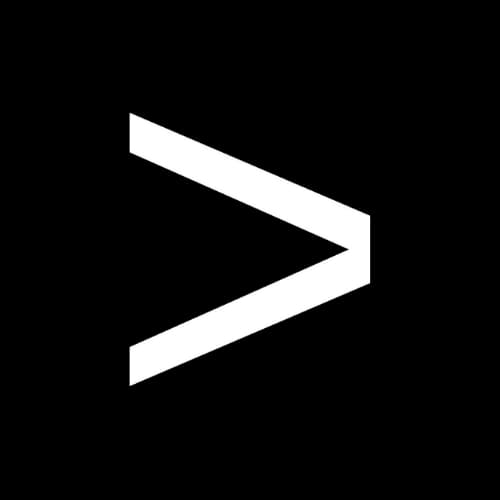
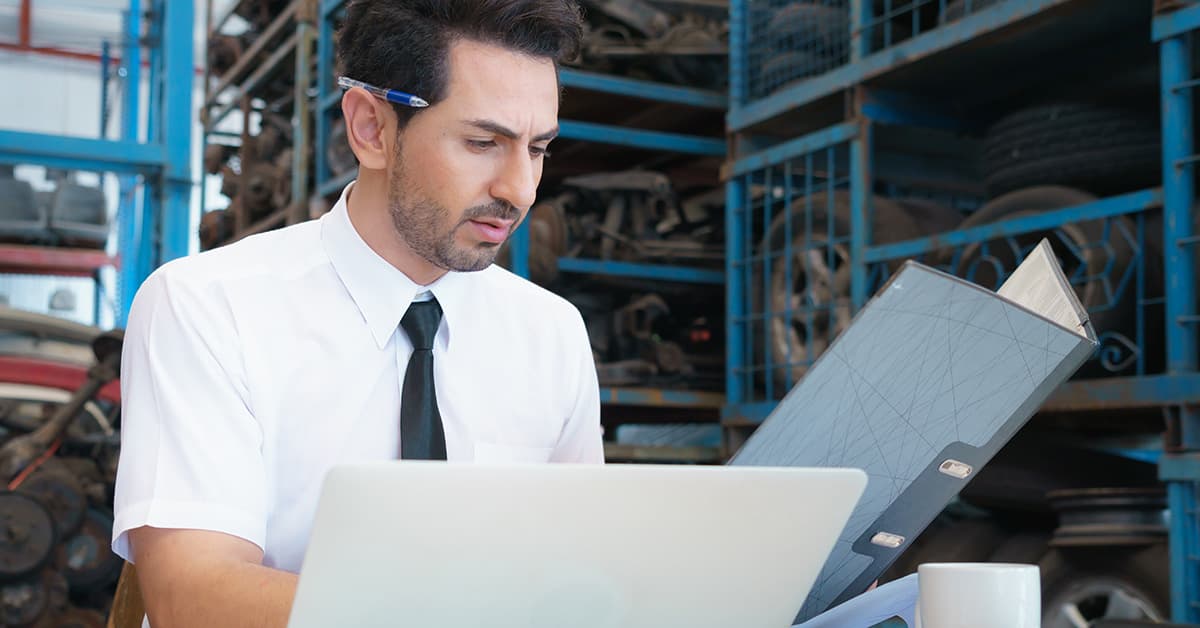
What do customer complaints, scrap reports and standard work instructions have in common?
They all provide insight into quality risks—and where to check frequently to prevent quality escapes. Otherwise, they can quickly become static and outdated if a company does not continually verify that work processes and corrective action steps are adhered to.
Many manufacturers use short, daily audits called layered process audits (LPAs) to reduce defects and catch problems before they leave the plant. The problem is, many rely on the same generic LPA questions, missing quality risks hiding in plain sight.
Today we look at how to avoid this problem by exploring 8 documents to use when creating LPA questions.
Get more LPA tips eBook and best practices with our free Ultimate Guide to Layered Process Audits eBook
Problem-Solving Reports
If you don’t update LPA questions from problem-solving reports, you’re missing risks that could result in serious quality escapes.
For example, let’s say you use the 8D method to uncover an issue with a temperature setting on a specific piece of equipment. Rather than just implementing a corrective action on that one machine, adding an LPA question to all similar equipment can help identify broader systemic issues.
Furthermore, adding an LPA question to ensure the corrective action is followed can also help ensure you don’t have a recurring issue.
FMEAs and PFMEAs
Failure mode and effects analysis (FMEA) is a root cause analysis tool for identifying where problems could occur in your process. Each failure mode or potential problem is scored on severity, occurrence and detection to come up with a risk priority number (RPN).
Process failure mode and effects analysis (PFMEA) works the same way, looking instead at potential failure points in a specific process. You can use FMEAs and PFMEAs to come up with LPA questions to verify controls identified for failure modes with a high RPN.
Work Instructions and Training Materials
Work instructions and training materials are also places to look when updating your LPA question library. Areas to focus on include high-risk steps or those linked to previous quality issues.
However, a word of caution:
You’ll want to avoid questions that ask whether work instructions are posted, since that tells you nothing about whether or not the process is in compliance. Instead, it’s better to ask whether the operator can demonstrate or explain each step in the process, or even point out the most critical step.
This focus will tell you more about whether the operator is confident and has been trained properly, or if further instruction might be needed. It’s also an important consideration in the context of COVID-19, where reorganized production lines mean many employees are working in new areas.
Scrap and Rework Reports
Reducing scrap and rework is one of the biggest benefits of conducting LPAs. It’s also especially important given today’s shortages and shipping delays, where companies can’t afford to let materials go to waste.
For example, you might find that a high proportion of scrap comes from a single process or work area. By digging down into the root cause, you can write questions that help prevent defects and waste.
Downtime Reports
Equipment downtime costs automotive manufacturers roughly $1.3 million every hour. And with manufacturing orders surging, companies need to squeeze every drop of productivity from their plants that they can.
Downtime reports can help pinpoint specific machines that require extra verification, for example if maintenance activities or equipment settings need to be checked regularly.
Customer-Specific Requirements
In the auto industry, suppliers must conform to customer-specific requirements for IATF 16949 certification. Using customer-specific requirements to write audit questions, however, is a best practice for any company that needs to build extra reliability into their process.
Not meeting customer requirements can quickly lead to a complaint. What’s more, they provide insight on what’s important to customers.
Let’s say, for example, you are a supplier to two different original equipment manufacturers (OEMs), each with their own similar (yet unique) requirements for a similar type of part.
To ensure that you don’t get the processes mixed up, using the requirements in your contract or scope of work to create LPA questions helps verify operators follow the right steps. This is precisely the type of situation that led to 15 million wasted COVID-19 vaccine doses at a Johnson & Johnson contract manufacturer’s facility in April.
Process Control Plans
Process control plans outline the key processes to ensure products conform to specifications.
Within this context, you might design LPA questions around whether operators follow the right frequency of specification checks. Note that you shouldn’t focus on product specifications themselves, but whether the operator checks them as described in the process control plan.
Autonomous Maintenance Plans
Autonomous or operator-based maintenance plans describe the steps employees must take at their work station daily, as compared with scheduled or preventive maintenance.
For example, let’s say a welding operator is supposed to use a wire brush to clean off weld slag from their area every time they do a tip change to prevent arcing. Every time they lift the wire brush off the storage board, a clicker logs a count, and the operator records their count on a check sheet to show they did it.
LPA questions here might look at whether they are using the wire brush as indicated, and whether they are recording the count correctly.
In an effective quality process, the documents discussed here aren’t just a paperwork exercise—they’re actually verified to ensure you’re doing what they say you do. LPA software like EASE makes it simple, letting you easily add, rotate and randomize questions for better coverage of risks, while also automating the scheduling process.
And ultimately, that’s where the real potential for results with LPAs lies—identifying risks, adding checks and putting in extra levels of verification to ensure your quality process works.