How to Reduce Manufacturing Costs: 5 Strategies to Lower Costs Without Sacrificing Value
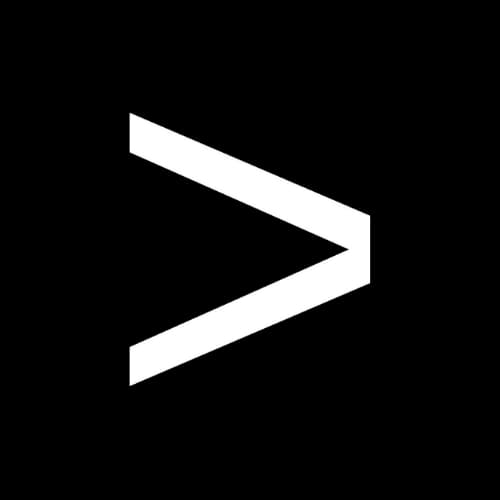
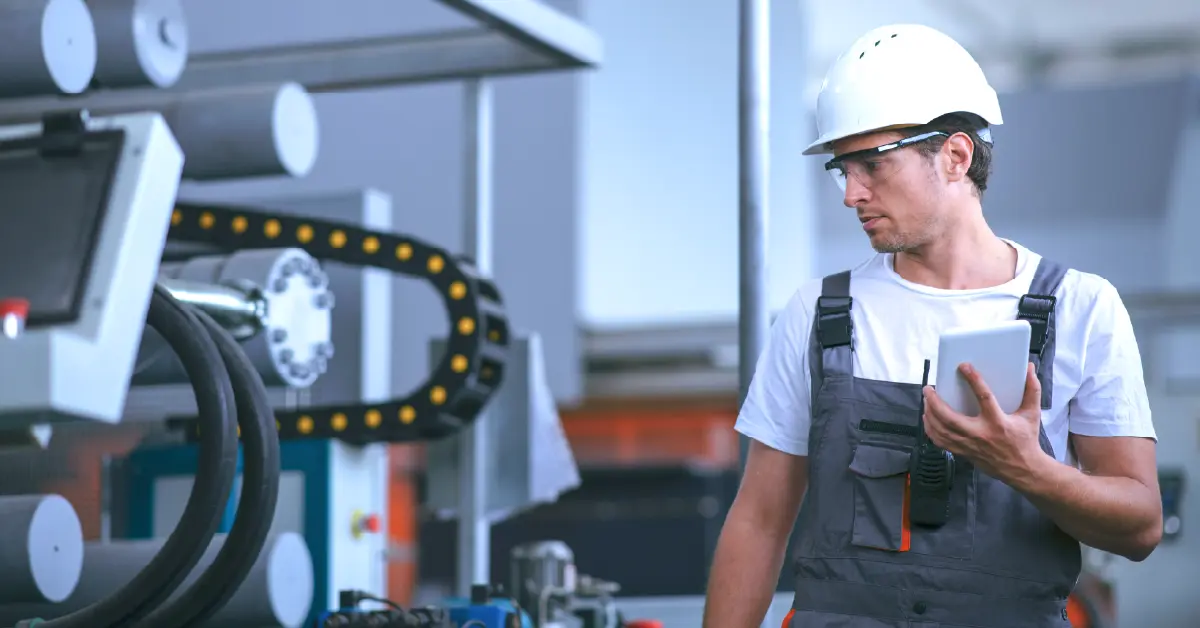
Increasing profits isn’t always about raising prices. It’s also about cutting costs. This is especially true in manufacturing, where waste can happen anywhere along the supply chain. How can manufacturers prevent these avoidable losses to get to the next level of performance and profitability?
In this post, we’ll address five key approaches to reduce waste. We’ll explore how to reduce manufacturing costs by:
- Streamlining production processes and improving efficiency
- Identifying risks before they manifest into bigger, costly problems
- Reducing scrap and rework upstream
- Automating key processes and using data-driven insights
- Enhancing workforce training and engagement
Download your free eBook on Cost of Quality: The Hidden Truth About Your Most Important Operational Metric
#1: Streamline Production Processes and Improve Efficiency for Reduced Production Costs
Complex manufacturing workflows, old systems, and long supply chains lead to inefficiencies, errors, and unnecessary waste—all of which can result in high operating costs.
Optimizing workflows can lower your costs without disrupting production—in fact, they should even improve your productivity levels.
Here are some methods of reducing overhead costs through process refinement:
Implement Lean Manufacturing Principles
We wrote about Lean in previous posts, but to summarize, lean manufacturing focuses on maximizing customer value by creating the most straightforward and cost-effective production line possible without compromising on quality.
The main principles of lean manufacturing include:
- Identifying value, or deciding what is most important and focusing on the processes that are directly linked to the customer’s experience and satisfaction.
- Mapping the value stream to identify and remove any tasks within the manufacturing process that don’t matter to the end-user.
- Eliminating bottlenecks within the production line for a smooth and uninterrupted flow from raw material to people to shipping.
- Establishing a pull-based system to eliminate the costs associated with overproduction, surplus, and storage.
- Seeking perfection through continuous improvement by creating a workplace culture that encourages everyone—from frontline workers to management—to take an active role in identifying areas that could be refined.
Utilizing lean manufacturing principles is a tried-and-tested way to reduce manufacturing costs.
Develop and Enforce Standardized Processes
Manufacturing standard operating procedures (SOPs) enforce ensure consistency and quality by standardizing all steps, processes, and practices.
They help employees perform tasks in a consistent way, which reduces errors and ensures a higher level of quality control. That can result in lower manufacturing costs.
SOPs also offer the added advantage of:
- Enhanced workplace safety
- Providing a standard to audit against
Digital SOPs are far superior than paper, as they offer employees real-time access to the most up-to-date version whenever they need it. Giving new employees the benefit of having digital SOPs on hand can also accelerate their training by tailoring instructions to an individual’s certification level.
Now that we’ve discussed how standardizing your processes and applying lean manufacturing methods can contribute to cost reduction in production, let’s look at how you can proactively prevent costly failures, including equipment.
#2: Identify Risks Before They Manifest into Bigger, Costly Problems
Identifying, mitigating, and managing risk is at the heart of modern manufacturing, especially in light of ISO 9001:2015’s emphasis on risk-based thinking.
Any disruption to your daily operations affects your bottom line. Considering the nature of your supply chain, a delay or a small defect in your machinery on one end of the production line can lead to expensive recalls or equipment failure on the other end.
Not only does taking a proactive approach to risk management lower manufacturing costs, it will inevitably help refine operational efficiency.
Proactive measures that help mitigate risk include:
- Predictive maintenance with IoT technology
- Layered process audits (LPAs)
- Employee training and engagement
For example, predictive maintenance can reduce downtime and extend the lifespan of machinery. Internet of Things (IoT) technology can help you find effective ways to reduce costs.
IoT sensors on critical equipment can directly monitor your machine’s performance, helping to reduce energy costs. They allow you to collect real-time data and use it to detect signs of wear, overheating, or other potential failures as early as possible. Once something is detected, they can trigger a process of corrective actions to fix the problem.
This preventive and proactive approach allows you to take care of problems before they turn into expensive failures.
Benefits of using predictive maintenance technology:
- You can schedule maintenance during non-peak hours, so there are no interruptions to the production schedule, and therefore, no loss in output.
- Taking care of small maintenance issues early and often means you’ll avoid larger issues or machine malfunctions in the future.
- Proactive measures can extend the lifespan of your equipment, which will maximize your ROI and significantly reduce your manufacturing overhead.
Now that we’ve taken a proactive approach to risk identification and assessment, let’s look at how inventory management can reduce the cost of storing and overstocking.
#3: Evaluate Upstream Quality Processes to Reduce Scrap and Rework
Costing up to 2.2% of manufacturing revenue, scrap and rework may not be completely unavoidable, but there are ways to bring that number down simply by evaluating your upstream processes and addressing issues and inefficiencies.
Factors that lead to scrap and rework include operator errors, machine issues, environmental conditions (temperature, humidity, etc.), measurement inaccuracies, and material problems.
Here are some ways you can minimize instances of these issues:
- Create and digitize SOPs
- Conduct Failure Mode and Defect analyses (FMEA)
- Perform frequent plant floor audits
Focusing on upstream processes also improves overall productivity, which, of course, drives down costs.
For example, regular audits and tools like FMEA help identify potential risks before they turn into something much more expensive to fix. As a result, manufacturing companies can produce higher-quality products with fewer interruptions, leading to significant cost savings and better performance metrics like improved Overall Equipment Effectiveness (OEE) .
We’ve just discussed ways to reduce scrap and rework. Now let’s take a look at how automation can lead to better insights and what that means for your bottom line.
#4: Automate Key Processes & Use Data-Driven Insights to Develop Strategies
Investing in automation and technology is fundamental to modern manufacturing processes and can lower the costs of your manufacturing operations. Automation also benefits frontline workers and companies whose processes rely heavily on labor-intensive, repetitive, or complex tasks—not to mention the myriad of insights its data can offer.
We’ve already discussed predictive maintenance. Now, let’s see how other technologies can help cut unnecessary manufacturing expenses.
RPA for Maximizing Efficiency and Reducing Labor Costs
Robotic process automation (RPA) speeds up production by taking care of repetitive but necessary tasks like assembly, product quality control, and packaging. It also reduces the indirect costs included in human labor, and redirects frontline workers to more important parts of their job.
Speed, efficiency, and accuracy of robotic technology all contribute to higher output but lower overall manufacturing costs.
Analytics to Track Production, Identify Issues & Reduce Costs
With all this data at their fingertips, businesses can gather insights to help lower manufacturing costs by identifying inefficiencies or waste anywhere along the supply chain. Without having to guess or spend time testing new process improvements, manufacturing companies make faster and more accurate business decisions.
Now that we’ve looked at cost-saving strategies through innovation, how can workforce-related strategies lower excess costs?
#5: Enhance Workforce Training and Engagement
We’ve already seen through lean manufacturing techniques that a workplace culture which encourages employee involvement is one of the ways to seek perfection through continuous improvement.
When businesses invest in training and upskilling their staff, they can expect several benefits on top of reducing costs in manufacturing.
Employees who are asked for input on process improvements are more likely to flag issues early and take an active role in fine-tuning SOPs for cutting costs and improving outputs. Similarly, frontline workers will be the first to detect and flag defects early in the production process, which could have been more costly to fix down the road.
Well-skilled labor is faster, more accurate, and less likely to make expensive mistakes or defective products. Investing in workplace training also reduces the risk of injury, which could lead to expensive worker compensation and administrative costs.
Going out of the way to ensure workers are safe and well-trained is a huge morale booster that will reduce employee turnaround, another direct labor cost.
In general, the more manufacturers can invest in the training, safety, and engagement of their employees, the more likely companies can minimize unnecessary waste—a huge cost saver.
Try These Strategies to Reduce Unnecessary Overhead
Reducing the cost of production and manufacturing is a fundamental challenge for manufacturing companies. With technology and innovation, businesses can solve problems faster and achieve higher first-time quality. Try these top five manufacturing cost reduction strategies for better outputs at a lower cost.