How FCA Customer-Specific Requirements for IATF 16949 Impact PSA Group Suppliers
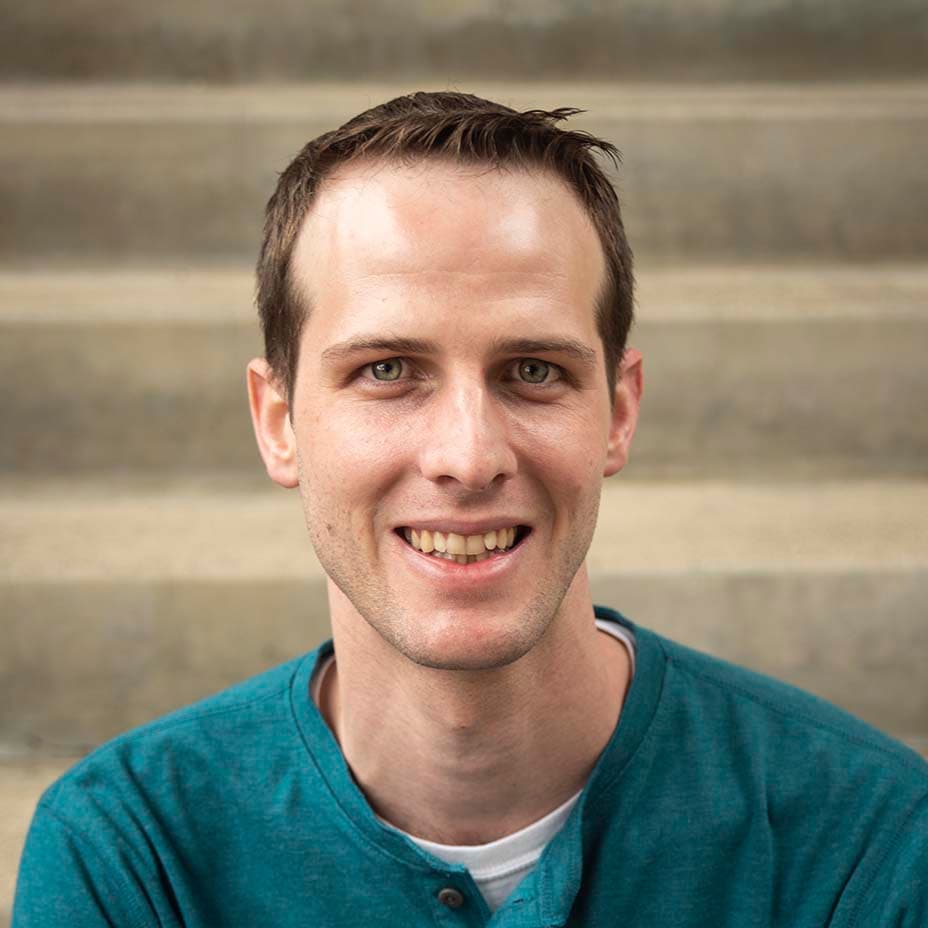
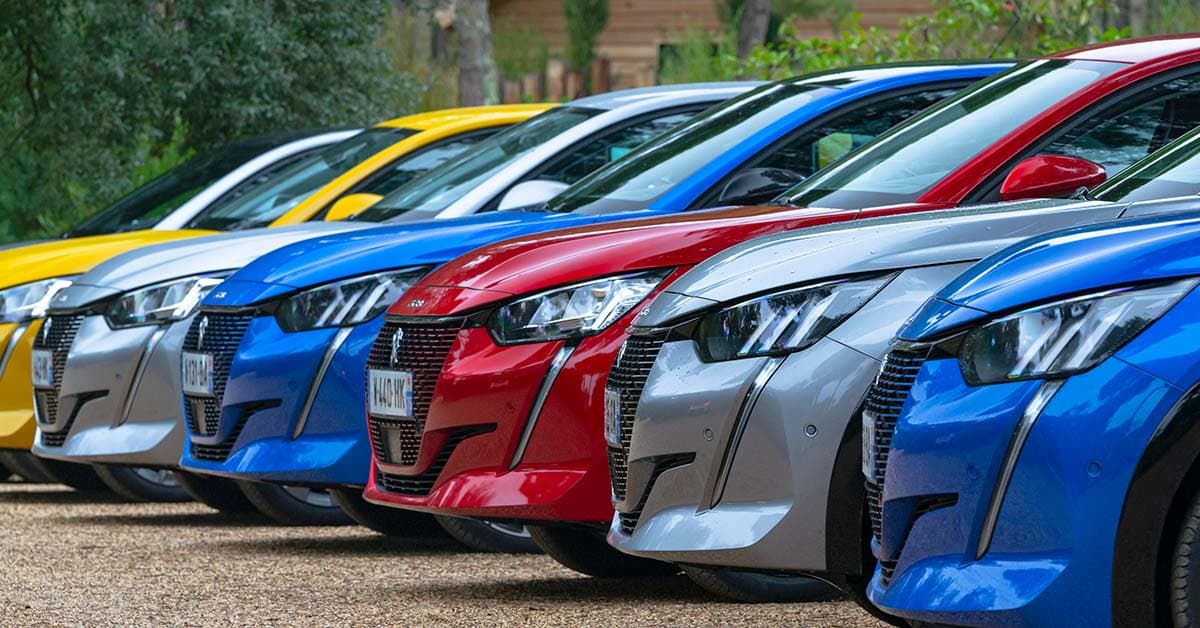
Change is coming to the PSA Group supply chain, and suppliers need to take note if they want to keep their customers.
The long-discussed merger between Fiat Chrysler and PSA Group was finally completed in January, creating the fourth-largest automaker in the world: Stellantis. While existing customer-specific requirements (CSRs) for PSA Group remain in place for now, PSA Group notified its suppliers in January that process convergence is underway. FCA updated its CSRs in March and PSA published its own interim update in May. However, given that FCA’s requirements are more stringent, it’s a safe bet that theirs will be the model ultimately used by Stellantis.
While there are many areas in the final Stellantis CSRs that are likely to affect PSA Group suppliers, it’s virtually guaranteed that requirements for layered process audits (LPAs) will tighten. We broke down Fiat Chrysler’s LPA requirements in 2019, but let’s see how their most recent CSRs for IATF 16949 compare to those of PSA Group to identify what PSA Group suppliers need to know most to prepare for the coming changes and avoid losing contracts over non-compliance.
Download our free Ultimate Guide to Layered Process Audits eBook to learn about a powerful strategy for cutting production defects and scrap rates
New Requirements for Your Auditors and Administrators
When Stellantis publishes its CSRs, the first area that PSA Group suppliers will need to address is the process of qualifying auditors and administrators. Today, PSA Group requires LPA auditors to be qualified but does not mandate any specific qualification. FCA, on the other hand, requires of its suppliers that “the [LPA] program shall be administered under the guidance of a competent manufacturing process auditor as defined in IATF 16949 Sanctioned Interpretation no.4 for Section 7.2.3.” Per the IATF 16949 Sanctioned Interpretation, this means suppliers must:
- Document the process of verifying that internal auditors are trained, including internal requirements and CSRs.
- Maintain a list of qualified internal process auditors.
- Ensure auditors understand the automotive process approach for auditing, applicable CSRs, relevant ISO 9001 and IATF requirements, and the process of planning, conducting, reporting, and closing out audit findings.
- Demonstrate that auditors understand the processes being audited, including process risk analysis and control plans.
Clearly, FCA’s auditor and administrator criteria are much more stringent than what PSA Group suppliers are used to today. The best way for PSA Group suppliers to get ahead of this change is to start at the top of their LPA programs. By ensuring that LPA program administrators are trained in the IATF 16949 standard, documenting LPA and CSR training processes, and building out their lists of qualified LPA auditors at each facility, suppliers can begin addressing the rest of the changes coming to Stellantis’s customer-specific requirements.
More Robust LPA Program Requirements
In addition to its requirements for auditors and administrators, FCA mandates that its suppliers conduct LPAs for every manufacturing process except “specific materials, parts or assemblies produced on such an infrequent or irregular basis that it would prohibit establishing a regular, weekly audit schedule.” Even with the exception of such processes (which must be documented), PSA Group suppliers may find themselves conducting far more LPAs than they currently are. Beyond the administration of more audits in more areas, FCA also holds its suppliers to a higher LPA standard than PSA Group. Customer-specific requirements that FCA suppliers must follow include:
- Using the latest available edition of CQI-8: Layered Process Audits Guideline to establish an LPA program.
- Conducting both Process Control Audits and Error Proofing Validation audits once per shift as part of the LPA program.
- Mandating participation in the LPA program by the highest level of senior management normally present at a facility at least once a week.
- Documenting audit structure, including auditor level and frequency of inspections.
- Creating compliance charts quarterly to document audit completion by layer for all layers and by-item percentage conformance by area.
- Putting reaction plans in place to immediately resolve non-conformances.
While many of these requirements are best practices that any organization conducting LPAs should be following, each one represents a potential opportunity to lose a supplier contract if not properly adhered to. PSA Group suppliers should be analyzing their LPA programs immediately in order to verify that these procedures are being followed at every facility. At minimum, since PSA Group does not require that senior plant management participate in LPAs with any set regularity today, suppliers will want to secure buy-in from managers outside of the Quality Department well in advance of any change in customer-specific requirements.
- Learn the 7 Habits of a Mature Quality Culture
Documented Planning for Corrective Actions & Root Cause Analysis
When Stellantis releases its final CSRs, suppliers will need to demonstrate that they have an adequate plan for addressing LPA findings. Specifically, FCA requires that its suppliers “show evidence of immediate corrective action, containment (as required), and root cause analysis (as required).” Additionally, where recurring non-conformances are involved, suppliers must maintain a separate communication procedure inclusive of resolution, escalation, and lessons learned. As in the last section, these procedures exist in any manufacturing plant. Suppliers will want to make sure that they are adequately documented, and even more importantly, that they have the visibility into LPA results that they need to quickly identify and correct recurring non-conformances before they cause problems for their PSA Group customers.
Legacy PSA Group Requirements May Still Apply
While much of what we’ve covered here has assumed that FCA’s standards will become Stellantis’s standards, it’s important to note that there are provisions in PSA Group’s CSRs that do not appear in FCA’s and may carry forward. Regarding LPAs, these fall into two main categories:
- PSA Group requires that LPAs be conducted in all operational areas, including logistics and maintenance.
- PSA Group expects its suppliers to document how LPA results are incorporated in employee training and requalification procedures.
Whether these provisions make it into the final Stellantis CSRs or not, expanding the use of LPAs to non-quality functional areas and taking action on LPA results are best practices that any manufacturer should follow. When qualifying auditors, training administrators, implementing new audit processes, and updating documentation to align with the new requirements, PSA Group suppliers would be wise to ensure that these procedures remain in place.
How EASE Can Help PSA Group Suppliers Meet these New Requirements
As soon as Stellantis finalizes its new customer-specific requirements, PSA Group suppliers will be expected to conduct more frequent, more rigorous, LPAs involving more levels of management. Suppliers will need to ensure that every step of the process, from training to auditing to addressing audit findings, is documented and properly adhered to in order to mitigate the risk of losing a valuable supplier contract. It is essential that PSA Group suppliers get ahead of the game immediately and begin preparations for the coming changes.
Pen-and-paper, Excel-based LPA programs or even QMS audit features simply will not be able to keep up with the task of conducting LPAs that meet Stellantis standards. Instead, PSA Group suppliers should be looking to implement digital LPA software to reduce administrative burdens, improve on-time audit completion, and provide real-time insight into audit results. EASE is built to handle almost any quality audit and gives automotive suppliers:
- Instant access to layered process audit reports and findings and the ability to create custom dashboards for customer-specific requirements, like audit completion rates.
- Simplified scheduling for a high volume of audits across all layers of management.
- Automated email notifications of upcoming audits and mitigations and escalations to managers when people miss audits.
- Mobile audit app that makes it easier to complete audits, even where WiFi access is unavailable, leading to higher audit completion rates.
- On-the-spot non-conformance correction or assignment of mitigations when an audit question is failed.
- Streamlined checklist updating to address complaints and verify corrective actions.
In addition to delivering an application that is tailor-made for conducting LPAs, every member of our implementation team is trained in and knowledgeable of CQI-8 standards for implementing LPAs. Our customer success team will have your facilities conducting digital audits that meet the CQI-8 guideline in as little as one month after your pilot program.
When it comes to customer-specific requirements, you don’t want to leave anything to chance. Change is coming to Stellantis, and for PSA Group suppliers, the time to start preparing is now.