Recognizing the Benefits and Pitfalls of Layered Process Audits
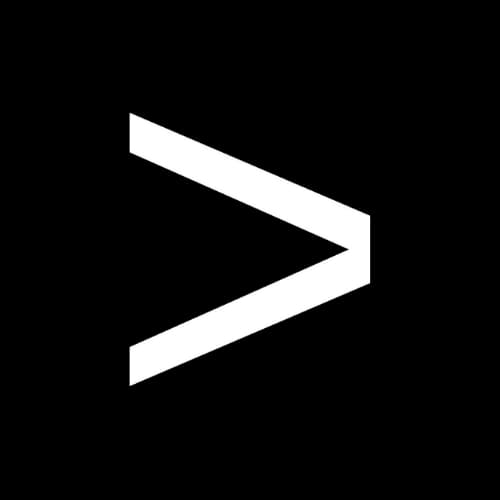
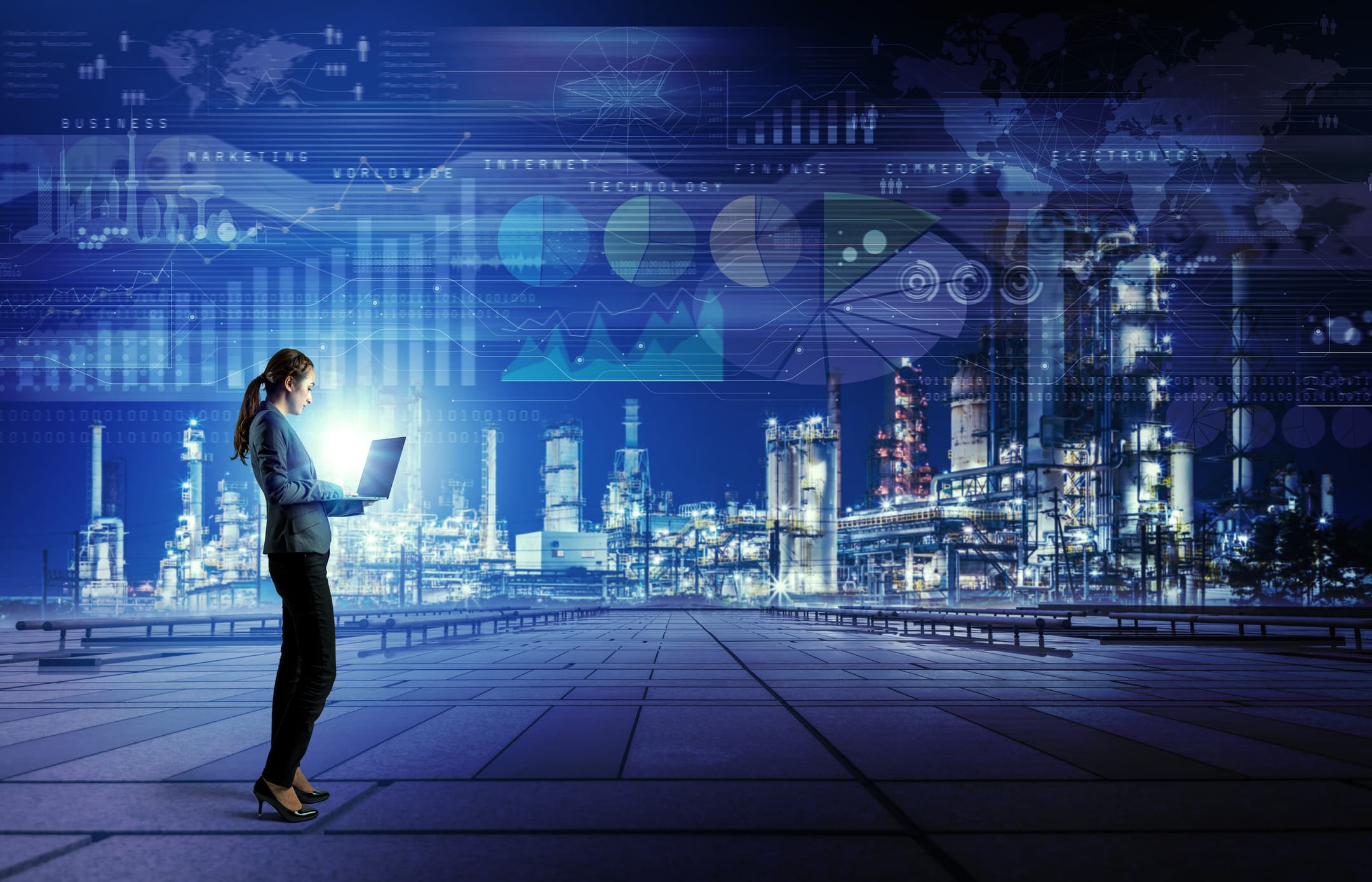
The Path to Better Performance and Profitability
What are layered process audits?
Layered process auditing (LPA) is a quality management approach increasingly used by manufacturing and service companies alike to address a gap in traditional product-oriented approaches. When properly implemented, layered auditing is the most effective way to ensure processes consistently follow approved standards, reducing waste and rework, improving quality, and driving cultural change throughout an organization.
LPA can put organizations on the path to increased profitability, but it’s critical to implement the right systems to keep track of these activities and their results to truly realize the benefits. LPA systems must address three essential elements:
1. Focus audits to address high-risk processes, and adapt to changes. Audits are essentially a series of questions to examine a process. In a LPA system, audits should focus on areas in the manufacturing process where variability, or process changes, represent a high-risk potential for producing defective products.
2. Use auditors from multiple areas of management to perform audits. In a LPA system, audits are performed periodically and at a predetermined frequency by multiple layers of management from across the organization.
Example: Let’s say the supervisor for each shift in a manufacturing plant performs an audit to examine a key process once every shift. With a good LPA system, another layer of managers from other areas of the organization would perform the same audit, along with similar audits, on a rotating basis. By assigning cross-organizational auditors to this layer, and developing a schedule that rotates through the system, the audits are completed by auditors from different areas to help mitigate against missed issues or pressure to “buddy pass.”
3. Adopt a system for reporting and follow-ups. For a LPA system to be optimized, it must capture analysis and corrective actions in real-time and help identify opportunities for improvement. With an effective system for recording and reporting information for an audit, a LPA system becomes the best-in-class tool for troubleshooting problem areas and identifying opportunities for improvement.
Example: If an auditor finds notable process deviations or non-conformances while performing an audit, that auditor should record his or her findings and take corrective actions to ensure that defective products do not get out of the door. Information regarding the findings should be noted and made readily available to management for subsequent analysis.
What are the benefits of layered process audits?
Organizations are implementing LPA systems to enhance their competitive position and as a safeguard from risk. Good LPA systems deliver these benefits in many ways:
- Decrease in PPM defects
- Decrease of internal rejections
- Decrease in scrap, rework, and warranty costs
- Increase in the number of improvement ideas received during audits
A good LPA system automates administrative processes, delivers real-time results, enables management to focus on reviewing errors, identifying problems, and addressing root causes. If your facility would like to improve any of these metrics, while also improving internal communication between management and manufacturing, a LPA system is central to the solution.
What are common pitfalls to avoid when implementing layered process audits?
Implementing a LPA system without taking into account certain the data volume and the potential overhead may result in a labor-intensive, minimally effective program that adds cost complexity; negating most of the value. Some of the most common mistakes in implementing layered process auditing are:
- Implementing a layered process auditing (LPA) system for the wrong reasons. Adopting a LPA system only to meet customer requirements, or only to add LPA to your Quality Management System to meet TS requirements, are both less-than-ideal reasons to pursue the integration. It’s important to understand that it is fundamentally more proactive, and more process-focused, than traditional solutions.
- Failing to recognize the importance of leadership and accountability. Leaving all the changes and implementation to the Quality department, or delegating implementation to people with very little process knowledge, are signs that there is a lack of ownership. It’s critical that leaders from every area support the implementation.
- Designing a system that is high-maintenance and provides low-value information. It’s important to understand the value and time-sensitivity of audit information when implementing LPA software. It’s equally important to understand who the real customers are when designing the process. The system and its user-interface should be easy to use, and easily adaptable.
- Overlooking the company culture reactions during implementation. Organizational culture plays an important role in the effectiveness of transitioning to a LPA system, so you’ll want to make sure everyone is aligned with the transition. Common mistakes include placing blame and passing judgement rather than making adjustments, and failing to react to issues quickly. Providing an intuitive, easy-to-use tool to assist users goes a long way to overcome these potential traps.
How can Ease help?
EASE’s powerful yet easy-to-use LPA platform helps manufacturers and service providers slash administrative overhead and provides immediate insight to help your organization improve quality and process performance. The system improves audit integrity, identifies problems early, and supports visual standards to easily communicate “good” from “not good enough.” Our audit management platform also provides real-time insights and automatic corrective action follow-ups, alerting your organization with quick and accurate results.