Continuous Flow Production: A Complete Guide
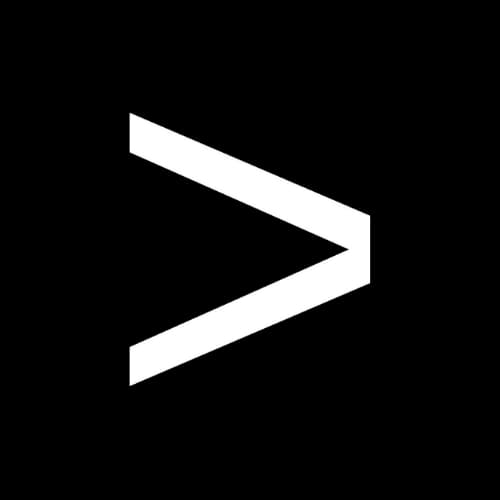
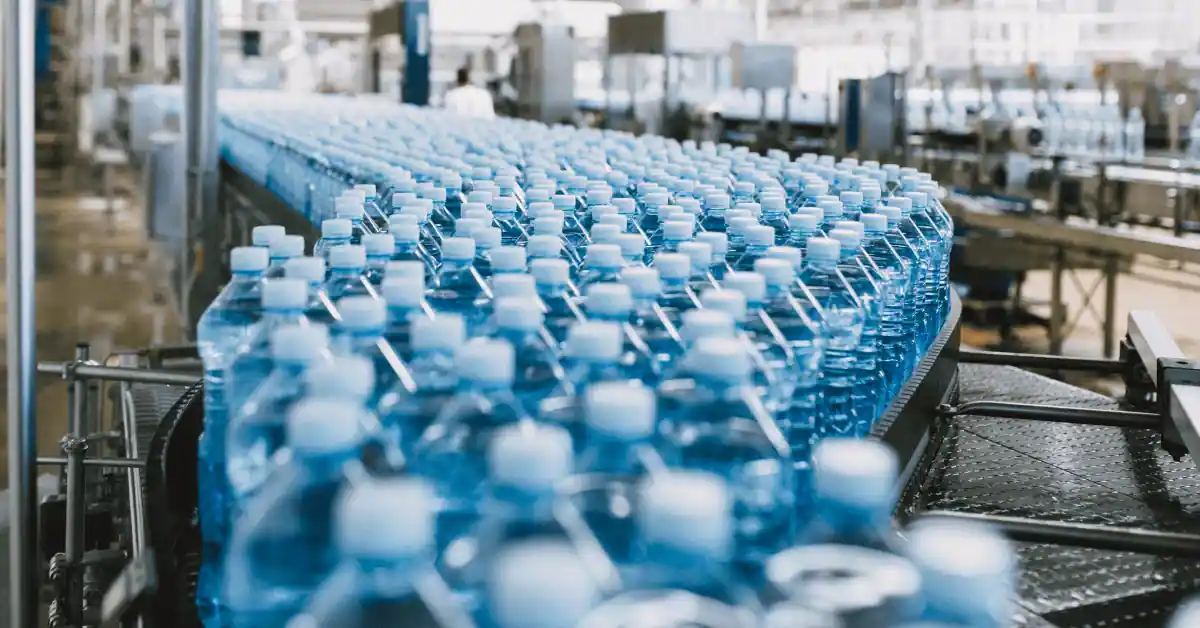
Continuous flow production systems have existed since the Industrial Revolution. Many of today’s manufacturers have perfected this process to improve efficiency and quality in their operations. How do they do it?
Whether you’re new to manufacturing processes or looking to optimize your current operations, this article explores:
- Core characteristics that define continuous flow manufacturing and its key operational elements
- Advantages and challenges to continuous flow production systems
- Process flow design, quality control mechanisms, and relevant industry examples
Continuous Flow Production: Definition and History
Continuous flow production, also known as continuous-flow manufacturing or continuous processing, is a manufacturing method that basically means nonstop production with zero downtime. Think of it as an assembly line that never stops. While technically it can be a manual process, typically, manufacturers rely on automation to keep a constant stream of identical products moving at a consistent pace.
The concept of continuous production emerged during the Industrial Revolution but gained significant prominence with Henry Ford’s assembly line in the early 20th century. Ford’s approach to automobile manufacturing proved the potential of continuous flow processes, and a variety of manufacturers use it today, albeit with more modern technology.
Core Characteristics of Continuous Flow Manufacturing
How do you know if continuous production is right for your organization? An even better question is, how do you know if continuous production is right for your product? It’s a better question because there are three main characteristics of operations that fit into a continuous production model:
- You need to produce a large volume of product every day
- You’ve standardized or can standardize your production process
- Every product is the same
How do you know your standardized processes are being done right the first time? Check out our whitepaper: Improve Production Quality with Layered Process Audits
Manufacturing systems exist on a spectrum: from job shop production where each item is unique, to batch production for items with some variation, to mass production for large-scale continuous operations. Each system has its place depending on product type and market demand.
Let’s examine Ford’s historical example. Continuous flow manufacturing was right for Ford because his cars were in demand and he was producing them in high volume. His company had a system in place where shift changes followed consistent operating procedures, and every car coming off the line was exactly the same.
Batch production is a manufacturing system designed for companies that offer variety in their product and/or have fluctuating demand. The production process consists of discrete runs or lots rather than continuously, allowing more flexibility and variation.
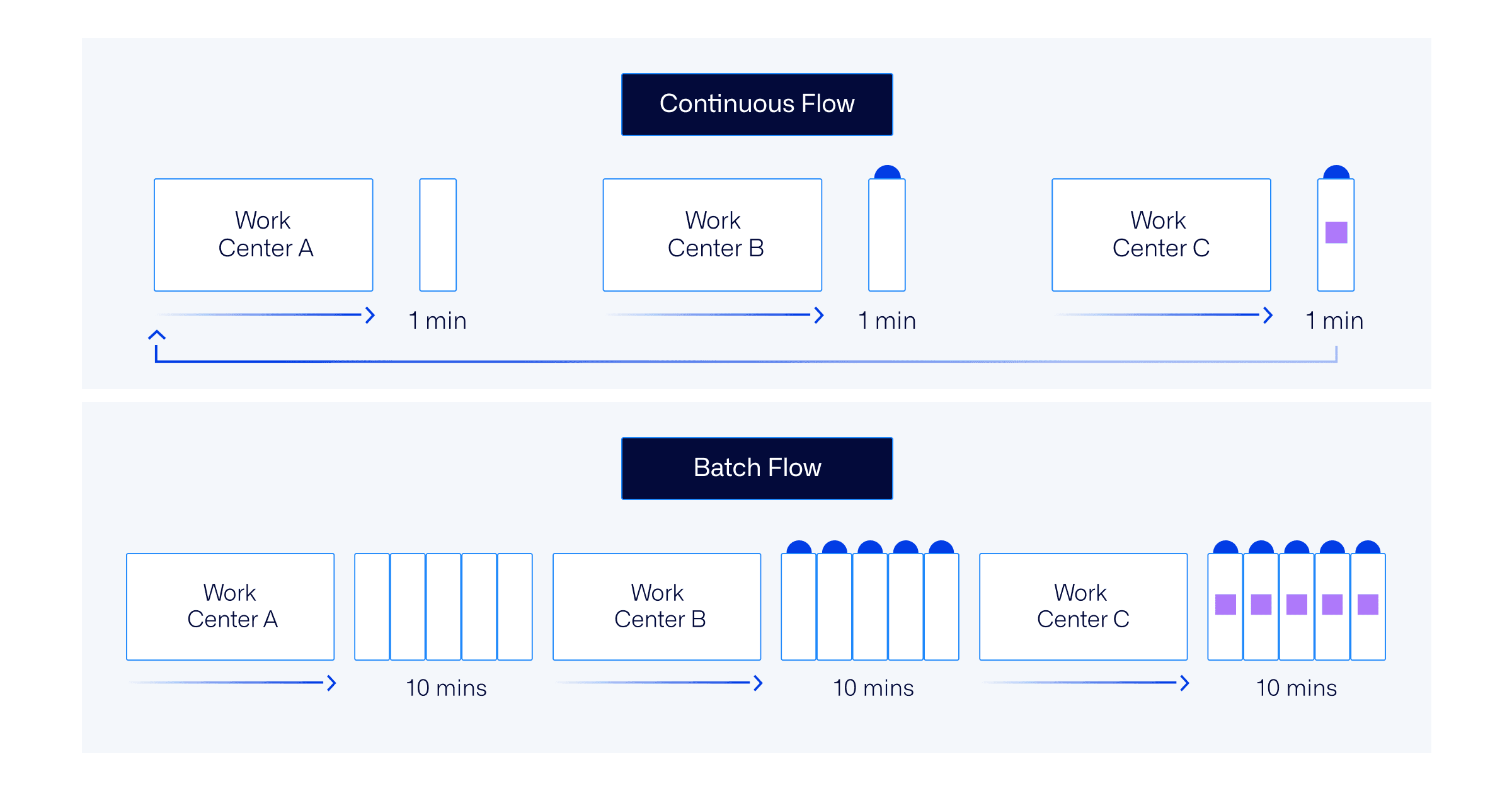
Benefits of batch production include the ability to:
- Tailor products to specific customer requirements while maintaining efficiency.
- Group similar products together, minimizing machine adjustments and downtime between production runs.
- Align production volume with customer demand.
- Adjust production schedules to handle seasonal fluctuations and changing market conditions.
Industries Using a Continuous Flow Process
You can probably guess some of the primary industries using continuous production. Food and beverage products—think soft drinks, condiments, and baked goods—as well as other consumer packaged goods like toothpaste and bath tissue are often made via continuous production.
Then you have materials manufacturing, like paper and packaging production, steel manufacturing, and glass manufacturing.
The pharmaceutical industry has adopted continuous manufacturing for certain drugs, medical devices, and biotechnology products. The FDA has actively encouraged this transition, recognizing its potential to improve drug quality and reduce manufacturing costs.
In all these industries, you’ll recognize the opportunity in continuous flow production to:
- Improve product consistency
- Reduce production costs
- Enhance quality control
- Meet regulatory requirements
Key Elements of Continuous Flow Production Systems
Continuous flow production systems rely on three interconnected elements that work together to ensure consistent, high-quality output. These foundational components—process flow, equipment, and quality control—form the backbone of any successful continuous manufacturing operation.
Precise Process Flow
In manufacturing, process flow is the production line designed to maintain constant movement, with each stage of the product build precisely coordinated with the next.
Equipment and cells/workstations are arranged in a logical sequence to optimize the flow of materials. This matches right up with lean manufacturing principles, which emphasize continuous flow and waste elimination throughout the production process.
A key metric is takt time—the maximum time allowed to produce a product to meet customer demand. Understanding and optimizing time is crucial for maintaining efficient continuous flow.
Equipment and Technology
Continuous flow production relies on special machines and controls. For example, advanced programmable logic controllers (PLCs) integrated with supervisory control and data acquisition (SCADA) systems work together to track and manage many parts of the process at once.
Smart sensors and Industrial Internet of Things (IIoT) devices provide real-time data on critical machine parameters like temperature, pressure, and flow rates.
Robots with AI-powered cameras help with core repetitive manufacturing tasks without interruption, and manufacturing execution systems (MES) track and report on everything being made.
Quality Control
Quality control in continuous flow production operates on two key levels—automated systems for real-time monitoring, and structured human oversight through layered process audits (LPAs).
At the automated level, integrated quality management systems constantly monitor the line, measuring for quality, making necessary corrections, and documenting everything for future analysis.
Digital tools can enhance LPAs by standardizing the audit process, creating accountability, and expanding visibility. Digital LPA platforms turn manual processes into an efficient, closed-loop system. This systematic approach aligns with the Plan-Do-Check-Act (PDCA) methodology you see in many continuous flow manufacturing operations.
Advantages of Continuous Flow Production
Continuous flow production offers compelling advantages in both economic and operational areas, particularly in improving production efficiency. These benefits stem from the system’s fundamental characteristics of non-stop operation, automation, and process standardization. When implemented effectively, you can significantly improve cost efficiency, product quality, and operational performance.
Economic Benefits:
- Lower unit production costs: A continuous operation spreads fixed costs across higher production volumes, decreasing the cost per item.
- Reduced labor costs per unit: Automation and standardization require fewer workers per shift because one operator can often monitor multiple processes.
- Improved energy efficiency: Maintaining steady operations rather than frequent starts and stops uses less energy.
- Better resource utilization: Precise control systems minimize waste and optimize raw material usage. For example, computer-controlled dispensing and processing means less spillage, scrap, and overuse of materials.
- Lower inventory carrying costs: Materials move directly into production, and finished products ship out quickly, reducing warehouse space and storage costs.
Operational Benefits:
- Consistent product quality: Automated systems eliminate human variability, and computer-controlled parameters like temperature, pressure, and timing ensure consistent quality in both continuous flow and batch manufacturing.
- Higher production rates: The non-stop nature of the process means no time is lost starting and stopping operations with shift changes or unplanned maintenance.
- Reduced waste: Precise controls measure the exact amounts of materials needed and can adjust to prevent errors.
- Better process control: Sensors throughout the line can detect and correct variations before they become problems, unlike manual inspections that catch issues after they occur.
- Simplified planning and scheduling: The predictable nature of continuous operations makes it easier to calculate output times and coordinate shipping and distribution.
Challenges and Limitations
While continuous flow production has significant benefits, such as reduced lead times, it also presents challenges in implementation and operation. These challenges arise from the system’s core characteristics of non-stop operation, complex automation, and rigid process requirements. Understanding these limitations is crucial if you’re considering or managing continuous production systems.
Technical Challenges:
- High initial capital investment: Setting up continuous flow production requires substantial upfront costs for specialized equipment, automation systems, and facility modifications.
- Complex maintenance requirements: Equipment must be maintained while the line is running, requiring predictive maintenance programs and specialized repair procedures to avoid shutdowns.
- Limited flexibility for product changes: Continuous flow production does not allow for variation in product features or production flexibility based on demand, unlike batch manufacturing, which can adjust batch sizes.
- Risk of complete line stoppage if one unit fails: The process interconnectedness means a failure in one area can halt the entire production line, impacting just-in-time delivery.
- Need for specialized technical expertise: Operating and maintaining sophisticated equipment requires highly trained personnel who understand both the technology and the production process.
Operational Challenges
- High reconfiguration costs: Changes to product specifications often require significant equipment modifications and line reconfigurations, making it costly to adapt to market demands.
- Precise timing: Unlike batch production, starting up or shutting down a continuous line requires careful sequencing and timing to prevent material waste and equipment damage.
- Costly downtime: When the line must stop for maintenance or repairs, the loss of production time is significant since the entire system must halt, not just individual sections.
- In-depth training and education: Your workers need to understand the entire production flow, the role of automation, and how their work impacts the process.
Future Outlook for Continuous Flow Production
When you look at the future of continuous production, you’ll find several emerging trends shaping the industry.
You can already see the beginnings of remote monitoring operations, where you can oversee multiple facilities worldwide from centralized control rooms. You’ll also have access to modular production systems that provide greater flexibility while maintaining continuous flow.
As manufacturing technology advances, you’ll find new materials and processing methods that will expand the suitability of continuous production.
Here are some key technological advances we can expect:
- AI and machine learning: You’ll be able to enhance your predictive maintenance systems and optimize processes through advancing AI and machine learning capabilities. These tools will help spot potential issues before they affect production.
- Industry 4.0 integration: Many companies are already using interconnected sensors to create digital twins of their production lines. As this technology advances, you’ll find virtual monitoring and optimization becoming standard practice in your operations.
- Advanced process analytics: You’ll gain access to big data analytics that will help identify patterns and optimization opportunities that weren’t visible before. This will further improve product quality and reduce waste.
- Automation systems: You’ll see next-generation robots and automated systems handling increasingly complex tasks. These systems will adapt to changing conditions, reducing the need for human intervention.
- Connected workforce: Connected worker technology is advancing manufacturing by providing the workforce with real-time data from machines, systems, and other sources to help make better decisions on the factory floor.
Continuous flow manufacturing also has important implications on the sustainability front:
- Energy efficiency: You’ll be able to implement smart power management systems that minimize energy consumption during low-demand periods.
- Zero waste initiatives: Precise control systems will minimize overproduction and material loss, while advanced recovery systems will capture and recycle the remaining waste.
- Environmental technologies: New equipment designs will focus on reducing water use, emissions, and chemical waste while maintaining productivity goals.
- Circular economy integration: You’ll need to redesign your production processes to use recycled materials and create products that are themselves recyclable, helping you build closed-loop manufacturing systems.
While continuous production’s core principles of non-stop, standardized manufacturing remain unchanged since the Industrial Revolution, modern implementations are leveraging AI, automation, and sustainable practices to achieve increased levels of efficiency and quality control.
As manufacturing faces increasing pressure to optimize operations while minimizing environmental impact, continuous flow production systems will likely play an even more vital role in shaping its future.