Managing Shifting Audit Schedules Due to COVID-19
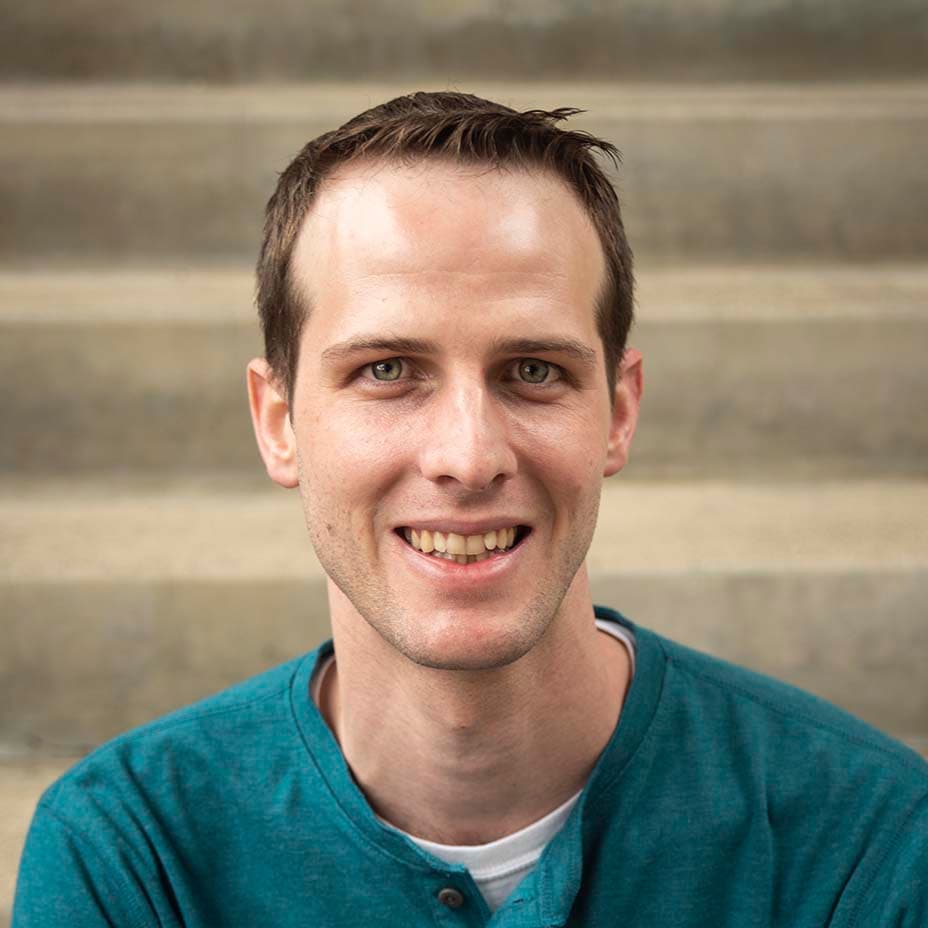
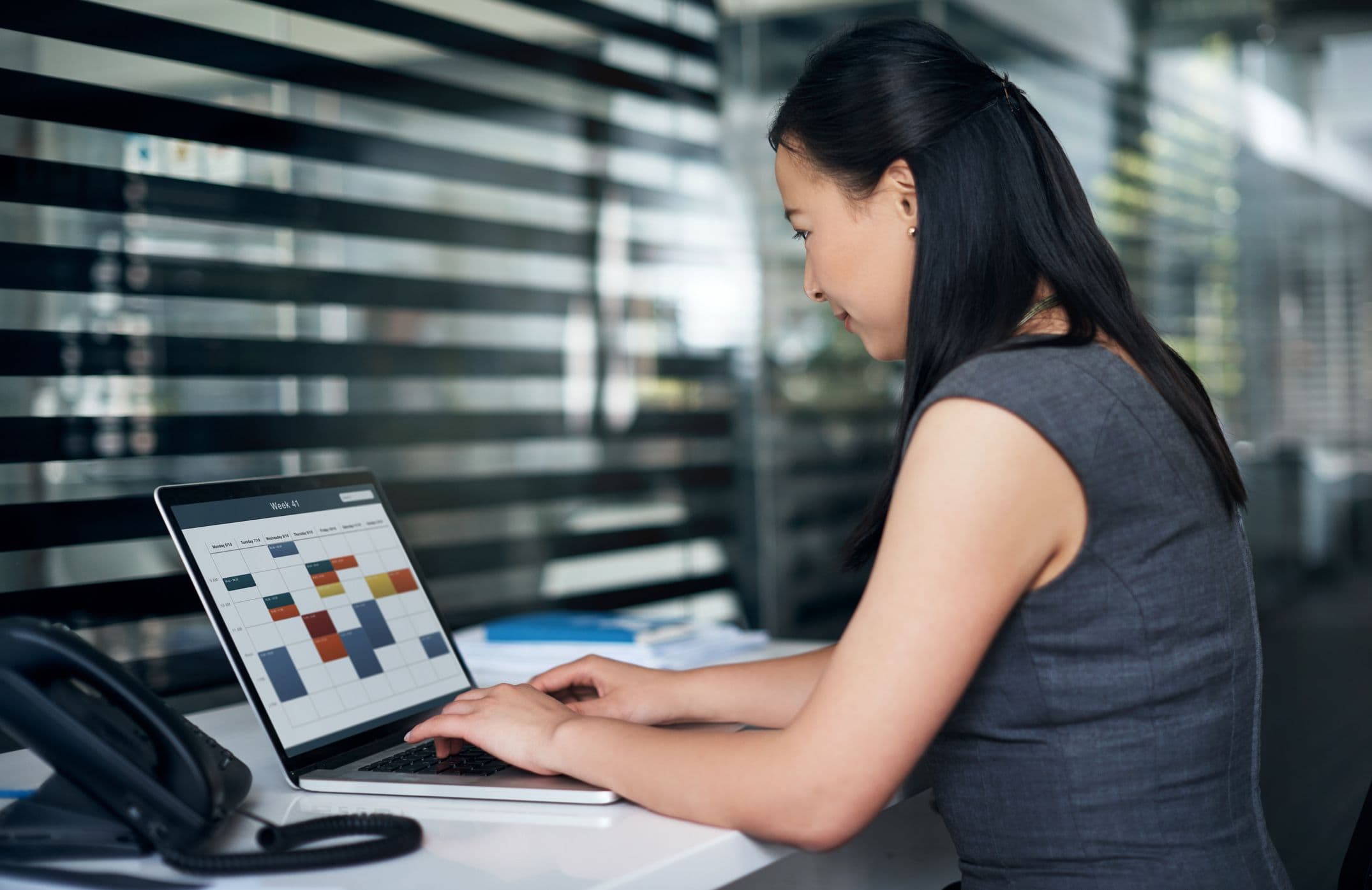
These are uncharted territories for most of us, although in the manufacturing industry, plant shutdowns are not completely uncommon.
If you’re in the automotive industry, when it comes to developing a layered process audit schedule that complies with CQI-8 as well as any customer-specific requirements, it can take a lot of fine-tuning and is constantly subject to changes due to operation schedules and staffing.
With the recent developments of COVID-19 and many governments opting for social distancing or stay-at-home directives, we understand that your finely tuned LPA schedule may need some out of the ordinary adjustments to reflect changes in auditing capacity. With that in mind, we’ve put together a few tips on making schedule changes in the EASE (Beacon Quality) auditing platform.
Remember that our customer success and support teams are here for you if you need anything. Just send us a message through our support portal
Delete Requests
If you have individual people missing work, we recommend trying our new delete requests feature. Admins can enable it in the site settings page, then auditors can submit a request to have a missed or upcoming audit removed from their schedule. This option helps by eliminating audits that would end up marked missed or incomplete if the scheduled employee must stay home.
Remove Audits via Location Calendars
If you have any equipment going offline or an entire site being shut down for a period of time, you can use our location calendars to remove audits for those dates. This is the best way to remove all audits for a given date range.
Remove All Audits
If you are shutting down and do not know when operations will resume, we recommend removing all audits from your schedule. You can do this from the assign page by clicking on one of your audits and deleting all related audits. This works best if you create your schedule all at once.
Additional Audit Questions to Incorporate
If you are staying open, you could incorporate new COVID-19 safety questions into your existing LPAs, 5S audits, or health and safety inspections. Examples include:
- Are employees maintaining a social distance of 6 feet?
- Are frequently touched surfaces being disinfected regularly?
- Are sinks stocked with soap and signs posted to wash hands for 20 seconds?
- Is hand sanitizer available where washing hands is not feasible?