Manufacturing Brain Drain: What It Means and How to Mitigate It
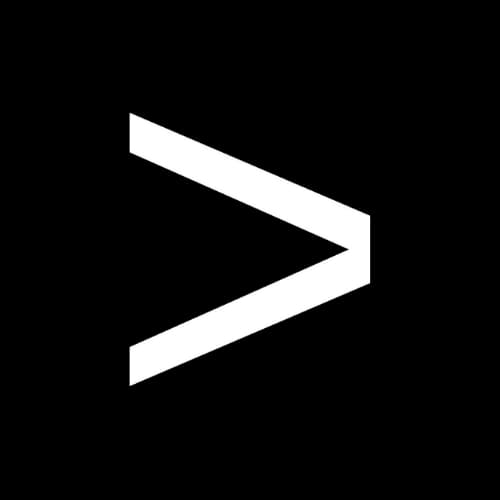
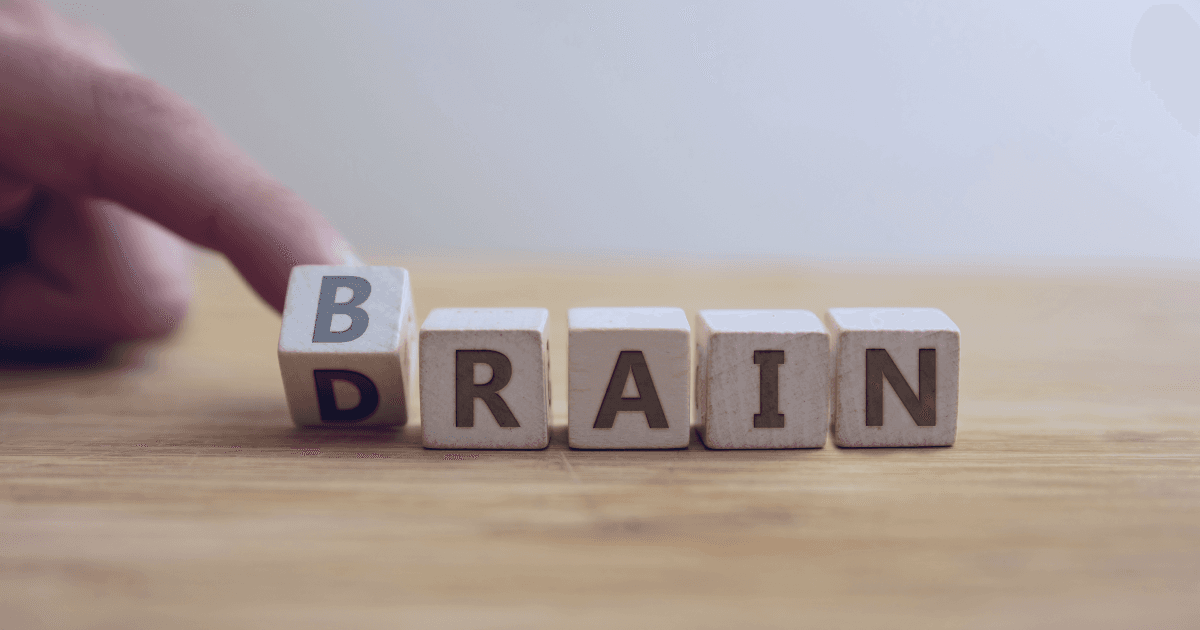
Brain drain and the loss of institutional and technical knowledge are critical issues plaguing the manufacturing industry. In fact, a report by the Manufacturing Institute reveals that 97% of organizations are concerned about brain drain, with nearly half considering it a grave threat to their operations.
Part of the problem is increasing numbers of baby boomers entering retirement, taking with them deep expertise that can’t be quickly replaced.
So what does this mean for manufacturers, and how can they mitigate the looming loss of institutional knowledge?
Below, we explore the critical impacts of the manufacturing brain drain on your organization, plus strategies for capturing institutional knowledge and reducing turnover.
Learn about 5 Big Problems with Traditional Employee Training
Hidden Impacts of the Manufacturing Brain Drain
When experienced employees leave, they take valuable institutional knowledge that may not be documented or easily transferred to new hires. This can lead to a loss of efficiency and productivity, as well as other impacts on:
- Employees: When experienced engineers leave, a loss of mentorship can limit the growth and development of younger employees. This isn’t limited to technical skills, but also how new hires learn to navigate the company culture. High turnover rates and the loss of valued colleagues can negatively impact the morale of the remaining employees, leading to decreased job satisfaction and engagement, and ultimately even higher turnover.
- Innovation: When a company is dealing with brain drain and struggling to maintain its workforce, it may have less capacity for innovation and long-term strategic planning. This can put the company at a competitive disadvantage.
- Customers: The loss of key personnel can delay projects and make it difficult to meet deadlines, potentially damaging the company’s reputation and relationships with clients.
Stemming the Impact of Institutional Knowledge Loss
Replacing employees is costly, with the Society for Human Resource Management estimating that replacing an employee costs six to nine months of their salary.
One big issue is that traditional training methods can’t effectively replace the deep understanding and practical skills that come with years of on-the-job experience. Without proper knowledge codification tools, such as knowledge bases, standard operating procedures (SOPs), or well-structured training courses, this knowledge remains locked in the minds of individual workers.
To address the problem, manufacturers must also develop strategies to shorten the learning curve for employees, so they can acquire the knowledge and skills required for their jobs faster.
This is where modern training solutions, such as digital shop floor microlessons within your connected worker strategy , come into play. By leveraging the power of targeted, easily digestible content, manufacturers can accelerate the learning process and help their workforce better adapt to changes in processes or operations.
These microlessons can effectively address issues such as:
- Quality, productivity and safety: Microlessons can be used to quickly communicate best practices, proper techniques and safety procedures. This helps to reduce errors, improve quality and increase productivity.
- Capturing and sharing knowledge: Documenting experts’ skills and insights in a digital library of knowledge helps bridge the gap between seasoned employees and new hires.
- Reinforcing classroom training: Focused lessons serve as refreshers, allowing employees to revisit key concepts at their own pace, to support continuous learning and knowledge retention.
Employee Turnover and the Manufacturing Brain Drain
Seasoned professionals retiring or leaving the company for better offers are just some of the issues contributing to the manufacturing brain drain. It can also manifest in other ways, such as high turnover rates among new hires.
For example, manufacturers may struggle with operators leaving before the 90-day mark because they feel they aren’t good at their jobs and keep making mistakes. What they take away is that the job — or even the manufacturing industry — isn’t for them, when the real issue is they haven’t been enabled to feel competent.
Companies can retain valuable talent and better support these employees by creating an environment where they can succeed from day one through proper onboarding, training and support.
Again, a connected worker strategy that leverages digital tools and devices can provide operators with critical information via short, visual one-point lessons available right at their workstations. This provides on-the-spot access to reference easily when executing a task, troubleshooting a process, or performing maintenance. Employees can efficiently address challenges and maintain productivity without disrupting their workflow or relying on external support.
The manufacturing brain drain is a serious challenge, but it’s not insurmountable. However, manufacturers must tackle the issue before it interferes with their ability to produce. By adopting modern training tools and focusing on knowledge sharing, companies can bridge the gap left by departing employees.