Understanding the 7 Principles of Quality Management: The ISO 9001 Standard
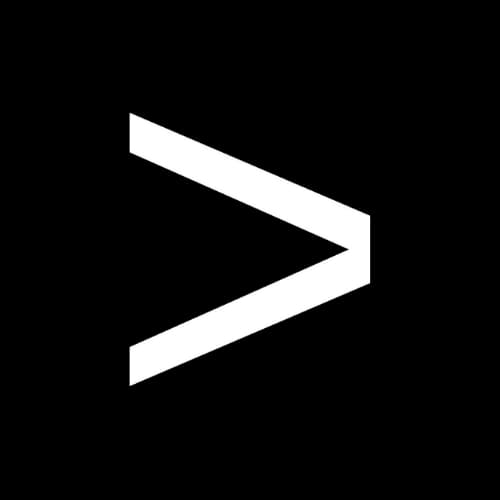
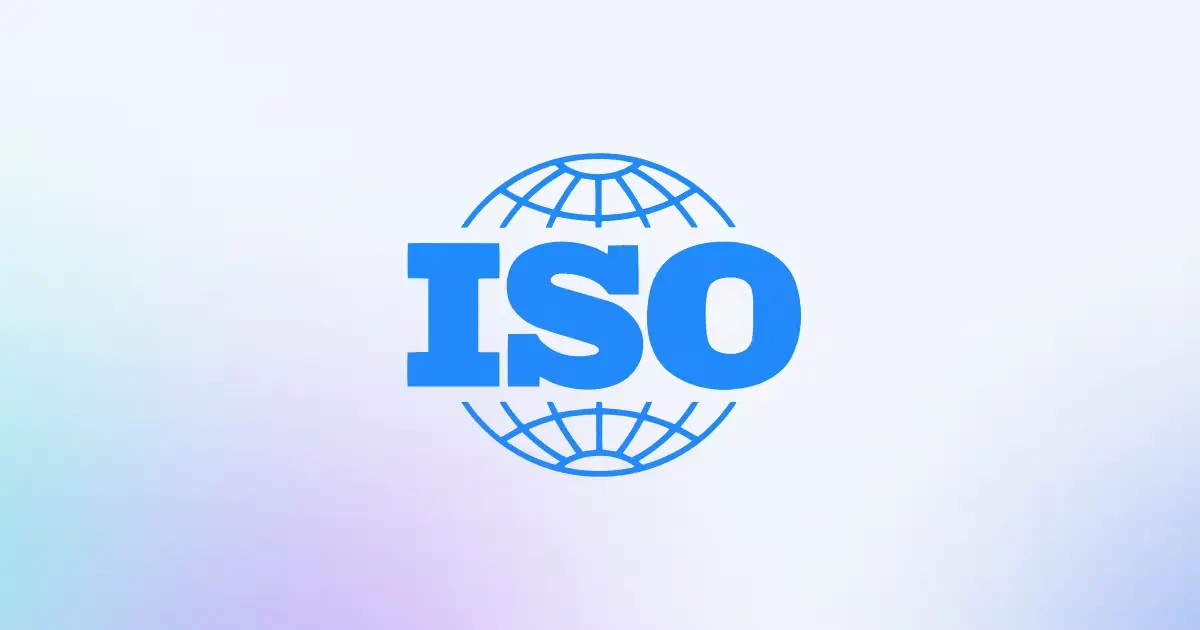
Far and away, one ISO standard towers above all others in terms of the sheer number of certifications and overall influence in manufacturing.
That standard is ISO 9001, with over 1.6 million sites certified worldwide.
First published in 1987, ISO 9001 is built around helping companies organize and continuously improve the efficiency of their quality processes. It also forms the basis for other industry international standards such as IATF 16949 for automotive quality and AS9100 for aerospace quality management systems.
The goal: deliver compliant, high-quality products that satisfy customers and provide a foundation for the long-term success of the company.
Here we explore the seven quality management principles that are the basis for ISO 9001, including:
- Customer focus
- Process approach
- Leadership
- Engagement of people
- Continuous improvement
- Evidence-based decision making
- Relationship management
First, however, we must understand why these seven principles are so important.
Learn what quality may be costing you with our free eBook on Cost of Quality: The Hidden Truth About Your Ultimate Quality Metric
The Importance of the 7 Principles of Quality Management
Our world has always relied on international trade, and with that comes the need for consistent quality standards. The International Organization for Standardization (ISO) addresses this need. The ISO 9001 principles specifically provide a framework for quality management systems (QMS) that guides organizations to ensure consistency, and to improve the efficiency and quality of their products and services.
ISO 9001 is part of the ISO 9000 family of quality standards. ISO 9000 acts as an overall reference document that explains fundamental quality management concepts and vocabulary. ISO 9001 builds upon the ISO 9000’s framework and terminology, providing specific, actionable requirements to implement a QMS that can be certified.
Let’s take a look at the seven quality management principles of ISO 9001.
The Seven Principles of ISO 9001
1. Customer Focus
ISO 9001 puts customer satisfaction front and center, recognizing that the primary goal of quality management is to meet and even exceed customer expectations.
Clause 4.2 of ISO 9001 details requirements around understanding the needs of interested parties, chief among them being customers. Under ISO 9001, manufacturers must:
- Identify customer requirements and link them to your organization’s objectives
- Evaluate and adjust processes to ensure they result in products that meet customer expectations
- Communicate customer needs with the organization regularly
- Monitor customer satisfaction to drive process and product improvements
- Be proactive in managing customer relationships
By designing their processes around creating high-quality products that satisfy customer expectations, companies also lay the foundation for improved profits and a strong brand reputation.
2. Process Approach
Like other ISO standards, ISO 9001 emphasizes the Plan-Do-Check-Act (PDCA) process approach to improving customer satisfaction. This process requires organizations to:
- Systematically define their processes (plan)
- Track and manage those processes effectively (do)
- Monitor performance consistently (check)
- Improve processes based on data and information (act)
PDCA represents a continuous cycle that promotes continuous improvement of processes and products. The clauses of ISO 9001 all fit into different steps of the PDCA process, as shown in the table below.
PDCA Step | ISO 9001 Clauses |
Plan |
|
Do |
|
Check |
|
Act |
|
3. Leadership
Clause 5 of the ISO 9001 on leadership, notably, is unique in that it fits in with every step of the PDCA process since leaders should be involved in all aspects of quality management.
In recent years, there has been an increased emphasis on management involvement across all ISO standards. That’s because without leadership participation, any quality effort is doomed to failure. Leadership involvement is also key to coordination and communication, helping facilitate a more effective quality process overall.
Because of this, ISO 9001 Clause 5 centers entirely on leadership, detailing requirements like:
- Setting the direction in terms of communicating the organization’s quality policy and objectives
- Promoting the PDCA process and risk-based thinking
- Taking accountability for ensuring that the quality management system delivers results
- Providing resources and support to facilitate continuous improvement
Leaders are responsible for creating a shared vision and culture of quality in the organization, one where management sets a positive example, empowers others, and recognizes their contributions.
4. Engagement of People
ISO 9001 recognizes that an engaged workforce is the backbone of value creation in organizations today. People at all levels must be involved with quality, with a focus on skill-building, empowerment, and recognition. This, in turn, improves team satisfaction and contributes to a shared culture of quality where everyone’s work matters.
Key actions here include:
- Communicating to individuals why their role is important to quality
- Having open discussions where you solicit feedback and invite people to share their knowledge and experience
- Measuring employee satisfaction and taking action based on the results
5. Continuous Improvement
A focus on continuous improvement makes manufacturers better able to adapt to change and even innovate in the face of new risks.
This quality management principle focuses on:
- Effective root cause analysis combined with corrective and preventive action
- Having a specified process for reacting to and documenting nonconformities
- Deploying improvement projects and tracking their results
- Making use of ongoing monitoring and measurement to inform continuous improvement projects and objectives
6. Evidence-Based Decision Making
Far too often, it’s the loudest voice in the room that ends up driving decisions. ISO 9001’s focus on data-driven deliberations, on the other hand, provides for more objective decisions. Not only does it improve decision-making, but it also provides a mechanism to review, challenge, and demonstrate the effectiveness of previous choices.
Action points around evidence-based decision-making include:
- Monitoring manufacturing KPIs
- Sharing accurate, reliable data with relevant parties
- Analyzing data in a timely manner and making sure people know how to evaluate it
7. Relationship Management
ISO acknowledges the importance of managing relationships with all interested parties, such as:
- Customers
- Employees
- Investors
- Partners
- Suppliers
- Society overall
Specific emphasis is placed on supply chain relationship management, as this is critical to being able to meet customer needs and expectations. In this context, action items should focus on:
- Monitoring supplier performance and providing them feedback
- Sharing information and resources to create value
- Enlisting suppliers to collaborate on improvement projects
The Key Benefits of ISO 9001’s Principles of Quality Management
Following these principles provides several benefits to organizations:
Improved Customer Satisfaction
The ISO 9001 standard helps businesses align their operations with customer expectations by prioritizing customer focus and feedback mechanisms. When manufacturers have ways to identify and address customer needs, their processes and, hence, products have fewer flaws and errors.
Accepting feedback and making changes based on it also makes customers feel heard, which builds trust and loyalty. This means they are more likely to recommend the business to others.
Higher Operating Efficiency
ISO 9001 encourages businesses to follow industry best practices and align processes with quality objectives, which reduce waste and inefficiencies. Since the core principles outlined in ISO 9001 encourage continuous monitoring and improvement, organizations can improve efficiency and respond to change quickly, leading to higher profitability and a competitive edge in the market.
Improved Decision Making
Collecting, analyzing, and sharing reliable information allows an organization to make choices that help operational performance and reduce risk. It also helps their effectiveness and alignment with strategic goals by providing a mechanism to review and challenge past choices.
The ability to make better decisions leads to more accountability and greater confidence in outcomes. Evidence-based decisions allow a business to improve continually and yield better long-term results.
Increased Revenue
We’ve seen how ISO 9001’s quality management principles lead to greater efficiency and less waste. They also help create consistent and predictable results that meet and exceed customer expectations. The former can reduce expenses, while the latter can lead to higher sales. Additionally, certification also creates opportunities to enter into new markets, contracts, and partnerships where quality assurance is necessary, further boosting revenue potential. All these factors combine to create a pathway toward higher profits.
Better Process Integration
Instead of considering each process in isolation, ISO 9001 treats them as a part of a larger system. When all processes are integrated into a cohesive framework, all departments can work together effectively. This creates a culture of communication between teams, which in turn gets rid of information silos. It also helps align activities with the wider business goals, which means identifying areas of improvement becomes easier. By connecting workflows and responsibilities, businesses can optimize efficiency, reduce redundancies, and ensure consistency across all departments.
Improved Credibility
When an organization commits to the ISO 9001 standards and is certified, it demonstrates a willingness to continually improve and deliver high-quality products. The ability to deliver consistent quality reliably leads to more trust, which not only helps bring in new customers but also strengthens existing relationships. This improved reputation also helps build better credibility with employees, partners, and other stakeholders.
Greater Employee Engagement
ISO 9001’s emphasis on internal communication creates a culture where employees feel more involved and valued. It encourages them to build skills, share more openly, and collaborate—all critical areas for employee retention.
Better Supplier Relationships
One of ISO-9001’s core quality principles is managing relationships with everyone, including suppliers. Collaborating closely with suppliers helps create shared value, where they are as invested in improving quality as you are. It also reduces risk and leads to smoother operations with timely deliveries and cost control.
Risk Reduction
ISO 9001 helps organizations identify, assess, and mitigate operational risks. By implementing risk-based thinking, businesses can prioritize efforts to prevent potential issues before they occur. This approach reduces the likelihood of nonconformities, operational disruptions, and reputational damage. Proactively addressing risks also enhances organizational resilience, enabling businesses to adapt to uncertainties and maintain consistent quality in their products or services. Reduced risks translate to greater customer confidence and operational stability.
Using Technology to Strengthen Quality Management Standard (QMS) and Become ISO 9001 Compliant
Technology has a key role to play in terms of safeguarding compliance with ISO 9001 requirements at every step of the PDCA process.
For example, digitizing standard operating procedures (SOPs) can help you ensure that all of your processes are documented and updated, which is a key focus of ISO audits.
Quality tools such as digital audit and inspection platforms, too, promote more effective, efficient ISO compliance with:
- Plant floor checklists for monitoring processes and generating data to drive decision making, continual improvement and leadership involvement
- Issue tracking to document and handle nonconformities effectively
- Dynamic training tools to increase workforce competency and engagement
Effective quality management is a multi-faceted process involving a wide variety of stakeholders, making technology a critical enabler of success. Even for manufacturers who do not certify to the ISO 9001 standard, following ISO quality management principles can help improve performance and competitive standing in the industry.