Customer Spotlight: Grammer’s Dynamic Approach to LPA Implementation
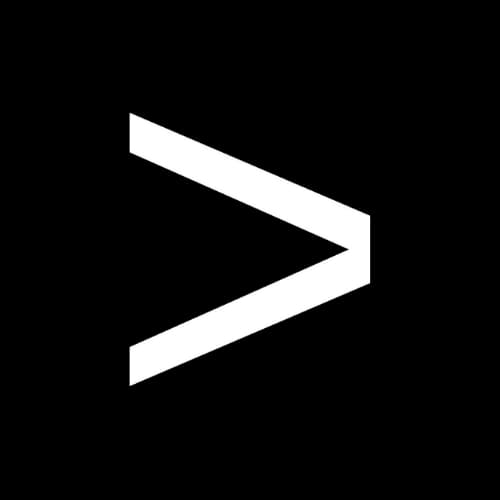
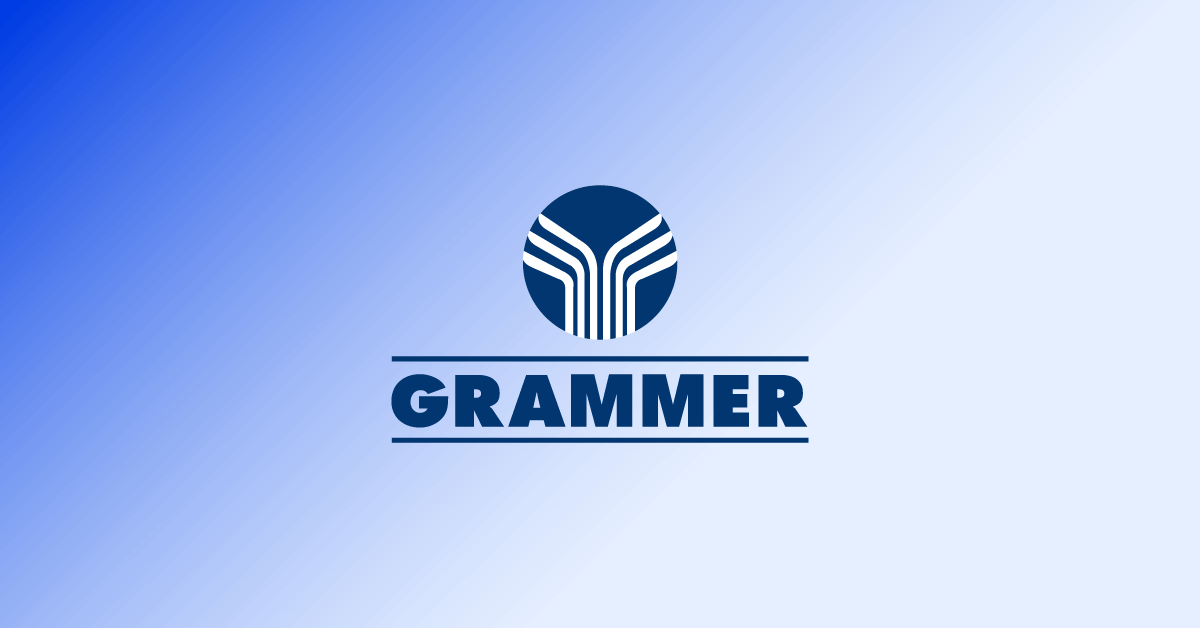
The first in our customer spotlight series is Grammer, a manufacturer of automotive and seating systems with more than 48 manufacturing facilities in 20 countries.
What caught our attention about Grammer was their unique approach to implementing EASE in its Querétaro, Mexico, plant. There the team used a multifaceted approach to digitizing its layered process audits (LPAs), leveraging a variety of tools to streamline training and ensure user adoption.
To learn more, we talked with Fabian Medina, the plant’s quality management system and metrology coordinator, and Guadalupe Garduño, quality management system trainer, about their innovative approach.
Download your free Ultimate Guide to Layered Process Audits for more LPA best practices, examples and tips
Confronting Cultural Change
Starting from a manual, mostly paper-based LPA process at Grammer, the software implementation took place in three stages. The first stage focused on creating the structure of their LPA program in EASE. The second stage involved adding all of their existing LPA questions and checklist items. In the final stage, the team tested and adjusted the system so it was ready to roll out to the entire plant.
“The process was great because EASE was clear about what was required and we were clear about what we wanted to do,” says Medina.
Part of the challenge of moving from paper and Excel to digital LPAs was helping their workforce adapt to conducting audits on mobile devices. The second challenge centered on closing out findings. According to Medina, employees weren’t used to having managers notified when findings weren’t closed on time, so the team wanted to provide additional training to get everyone on board.
A Dynamic Approach to Training and Implementation
Medina says they started communicating early with auditors and others involved in their LPA program about the upcoming software implementation, so everyone was aware of the coming changes.
In addition, Grammer added a direct link to the EASE platform on the company intranet, so that employees could easily pull it up when it came time to conduct audits. Leadership was committed to the implementation, helping drive cultural change from the top.
For training, Garduño created a streamlined user manual showing people exactly how to access the system, conduct audits and manage findings. It also showed them how to document findings outside of an official audit, for example observations on the plant floor requiring follow-up. Garduño’s user manual was an invaluable resource during the different online and offline trainings she conducted.
Perhaps the most innovative part of their training program, however, was the series of short videos they created to familiarize employees with EASE and provide implementation updates. These videos now live on various Grammer social media channels, including YouTube, Facebook and even TikTok.
“We included interviews on what EASE was and what the benefits are,” says Medina. “We also showed them on the breakroom screens and in meetings with managers.”
Building on Ideas to Drive Results
Throughout the process, EASE partnered with the Grammer team to bring their ideas to life and get the most from the software. As noted above, Grammer already had a well-developed LPA system. Medina and others also had ideas about how they wanted to improve it, leaning on the EASE implementation team to help turn them into reality.
The customer success team was with them at every step of the process, explaining the system and new audit tools they didn’t have previously. That in turn gave Grammer more ideas about how to improve their LPA process as a whole.
“It helped that top management was involved from the beginning, helping smooth out the process from the top down,” says Medina.
Today, Medina has access to detailed reports that help him communicate the results of their LPA program. For instance, Medina can now share dashboard reports showing the top three auditors every month, audit completion rate, status of findings and performance for each production line. He uses these reports to help keep employees engaged with the LPA process so everyone knows what they need to do to drive improvement.
Future Plans with EASE
Ultimately, Grammer discovered that the software would work not just for LPAs, but also other types of plant controls, such as poka-yoke audits, engineering control audits, product audits and VDA audits. As a result, Medina says Grammer plans to expand the use of EASE to other types of auditing at his plant.
The Querétaro site will also serve as a model for other Grammer plants implementing EASE, helping share best practices to ensure a successful rollout there.