How to Use Operator Feedback in Layered Process Audit Questions
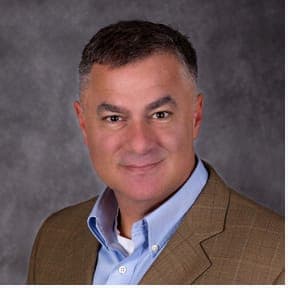
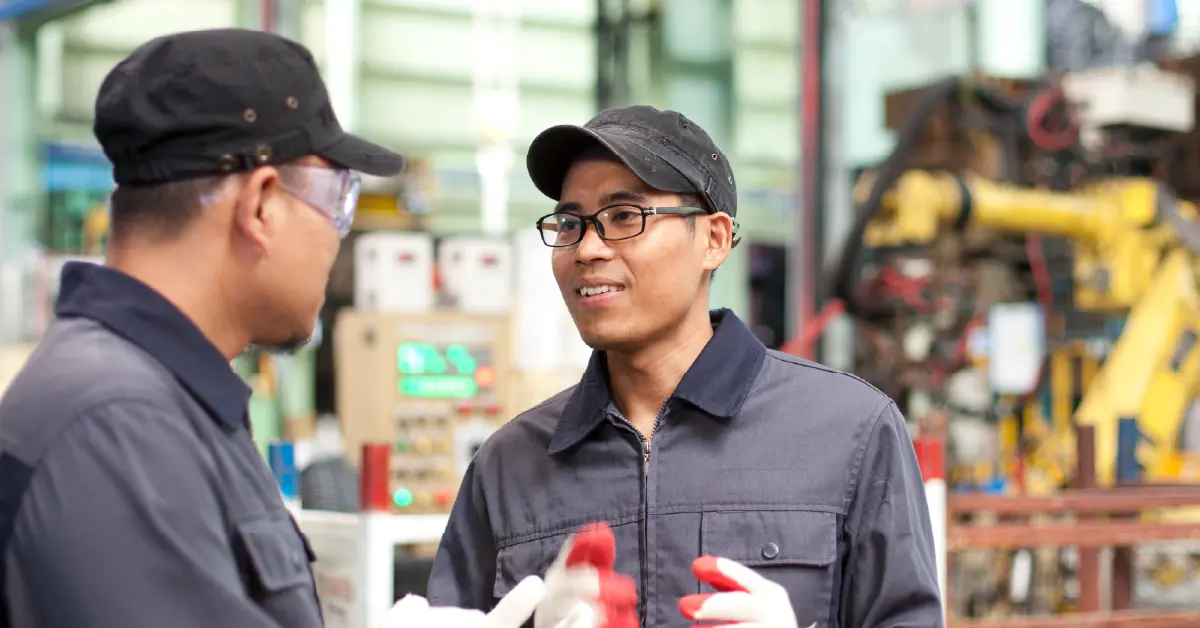
When most people think of layered process audits, they think of holding the process to the standard. However, there are other benefits to doing these high frequency audits. One of the biggest advantages of implementing a layered process audit program is the opportunity it provides for soliciting operator feedback.
This feedback often leads to important insights. For example, you may learn operators aren’t following a standard because they don’t have the right tools, they have insufficient training or it’s ergonomically difficult to do the work at their station. In addition, this feedback can reveal continuous improvement opportunities.
To reap these rewards, it’s key to start by including operator feedback when writing layered process audit questions. Here we take a look at how to do it, including the most important places to get operator input and why it’s essential to creating a culture of quality.
Download your free Ultimate Guide to Layered Process Audits for more LPA question best practices, examples and tips
Finding Your Critical Layered Process Audit Questions
When you’ve written layered process audit (LPA) questions for a process area, the last step we recommend at The Luminous Group is to ask operators, “What is the most likely thing to fail today?”
Maybe they tell you it’s contamination in a raw material, or that the cutting fluid on a machine might run low. The key is that operators know the weak link in the process, even if they’ve only been on the job a short time. That weak link becomes the LPA question you should ask at the start of every shift.
The above feedback might be turned into questions such as:
- Is the raw material box completely covered with a lid?
- Is the cutting fluid pressure on the machine between 15 psi and 20psi psi?
If you’re using LPA software, you can use custom tags to rotate these high-risk questions in frequently so you ensure the issue gets regular attention.
Eliminating Low-Value Audit Questions
The next area you want to make sure to solicit feedback from operators is to identify and remove questions that bring no value to audits. The crucial thing to remember here is that LPA questions must focus on elements that vary. Something may be important and easy to check, but if it never changes then it doesn’t need an LPA question.
To address this, you should have operators look over questions and point out the few that never fail. This isn’t to say that operators should have veto power over questions, only that they have first-hand knowledge of which elements don’t actually vary in practice.
For instance, let’s say you put in a corrective action involving a poka-yoke (error-proofing) device bolted onto a machine. Are you going to ask every day if it’s bolted in place? Once you’ve established it’s there and working, how often do you need to check on it? The answer is to ask the operator.
Because while you may think something is important, the reality is they might never have seen it cause a problem in 10 years on the job. That’s not a question worth asking. What’s more, it’s these types of low-value questions that make people feel like LPAs are a waste of time. When that happens, people start speeding through audits without paying attention to details—which is precisely when problems get missed.
Reviewing Layered Process Audit Questions
The final place you should solicit operator input on questions is when you conduct your 3-month or 6-month review of your LPA system. At this point, you want to go back to the operators and ask, “Have these questions helped you in any way?”
The operator might say, for example, that LPAs have helped them be more aware of a safety risk or helped make sure they put their tools away correctly. Based on this, you can find other processes where a similar question would help people keep tools put away properly. This is how you translate smaller wins into plant-wide improvements.
From a big-picture perspective, gathering operator feedback is part of a culture of engagement and listening that LPAs are uniquely suited to provide. It shows respect for the operator’s expertise, providing more value to the audits while increasing buy-in for your LPA goals.
Ultimately, it’s up to management to communicate that what you’re doing isn’t just about the questions themselves. It’s also about improving the process that the questions address and operators have a central role in making that happen.