The Connected Worker: One Platform, a Collection of Tools, or a Larger Strategy?
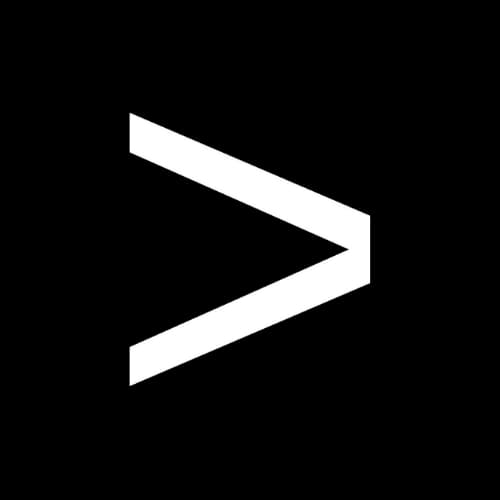
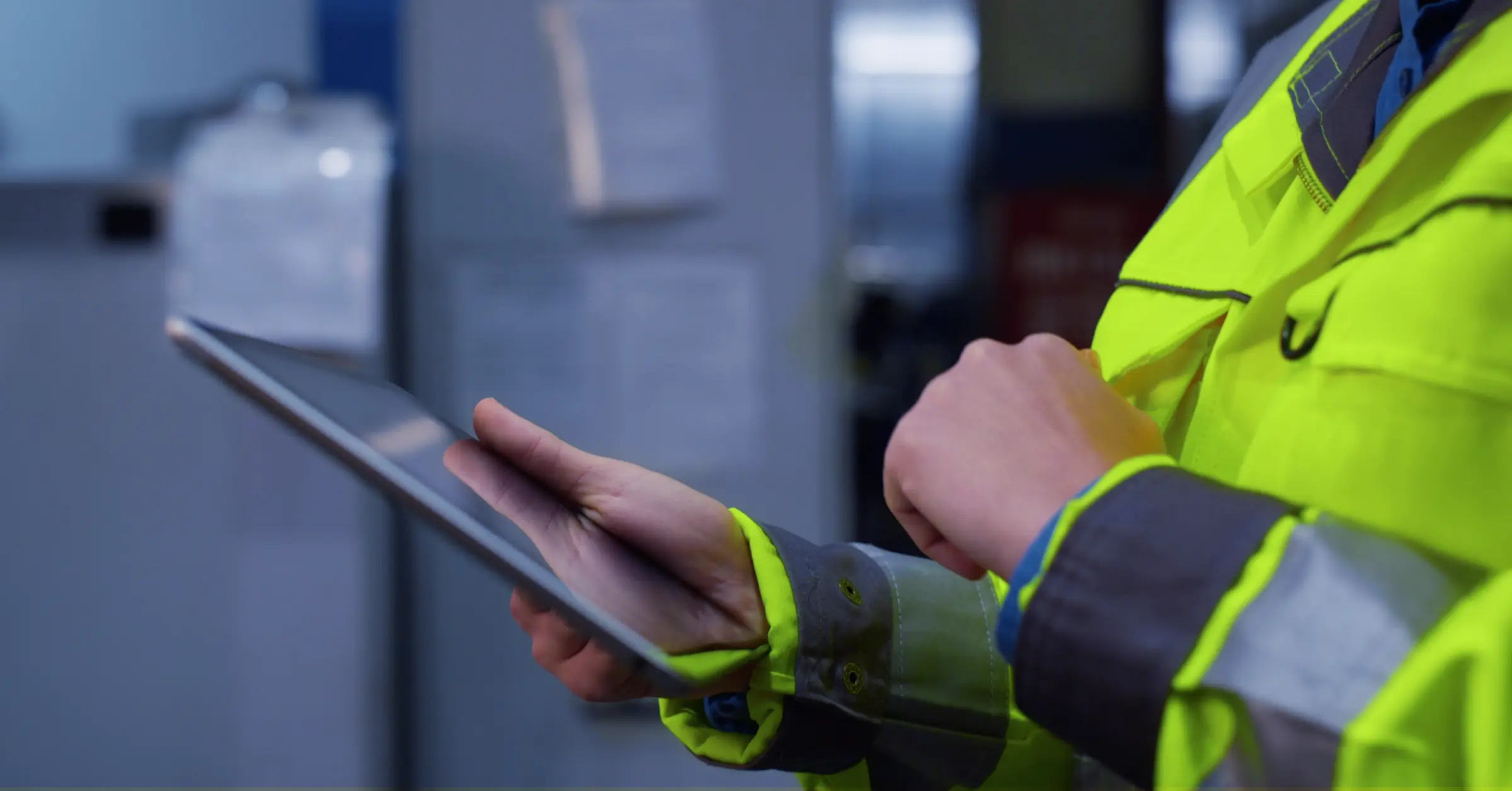
According to analysts at LNS Research, connected worker solutions are manufacturing’s next “must-have” technology, with the number of manufacturers implementing them growing steadily in recent years.
Those who look at connected worker solutions as yet another technology tool, however, are missing the point.
In reality, connected worker is a strategy consisting of multiple tools, all aimed at bridging the digital divide between people, sources of information, systems and machines.
The overarching goal: giving the right people the right information at the right time, so they can make the best decision.
Download your free eBook on Plant Floor Audit Software: Should You Build vs. Buy?
Digital Isolation is Growing
As digital adoption continues its meteoric rise in manufacturing, the stark reality is that it’s the people who are getting left behind. Despite the proliferation of digital tools, many manufacturers still struggle to connect their people with:
- Other individuals in the organization
- Information needed to determine the right path of action
- Systems and machines that provide visibility into operations
What does this breakdown look like on a day-to-day basis?
People must collect data manually and turn in paper records that someone else then transcribes into systems of record. Employees use radios to notify supervisors of a problem on the plant floor. IIoT sensors collect data on machines, but that data isn’t translated into real-time guidance for operators.
In all cases, there’s a distinct divide between when information is captured and when it is needed most, creating inefficiency that stands in the way of operational excellence. Moreover, this digital isolation doesn’t just affect frontline workers—it also impacts business leaders who can’t access the operational insights they need to drive the business forward.
Without the Right Tools, Inefficiency Reigns
When you look at the inefficiencies created by digital isolation, several problems begin to make themselves clear:
- Delayed response: Lag time between information capture and analysis makes manufacturers slow to react to issues, inefficient workflows or performance problems on the plant floor.
- Low process compliance: Lack of access to critical information means operators are often left to rely on their judgment about how to handle unexpected issues. Meanwhile, manufacturers have no way of knowing if work on the plant floor follows documented standards.
- Expertise and skill gaps: Inability to transfer or share institutional knowledge leads to extensive onboarding, over-reliance on experts and variation in quality. What’s worse, the Great Resignation and corresponding brain drain have thrown all of this into overdrive.
- Lack of access to frontline data: Manufacturers can’t easily access paper-based data, nor can they capture critical data on frontline activity. This blocks visibility into the variables impacting production outputs.
So where do manufacturers see the biggest results? Going digital often has the largest impact on the first two, accelerating response to issues while providing better visibility and standardization over plant floor processes.
Finding the Right Tools for Your Connected Worker Strategy
The market has seen a proliferation of tools in the connected worker space, all of which aim to address the underlying breakdown in information flow driving manufacturing efficiency. These solutions include:
- Work execution tools such as digital audit platforms to ensure process compliance
- Knowledge base tools to put information in the hands of those who need it
- Remote expert tools to connect people with others when they need support
- App builders for creating custom software solutions
- Applications that extend access to legacy systems such as ERP and CMMS to the plant floor via mobile device
The combination of tools that make the most sense to implement will depend on what problems your organization is trying to solve. It will also depend, in part, on your overall digital maturity.
The Path to Digital Maturity
Connected worker is a journey, not a one-and-done event marked by a single technology implementation. In our connected worker maturity model, the path from digital isolation to digital maturity takes place over three key phases:
- Building your digital foundation: This step focuses on digitizing work processes and putting the tools in place to connect your workers.
- Connecting your workers: At this phase, the goal is to connect workers to people, information, systems and eventually machines.
- Transforming your operations: In the final step, the foundation you’ve laid allows for seamless information flow and real-time response, layering in predictive and even prescriptive capabilities through technologies such as AI.
Digital isolation presents a mounting challenge for manufacturers pursuing digital transformation strategies. As this digital isolation grows, companies that address it head-on will have a competitive edge over those that leave workers in the dark.
What we’re seeing now with connected worker solutions is about more than just technology—it’s a movement that will reshape the future of manufacturing. One where real-time information flows without bottlenecks, where the waste from information breakdowns is eliminated, and where the full potential of Lean can finally be achieved.