The Future of Automation in Manufacturing
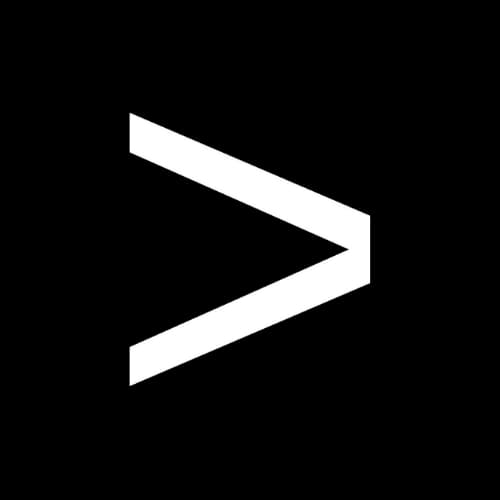
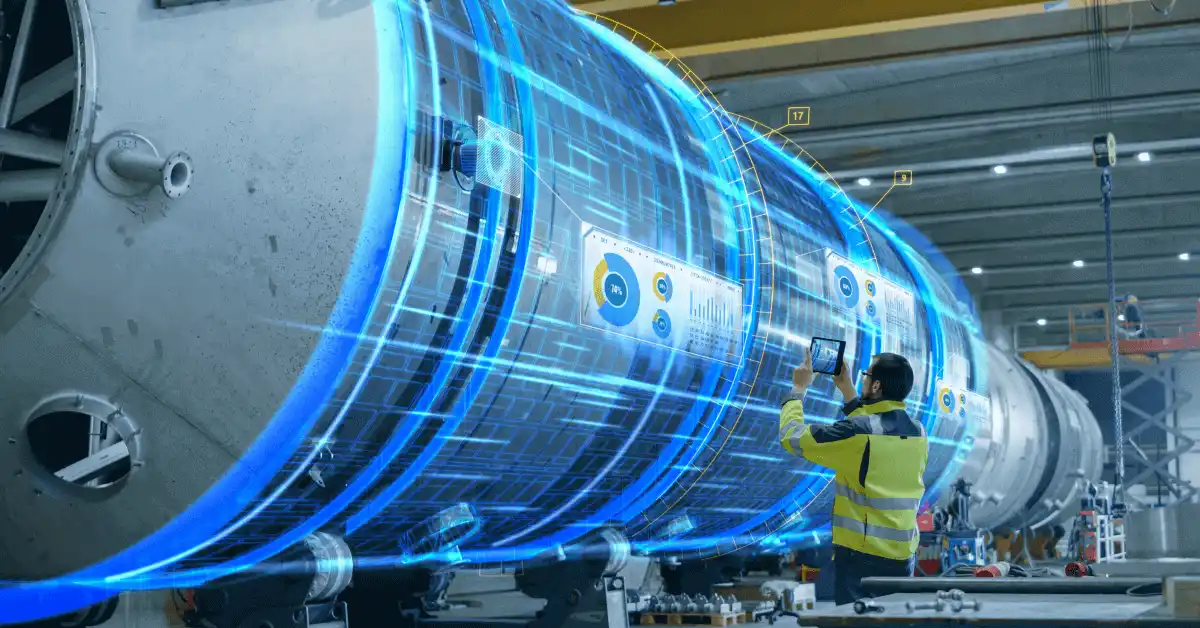
Experts at McKinsey predict that as soon as 2030, advanced manufacturing technology will transform plant floors into what they call “smartphones with robotic arms.”
Over the centuries, automation has been a catalyst for rapid improvements in quality, efficiency, and cost, and Industry 4.0 is no different. Today’s accelerating rate of change in modern manufacturing automation solutions can help companies streamline operations and meet production goals and KPIs, all while delivering more consistent products and ensuring the safety of workers.
At the same time, many systems exist to automate production processes, extending from the shop floor all the way up to enterprise-level business planning. To explore how these technologies are changing the game for manufacturing sector, we’ll look at:
- he history of automation used in manufacturing businesses
- The five levels of automation in manufacturing
- Emerging manufacturing automation applications
- Strategies for achieving long-term value with automation and robotics
Learn more about improving efficiency and productivity with our free eBook on The 5S of Lean Manufacturing Principles
What is Automation in Manufacturing?
Manufacturing automation refers to the integration of technology and machinery to handle production tasks independently, with little to no human input. This approach focuses on improving operational efficiency, achieving consistent accuracy, and accelerating production timelines.
By minimizing manual intervention, automation is used not only to reduce costs but also significantly lowers the risk of human error, ensuring reliable and high-quality results.
History of Automation in Manufacturing
The development of automated processes in manufacturing systems spans several centuries, from basic mechanization all the way to today’s smart factories.
Over that time, automation used in manufacturing has been marked by several phases of industrial advancement:
- Industrial Revolution: Beginning in the 18th century, steam engines and water-powered machines transformed labor-intensive processes like textile manufacturing through simple mechanization.
- Electrification and mass production: By the late 19th and early 20th centuries, the introduction of electricity further improved mechanization efforts and reduced the manual labor involved in turning out products. In 1927, Henry Ford’s introduction of the Model T marked a new era of mass production, showcasing hard automation (also known as fixed automation) with standardized parts and processes to enable rapid production of vehicles.
- IT-powered production and robotics: The development of computerized numerical control (CNC) machines and programmable automation via logic controllers (PLCs) enabled automated control of processes, expanding across numerous industries. The use of industrial robots in manufacturing plants also helped dramatically increase production output, efficiency, and safety as robots were integrated into production floors and assembly lines for tasks like welding.
- Industry 4.0: Today we are in the midst of what’s called the Fourth Industrial Revolution, or Industry 4.0. Leveraging technologies that enable machines to communicate and self-optimize, Industry 4.0 is reimagining the manufacturing landscape as we know it. More recently, the potential and application of artificial intelligence (AI) and flexible automation are poised to accelerate progress even faster.
ISA-95: The Different Types of Automation in Manufacturing
The International Society for Automation ISA-95 standard for Enterprise-Control System Integration defines guidelines to help manufacturers manage and share data across different levels of industrial automation.
The ISA-95 model comprises five levels, each representing distinct functions from the manufacturing floor to management:
- Level 0 – Physical Processes: This level represents the physical manufacturing process itself, such as machinery operations or production processes.
- Level 1 – Field Functions:This level focuses on sensing the entire production process, and includes sensors, valves, and devices that collect data or impact production.
- Level 2 – Monitoring and Control:Level 2 consists of control and monitoring systems that execute real-time instructions for machinery based on data inputs.
- Level 3 – Manufacturing Operations Management:This level involves workflow control to optimize coordination of manufacturing tasks and production processes, and includes functions like production scheduling, quality control, and inventory management.
- Level 4 – Business Planning and Logistics: This level includes business planning and logistics functions, like production scheduling, inventory, and supply chain management.
Based on the Purdue Reference Model for computer-integrated manufacturing, the ISA-95 framework defines a common language and architecture for connecting software and technology across the plant.
Now let’s take a look at each of these in closer detail.
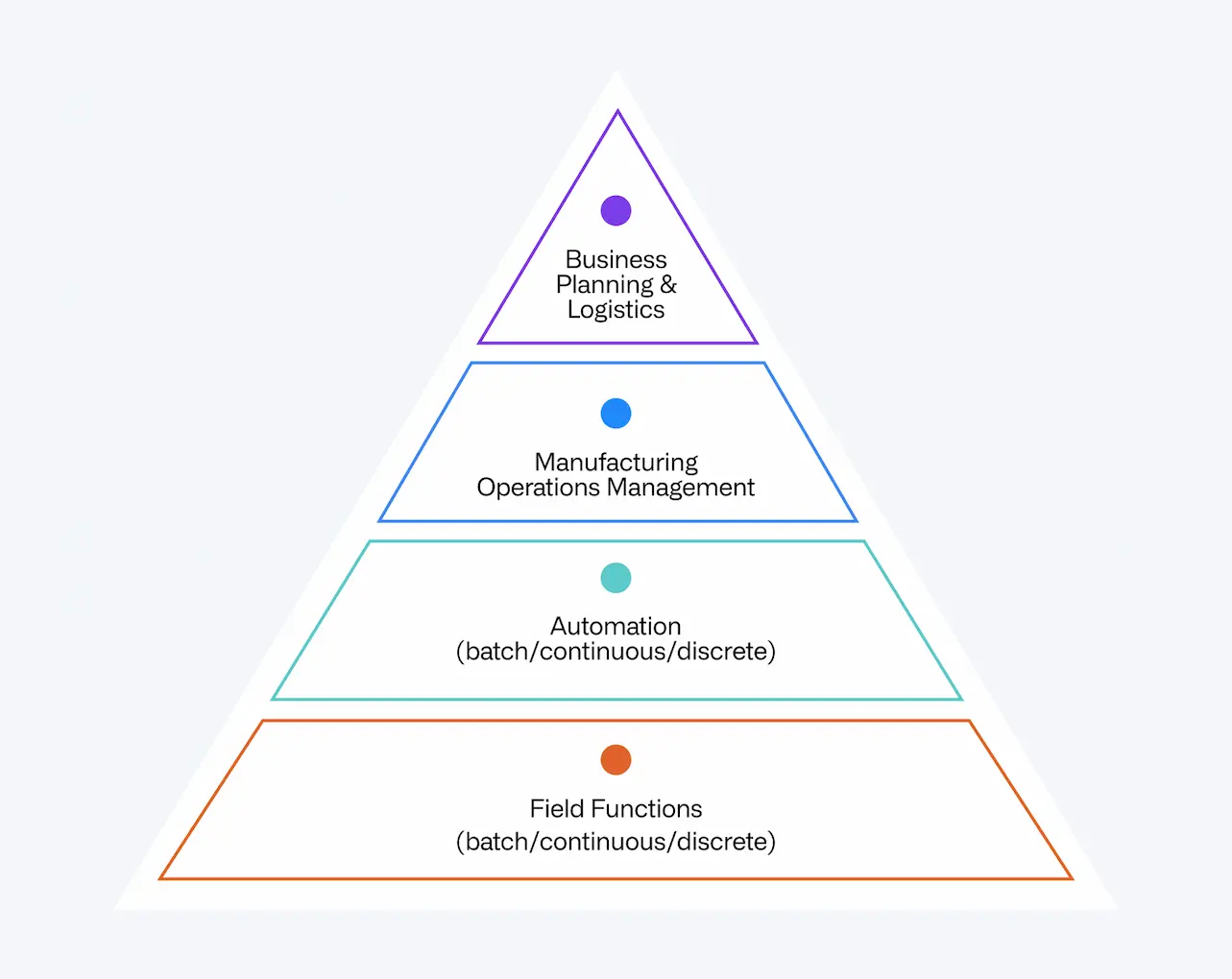
ISA-95 Level 0: Physical Processes
In the ISA-95 industrial automation standard, Level 0 is foundational, representing the physical process itself within the manufacturing environment. This level encompasses all the real-world operations such as machinery, production equipment, and the physical handling of materials.
Level 0 is the point at which raw data is generated, which is then fed into Level 1.
ISA-95 Level 1: Field Functions
ISA-95’s Level 1 in the industrial automation hierarchy focuses on collecting data and manipulating physical processes. This level refers to systems and devices responsible for live data collection and machine operation adjustments, including:
- Sensors (e.g., temperature and pressure)
- Valves that can be manipulated to turn equipment on or off
- Pumps and motors
- Fieldbus systems that allow sensors and devices to communicate with control systems
Data collected here enables immediate feedback mechanisms essential for maintaining production flow and detecting issues such as temperature, speed, or pressure deviations.
This level is foundational to creating stable, effective industrial control environments and serves as the basis for coordination with the supervisory control systems at Level 2.
Level 2: Monitoring and Supervisory Control
Level 2 in the ISA-95 model focuses on supervisory control and process monitoring, where data is managed and analyzed in real time to adjust operational processes efficiently.
This level refers to control devices such as:
- Programmable logic controllers (PLCs) that automate and control machinery and operational processes.
- Distributed control systems (DCSs) that integrate multiple controllers to manage complex, large-scale industrial processes.
- Human-machine interfaces (HMIs) that connect monitoring data to operators who oversee and interact with the process (e.g., starting and stopping machines, responding to alarms or adjusting process variables).
The primary role of Level 2 is to oversee and optimize the operations happening on the factory floor in real time, with the goal of ensuring consistent production quality and responding swiftly to any issues. These systems gather data from sensors and machines, providing operators with critical information to make immediate decisions about equipment status, productivity, and quality.
Unlike the higher levels, which concentrate on planning and management, Level 2 is directly engaged with the operational process itself, connecting operators and engineers with essential production data.
Level 3: Manufacturing Operations Management
ISA-95 Level 3 centers on manufacturing operations management (MOM). It serves as the bridge between the real-time production activities at Level 2 and the broader business and planning functions at Level 4.
Level 3 systems coordinate production processes, including:
- Scheduling
- Resource management
- Quality control
- Maintenance operations
- Workflow management
One of the primary functions of Level 3 is to handle work-in-progress (WIP) data and ensure traceability, meaning that production activities are tracked to meet both regulatory and quality requirements. It also ensures timely transitions between workstations across the production line, particularly when dealing with different products or a new product launch.
A manufacturing execution system (MES) is a key part of MOM, though the terms are frequently used interchangeably.
Systems at this level can trigger quality assurance activities or adjustments based on data collected from production, allowing companies to act quickly if an issue is detected in the workflow. By standardizing operations management, Level 3 systems help maintain consistency across processes, showcasing the benefits of manufacturing automation by reducing downtime and increasing responsiveness to changes in demand or unexpected issues.
Level 4: Business Planning and Logistics
ISA-95 Level 4 involves high-level business operations like planning, logistics, and resource coordination to align production schedules with market demand and supply chain requirements. A prime example here are enterprise resource planning (ERP) systems, with activities at this level addressing enterprise-level decision-making and tasks like:
- Resource allocation
- Order processing
- Supply chain logistics
- Forecasting and cost analysis
Integrating Level 4 with manufacturing control systems lets companies align business goals with manufacturing processes, enhancing responsiveness to changes in market demand or material availability.
For example, when production data from Level 3 informs Level 4 planning, businesses can make proactive decisions, such as adjusting schedules to prevent bottlenecks or shortages. This continuous information flow supports a seamless transition between business strategies and live manufacturing execution.
Emerging Applications of Manufacturing Automation Tools
As Industry 4.0 continues to make rapid advances, a number of emerging applications are driving a step change in manufacturing efficiency, quality, and productivity. Below, we look at some of the most significant of these emerging applications of industrial automation.
Collaborative Robots
Cobots, or collaborative robots, are designed to work alongside humans in manufacturing environments, exemplifying the different types of automation available today. Unlike traditional robots that are isolated for safety reasons, cobots can safely share workspaces with humans, assisting with assembly, quality checks, and packaging tasks, making them highly versatile and cost-effective in smaller production facilities.
Digital Twins
A digital twin is a virtual replica of a physical manufacturing process, product, or system. By creating a digital version, manufacturers can simulate and test processes, troubleshoot issues, and predict maintenance needs in real-time to improve efficiency and reduce downtime.
Internet of Things (IoT)
Internet of Things (IoT) refers to physical objects like devices and machinery that are embedded with smart sensors, which communicate with each other and centralized systems.
IoT sensors, for example, can be used to monitor equipment parameters such as vibration, temperature, and pressure to enable predictive maintenance, rather than relying on maintenance schedules or breakdowns. Here, IoT sensors can reduce costly downtime by alerting operators to potential failures before they occur and minimize disruption to operations during repairs.
AI Vision Detection
AI-powered vision systems are used to perform quality inspections by analyzing products for defects. These systems can detect imperfections that may be missed by human inspectors, improving accuracy in quality control and ensuring consistency in product quality, which is a key benefit of implementing automation.
3D Printing
Additive manufacturing, or 3D printing, is increasingly used for prototyping, tooling, and even end-use parts. 3D printing helps manufacturers bring products to market faster, also reducing inventory costs by allowing for on-demand production of spare parts.
Autonomously Guided Vehicles (AGVs)
Many manufacturers have integrated autonomously guided vehicles (AGVs) into their operations to automate material handling and more materials around their plants more efficiently. AGVs also help minimize human error, both in terms of inventory management as well as human-related safety risks associated with traditional forklift operation.
Augmented Reality (AR)
Augmented reality (AR) tools have a number of applications within the manufacturing environment, including:
- Remote training and troubleshooting
- Maintenance and repair guidance
- Assisting operators with assembly
AR overlays virtual instructions on physical equipment, helping guide operators step-by-step through processes that they might not know very well. These tools help shorten training time, speed up complex tasks, and minimize errors, while reducing travel requirements and costs for offsite experts.
Blockchain
Blockchain technology creates a transparent and secure record of each transaction in the production of finished products, starting with raw materials. Experts regard blockchain as a central component of supply chain traceability, enhancing accountability and trust by providing real-time data on a product’s history and material origin.
Cloud Software
As companies continue to move their IT infrastructure to the cloud, cloud-based tools specific to manufacturing are making it easy for companies of all sizes to automate their processes.
Examples include cloud-based solutions for:
- MES and MOM applications
- ERP
- Enterprise quality management systems (EQMS)
- Specialized applications for quality processes like audits and inspections, statistical process control (SPC,) and nonconformance management
Challenges of Automation
There’s no question that automation in manufacturing has unlocked new frontiers in manufacturing efficiency and innovation. At the same time, getting it right presents significant challenges, especially where large or complex automation initiatives are concerned.
So, what are some of the biggest challenges manufacturers should be prepared for along their automation journey? Let’s look at a few of the most significant.
High Initial Investment Costs
The upfront cost of many automation projects is a considerable barrier, especially for small to medium-sized businesses. Purchasing and installing advanced equipment, integrating it with existing systems, and training workers all add up, in some cases delaying ROI and making it harder to secure budget approval.
Workforce Transformation
As automation grows, so does the need for skilled workers who can operate, maintain, and program automated systems. The manufacturing industry already faces a skills shortage, in part due to the Great Resignation, with automation only intensifying the need.
Companies are struggling to find workers proficient in areas like robotics, AI, and data analytics. Bridging this skills gap requires investment in training and educational partnerships, but these are long-term solutions that don’t address the immediate need.
Complex Legacy Systems
Many manufacturing operations are built on legacy systems that may not be compatible with modern automation technology. Integrating new technologies with outdated infrastructure is complex, requiring time, expertise, and in many cases costly customization solutions.
This integration challenge can slow down the automation process and lead to expensive delays when manufacturers don’t address them proactively.
Maintenance and Downtime Management
Automated manufacturing equipment and devices require regular maintenance to ensure optimal performance, and unexpected breakdowns can lead to costly downtime.
Predictive maintenance strategies are essential to keeping complex automated systems running, but effectiveness depends on robust data quality and analytical tools.
Resistance to Change
Any automation initiative is likely to elicit resistance from the workforce. Workers may fear losing their jobs and be reluctant to adopt new technologies, especially when there’s a lack of transparency about how automation will affect their roles.
A strong change management plan that emphasizes how automation may enhance productivity and make workers’ jobs easier, rather than replace them, can help alleviate these concerns.
The Journey: Capturing the Benefits of Automation
Capturing long-term value from automation in manufacturing requires careful planning and a balanced approach.
Faced with an ever-growing number of automation options, a common starting point for many is deciding what to automate. Repetitive, hazardous, or high-precision tasks that machines can handle more efficiently than humans are a key target, freeing up employees for more complex, value-added work.
It’s also important to avoid “shiny object syndrome,” where a solution’s bells and whistles obscure. Ask first what problem you are trying to solve, taking time to compile your requirements and evaluate whether a given solution will truly help you meet your objectives.
In some cases, focused projects such as addressing inefficiency in a particular process or leveraging cloud-based software to solve quality challenges can provide significant benefits without massive capital investments.
Connecting Workers to Automation Insights
It’s worth noting that automation in and of itself is not a silver bullet. The reality is that, as automated systems generate vast amounts of data, there is a widening digital divide between the data that’s created; the data that’s actually needed to drive a specific change or improvement; and the people who need that data.
To capture automation’s full potential, companies must address manufacturing communications challenges to turn data into insights for everyone from the plant floor up to top management.
EASE’s connected worker maturity model views the path to digital maturity as taking place over three distinct stages:
- Creating a digital foundation by digitizing processes
- Connecting your workers to people, data, systems, and equipment
- Transforming operations through seamless information flow and advanced technologies like AI, and predictive and prescriptive capabilities
Automation has long been the driving force of innovation in manufacturing, evolving from simple mechanization to the highly connected and intelligent systems of today. The integration of robotic, IoT, AI, and cloud software is unlocking new levels of quality and productivity, but long-term value hinges on thoughtful strategy and implementation.
Ultimately, manufacturers must find ways to connect the data generated by these systems to the people who need it to do their jobs better.