How to Reduce Manufacturing Rework
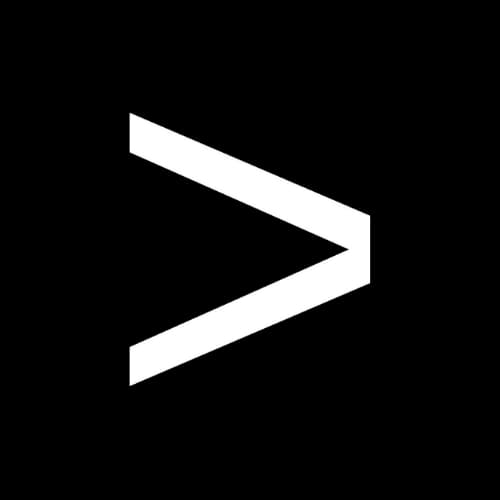
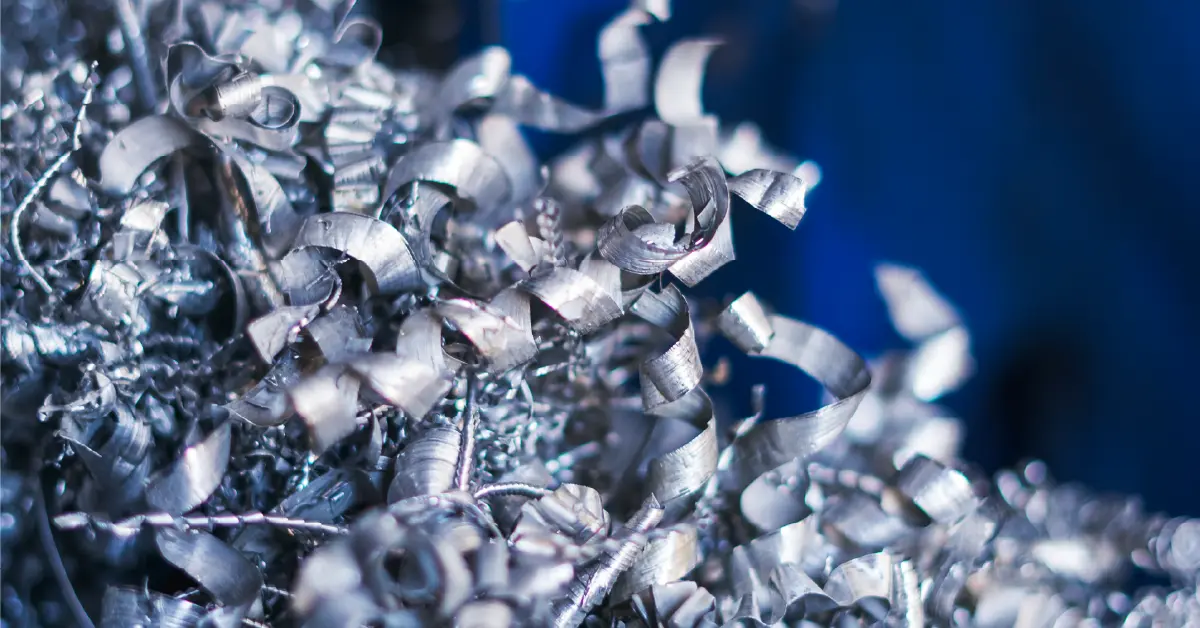
Scrap and rework costs manufacturers up to 2.2% of annual revenue, according to the American Productivity and Quality Center. For a company with $1 billion in revenue, that means $22 million in added costs.
For top performers, that number shrinks to 0.6%, or $6 million in the above hypothetical scenario, totalling $16 million in savings compared with bottom performers.
So how can companies reduce manufacturing rework and eliminate unnecessary costs while creating a reputation for quality?
Below we explore common factors that drive up scrap and rework, plus strategies for ensuring products are made right the first time.
Download your free Root Cause Analysis 101 Guidebook for an overview of the top 5 root cause analysis tools in manufacturing
What Is Manufacturing Rework?
Rework in manufacturing means correcting or repairing parts that are defective or don’t meet specifications. Rework increases quality costs and adds time to the manufacturing process, potentially delaying shipments. It also ties up labour and equipment that could be better used elsewhere, reducing productivity and capacity.
Reasons for Manufacturing Rework
A wide variety of hidden factory problems lead to rework, many of which are preventable with a proactive approach to quality. These factors broadly align with the 6Ms of process control and include:
- Operator error: Ensuring people follow standardized work every time is key to preventing defects, which also relates back to employee training.
- Machine problems: Equipment breakdowns or calibration issues are a major contributor to product defects.
- Environmental conditions: High humidity or temperature are two examples of environmental factors that can impact the manufacturing process or materials.
- Material inputs: Supplier quality problems, variation among suppliers or issues with material quality can all lead to product variation.
- Measurement inaccuracy: How operators take measurements and the accuracy of measuring equipment can introduce variation in parts.
Reducing rework requires a strong focus on defect prevention. To do that, manufacturers need to evaluate their upstream quality processes, which we examine next.
Documenting Your Processes
Developing standard operating procedures (SOPs) is the foundation of quality control, providing the crucial first step in the Plan-Do-Check-Act process. Standards like ISO 19001 and ISO 14001 require manufacturers to document their processes, making this step essential to compliance.
SOPs provide a defined standard for everyone to follow, setting the groundwork for subsequent activities such as employee training, plant floor audits and corrective action.
When documenting processes, it can help to start with a process map outlining what should happen in the work cell. This allows you to ask what could go wrong, so you can add steps to prevent it. Each step in the SOP should define:
- What the operator should do
- How they should do it
- Why it is important to quality
Developing and Updating FMEAs
Vital to preventing defects at the design stage is conducting failure mode and effects analysis (FMEA). This process defines all the ways failure can occur, rating each failure mode by severity, occurrence and detection. Multiplied together, these factors provide a calculation for the overall risk priority number (RPN), which can help prioritize which risks need additional controls.
FMEAs can focus on product design (DFMEA) or process design (PFMEA). Rather than just a one-and-done activity, FMEAs should be continuously refined throughout the process. For example, revisiting your FMEA after a customer complaint can help identify whether:
- There were any risks missed on the original FMEA
- New countermeasures or updates to the standard are needed
- Action is required elsewhere to prevent similar issues with other customers or product lines
Auditing Process Inputs
Frequent plant floor checks are paramount for verifying that operators are following standardized work. Process audits in particular help catch variation that causes defects and provide important clues when investigating potential sources of scrap and rework.
Layered process audits are gaining steam as a way to ensure frequent checks, with audits performed daily by different ‘layers’ of management. Layered process audit software can help manage the high volume of audits and provide real-time reporting on process issues while making it easy to complete audits quickly.
Keeping Workers Connected
Defects are a predictable outcome when operators can’t access what they need to do their jobs right. Connected worker software can help bridge this gap by providing:
- Guided procedure checklists based on operator expertise to ensure critical-to-quality process elements are highlighted
- Instant messaging capabilities so operators can notify the team of issues like component needs, equipment problems or defective parts
- Real-time guidance and troubleshooting for when workers have questions about a task or encounter a problem
- Implementing essential components of Good Manufacturing Practices (GMP)
Reducing scrap and rework is a hefty goal for companies struggling with defects and complaints. Getting there requires going back to the basics to ensure clear documentation, and then developing a system to verify process standardization. Technology provides a crucial tool in addressing these challenges, providing visibility into processes and giving operators the resources needed to ensure first-time quality.