How Layered Process Audits Drive a Culture of Quality
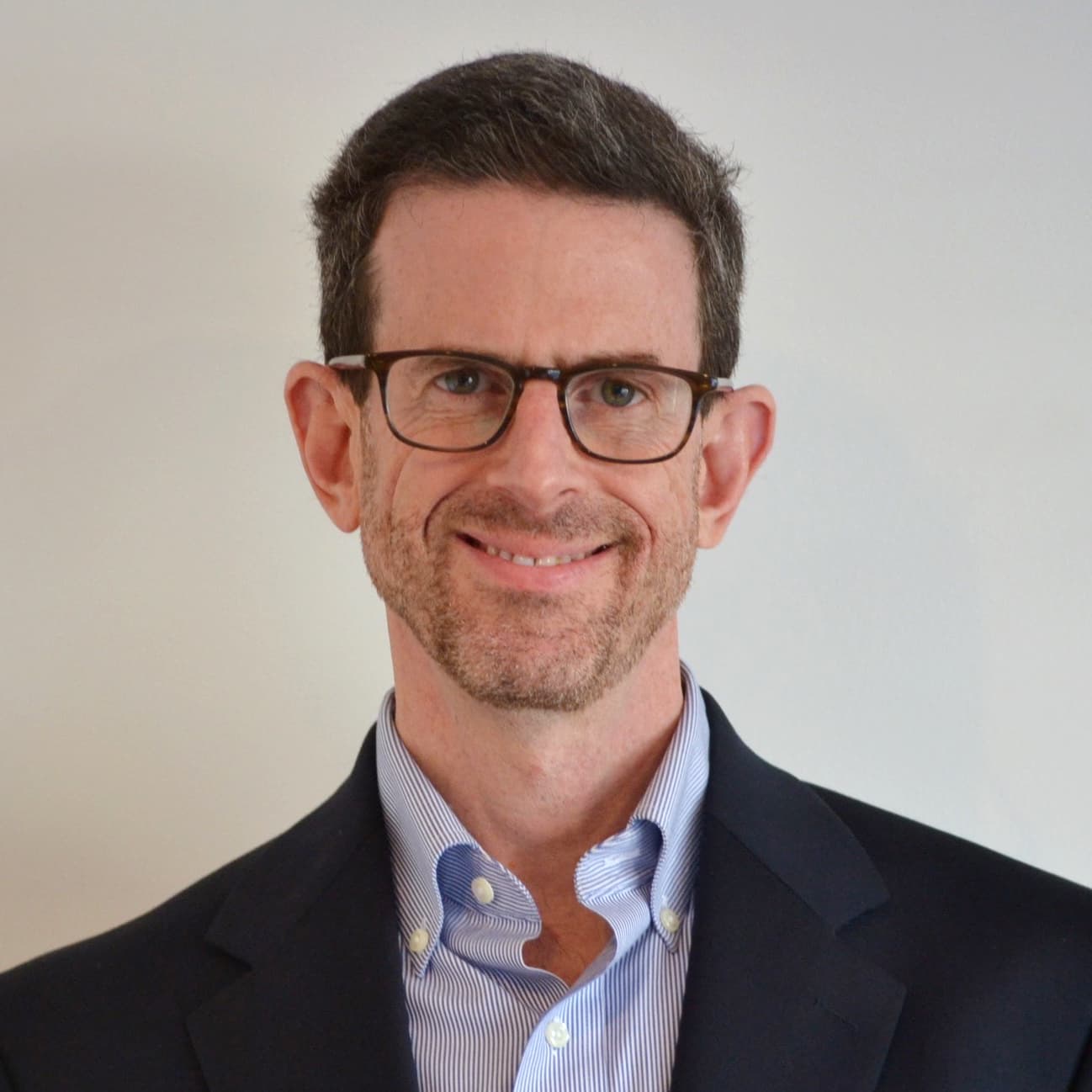
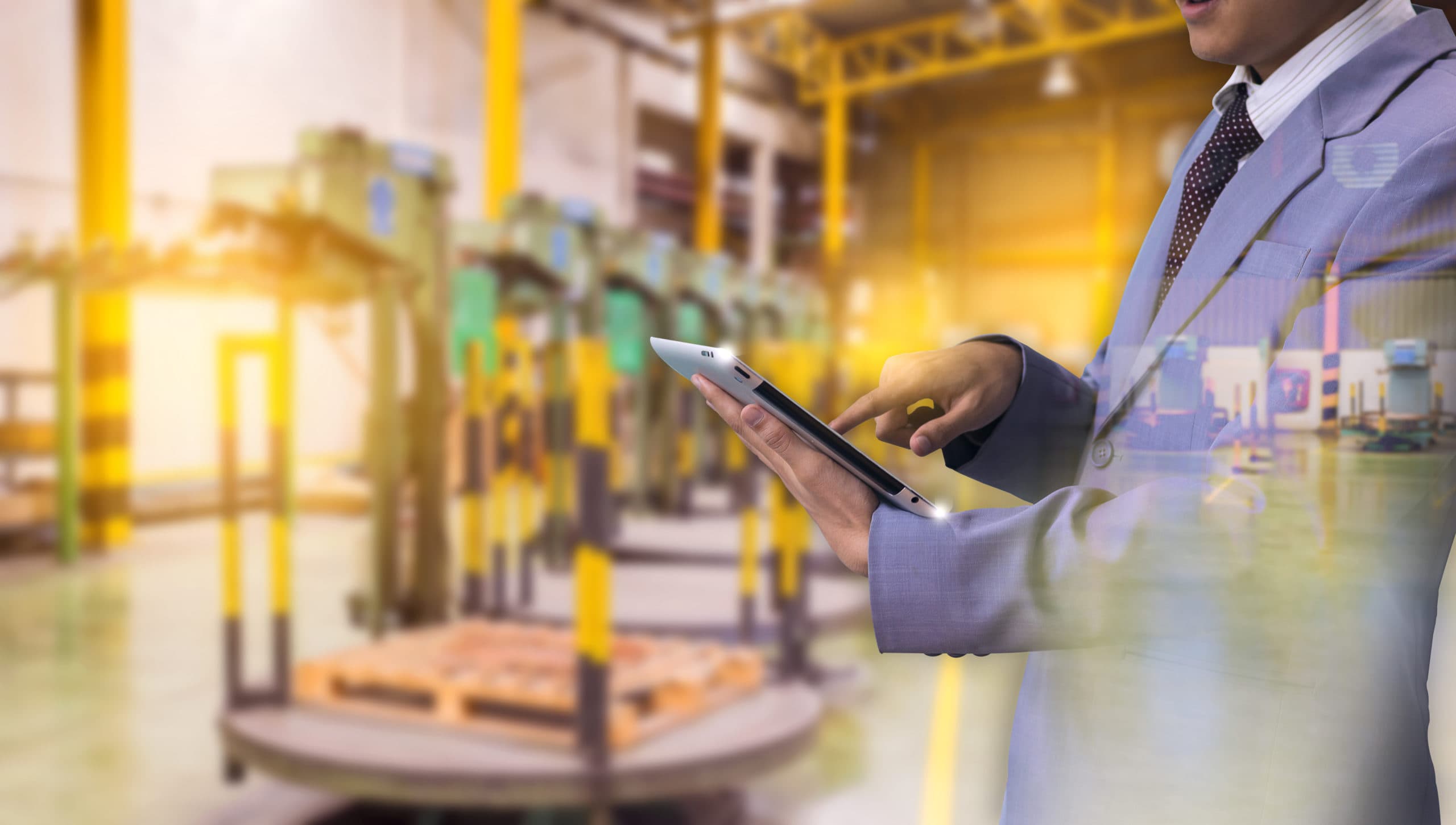
Quality is actually quite simple—it’s the human element that makes it difficult. We all know it can be challenging to get employees to follow a standardized set of steps, as people often have their own reasons for taking shortcuts or deviating from the established standard.
The problem is that when people deviate from standards, you’re less likely to achieve the desired outcome. That’s where layered process audits (LPAs) can make a big difference, providing frequent process verifications that address the human element of process adherence.
In this post, we’ll look at how LPAs help create a culture of quality in manufacturing plants, promoting process conformance and employee engagement. The payback is in improved quality metrics and lower cost of poor quality.
LPA Basics
LPAs are short, frequent audits that verify key steps in high-risk processes. Formalized about 20 years ago at General Motors (GM), LPAs are different from quality system audits in that they’re completed every single shift on critical process elements.
LPA questions focus on process inputs, rather than outputs. When operators complete processes correctly, outputs will more likely meet spec, reducing the cost of non-conforming product.
The “layers” in layered process audits refer to the different groups conducting audits, shown in the table below:
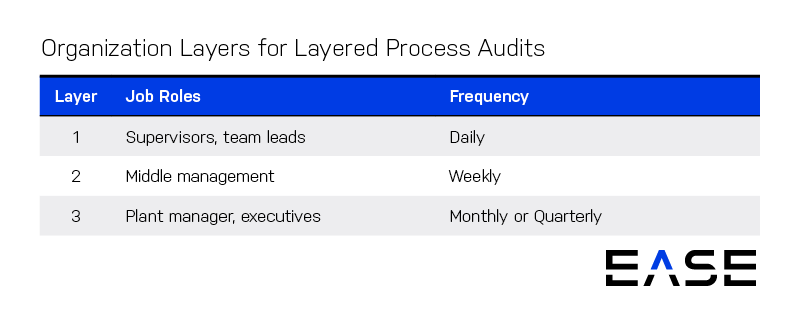
Ensuring Process Adherence
Automotive OEMs have high expectations in terms of quality. They take zero defects seriously, imposing expensive consequences on suppliers who ship defective parts. For instance, if you supply defective parts to a vehicle assembly plant, you could be responsible for:
- Expediting replacement parts
- Third-party inspection and sorting costs
- Yard-hold costs
- Product recall
- Regulatory fines and penalties
It’s because of these high costs that LPAs emerged as a strategy for preventing defects. Unlike tools such as failure mode and effects analysis (FMEA), which establishes process controls against what could go wrong, LPAs verify controls are in place and working on a daily basis.
Most companies simply assume employees follow standards according to training. But because of the human element—in this case, difficulty following guidelines over the long term—audits help to ensure operators consistently follow standard procedures.
That means instead of waiting for problems to surface as scrap, rework and complaints, you proactively identify process deviations that could cause defects. To do that, you need more than just generic checklists. Each work cell needs its own audit questions tailored to the process to ensure the key preventative and detection elements for that cell, station, or line, are in place and are performing as intended.
Driving Employee Engagement
LPAs aren’t about blaming people for mistakes. At their core, their purpose is verifying work follows standards. A positive approach centered on coaching—which is leadership’s job—makes all the difference when it comes to buy-in.
Getting people on board is important because LPAs engages multiple levels of the company, including:
- Supervisors: Each supervisor verifies that team members follow key process requirements on every shift.
- Management: Management checks the same process elements as supervisors, adding accountability while sending the message that leadership is committed to quality.
- Operations: Unlike quality system audits, LPAs should be part of the operations function.
- Other departments: Auditors should also come from departments such as human resources, finance and shipping. This makes quality part of everyone’s job description, laying the foundation for a culture of quality.
How auditors interact with employees is critical. A respectful, responsive approach enables open lines of communication and improvement. To maximize engagement, auditors should:
- Make eye contact when asking questions and show genuine interest in the answer
- Acknowledge when people are following standards and processes are operating correctly
- Solicit ideas for improvement and relay them forward
Closing the Loop
When an audit uncovers a non-conformance, the next step is to record the problem and initiate corrective action. Fixing problems promptly demonstrates prioritization and commitment to quality, while ignoring non-conformances undermines any good intentions.
Closing the loop on corrective actions also has a direct impact on LPA engagement. When auditors respond to problems and are open to suggestions, people actually want to be audited. LPAs become not just another box to check, but a collaboration strategy that helps all employees do their best work. And when auditors have such a marked impact, they’re less likely to skip scheduled audits.
Executed properly, LPAs do more than just improve process adherence and reduce quality costs. When a manufacturer consistently verifies key processes while showing respect for individual contributions, it creates a culture of excellence visible throughout the organization and builds on people’s desire to make a positive impact where they work.