Manufacturing Communications: How You Can Improve Them in Your Workforce
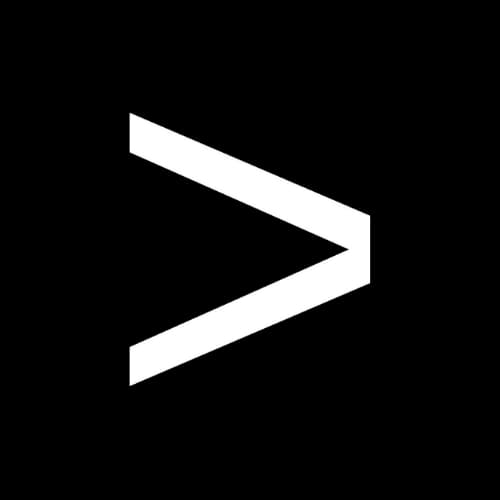
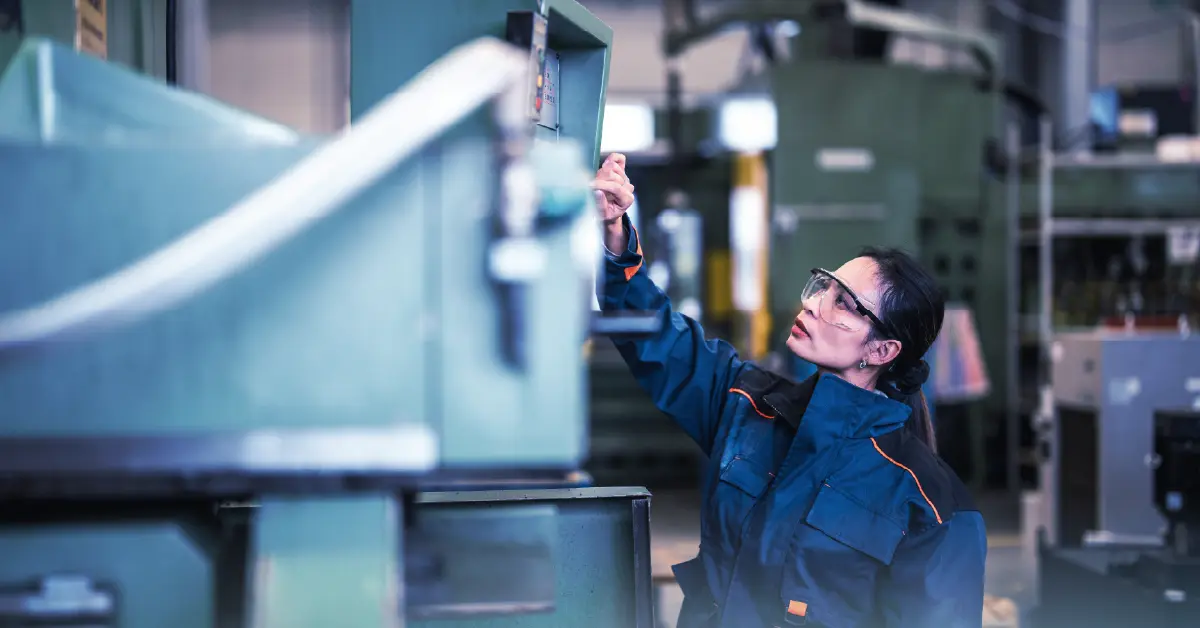
Before the arrival of Industry 4.0, internal manufacturing communications were notoriously inefficient and error-prone.
Important emails would get buried in inboxes. Policies and procedures sat gathering dust in binders or hidden in shared server drives. Paper forms and checklists meant painstakingly slow problem-solving, review, and approval, with corrective actions often needing months to complete.
On the plant or factory floor, each operator was essentially an island, disconnected from the team and the information needed to do their jobs well.
Today, digital transformation is changing all of that, streamlining communications plant-wide to help solve problems faster, keep production running smoothly, and engage operators as vital team members.
To see how, this article looks at:
- Why manufacturing communications are so important
- Common communication challenges
- Technologies and best practices for better communications in manufacturing
Download a free white paper to learn Why and How Digital Safety Inspections Help Manufacturing Companies Work Safer
The Importance of Manufacturing Communications
Plants are becoming increasingly aware of the importance of streamlining communication with technology to reduce risk and increase efficiency. Digital workflows for root cause analysis and maintenance alone, according to McKinsey, can add $180 million to the bottom line for a $1 billion company.
Using technology to improve communications can, for instance, mean pushing out quality alerts faster, reducing risk by raising awareness of quality issues. Connected worker platforms are also an integral enabler of real-time, two-way communication, accelerating problem solving with tools like instant messaging, automated issue management, and remote support.
There’s another huge reason improving communication has become such a high priority, however, and that is because of its impact on employee engagement.
Why Employee Engagement Is Essential
There is a growing recognition in the manufacturing workforce that reducing turnover is paramount to addressing widespread worker shortages. While people might think increasing pay is the best way to improve employee retention, research says engagement is what’s really essential to attracting and retaining employees.
Gallup’s 2022 State of the Global Workplace survey reports a strong correlation between engagement and retention, noting only 21% of employees globally are engaged at work.
Disengaged employees:
- Are resentful because their needs aren’t met
- Are more likely to quit
- Undermine quality, safety, and productivity
- Don’t put energy into their work—they just clock in to collect a paycheck
Engaged employees:
- Are involved and enthusiastic because their needs are being met
- Have opportunities to contribute as well as to grow
- Take ownership of problems so they get resolved faster
- Are more productive and focused, making fewer errors
- Are more likely to stay with a company
First and foremost, improving manufacturing communications is about integrating frontline employees and operators into the company community. This gives them a way to communicate their needs and feel that what they say matters, helping reduce turnover and ultimately mitigate the effects of the manufacturing skills shortage.
Challenges in Internal Manufacturing Communications
Companies face a variety of challenges when it comes to manufacturing communications. Below we discuss some of the biggest difficulties they’re up against, including worker isolation, outdated communication methods, and limited visibility into processes.
Isolated and Disconnected Manufacturing Employees
Operators have traditionally been isolated on the plant floor. If you’re a frontline worker, you may be doing the same thing 60 times per hour with nobody there but yourself. In this situation, it’s hard for people to feel like they matter to the organization.
Not being able to connect with employees or communicate with others is a persistent challenge for manufacturing operations as it often means operators’ needs aren’t being met, also causing quality and safety problems. For example, if an operator runs out of components or if a machine isn’t working properly, they’re more likely to keep going since they can’t leave their station for assistance.
Outdated Communication Methods
Many manufacturing environments rely on outdated methods to communicate with employees that are both inefficient and ineffective. These include:
- Posted paper: The problem with posting information on paper or a bulletin board is that it may sit there far longer than intended, degrading and becoming out-of-date over time.
- Binders: Keeping binders of work instructions, policies, and troubleshooting guides is useless because people typically don’t know where they are or how to find information within them.
- Kiosks: People can’t easily reference digital information stored on a central kiosk, nor is it located in a place where they see it regularly.
- Display screens: Here operators can see information but can’t interact with it. For instance, they can’t notify others on a line that a part needs rework if a situation arises where there’s a problem with assembly.
These outdated tools are especially problematic in a mobile-first world, where smartphones are increasingly central to production floor communication.
Limited Visibility Into Manufacturing Processes
To do their best work, frontline workers need real-time information relevant to the processes they work on and how to improve them. This includes information such as:
- How the line is running that day
- What expectations are, such as whether they need to be producing 48 vs. 72 parts per hour
- Any defects that have been found related to their station
For instance, let’s say a plant is building up a wire harness involving multiple wires, circuits, and connectors, and that only 12 of 15 circuits passed end of line testing. Traditionally plants might simply have posted those results, but how does the operator know if they made the three bad parts?
Process data can provide insights into which circuit from which workstation was the problem, and therefore which operator needs feedback to prevent it in the future. Integrating communications with process data is one-way digital transformation is helping bridge this gap and improve access to information for frontline workers.
How Technology Is Changing Internal Communications in the Manufacturing Industry
Industry 4.0 has created a sea change in how information is collected, communicated, and used throughout the manufacturing process. Industrial Internet of things (IIoT), connected worker platforms, and mobile audit and inspection software in particular have become indispensable tools for improving connectivity, efficiency, and consistent communication in manufacturing.
IIoT Technology
IIoT sensors and smart devices provide a seamless flow of real-time production data for monitoring and gaining insight into machine performance, inventory, and quality control. Rapid information change allows for:
- Seamless communication strategies among production lines to minimize bottlenecks
- Faster decision-making, more proactive maintenance, and accelerated resolution of issues
- Reduced downtime and increased productivity
Connected Manufacturing Worker Platforms
Connected worker platforms encompass a variety of tools providing workers actionable insights and the ability to share real-time information about plant floor conditions. These tools include:
- Instant access to digital work instructions, troubleshooting guides, and remote support to minimize downtime and prevent defects
- Workstation alerts, such as when to shut a machine down to prevent quality or safety issues
- Instant messaging to send requests or notify management of potential problems
- Mobile incident logging and automated issue management to speed up corrective action
Mobile Quality and Safety Inspection Software
Digital quality and safety inspection software is another way technology is changing communication on the manufacturing floor. By moving away from paper-based plant floor checks, manufacturers are able to streamline communication by allowing them to:
- Target audit and inspection questions to individual work areas, providing frontline workers with relevant feedback on the most crucial elements of their processes
- Identify and report on process non-conformances as they happen to spot trends and emerging risks
- Assign action items and steps to contain, correct, and follow-up on issues found on the plant floor
- Log ad-hoc observations on the fly, or as part of safety walkthroughs or Gemba walks
How to Create Effective Communications in Manufacturing Companies
As plants consider efforts to improve communications in manufacturing, keep the following best practices in mind, which we discuss in detail below:
- Setting clear objectives
- Using real-time, two-way communication
- Considering the employee’s perspective
- Remembering the golden zone
- Using push notifications sparingly
- Following through on employee feedback
- Prioritizing health and safety communications
- Implementing 5P’s of Good Manufacturing Practice
Deciding on Your Objectives
At the beginning of any continuous improvement effort, setting clear objectives helps determine the most strategic path forward while providing a yardstick for gauging success.
What are some common objectives manufacturers might have for improving communications?
- Providing immediate feedback on quality: Providing faster feedback on quality, such as in the example above with the wire harness circuits, helps prevent defects and the need for reworking parts.
- Communicating the ‘why’: Manufacturers often assume people will simply do what you ask them, when in reality they do what they think is best. Whether it’s conducting an FMEA or layered process audits, using PPE or doing a procedure a certain way, giving concise context on why it matters promotes process adherence.
- Emphasizing recent changes: If you change one step in a process, work instructions should highlight the new step, ideally with bold text and a photo of the change. If you’re using digital work instructions, you could also require the operator to check off the new step to help train them to the new process.
Using Real-Time, Two-Way Employee Communication
Lag time in communication is a source of inefficiency in manufacturing plants, making it hard to solve problems quickly and creating the conditions for quality and safety failures.
Live communication tools like instant messaging can help, for example if an operator runs out of push pins for an assembly and needs a new box delivered. However, there must be clear rules around communication to prevent people from getting overwhelmed. And when people are overwhelmed with notifications, that’s when they ignore them.
To prevent this problem, you need to decide who communicates with whom, in what sequence, and who ultimately makes decisions. For instance, you may have operators communicate with supervisors, rather than messaging maintenance directly. A standard operating procedure (SOP) that outlines these rules is essential. Tools like instant messaging and Slack are useful, but nobody will know what applies to them if you just have one team for the whole plant floor.
Consider Workforce Challenges
When looking to improve manufacturing communications, taking into account the employee perspective goes a long way towards creating buy-in and ensuring visibility.
First, as you look to harness insights from frontline workers, how do you help them feel supported rather than spied on? How do you make them feel safe to communicate rather than hide information?
The operator has to know that if they communicate that the box of push pins is empty, they aren’t going to get their friend who drives the forklift in trouble. What you want to emphasize is there’s no blame, no shame, and no finger-pointing.
Just as important, management needs to be accountable for following through on fixes. After all, what would be the point of communicating problems if your team isn’t confident you will fix them? Not closing the loop creates a huge credibility gap that can undermine success.
Remembering the Golden Zone
When bringing new communication devices to the plant floor, keeping them in the golden zone helps ensure you aren’t creating inefficiency in your processes.
The golden zone applies to the workstation setup, defined as 45 degrees left and right of the worker’s position and 30 to 60 inches high. If operators have to move out of this zone, they are wasting time and effort.
For example, one electric vehicle battery plant had a touchscreen for operators to swipe through digital work instructions mounted at the top of the work cell. The operator had to look up to see it, taking their eyes off the work piece and reaching up to swipe. Moving the screen down so they had to reach out rather than up kept the operator in the golden zone, streamlining the process and reducing opportunities for errors.
Keeping devices such as display screens, tablets, and connected worker terminals in the operator’s line of sight improves the chance they will actually use them. What’s more, they can do so without slowing down the process.
Using Push Notifications
Using manufacturing software to send push notifications to plant floor devices can be useful for communicating things like quality alerts, production schedule changes, and more. However, it’s absolutely critical that these messages are relevant to the person receiving them, such as safety protocols or urgent maintenance updates and onboarding notifications for new employees.
Remember, operators don’t want to see quality notices for someone else’s cell, nor does a worker on line three need to see production changes applicable to line two. If you’re sending irrelevant push notifications to the plant floor (such as high-fives for employee recognition), this is poor communication and people will very quickly start ignoring your messages. These general notifications could be reserved for a newsletter or calendar update.
Engaging with Employee Feedback
Improving manufacturing communications isn’t just about getting more information to the plant floor. It’s also about engaging with operator feedback, using it to improve productivity, efficiency, and quality.
Here are some examples:
- When an operator is running low on components, they can alert someone through the connected worker terminal that they need more delivered to their work station.
- If a tool is beginning to show wear, the operator can send an alert that the drill bit is getting dull so someone can come change it.
- If an operator is using a specific tank-fed gas, they can send a message when the tank is one-quarter full so someone can come replace the tank.
- Most importantly, if an operator says something is unsafe, you can provide immediate guidance on whether to shut down the machine or take other steps.
Management should also engage with operator feedback as part of their continuous improvement efforts, such as during Gemba walks, Kaizen events, plant floor checks, and more. Creating a culture of openness, communication, and follow-through will help people feel comfortable sharing their concerns and ideas.
Prioritize Health and Safety Communications
Communicating about health and safety practices should be priority number one when working to improve manufacturing communications. This helps leverage learnings from previous issues and prevent recurrence throughout the plant.
In this context, plants can communicate effectively about hazards and best practices that come from:
- Near-misses and good catches
- Corrective actions
- Incidents and safety violations
- Internal and external inspection findings
Again, it’s crucial to remember the context, keeping messages specific, relevant, and targeted. Rather than flood workers’ feeds with notices, you might publish one alert at the beginning of the shift, on why they need to wear side shields on safety glasses.
Insights that Make Manufacturing Efficient
Optimizing manufacturing communications can deliver valuable insights for improving operational efficiency and reducing downtime, defects, and scrap.
To this end, plants should consider:
- Using process data to provide specific guidance for operators, for instance if a machine needs to be shut down or parts need to be moved offline for testing
- How to use operator feedback to better meet the needs of plant floor workers as problems arise with components, tools, machines, and more
- Soliciting open-ended feedback, whether as part of plant floor checks or with connected worker technology. For instance, you might ask the operator, “Is there anything that could be done to make our work cell more efficient today?”
If you take this approach, consider adding the question at the shift start or after break, rather than the end of the shift when operators just want to go home.
As discussed here, the key is making sure you do something with that feedback. If you don’t, people won’t be willing to share their thoughts, nor will they believe in management’s stated commitment to quality.
Enhancing communications in manufacturing provides many benefits to companies, making operations more efficient, more productive and more reliable. It also comes with its challenges, demanding a controlled approach to keep communications specific, relevant, and targeted to those who need to receive them.
Technology like IIoT, connected worker platforms, and quality software are helping make strides in meeting these challenges, giving industrial transformation leaders a competitive advantage in today’s fast-changing manufacturing business environment.