How to Verify Control Plans with Layered Process Audits
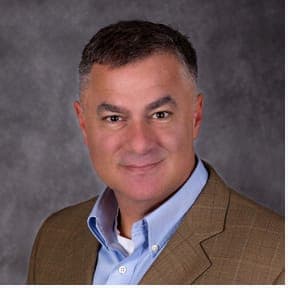
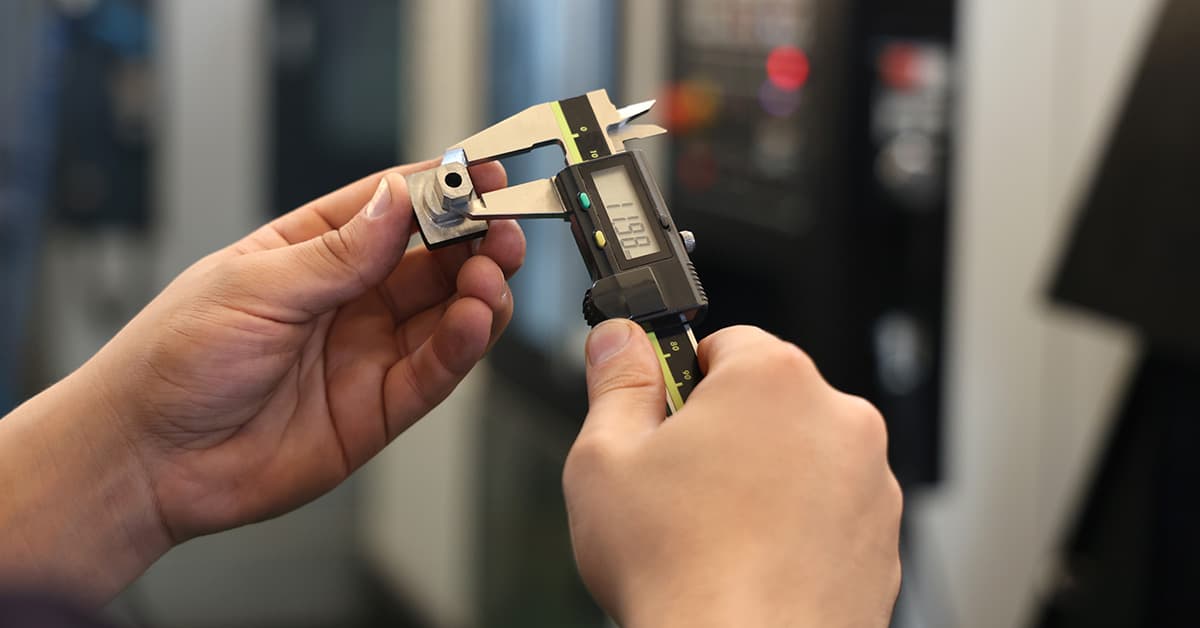
Picture the following scenario:
A control plan states there should be a dedicated gauge for a product at a workstation, but the gauge isn’t present and an operator is using a caliper instead.
The employee believes they are protecting quality, but the caliper isn’t calibrated, nor is it sufficient to the task.
This departure from standards is exactly the kind of small drift or hidden factory process that increases the risk of production defects.
Rather than waiting weeks to find out the operator has the wrong tool, a layered process audit (LPA) to verify your control plan can help find the problem right away.
At The Luminous Group, we recommend using LPAs to reinforce control plans to better support that operators are using the right tools and techniques. Taking this critical step ensures a supervisor is on the plant floor checking to see that the work cell is set up to the standard and the gauge is there for the operator to use.
Let’s look a little deeper at the elements of the control plan that can be verified, and the number one mistake to avoid in creating and verifying your control plan.
Download our free Ultimate Guide to Layered Process Audits for more best practices and tips to improve quality with plant floor audits
What is a Control Plan?
A control plan outlines methods for ensuring products and processes meet specifications. Control plans have multiple elements which include:
- Product characteristics
- Process characteristics
- Specifications and tolerances
- Evaluation and measurement techniques
- Sampling quantity and frequency
- Control method
- Reaction plan
Using control plans correctly starts with getting failure mode and effects analysis (FMEA) right. An FMEA identifies risks and controls to mitigate those risks, which then get fed into the control plan. LPAs help ensure you hold those controls in place, reducing the risk of a quality escape.
Which Control Plan Elements to Verify with LPAs
Layered process audits (LPAs) are short audits that take place every shift to verify key process inputs. When applying these checks to control plans, you will want to emphasize that your LPAs verify proactive elements that are critical to meeting your customers’ requirements. The LPA uses the process failure mode effects and analysis PFMEA rankings of risk, severity in particular, to identify the most important elements on the control plan to verify. At The Luminous Group, we emphasize the process characteristics that influence the key product characteristics.
From there, you’ll want to look at methods outlined under control plan, focusing on whether operators are using the right tools at the right frequency. For instance, under evaluation and measurement, you’ll want to ask questions like whether the operator has the right gauge and whether they are following the gauge instructions.
Sampling is another element of the control plan to check. For example, if the control plan states that the operator should check the oil pressure on a machine once every hour, when was the last time they actually checked that pressure? Going even a step further, you can have the LPA check the pressure on the spot to make sure it’s still in spec.
Here’s another example:
Let’s imagine your control plan says you’re going to run 100% of parts through the vision system. Rather than checking if you’re running 100%, you can run a known bad part or “red rabbit” and use the LPA to see whether the system correctly detects it.
The Number One Mistake to Avoid
The biggest mistake we see is that manufacturers weigh control plans heavily towards product validation. In reality, control plans should be 80% process validation and 20% product validation.
Using Mobile LPA Software to Verify Your Control Plan
A mobile audit platform like EASE can simplify the process of using LPAs to verify your control plan. Tools you can leverage include:
- Automated scheduling and notifications to boost audit completion rate, improving awareness of control plan requirements on the plant floor
- Labeling LPA questions with a control plan tag for easy rotation, randomization and reporting visibility
- Using photo uploads to demonstrate what good and bad looks like or to verify that an audit took place
Control plans are an essential tool in the quality professional’s toolkit, but they don’t exist in a vacuum. More than just documenting controls, you have to make sure your plant is actually holding them in place.
LPAs ensure you close that loop, so it’s not a customer complaint that alerts you to the fact that your control plan isn’t being followed. LPAs help you find these problems earlier in the manufacturing process, reducing defects and wasted resources while protecting quality and safety for customers.