How to Promote a Culture of Safety with Plant Floor Inspections
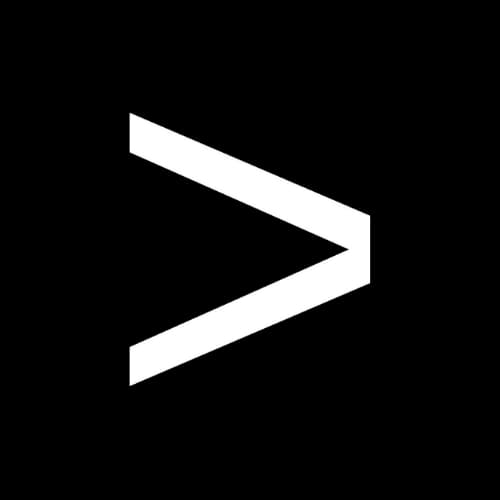
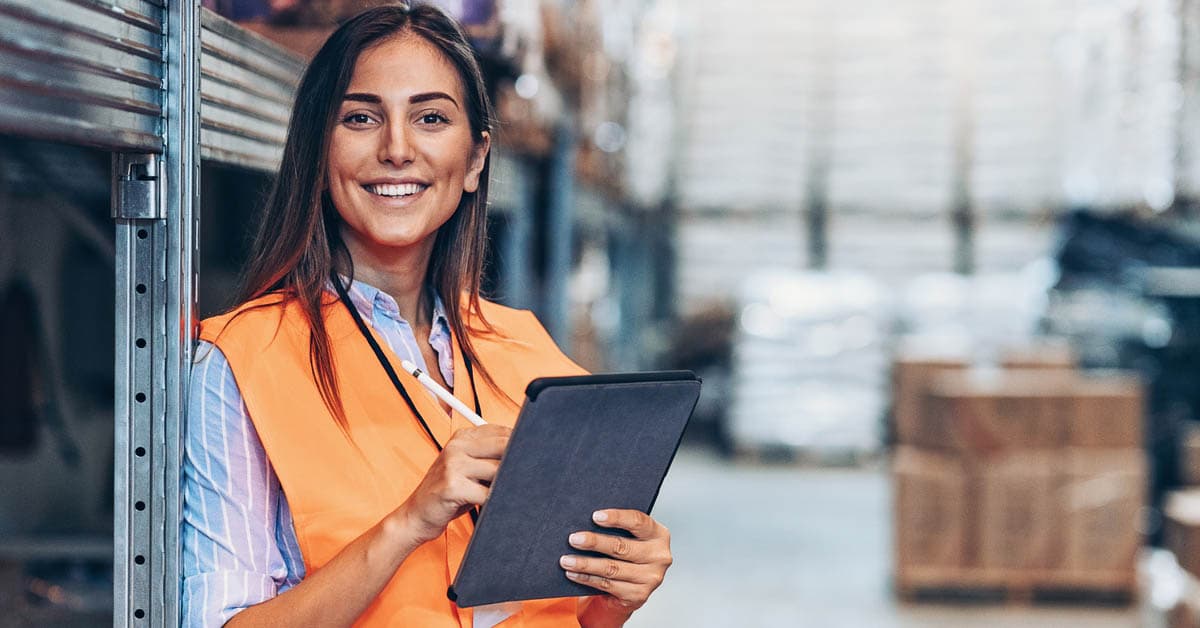
When you think about a culture of safety, what comes to mind?
For many, it’s lofty ideas about attitudes of employees, whether they take ownership of identifying hazards and how engaged they are in safety as a whole.
Achieving this state, however, requires a command of more practical matters such as safety inspections that reveal what’s really happening on the plant floor.
Multiple U.S. Occupational Safety and Health Administration (OSHA) standards require frequent or even daily attention, including personal protective equipment (PPE) and respiratory protection standards. Moreover, OSHA views safety inspections as a core component of an effective safety program.
Today we’re looking at how to leverage these inspections to create a culture of safety, including how to raise awareness, improve decision-making and prevent repeat incidents. As we go, we’ll also look at how a digital inspection platform can act as a catalyst for lasting change.
Raise Awareness
Questions that appear on safety inspection checklists such as daily preventive maintenance (PM) audits that take place at the workstation help call attention to known and emerging risks. This workforce awareness is essential to promoting a culture of safety.
The problem is this:
How do you truly engage employees in noticing conditions and hazards, instead of just speeding through checklists on auto-pilot?
The key is continuously updating checklists, for example by:
- Adding new questions after safety incidents
- Checking to see whether corrective actions are in place and working
- Linking job safety analysis (JSA) updates to new questions
- Rotating and randomizing questions using plant floor inspection software
In addition, for those using software, companies can require employees to upload photos for specific questions to verify critical items or just to keep people paying attention.
Report on Risks
A culture of safety requires timely access to safety performance data for making decisions and intervening before incidents occur. Plant floor inspections are a crucial source of this data, allowing teams to:
- Get insights from the front line on risks
- Monitor trends and leading indicators
- Improve communication with the team regarding risks, performance and goals
- Measure the effectiveness of safety programs
Daily inspection data should be readily available to safety managers and committees. Unfortunately, this can be difficult when relying on paper checklists stored in a file cabinet or waiting to be entered into a spreadsheet.
Automated platforms, on the other hand, give teams a window into real-time safety conditions on the plant floor. Having data instantly at hand gives leadership information for conducting management reviews so they can take action on trends and even identify systemic issues that aren’t just one-off nonconformances.
Develop Leading Safety Indicators
Creating a culture of safety in a plant relies on the ability to identify and actively track leading indicators, an area where plant floor inspections play a key role.
Leading safety indicators are those metrics that correlate directly with safety performance measures and goals. Near-misses for example, are a leading indicator of safety incidents, highlighting where future safety failures are likely to occur.
Plant floor inspections, Gemba walks and safety audits provide data for developing and monitoring leading safety indicators such as:
- Number of inspection findings
- Frequency of inspections
- Number of reported hazards
- Availability of personal protective equipment (PPE)
- Compliance with safety standards and protocols
Prevent Recurrence
If you want a culture of safety, you need to be able to root out and fix problems permanently. Plant floor inspections help achieve this goal by giving safety managers tools to verify corrective actions and log observations about known hazards.
To that end, it’s important to update inspection checklists after safety incidents, audit findings and corrective actions. For example, let’s say an eye-washing station malfunctioned when an employee needed to use it—a severe problem considering that the person needing to use it can’t see to find another one.
Rather than just fixing the one piece of equipment and moving on, you’ll want to check back in periodically to see it’s working. You’ll also want to add the question to inspect eye-washing stations elsewhere. That means either updating and redistributing paper checklists, or just adding another question into the rotation on your inspection software.
Why is this so important?
From a safety culture perspective, it’s not just about minimizing incidents. The truth is that if you don’t make a visible effort to find and fix problems for good, your team won’t believe that you’re truly committed to safety. And when that’s the message you’re sending, you might as well not have a safety program at all.
When you don’t conduct frequent safety inspections and audits, you leave it to the OSHA inspector to uncover your organization’s issues. It’s a dangerous approach that stands in the way of safety, increasing risks to workers and the company.
Used correctly, however, plant floor inspections can provide data to proactively track risks, communicate with your team and empower employees to speak up when they notice hazards. With those pieces in place, companies can build a path towards a true culture of safety.