Developing Leading Indicators from Plant Floor Inspections
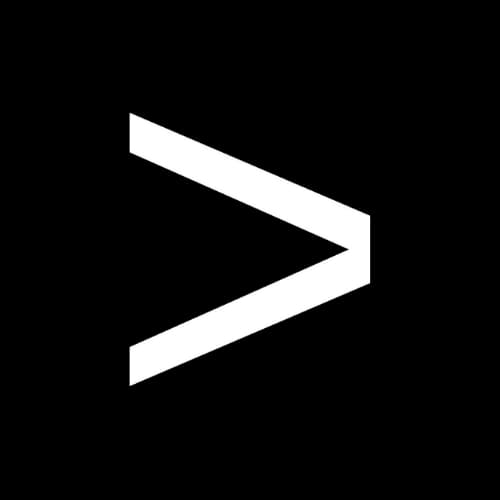

It’s common for safety managers to focus mainly on metrics like total recordable incidence rate (TRIR) or workers’ compensation claims, but this approach leaves plants open to preventable incidents.
In fact, the U.S. Occupational Health and Safety Administration (OSHA) recommends manufacturers use leading indicators as proactive metrics for predicting where incidents are most likely to occur. The biggest benefit of developing and tracking leading indicators is that their predictive nature allows you to take action to prevent incidents before they hurt workers.
One place to start when it comes to collecting the data: plant floor inspections.
In today’s article, we explore how companies can develop leading indicators from plant floor inspections and gain a key tool for preventing incidents.
Looking to get started with more frequent safety inspections? Download our free checklist template
The Difference Between Leading Indicators and Lagging Indicators
Lagging indicators describe what’s already happened in the past and include numbers like incidence rate and workers’ compensation costs. Leading indicators describe events that happen before safety incidents, such as how long it takes to respond to an inspection failure. In this example, increasing time to fix problems can indicate the presence of unmitigated hazards that could cause workplace injuries.
Leading Safety Indicators to Track from Plant Floor Inspections
Leading indicators can be developed from data you already collect during plant floor inspections, or to target a specific hazard or safety goals.
OSHA provides a helpful guide to leading indicators with ideas on metrics to track. Below are some ideas of leading indicators that can be tracked based on plant floor inspection data:
- On-time completion percentage for safety inspections
- Time to respond to inspection findings
- Number of operators with incomplete training
- Inspection pass rates
- Number of slip, trip and fall hazards identified during inspections
- Proportion of overdue maintenance requests or corrective action requests
It’s important to note that what may be a leading indicator in one plant may not be in another. It all comes down to your own plant’s data, meaning you must periodically assess whether changes in leading indicators correlate with changes in lagging indicators.
Getting Good Data from Plant Floor Inspections
Leading indicators are only as reliable as the data they’re based on. That means taking special care to avoid common pitfalls that can impact inspection data, which is where a digital inspection platform can help.
Digital safety inspection software makes it simple to:
- Avoid pencil-whipping: Randomized and rotated questions are harder to skip through, so people actually have to stop and read the questions rather than just flying through the inspection. Requiring photos to be taken during inspections also verifies whether an inspection actually took place on the shop floor instead of at someone’s desk.
- Take action faster: Instead of having to enter inspection findings manually and crunch the data, a digital platform provides real-time data via dashboards to raise awareness of emerging risks.
- Increase inspection frequency: More frequent inspections mean more chances to identify risks. Digital safety inspections make it easy to complete more checks by automating scheduling and reminders and allowing inspectors to pull up checklists on a mobile device.
- Stay on top of risks: With digital safety inspections, you can create questions based on recent incidents and corrective actions to ensure effective risk mitigation. You can also easily add questions designed around metrics you’d like to track, specific hazards you’d like to control or other safety goals.
Relying on leading indicators rather than lagging indicators can help companies protect workers while also reducing costs of workers’ compensation, legal fees, regulatory penalties and more.
Digital safety inspection software like EASE streamlines the process of developing and tracking leading indicators, providing better data while making it more visible to the organization. Ultimately, even one serious incident avoided can justify the effort required to implement a digital approach.