Layered Process Audit Metrics: 4 Enterprise-Level Numbers to Track
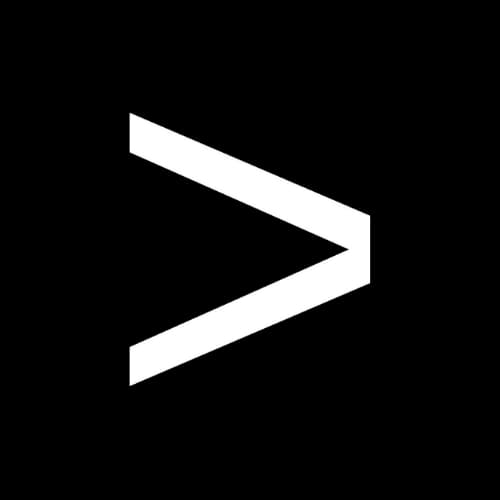
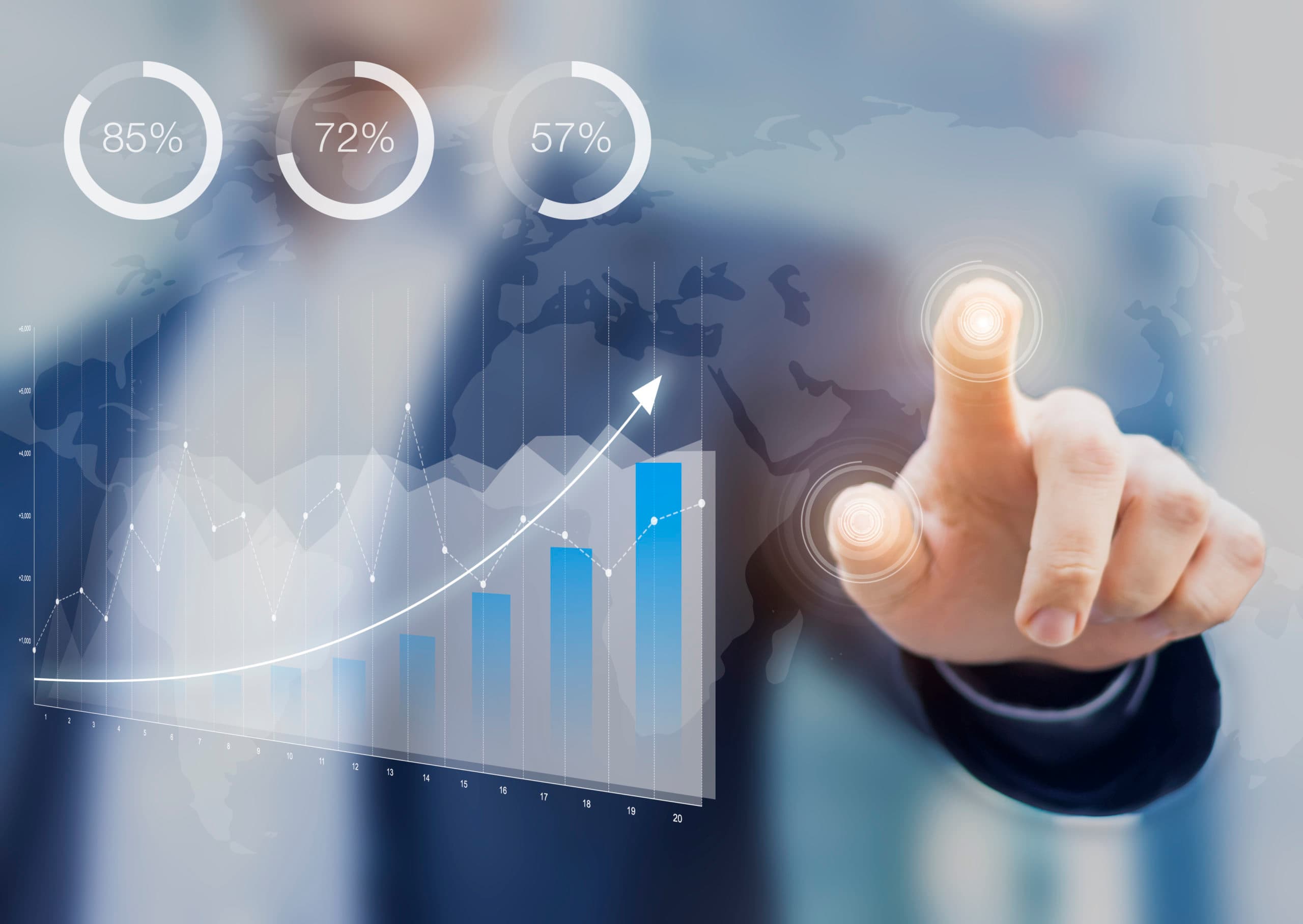
According to a recent LNS Research survey, 37% of quality leaders cite an inability to measure quality metrics as their number one barrier to achieving quality goals. Even worse, the survey showed a full 4 in 5 companies have poor visibility into real-time metrics.
These figures highlight a central problem in quality management: in an era of increasingly large data sets, how can manufacturers leverage this data for meaningful improvement?
It’s a question that’s especially relevant for manufacturers engaged in layered process audits (LPAs), a high-frequency verification strategy where teams conduct short audits every shift. With hundreds or even thousands of audits taking place over the course of a year, making sense of a large volume of data is a core challenge of LPA programs.
While plant managers often track metrics at a granular level, director and VP-level leaders need to look at the data a little differently at a higher level. Let’s look at four of the most important enterprise-level layered process audit metrics to track.
Learn about the basics of layered process audits with our free eBook, LPAs 101
1. Audit Completion and Pass Rates
Like site-level leaders, management should keep a close eye on audit completion rate and audit pass rates. On an enterprise level, you’ll want to analyze this metric by location to see where audits are happening, which plants are most successful and which ones need extra help.
This information can give you better visibility into problems and strategic actions needed to improve LPAs, such as identifying plants that are pencil-whipping or rushing through audits. For example, if a plant with lots of defects and complaints also has a high audit pass rates, it’s a good sign that leadership will need to investigate.
On the other hand, you might have certain plant or plants performing well on audit completion and pass rates while also achieving minimal defects. This case represents a potential opportunity to extract best practices from those high performers and apply them across the organization.
But won’t people avoid noting nonconformances to make their audit pass rates look better than they actually are? It’s a definite possibility. To counter this tendency, consider tracking this metric on a high level without publishing it down the pipeline or making it part of a plant’s official targets.
2. Nonconformances by Category
Slicing and dicing nonconformance data in different ways is a quick way to identify your biggest trouble areas on an organizational level. Many companies will track audit nonconformances according to categories such as:
- Process area
- Types of LPA questions failed
- Nonconformance type, e.g. tool calibration, process, documentation or scrap
- Most common corrective actions
- Quality versus health and safety findings
Viewing this data in Pareto chart format can help you pinpoint where your efforts will have the biggest impact in the organization. Let’s say you have an ambitious goal of reducing failures 25%. Using the second y-axis that correlates to cumulative percent, you can easily pick out a few categories to focus on that will get you to your goal.
3. Nonconformance Rate
Nonconformance rate is another popular LPA metric that manufacturers are tracking at an enterprise level. In other words, of the number of audits completed, how many actually lead to nonconformances or corrective actions and why?
This metric is important because it gives leaders a sense of how effectively plants are using LPA data. A plant with an abnormally high nonconformance rate is indicative of a more systemic issue on the plant floor that requires addressing at a deeper level.
4. Predictive Analytics
Many organizations are interested in using predictive analytics to improve quality performance. One way they can do that is to look at how metrics like audit completion rate, audit pass rate and nonconformance rate change over time. Applying time-series analysis to this data, companies can identify trends and potentially even predict what that rate will look like three months into the future.
This analysis is particularly powerful when applied to leading metrics that correlate with other key quality outcomes. For instance, if an uptick in audit nonconformance findings usually precedes customer complaints, you can step in before that happens if you notice nonconformances increasing in any given plant.

Taking it a step further, manufacturers could then use this information to develop poka-yoke tools targeted to specific high-risk processes or steps. At the end of the day, this kind of concrete action is what tracking LPA metrics is all about, using completion rates, pass rates and nonconformance data to drive targeted quality improvements.