Corrective Action: How to Sustain the Gain
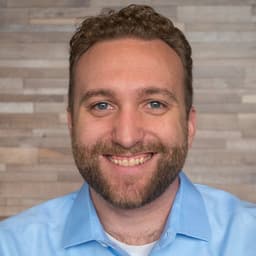
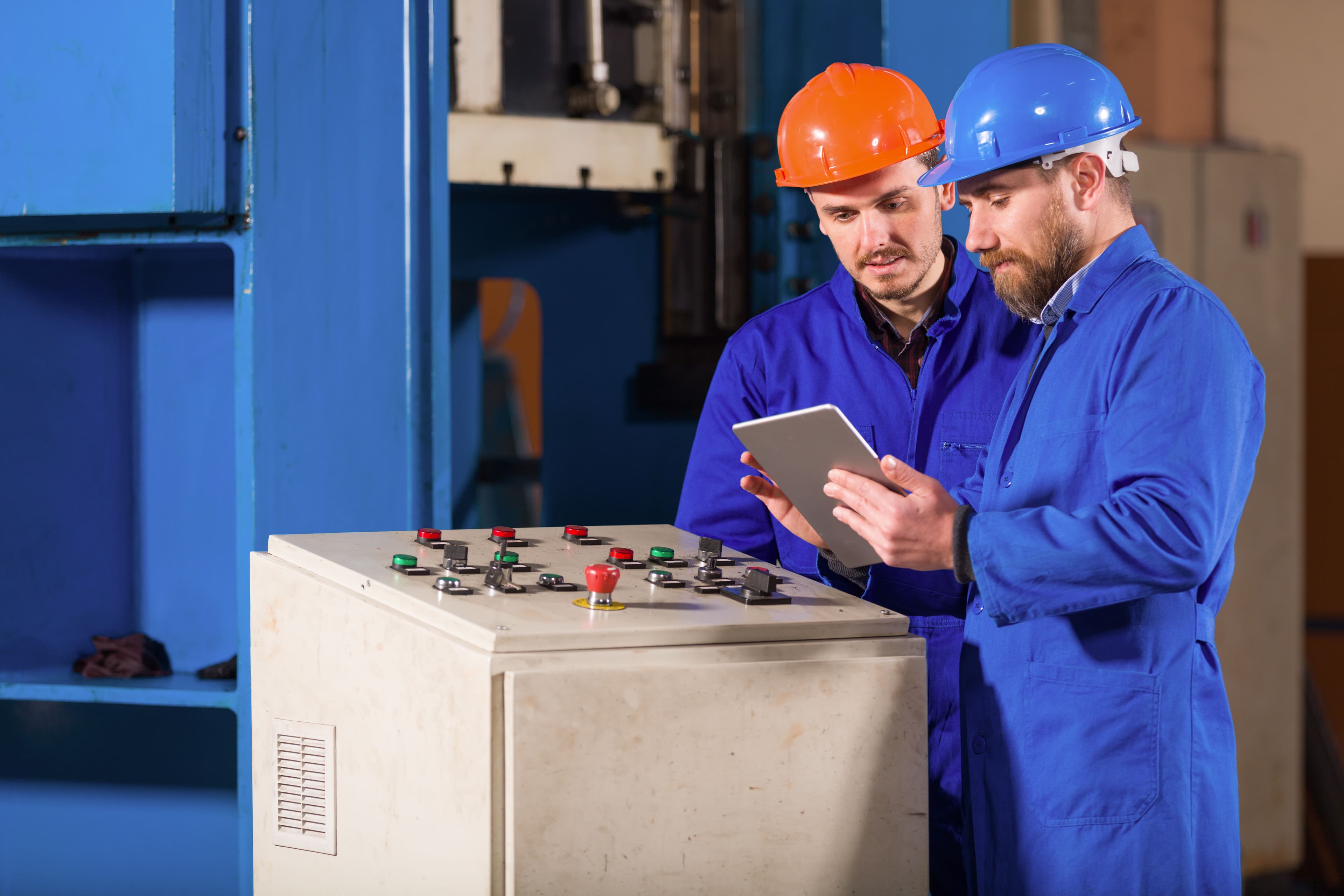
Equipment downtime gets expensive fast in automotive and aerospace manufacturing, a risk many companies try to mitigate by storing spare parts onsite. A machine breaks down, haul out the parts and hopefully you’re back in business with minimal disruption.
The problem is, manufacturers get so wrapped up in hitting production targets that they don’t stop to ask why the machine went down in the first place.
The result? The equipment goes down again, whether two days, two weeks or two months later, causing additional downtime because the “corrective” action was never designed to last.
To avoid backsliding after corrective action, companies must adopt a more proactive approach. A prevention focus, more frequent checks and cross-functional collaboration can help, but only if management is willing to move beyond short-term solutions. Read more on supplier corrective actions processes
Avoid Band-Aid Fixes with a Prevention Focus
The biggest reason corrective actions aren’t sustainable over time is because they aren’t real solutions to begin with—they’re just band-aids. Two of the most common mistakes in this category are blaming problems on operator error and stopping at containment.
For example, let’s say an automotive supplier gets a complaint over leaking A/C lines. Someone fills out a form listing the root cause as operator error and assigns more training, without examining similar parts for other customers. It’s not long before the company is back at square one, possibly millions of dollars poorer.
A better approach would be to do a reverse failure mode effects analysis (FMEA) to fill any potential gaps, asking questions like:
- What went wrong with our process?
- How did the problem happen?
- How did it escape detection?
- Have we fixed all lines of similar products?
In many cases, these questions may lead back to a design, tooling or process issue. Regardless, it’s important not to treat FMEAs as just another piece of paperwork. They are tools you should be using on the shop floor, comparing them against results to refine them and devise permanent fixes.
Expand Corrective Action Beyond the Quality Department
Manufacturers can’t expect corrective actions to be sustainable when they are the responsibility of the quality department alone. This problem gets back to the issue of quality culture, which by definition requires company-wide engagement.
In the example above, let’s say the company decides to implement error-proofing procedures to test the A/C lines for leaks. Rather than assigning these types of tasks to the quality department, assigning them to process owners can help:
- Leverage a relatively small quality team to implement more solutions than would otherwise be possible
- Make quality more visible for all departments and individuals
- Give people a first-hand look at how their work impacts quality, so they’re more invested in preventing problems
Making quality everyone’s responsibility is essential to sustainable corrective actions, since it means people can no longer treat quality as an afterthought.
Audit High-Risk Processes Frequently
High-frequency auditing is quickly becoming recognized as a best practice for driving quality improvement in automotive and aerospace manufacturing. Not only does it cast a wider net for catching problems, high-frequency audits also provide multiple opportunities to check that corrective actions are actually working.
As an example, let’s look at layered process audits (LPAs). These audits get their name from the various layers of personnel who participate in short, roughly 10-minute checks focused on process inputs known to contribute to quality problems.
Companies can use LPAs to hold the gains by rotating audit questions based on recent corrective actions, which is simpler than updating LPA questions via paper checklists. Automotive manufacturers have reduced internal PPM up to 73% with an automated LPA platform, and LPAs are quickly gaining traction in the aerospace manufacturing industry as well.
Evaluate Long-Term ROI, not Short-Term Costs
From a mindset perspective, a major barrier to sustainable corrective actions is the fact that companies typically prioritize production quantity over quality. Quality is treated as a net cost, pitting quality professionals against plant managers whose top priority is achieving production targets.
Permanent corrective actions can be expensive, so leadership tends to look for cheaper, short-term solutions. That shortsightedness comes with a price, however. For instance, suppliers often spend thousands in last-minute travel to a customer’s plant to fix a problem that might have cost just a few hundred to address before it left the factory.
Or let’s say you’re able to trace a large proportion of repeat issues back to packaging problems. If packaging errors cost you $700,000 annually, but leadership deems investing $10,000 per line for automated packaging too expensive, where’s the financial sense in that decision?
Overall, it points to a lack of understanding of the full cost of quality, which a majority of companies fail to track at all. Market leaders look at the full picture of what quality costs, recognizing that smart investments in quality decrease the likelihood of recurring problems. At the root of it all, it’s clear that this long-term perspective is necessary for sustaining and extending the gains you make with corrective action.