Kamishibai Boards: What They Are and Why You Need a Better Solution
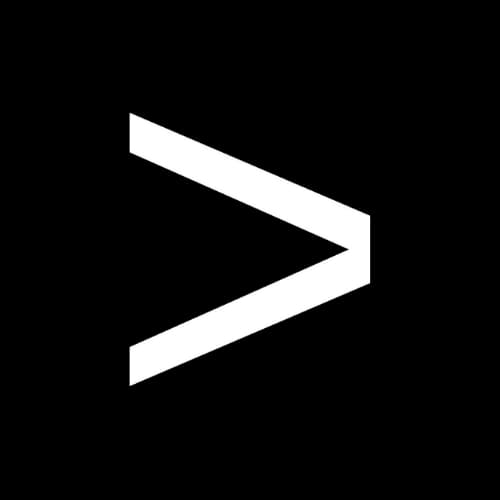

In 12th century Japan, Buddhist monks first created kamishibai or ‘paper drama’ as a visual storytelling technique used to dramatize moral tales for audiences that couldn’t read.
Centuries later, the Toyota Production System adopted the technique as a tool to track and standardize tasks on the plant floor. While this approach promises significant benefits, many plants have discovered that practical limitations often get in the way of effectiveness.
In this article, we discuss the basics of kamishibai boards and why manufacturers are moving away from them, covering topics that include:
- Why manufacturers use kamishibai boards
- Drawbacks and limitations to using this approach for plant floor audits
- Advantages of a digital layered process audit solution over kamishibai boards
- Implementation challenges and considerations for digital solutions
We also detail a real-life case study of how a leading automotive manufacturer replaced its kamishibai board with a digital layered process audit solution, and the potential ROI of adopting plant floor audit software.
Read a free case study to learn how Jacobs Vehicle Systems replaced its kamishibai board with EASE digital layered process audits
What Are Kamishibai Boards in Manufacturing?
A kamishibai board is a visual management tool used to track completion of tasks such as 5S checks and process audits on the plant floor. The kamishibai board consists of a series of color-coded cards representing individual tasks for verifying that operators are following standards. In many plants, kamishibai boards are used specifically for layered process audits, a high-frequency auditing strategy prevalent in automotive manufacturing.
How a Kamishibai Board Works
A kamishibai board is comprised of a series of double-sided cards called T-cards arranged on a board in a prominent location on the plant floor. Each card has one red side and one green side, providing instructions for auditing standard work.
The process of using a kamishibai board is relatively simple. The supervisor or team lead chooses a card from the board, follows the instructions for auditing the process and records the results before returning the card to the board.
When the red side of the card is visible, it means the audit hasn’t been completed yet. When the green side is facing out, this indicates that the check has been completed. Each T-card should detail the who, what, where, when, why and how (5W1H) of the process being audited.
Plants often arrange T-cards in a grid, with each row corresponding to a specific audit frequency (e.g., daily, weekly or monthly tasks). In this sense, the rows correspond to the different layers in a layered process audit system. A kamishibai board also typically includes a chart for recording audit findings and any countermeasures implemented as a result of identified noncompliances.
Why Manufacturers Use Kamishibai Boards
Kamishibai boards provide several benefits to manufacturers. These include:
- Fewer compliance issues: Ensuring that operators follow standardized work promotes conformance with quality and safety protocols, reducing compliance problems and resulting errors.
- Early detection of process variation: Consistently performing process audits allows plants to detect and correct process variation faster to prevent quality and safety problems.
- Easy visual verification: Red and green T-cards make it easy to see at a glance whether plant floor audits have been completed. The information on the cards also makes the checks themselves simpler, providing clear criteria for verification of key standards.
- Leadership involvement: This strategy helps supervisors develop a daily routine for conducting plant floor audits, forcing them to observe processes in person. This ensures leadership is a daily presence on the plant floor, promoting credibility and buy-in for quality management initiatives.
- Providing structure for Gemba walks: Gemba walks are a Lean tool for getting leadership out on the plant floor to see what’s actually happening where the work is done (or ‘Gemba’). Kamishibai boards can add structure to Gemba walks by providing guidance on specific standards and controls requiring verification.
Done right, kamishibai boards improve communication on the plant floor, ensuring that everyone knows what they should be doing. They also promote greater productivity in that less variation means more time spent making profitable parts means fewer resources needed to address defects and complaints.
Limitations of Kamishibai Boards
Despite the benefits, kamishibai board have clear limitations in terms of efficiency, timeliness of data and coverage of standards. These problems create added risk given the pace of change in manufacturing, where evolving customer requirements and risks demand an agile approach to plant floor audits.
Imagine you receive a customer complaint over an automotive part breaking down in the field, requiring operators to add an extra step to the process. Checking that they’re actually doing this requires manually creating a new card and updating the board, a cumbersome process that can cause delays, if it even gets completed at all.
Depending on the number of cards in your rotation—and the number of new issues that pop up—it can be hard to ensure frequent enough verification. It also can be difficult to make sure you don’t have gaps in your audit questions.
Another limitation is the lack of real-time data. Having to enter findings manually and analyze spreadsheet data limits visibility into process issues, creating lag time in identifying trends and root causes.
For some manufacturers, the result is a lot of time and effort invested in creating kamishibai boards that sit unused. Ultimately, this means process issues can slip by unnoticed, also hurting overall credibility of the organization’s quality mission.
Advantages of Digital Solutions Over Kamishibai Boards
Recognizing the inherent limitations of kamishibai boards, many manufacturers are turning to digital plant floor audit software to streamline plant floor checks and improve process visibility. For layered process audits in particular, going digital is critical to managing daily, even shift-level audits.
In this context, digital solutions provide several advantages such as:
- Real-time data collection and analysis
- Efficiency and scalability
- Broader coverage of standards
- Issue tracking and trending
Below we look at each of these in more detail.
Real-time Data Collection and Analysis
With layered process audit software, team members complete audits on a tablet or smartphone, after which findings are immediately compiled and available for viewing.
Instead of having to wait for someone to manually tabulate and analyze audit data, leaders can instantly see where process noncompliances occurred. Custom dashboards provide data in graphical format such as Pareto charts to identify the biggest sources of problems.
The ability to access data in real-time allows teams to find and fix problems faster, before they become larger downstream quality issues. It also makes it easier to share data across multiple work areas or even different plants, so leadership can proactively track and trend audit metrics and findings.
Efficiency and Scalability
A digital platform to manage layered process audits provides greater efficiency and scalability compared with manually creating and maintaining kamishibai boards.
A few examples:
- Leaders can create an annual audit schedule with just a few clicks, assigning audits to various layers according to their required audit frequency (e.g. daily, weekly, monthly)
- Team members automatically get reminders of scheduled audits, with instant visibility into who’s missing their audits to ensure accountability
- Audits can easily be scaled across different production lines and plants without having to build new boards and T-cards
Broader Coverage of Standards
Kamishibai boards can only cover as many standards as there are T-cards. Cards can be shuffled and redistributed, but how can companies know that their most important standards are being followed?
A digital plant floor audit solution solves this problem with a dynamic question library that allows manufacturers to:
- Add new questions in response to process changes or corrective actions to verify that people are following new procedures and not backsliding into old habits
- Rotate and randomize process audit checklist questions to ensure you don’t miss key areas aren’t missed
- Adjust the frequency of questions based on how frequently they fail, for example only asking a question with a 99% pass rate on an occasional basis
- Tag questions by process element (e.g., safety, standards, error-proofing, measurement, material, or operator) for more robust reporting and visibility into risk
Issue Tracking and Trending
With kamishibai boards, following up on audit findings is labor-intensive and time-consuming. In some cases, it may be limited to corrections on the plant floor rather than analyzing trends in failures, which can provide important context for root cause analysis. With a digital solution, plants can:
- Document on-the-spot mitigations and assign additional action items to specific individuals
- Keep leadership informed of process failures, with the ability to track trends and patterns over time
- Monitor metrics such as number open issues to prevent a growing backlog of unresolved problems
- Improve root cause analysis by with failure categorization and conditional questions
Implementation Challenges and Considerations for Digital Audit Solutions
Manufacturers considering deploying an automated solution must contend with several implementation challenges and concerns. Chief among them are user adoption, security and vendor support, as well as overall cost and ROI.
User Adoption
User adoption is especially vital considering the overwhelming number of companies who report having wasted money on ‘shelfware,’ or purchased software that’s never used. In this sense, an intuitive platform that simplifies auditing and reporting both improves buy-in and makes it possible to get more value from your investment.
Data Security
Cloud security is also an important consideration given the sensitive nature of manufacturing information and potential intellectual property implications. A few items to note here:
- Cloud-based applications can actually be more reliable than on-premise software, while also restricting access to your company’s data.
- Your vendor should have built-in security features like data encryption and multi-level security controls, as well as a GovCloud option for companies that must comply with FedRamp security requirements.
- Mobile device management (MDM) solutions provide several controls to limit risks of using devices on the plant floor, such as data and photo encryption and geo-fencing.
Overall Cost and ROI
In terms of cost, solutions priced per user may cost more compared with layered process audit solutions where pricing is based on overall plant size or number of employees. Per-user pricing can also be more difficult to manage considering that staffing levels often fluctuate in a plant.
For a simple look at the ROI of layered process audit software, plants need only consider the annual financial impact of quality escapes. One study of the EASE platform, for instance, showed a potential one-year ROI of 362%, delivering nearly $1 million in annual savings for a hypothetical company with $250 million in revenue.
In terms of choosing the right solution, look for a vendor that can provide several examples of how they’ve helped manufacturers measurably reduce costs and improve audit efficiency.
Moving from Kamishibai Boards to EASE: A Case Study
Jacobs Vehicle Systems, a global manufacturer of braking systems, initially started with a paper-based system for managing layered process audits. Shortly after, they moved to a kamishibai system consisting of T-cards chosen randomly from two decks.
The card chosen from the first deck would indicate the location of the audit. The card chosen from the second deck showed the process to be audited on the green side, with images of noncompliant processes on the red side. After the audit, team members would have to post results on a dry erase board before transferring them to spreadsheets.
Kamishibai Audit Challenges
According to Quality Systems Manager John Rose, there were several drawbacks to the kamishibai approach:
- Audit gaps: It was quickly evident that some work areas and questions were hardly ever audited, creating audit gaps that increased process risk.
- Difficulty updating questions: Updating questions required updating a spreadsheet, scanning photos, printing new cards and laminating them. This made it hard to maintain card decks and clarify questions that operators found confusing.
- Inefficient follow-up: The kamishibai system provided minimal visibility into findings, with difficulties following up on them and communicating with the team about quality issues.
As a result of these issues, the management team decided to seek a different approach. What they wanted was a system that allowed them to cover more questions in each audit, randomize audit scheduling and improve reporting for better visibility into problems.
Testing an Automated Layered Process Audit Solution
Quality Systems Manager John Rose recommended the team try EASE, a digital layered process audit platform he had experience with in a previous role. During the free trial, he says management was impressed with how simple it was to add and change questions compared with the kamishibai process. He also notes the cloud-based web app made it easy to see audit results in real-time.
After the free trial, the team decided to pilot EASE in its Bloomfield, Michigan plant. Rose notes that throughout the process, the implementation team took time to understand the company’s goals and guide them on how to get the most from EASE, calling the training and tech support “unsurpassed.”
Results of Switching from Kamishibai to EASE
Perhaps the biggest result from implementing an automated system for plant floor checks was a more than 40% increase in audit completion rate. Rose reports several other notable results, including:
- Improved accountability: Each week Rose is able to pull up audit results and Pareto charts of noncompliances, with EASE also helping him track open action items and bottlenecks.
- Broader coverage of audits: Even distribution of audit scheduling across different locations now helps minimize audit gaps and resulting process risks.
- Simplified checklist maintenance: EASE’s audit question library means the team can easily clarify confusing questions and add new ones in response to process changes or customer complaints.
- Third–party audit preparedness: Rose says the audit questions have helped his team better prepare for third-party audits.
As a result of this successful pilot, Jacobs deployed EASE in additional plants globally, also using the platform for 5S and safety audits. With EASE, the team can now monitor top-level metrics and spot trends within and across plants.
Making Your Audits Easier with EASE
Kamishibai boards provide a visual method for tracking and managing audit tasks on the plant floor. That said, it is a labor-intensive tool that can often fall into disuse as a result of its limitations.
A digital platform like EASE helps plants achieve the goals of kamishibai while significantly improving ease of use. Making audits simpler—and making it easier to view and act on results—means more checks get completed, generating more data and insights to drive continuous improvement.