The Hidden Cost of Doing Nothing: An Audit Management Perspective
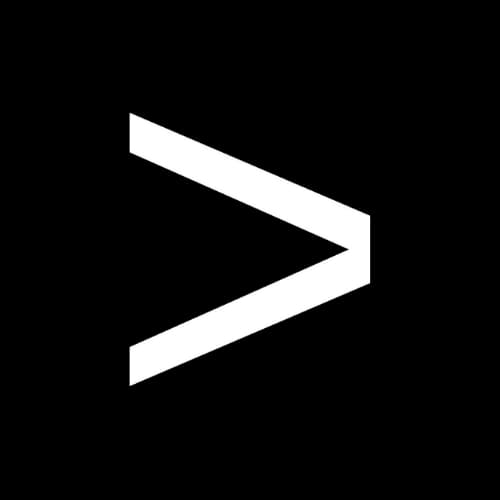
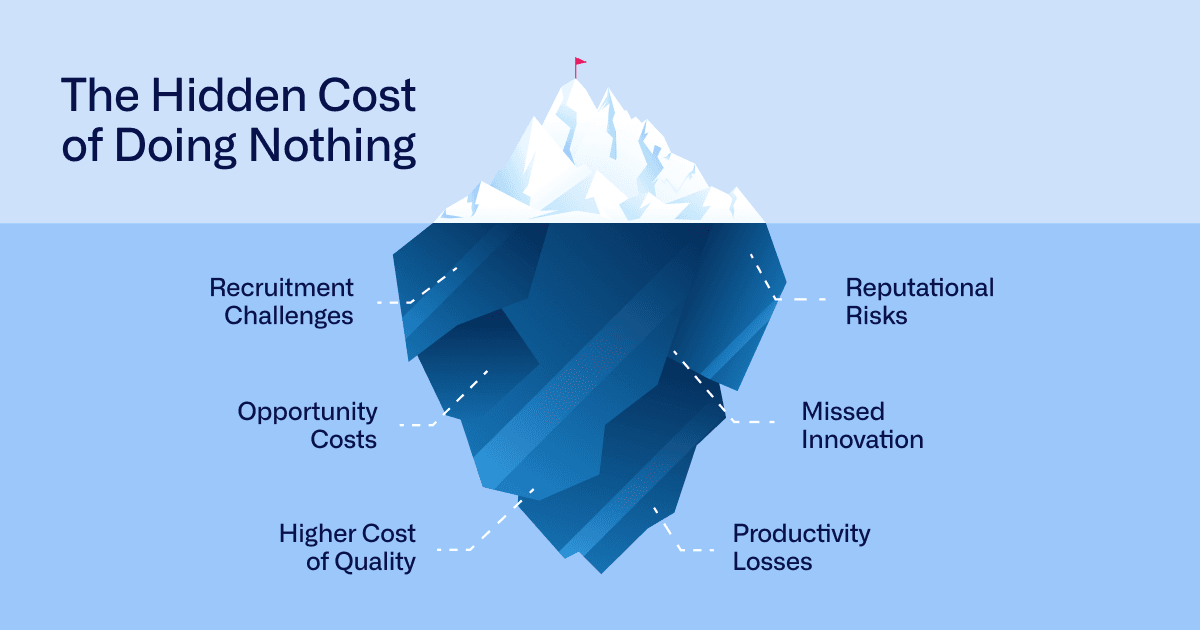
When facing a decision to try something new or stay the course, two things are true:
- Not making a decision (or delaying it) doesn’t mean avoiding risk; this is a choice in and of itself.
- Sticking with the status quo can have significant implications.
In the context of deploying plant floor audit management software, those impacts include higher cost of quality, reputational risks, barriers to innovation and more. Let’s jump in and look at these in more detail.
Download your free Ultimate Guide to Layered Process Audits to learn how process audits can help reduce defects quickly
If you’re using generic checklists or manual audit management processes to conduct plant floor checks, the hard truth is that you’re going to face increased quality costs. This is due to factors like:
- Static checklists preventing you from adapting to emerging quality risks and known problems
- Inefficient reporting that allows problems to remain hidden, and makes it hard to spot systemic risks and trends in plant floor nonconformances
- Lack of robust data due to low completion rates when people ignore, forget or pencil-whip their assigned audits and inspections
- Disjointed corrective action processes that fail to close the loop on nonconformances in a timely manner
Software that digitizes plant floor audits eliminates these barriers, allowing companies to drive down defects and associated costs faster. One windshield wiper manufacturing plant, for instance, was able to reduce quality costs by a full 50% after deploying EASE plant floor audit software. Other examples of real-life results companies have achieved with the software include:
- 53% reduction in customer defects
- 73% reduction in PPM (parts per million)
- 94% reduction in overdue corrective action requests
Note here that the average company loses 10% to 40% of revenue in quality costs. Depending on the size of the company, sticking with spreadsheets could mean leaving millions in savings on the table due to increased scrap rates, corrective action costs and warranty claims.
Risk: Productivity Losses
In addition to quality costs, there are also hidden productivity impacts associated with using paper and spreadsheets to manage plant floor audits and inspections. Lack of visibility into standard adherence can cause problems such as:
- Lower OEE: Higher defect rates and slower cycle times reduce overall equipment effectiveness (OEE), a key measure of how well you’re using machines relative to their capacity.
- Higher employee turnover: Safety issues and confusion over how to execute processes can lead people to feel unsupported in their roles, making them more likely to seek work in higher-performing plants.
- Lower throughput and productivity: If you’re constantly reacting to problems rather than proactively preventing them, this will slow down the process and result in lower volumes of salable products.
One plastics manufacturer, for instance, was able to achieve a roughly 20% increase in throughput and nearly 100% on-time delivery with plant floor audit software.
Risk: A Battered Reputation
A robust system of checks to ensure that process inputs and operator behavior conform to standards is critical to preventing recalls, failures and reputational damage. Because the truth is, it doesn’t take much to find yourself in the spotlight for all the wrong reasons.
For Boeing, all it took was a set of loose bolts on a 737 Max to put them at the center of a public safety disaster—and in the crosshairs of regulators.
Even when production defects don’t result in a recall or safety failure, the resulting complaints can put key contracts at risk and erode relationships that took years to build.
Risk: Difficulty Attracting New Employees
One reason why manufacturing struggles to attract talent is the fact that the industry has a reputation for being behind the times. Tomorrow’s manufacturing leaders are digital natives who come in with the expectation of using modern software tools rather than outdated pen-and-paper methods to manage quality.
Those companies that remain stuck in the past will have a hard time competing for talent with manufacturers that adopt modern, intuitive apps for managing plant floor compliance. Using old-fashioned paper checklists, forms and spreadsheets sends the wrong message, compared with showing prospective employees you have a future-oriented culture that prioritizes technological innovation.
Risk: Lack of Resiliency and Innovation
Manufacturing resiliency and innovation require an ability to adapt to changing conditions, specifications and risks quickly. Manufacturers also need a way to sustain those changes, something that is much more difficult if you’re using traditional audit and inspection methods.
Low audit completion rates, manual signoffs, disjointed corrective action processes—all of these and more create barriers to agility that slow your organization down. The result is often increased costs and a growing backlog of problems, and an inability to respond to industry trends and competitors’ moves.
Risk: Opportunity Costs
One final element to consider is the opportunity costs associated with the problems discussed here. Let’s take a closer look using a quick calculation from the wiper plant mentioned earlier.
Had the manufacturer delayed implementation by even six months, that would have translated to an additional six months of higher quality costs. For a company with $10 million in revenue and even just 10% in quality costs (the low end for most companies), that’s $500,000 in avoidable costs.
What initiatives or innovations could your plant be pursuing with that kind of additional money? Are you pouring resources into correcting problems that could be better used for strategic projects?
In the end, the decision to challenge the status quo is underlaid by one essential truth: If you’re not moving forward, you’re moving backward.