Jidoka: What Is It?
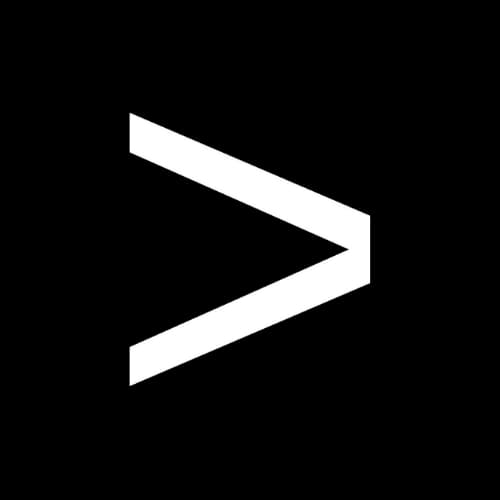
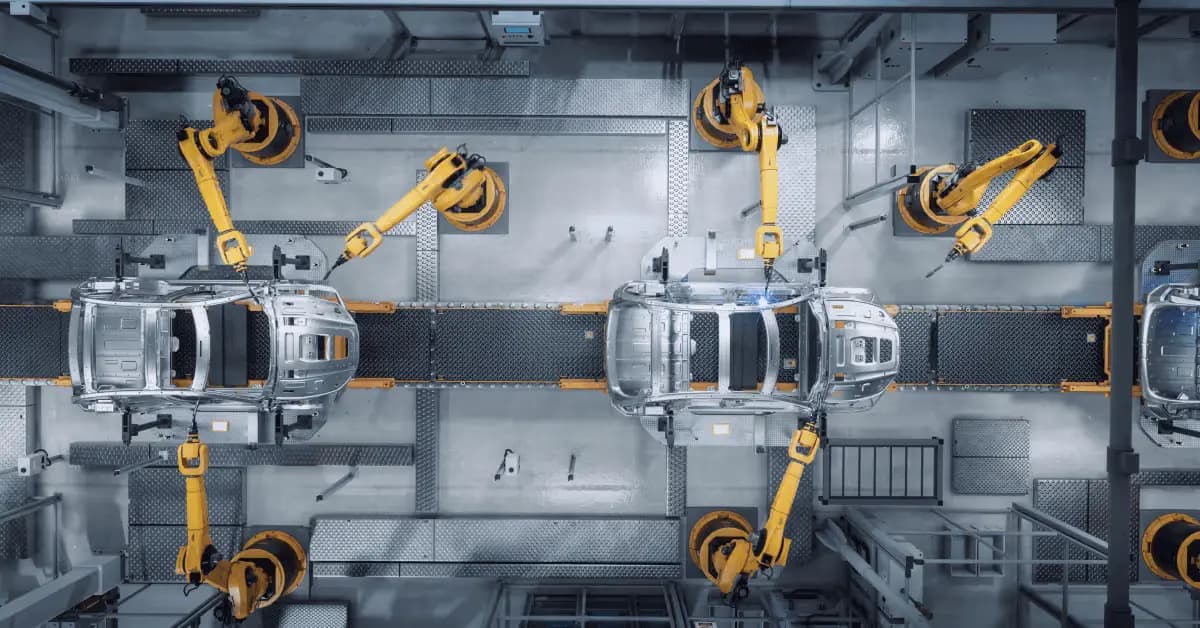
The concept of Jidoka emerged as a transformative manufacturing approach that fundamentally reimagines quality control in production processes. Its roots can be traced back to the early 20th century, specifically to the innovative work of Sakichi Toyoda, a pioneering Japanese textile maker and inventor who dramatically changed how machines interact with human intelligence.
The Origin of Jidoka
Before the widespread adoption of mechanized looms and spinning machines, textile manufacturing relied heavily on manual labor. Workers, often children, operated spinning wheels and handlooms, which required significant time and effort to produce fabric and also led to quality issues and inconsistencies in the fabric produced.
Given these issues, Sakichi Toyoda sought to revolutionize the industry. He identified that existing looms were inefficient and prone to production interruptions caused by thread breaks. This led to his most significant innovation: an automatic loom with several revolutionary mechanisms:
- Automatic thread break detection: Toyoda’s automatic loom was equipped with a mechanism that could detect when a thread broke during the weaving process. This innovation ensured that any breakage was immediately identified, preventing the production of defective fabric and maintaining the quality of the output.
- Immediate machine shutdown when an abnormal condition occurred: The loom was designed to stop automatically as soon as an abnormal condition, such as a thread break, was detected. This immediate shutdown prevented further damage and waste, allowing operators to address the issue promptly and resume production with minimal disruption.
- Reduced human monitoring requirements: With the automatic detection and shutdown features, the need for constant human supervision was reduced significantly. Operators no longer had to continuously monitor the machines for issues, freeing them to focus on other tasks and increasing overall productivity.
- Dramatically improved production efficiency: The combination of automatic detection, immediate shutdown, and reduced human monitoring led to a dramatic improvement in production efficiency. The loom could operate more reliably and consistently, producing a high-quality fabric at a faster rate and with less waste.
In addition to these innovations, Toyoda introduced several key manufacturing principles, including embedding intelligence directly into machines, creating systems that could autonomously detect and respond to problems, and prioritizing quality over continuous production.
Toyoda’s automatic loom patent eventually was sold to Platt Brothers & Co, a British company that continued to push the forefront of technological innovation in the textile industry, resulting in improved techniques used in cotton spinning and perfecting machines including the carding machine for yarn and thread production. The money from the sale of the patent generated funds that eventually helped establish the Toyota automotive manufacturing enterprise, fundamentally cementing Toyoda’s technological innovations to the company’s future success.
Key Principles of Jidoka
Jidoka, often translated in English as “autonomous automation” or “intelligent automation,” represents a holistic management strategy that empowers machines and operators to prevent defects proactively rather than waiting to detect them after they occur.
Jidoka’s approach to quality control is multifaceted, encompassing several core principles that collectively enhance production efficiency and product quality. By integrating intelligence into machines and empowering operators, Jidoka ensures defects are detected as well as prevented from reoccurring. Let’s delve into the key principles that define Jidoka to understand how they contribute to a robust manufacturing process:
- Autonomous detection: Machines are designed with embedded intelligence to recognize and respond to quality issues without constant human monitoring. This automation reduces human error and increases operational excellence.
- Automatic stoppage: Jidoka’s main goal is to stop production immediately when an abnormal condition is detected. Unlike traditional manufacturing approaches that might allow defective products to continue through the production line, Jidoka mandates immediate intervention.
- Correct the issue: After the production line is stopped, immediate action is taken to correct the cause of the problem. This often involves the human operators identifying the issue, fixing it and ensuring it is resolved before resuming production. This step helps prevent the recurrence of the same error and ensures quality control.
- Root cause analysis: Jidoka is about more than simply stopping production; it is designed to detect abnormalities and understand why a problem occurred. Each defect becomes an opportunity for continuous improvement, driving systematic problem-solving.
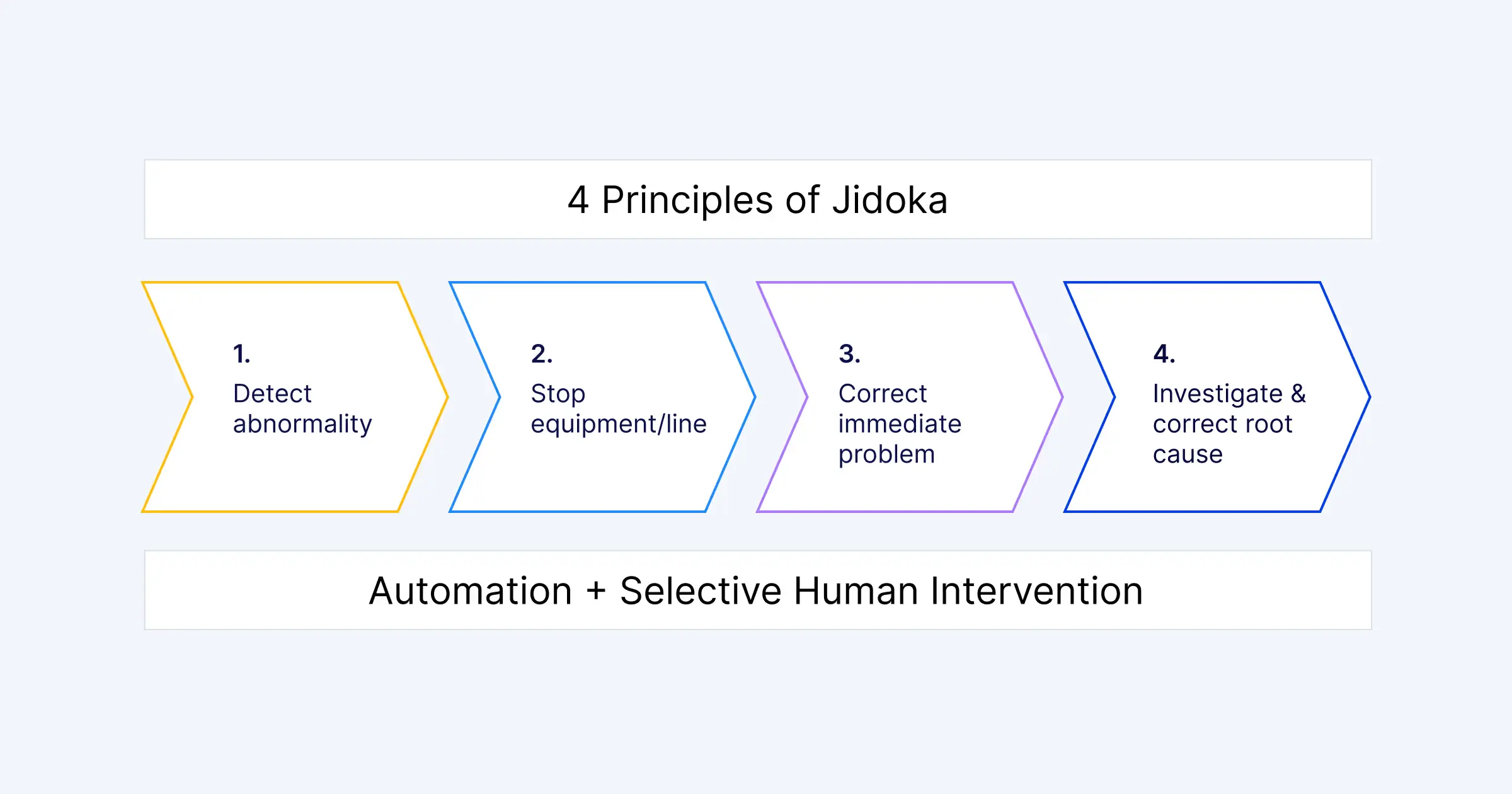
Download our free guide to learn the five most common root cause analysis tools.
Jidoka Tools and Techniques
Several specific methodologies support Jidoka implementation:
- Poka yoke: Poka yoke is a technique used to prevent mistakes from happening in the first place. Think of a USB plug that only fits into the port in one direction. This design prevents a user from plugging it in the wrong way, which would cause damage or errors.
- Visual management: This technique uses visual signals to communicate important information (including abnormal conditions) enabling rapid problem identification and resolution. Imagine traffic lights. The colors red, yellow, and green give drivers clear instructions on what to do without needing to read any signs. In a workplace, this could be color-coded bins for different types of waste or image labels on shelves to show where items belong.
- Standardized work procedures: Standard operating procedures (SOPs) create a consistent way of doing tasks to ensure everyone follows the same steps. For example, the recipe for baking a cake provides specific instructions on the ingredients and steps to follow, so anyone can make the cake the same way every time. On the plant floor, this could be a checklist for assembling a product to ensure it’s done correctly each time, reducing the potential for quality issues.
Benefits of Jidoka
Jidoka brings a number of advantages to manufacturing processes. By integrating human oversight into automated processes, it enhances efficiency and ensures high-quality output. The following benefits highlight how Jidoka can transform production environments, leading to significant improvements in various aspects of manufacturing.
Specifically:
- Significant waste reduction: Jidoka helps to cut down on waste considerably. When a baker catches mistakes in the dough-making process early on, it prevents batches of bad dough from being baked into bread that would need to be thrown away. By catching errors early, less material and fewer resources, such as fuel and human labor, are wasted.
- Enhanced customer satisfaction: Jidoka leads to happier customers because they receive higher-quality products. When a car manufacturer uses Jidoka to ensure every car part is perfect before assembly, customers get reliable cars with fewer defects, making drivers more satisfied with their purchase.
- Lower production costs: Jidoka helps to reduce the cost of making products. By preventing mistakes and reducing waste, a factory spends less on materials and (wasted) labor. This means it can produce goods more cheaply and efficiently.
- Improved manufacturing flexibility: Jidoka makes it easier for manufacturers to adapt to changes. If a toy company needs to switch from making dolls to making action figures, Jidoka ensures that the transition is smooth and quick, without compromising on quality.
- Continuous process improvement: Jidoka encourages ongoing improvements in the way things are made. For example, a smartphone manufacturer constantly looks for ways to make its production process better, faster, and more efficient, allowing them to keep up with new technologies and customer demand.
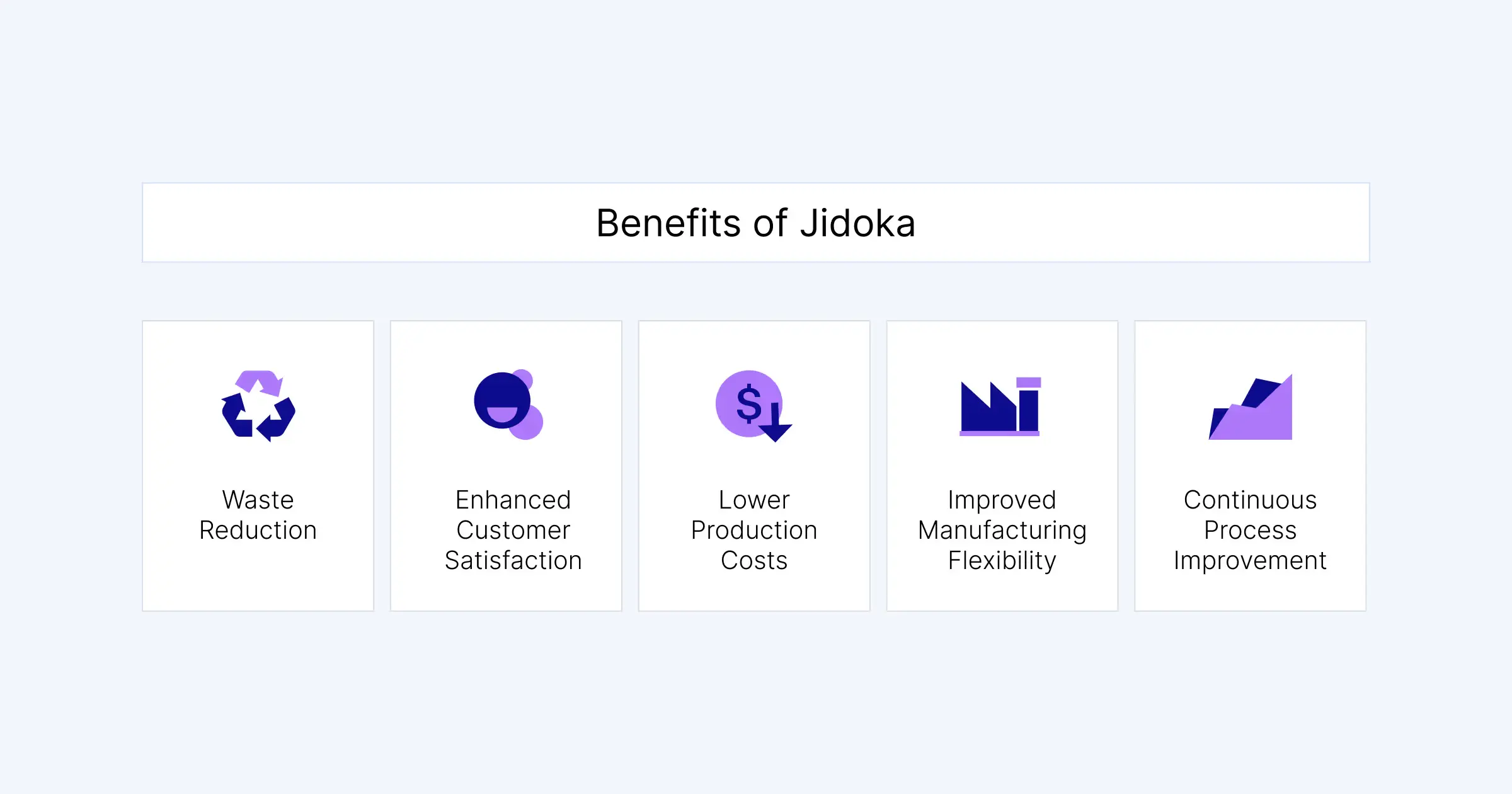
Jidoka Implementation in the Toyota Production System
Taiichi Ohno, a central figure in lean manufacturing, further developed Jidoka as a critical pillar of operational excellence, transforming Jidoka from a theoretical concept into a comprehensive manufacturing philosophy. While Sakichi Toyoda laid the foundation with his innovative automatic loom, Ohno’s work transformed Jidoka into a cornerstone of the Toyota Production System (TPS), emphasizing not only machine learning but also a cultural and organizational shift toward quality and continuous improvement.
Ohno’s implementation of Jidoka focused on three core areas: systematic problem detection, operator empowerment, and process standardization. These elements were designed to create a seamless integration of human oversight and machine automation, ensuring defects were not merely detected, but prevented.
Systematic Problem Detection
Ohno introduced structured methods to identify and address abnormalities in the production process. His key initiatives included:
- Visual management: Visual management tools like Andon boards and color-coded signals were implemented to provide real-time visibility into production status, enabling quick identification of issues.
- Workflow interruption protocols: Clear guidelines were established for stopping production when imperfections were detected, ensuring problems were addressed immediately.
- Root cause analysis: Standardized processes, such as the “5 Whys,” were developed to systematically investigate and resolve the underlying causes of defects.
Operator Empowerment
Ohno recognized that empowering workers was critical to the success of Jidoka. He implemented strategies to ensure operators were actively engaged in maintaining quality:
- Authority to stop production: Line operators were given the responsibility and authority to halt production if they identified a defect, fostering a sense of ownership and accountability.
- Quality-centric training: Comprehensive training programs were developed to instill a deep understanding of quality standards and problem-solving techniques.
- Feedback mechanisms: Systems were put in place to encourage operators to report issues and suggest improvements, creating a culture of collaboration and continuous learning.
Process Standardization
To ensure consistency and reproducibility, Ohno emphasized the importance of standardizing processes across the production system:
- Documented best practices: Manufacturing procedures were meticulously documented to create a reference point for quality control and training.
- Modular process design: Production processes were broken into modular components, allowing for easier adjustments and scalability.
- Reproducible quality control: Standardized checklists and inspection protocols were developed to maintain uniformity in quality across all stages of production.
Ohno’s implementation of Jidoka fundamentally reshaped Toyota’s approach to manufacturing. By embedding intelligence into both machines and processes, he created a system that both minimized defects and downtime while also fostering a culture of continuous improvement. This holistic approach enabled Toyota to achieve unprecedented levels of efficiency, quality, and customer satisfaction, solidifying its position as a global leader in automotive manufacturing.
A Principle of Excellence
Through Ohno’s vision, Jidoka evolved from a technical innovation into a strategic business principle, demonstrating how proactive quality management can drive operational excellence and long-term success.
Jidoka represents more than a manufacturing technique; it’s a philosophical approach to quality that places intelligence, prevention, and continuous improvement at the core of operational strategy. By integrating human touch with machine capabilities, Jidoka transforms production from a potentially error-prone process into a precision-driven system of operational excellence.
Perhaps most significantly, Jidoka’s principles extend beyond the plant floor, offering valuable lessons for organizations across industries. Its emphasis on defect prevention, root cause analysis, and operator empowerment fosters a culture of accountability and innovation.
In an era where efficiency and quality are paramount, Jidoka serves as a timeless reminder that excellence is not just about achieving results, but about building systems and team mindsets that sustain success over time.