Digital Lean: The Future of Manufacturing Efficiency
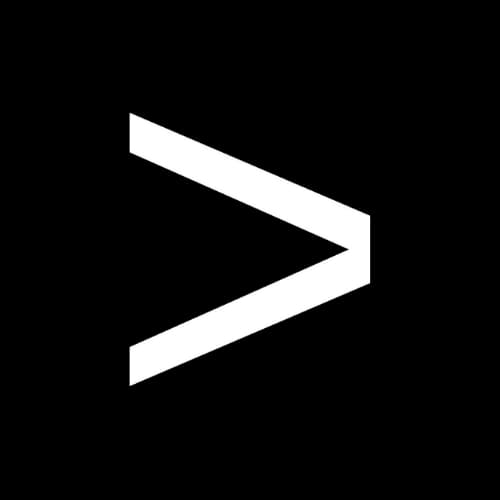
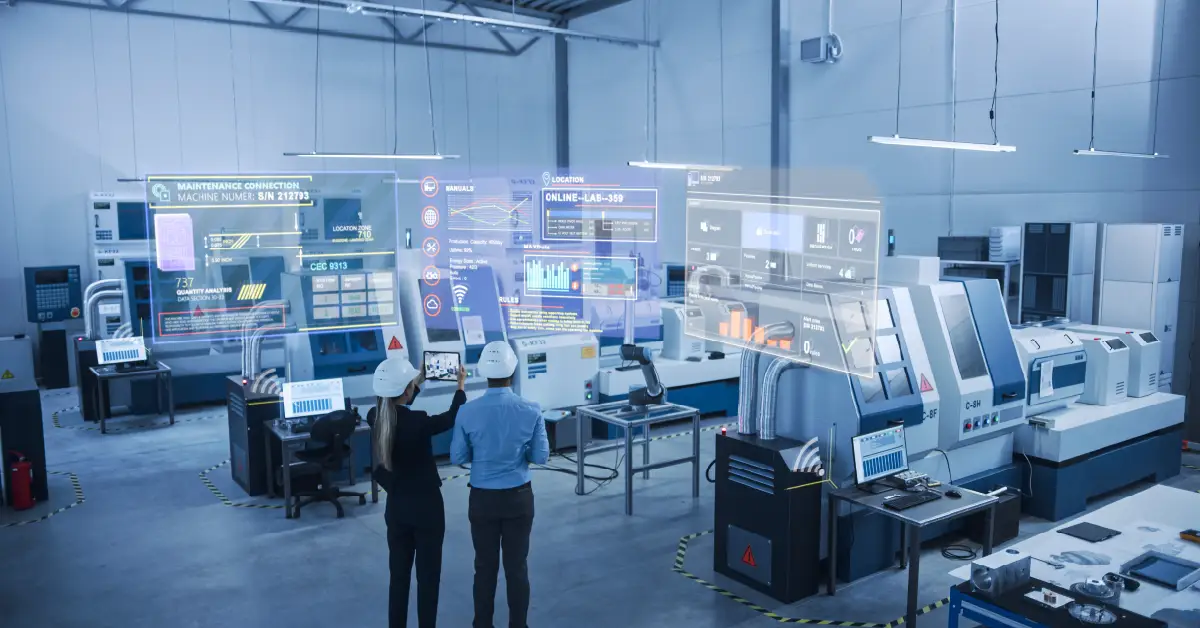
For decades, manufacturers have embraced Lean management principles, strategically aligning with the ethos of ‘digital lean‘, to design processes that reduce waste and create more value for customers and businesses.
The advent of Industry 4.0 has redefined what’s possible in operational excellence, leading to a new quality methodology that combines proven Lean principles with emerging digital tools.
Termed Digital Lean, it can create a multiplier effect in terms of results, amplifying the impact of Lean with more data, insights and agility in achieving transformation.
Here we explore what the nascent practice of Digital Lean means for manufacturers, including:
- Foundational elements for deploying Digital Lean initiatives
- Applications and benefits of Digital Lean
- Implementation strategies and challenges to consider
Browse our free content library for checklist template downloads, eBooks and more
What Is Digital Lean?
Digital Lean refers to the integration of Lean principles with emerging digital technology such as automation and advanced analytics to reduce waste and improve efficiency. In manufacturing, Digital Lean goes beyond traditional Lean practices to incorporate tools such as the Internet of Things (IoT) and machine learning to provide a data-driven approach to process optimization.
The Foundation of Digital Lean
According to experts at Deloitte, Digital Lean is driven by three critical enablers:
- IT and OT convergence: Digital Lean involves integrating IT systems with operational technology (OT) such as control systems and industrial networks to make critical data available to users.
- Process standardization and data management for enhancing OEE (Overall Equipment Effectiveness) in manufacturing processes: Digital Lean relies on accurate process data inputs, however, this isn’t possible without process standardization.
- Digital technology platforms: Flexible Technology platforms, integrate with other systems and streamline data management are necessary to unlock the full potential of Digital Lean.
Digital Lean with Smart Manufacturing: Applications and Use Cases
Lean management gets its name from its focus on eliminating different types of waste, resulting in a leaner process where every step creates value. Lean has its origins in the Toyota Production System, and today encompasses a wide range of Lean manufacturing tools used in plants worldwide.
Adding digital tools accelerates access to information, decision-making, and ultimately, action. It eliminates the time wasted waiting for information—and the time it takes to achieve improvement. Below are some applications of Digital Lean and smart manufacturing, and how the addition of accurate, timely data can help accelerate results.
Production Flow, Line Balancing and Scheduling
Real-time data on demand signals and production processes can help synchronize production capacity to facilitate just-in-time production and avoid manufacturing goods that aren’t needed.
Advanced analytics combined with live production data can also help balance operations, identify unnecessary bottlenecks, and reduce waiting time in your processes, furthering continuous improvement efforts. For example, applying big data to Heijunka or production levelling techniques provides a data-driven approach to eliminating unevenness in operations.
Work Standardization and Worker Guidance
Process standardization is a cornerstone of Lean management and an area where digital solutions can help ensure you’re getting accurate data from your processes. Connected worker platforms promote process standardization and minimize slowdowns by giving workers on-the-spot access to critical information, including:
- Digital work instructions and troubleshooting guides
- Guided procedure checklists based on the operator’s experience level
- Remote engineering helps in real-time when operators on the shop floor run into unexpected issues.
Reducing Errors and Process Variation
Digital Lean tools can help identify precisely where processes deviate from standards to reduce errors and process variation while accelerating problem-solving.
A digital audit and inspection platform, for instance, can replace time-consuming audit and inspection processes, so teams can:
- Get real-time visibility into plant floor issues needing attention to boost productivity through effective management practices.
- Assign and track action items to close the loop on nonconformances faster
- Analyze trends in process failures without manual data entry
Resource Optimization
Resource optimization is another area where Digital Lean tools can help identify inefficiency and waste. An example here would be implementing IoT sensors and smart meters on equipment to monitor energy usage in real time, using advanced analytics to identify patterns and anomalies. This would then allow the plant to optimize energy consumption based on production needs, for instance, by adjusting machine schedules during times of peak energy demand.
Inventory Management
Digital inventory monitoring combined with smaller inventory buffers helps avoid the buildup of excess inventory which requires resources to produce and store.
Digital Kanban systems, for instance, can replace physical Kanban cards with automated or operator-initiated signals to request additional materials. RFID technology can also help monitor and replenish parts automatically, with advanced analytics to adjust replenishment levels according to usage rates and pending orders.
Identifying Inefficiency in Your Operations
Digital Lean and smart manufacturing tools can help identify inefficiency in your operations, including Lean wastes such as:
- Overprocessing: Using digital twin technology, plants can pinpoint and eliminate steps in the process that don’t add value for the customer, thereby reducing waste.
- Worker movement: Analysis of work cell layouts and processes and advanced simulations can help identify operator motions that can slow down the production process.
- Transport: With real-time data on production, plants can identify areas where dispersed materials and processes can be better organized to reduce transport time.
Why Adopt a Digital Lean Manufacturing Strategy
Digital Lean provides a foundation for digital transformation rooted in proven Lean principles. More importantly, Digital Lean initiatives can help achieve greater results than would be achieved through digital or lean projects alone.
Without digital tools, companies are limited in what they will be able to accomplish. This lack of digital tools creates a constraint that increases lag time in solving problems, driving up waste overall.
According to Bain, for example, Digital Lean can lead to cost reductions of up to 30%, compared with 15% through traditional Lean projects. Below we discuss some of the benefits of Digital Lean and how it leads to more efficient, more profitable operations.
The merging of digital technologies and lean principles has led to what we now call “digital lean” – a blend that brings together the best of both worlds to reduce waste and make processes more consistent.
Improved Quality
Digital Lean offers the ability to improve quality faster than traditional Lean approaches by giving teams what they need to:
- Identify hidden factory issues that negatively impact quality
- Get real-time visibility into production issues
- Solve problems faster with more detailed, accurate data, a fundamental aspect of traditional lean improvement projects
- Minimize process errors and defects that are hard to detect with manual approaches
According to Deloitte, Digital Lean has the potential to improve quality by up to 35% by reducing scrap and lead times while increasing fill rate and yield.
Reduced Equipment Downtime
Predictive maintenance using IoT-enabled sensors can improve the efficiency of maintenance activities and reduce costly equipment downtime and production delays. For example, machines can perform self-maintenance or trigger maintenance activities based on real-time machine data such as vibration and temperature, rather than performing maintenance on a scheduled basis.
Improved Decision-Making and Problem-Solving
Automated anomaly detection and real-time analysis of process data can help speed up root cause analysis and solve problems faster. For example, operators can log observations or audit and inspection data from mobile devices, providing added visibility into process deviations and even photos of plant floor conditions needing attention.
Digital Andon systems are another example, replacing traditional lights with digital displays of production line status to make issues and line stoppages immediately visible.
How to Build a Successful Digital Transformation Strategy
Adding digital tools to Lean methodologies can unlock new efficiencies that, until now, were not possible with traditional approaches. That said, achieving these benefits demands careful thought and planning to avoid the pitfalls associated with digital transformation.
To that end, the planning process must address three questions rooted in the principles of lean manufacturing:
- What problem are you trying to solve?
- Where and how will you start?
- How will you secure organizational buy-in?
Focus on Problems, Not Technology
Instead of focusing on a new tool or technology that you want to implement, it’s important to start by identifying a high-impact problem to solve. This is what will allow you to get a higher return on investment, rather than being caught up in the “shiny object syndrome” that so often derails digital transformation efforts.
Examples of high-impact problems include:
- Reducing the cost of poor-quality
- Reducing machine downtime
- Improving supply chain visibility
- Reducing rework and scrap
Implementation Strategy
Many organizations use a Kaizen approach to gather ideas about where to start and how to implement Digital Lean initiatives. Pilot projects are common, allowing you to test and iterate your strategy to facilitate a smoother plant-wide rollout.
One strategy to consider here is Hoshin Kanri, a Lean tool based on the Plan-Do-Check-Act process to align projects with organizational objectives. Hoshin kanri, which translates to policy deployment, brings strategy together with tactics and execution to ensure organization-wide consistency in rolling out new initiatives.
Addressing the Human Element of Digital Transformation
Finally, it is vital to consider the human element of any Digital Lean initiative. Overcoming organizational resistance is essential, requiring a strategic change management plan that addresses the needs of all stakeholders.
Here you’ll want to focus on strategies such as:
- Soliciting input from users
- Communicating how your Digital Lean project will make various users’ jobs easier
- Seeking out those with influence on the plant floor, whose buy-in will help pave the way for wider user adoption
While Digital Lean is the future, it’s not a cure-all, nor does it replace traditional lean practices. Instead, it requires a paradigm shift in terms of data-driven decision-making, and a solid change management strategy to ensure organizational buy-in.
With the right approach to people, processes and technology, Digital Lean has the potential to revolutionize how manufacturers do business—and the value they deliver to customers.