Creating a Supplier Audit Checklist That Covers All Your Bases
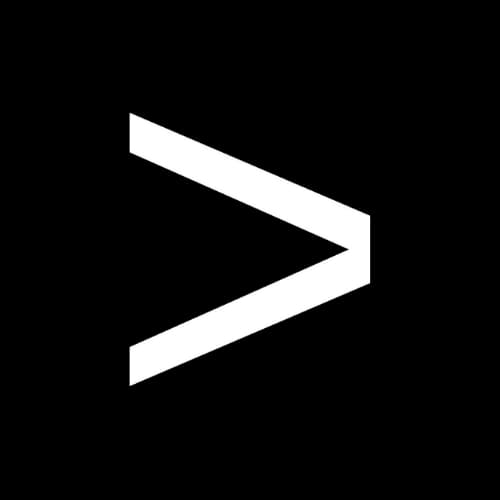
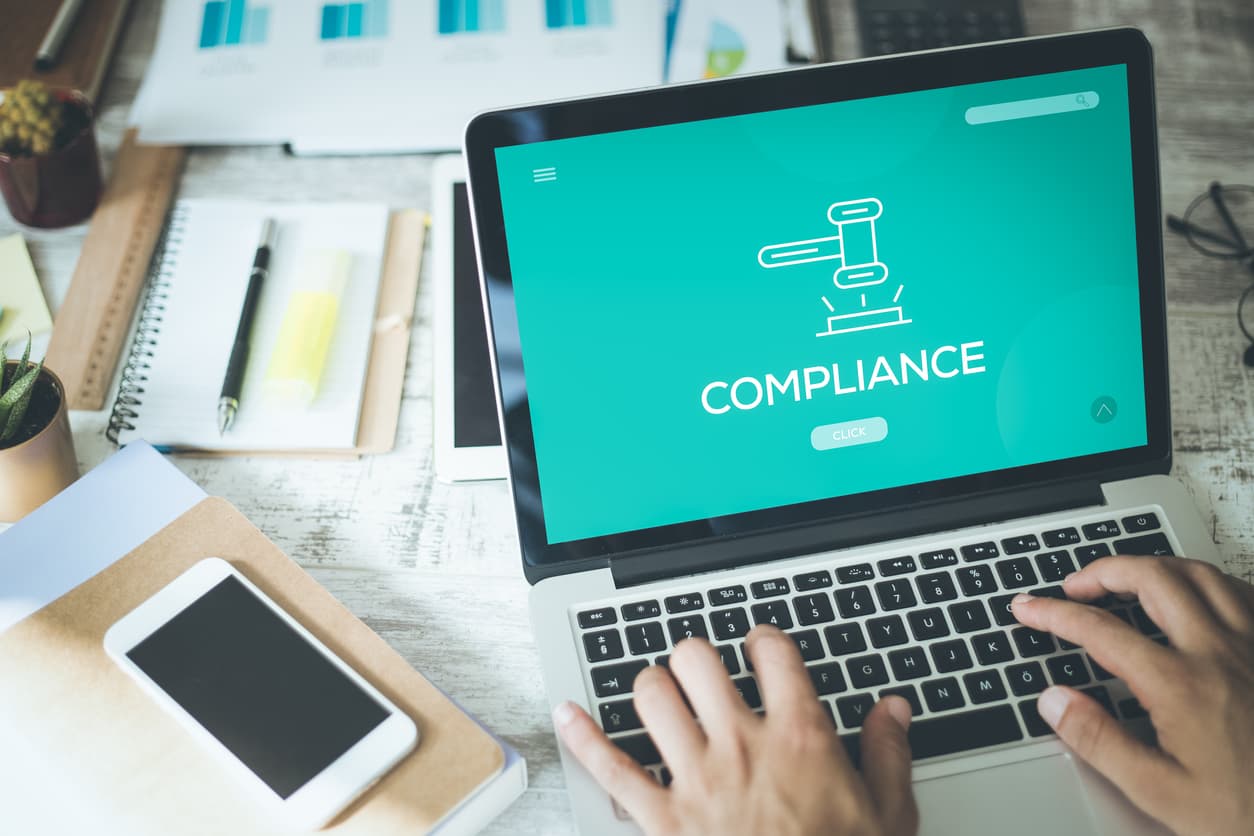
With most endeavors the amount of detail and forethought you devote to your preparations, the better your final result, and layered process audits (LPAs) are no exception. One of the most significant tasks of implementing an LPA system is writing the questions for your LPA checklists. Spending time upfront to investigate what has gone wrong in the past with your processes provides valuable insight for preparing an audit checklist that covers all the bases to satisfy your customers and promote a culture of quality throughout your organization.
Doing Your Homework
While few people really enjoy completing homework assignments, doing your research before writing audit checklists will pay dividends. Here are a few items that you can review which will provide a wealth of insight about your processes that are most at risk for non-compliance:
- Customer complaints
- The results/findings of Pareto charts created to pinpoint the root causes of non-conformances
- First-time through data/scrap reports
- Process failure modes effects analyses (PFMEA)
- Risk analysis reports, and in particular, those elements in the report which scored the highest risk priority numbers
- Flow charts for processes which are critical to customer satisfaction
- Quality management systems audit results
- Rework instructions
What Should Your LPA Verify?
LPAs are essentially a series of verifications to ensure that standards and controls are in place for your core processes and that they are being followed. It is important to audit not only manufacturing areas, but also non-manufacturing operations and support functions. To create your checklist for an LPA, you need to think in terms of what it is that you want to verify during an LPA. Audit areas of high risk first, determined through a PFMEA.
Below are some suggested verifications that will get you started with your list:
- Workmanship/craftsmanship standards practiced by operators
- Customer-facing features such as mounting holes, clearances, etc.
- Process/equipment parameters and settings
- Effectiveness of error-proofing measures
Remember, that your checklists are for auditing a specific process, not a product. With the help of audit management software you can effortlessly schedule a cross-functional group of auditors to cover LPA audits across your organization. An auditor should be able to complete an LPA in approximately 10-15 minutes. If a particular process is quite complex or has multiple sources of uncontrolled variation, it does not belong in an LPA.
Creating Your Checklist
LPA checklists are essentially a series of questions that your auditors will use when conducting an LPA of a specific process. Here are four items to cover when developing your checklist:
- What is the process and where to check it
- How to check the process
- Why this question was selected (explanation)
- How to react if a nonconformance is detected and what must be done to correct the nonconformance (reaction plan)
Two of these sections—explanations and reaction plans—warrant further review here.
The explanation section of your checklist is provided for auditors who may not be aware of the purpose of an audit question or the expected answer. In this section, it is a good idea to provide clarification with a defined purpose for the question and a response that would be expected from the auditee.
A reaction plan in your checklist will outline the steps that should occur if the item is non-conforming. It contains pre-determined steps to prompt the auditee to correct the nonconformance. If the issue is corrected during the audit, then the auditor will record this information on the checklist. This issue is still noted as a non-conformance although it was corrected. On the other hand, if the issue cannot be corrected immediately, it will remain as an open nonconformance.
Example Question
Here’s an example LPA checklist question from a manufacturing organization’s tool room:
Question: Is die maker wearing the following safety equipment: steel-plated boots, safety goggles, and ear protection?
Explanation: Without proper protection the worker could be injured.
Reaction plan: If a nonconformance is noted, correct it by having the worker put on the proper gear.
A question such as this would be audited at the beginning of each shift by the level-one auditor, the supervisor, and then on a weekly basis by a level two or three auditor.
If you complete your homework upfront and complete the research to create well-designed audit checklists, your LPA process will earn high marks.