MES vs MOM: What’s the Difference?
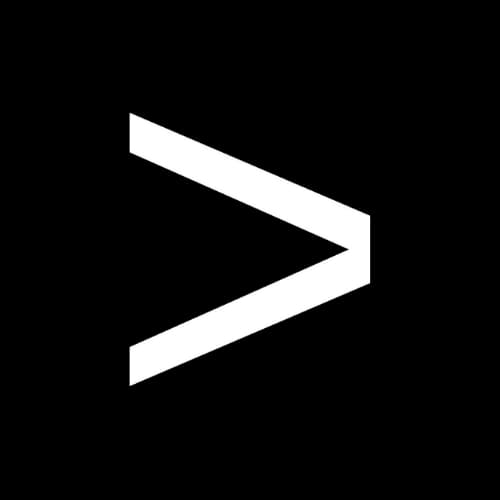
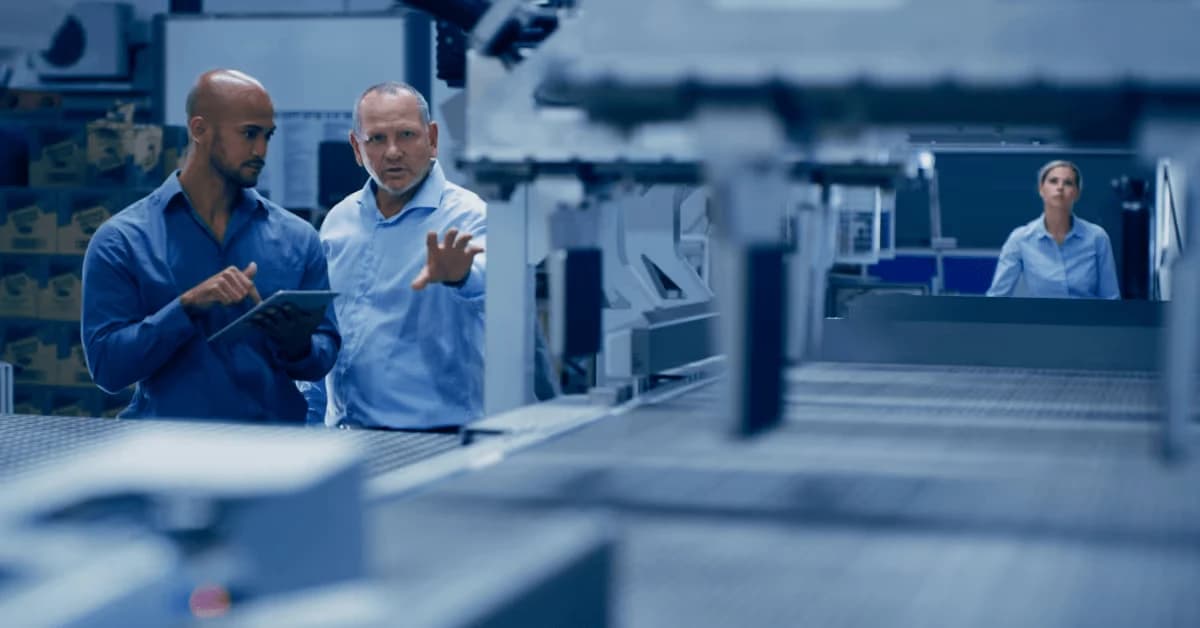
MES, MOM, ERP, PLM—there’s no shortage of acronyms in manufacturing technology, and sorting out the differences isn’t always easy.
This is especially true when it comes to understanding MES vs MOM, which are often used interchangeably but refer to two distinct types of automated manufacturing systems or smart manufacturing.
To help manufacturers understand this distinction and why it matters, this article explores:
- Where MES vs MOM overlap and where they differ
- Benefits of implementing MES vs MOM systems
- How MES and MOM fit into the larger picture of Industry 4.0
- The vital role of verification in ensuring MES and MOM systems are working as intended
Download our free eBook on Cost of Quality: The Hidden Truth About Your Ultimate Quality Metric
What Is A Manufacturing Operation Management (MOM)?
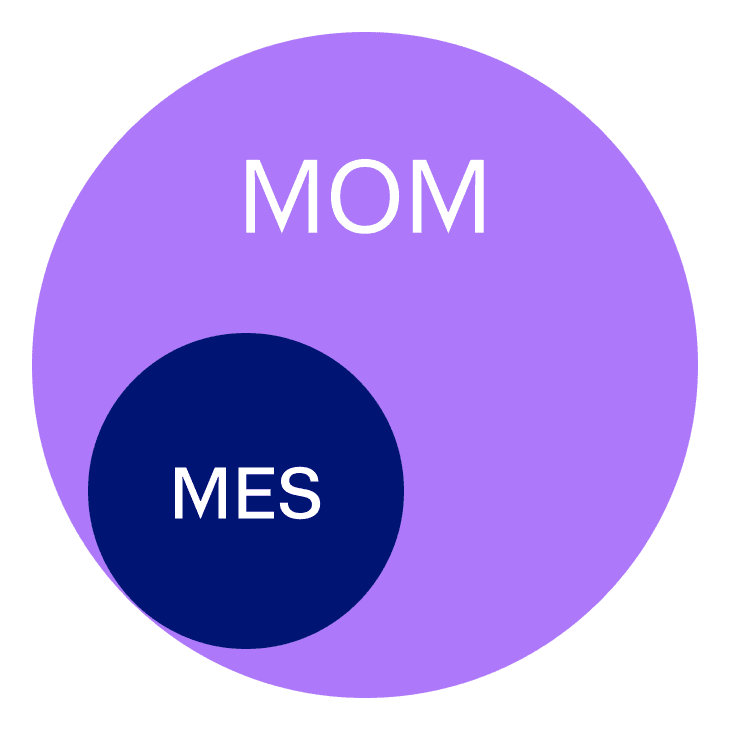
Manufacturing operations management (MOM) comprises Level 3 of the ISA-95 architecture, a framework developed by the International Society of Automation (ISA) to help manufacturers integrate business systems with control and automation systems. MOM is a system for tracking and managing your extended enterprise, encompassing other systems like:
- Manufacturing execution systems (MES)
- Supply chain management
- Shipping integrated logistics
- Quality execution
What Is A Manufacturing Execution System (MES)?
A manufacturing execution system (MES) is a central subset of MOM systems, and is used by companies to monitor and manage production processes in real time. The MES guides the flow of activities and materials on the plant floor, collecting data along the way that can be used to optimize manufacturing processes.
MES is event-driven, focusing on information like:
- When products are made
- How long it takes
- What resources are consumed
- What machines are used
MES vs MOM: Key Differences
MES and MOM differ in several key ways, including their scope, focus, integration, and visibility level:
MES | MOM | |
Scope | A subset of MOM. Focuses on plant floor production control activities such as production tracking and work instructions. | Holistic system that also encompasses all production support activities.
|
Focus | Primarily event-driven. Designed around improving efficiency and reducing waste in the production process itself. | Looks at optimization of all plant operations, covering areas like quality management, materials, maintenance, supplier management, and more.
|
Integration | Integrates with data from the plant floor and enterprise resource planning (ERP) systems (another term often used interchangeably with MES). | Integrates data from a wide variety of systems, including MES, quality execution systems, warehouse, logistics, and supply chain.
|
Visibility | Provides real-time visibility into every stage of the production process. | Offers broader visibility into plant operations beyond just production, like inventory and supply chain data.
|
Why Is the Distinction Between MES and MOM Important?
The difference between MES and MOM is important because of how they interact with aspects of the manufacturing environment.
Let’s take a look at a hypothetical example.
Imagine an MES that uses the Internet of Things (IoT) to automatically recognize when events have occurred. You see that the product has completed station 20 and has arrived at station 30, but hasn’t been processed through that step yet. What the MES shows you is that:
- You have work in process inventory between steps 20 and 30
- It has five more steps to be completed
- It will take two days, after which it will be ready to ship
However, just because you’re ready to ship doesn’t mean you have a truck coming to pick it up. This is where a MOM system would pull in information such as:
- The purchase order for a customer that must ship on a certain date
- What size truck will be needed to deliver the product
- The time window when the truck needs to arrive
Here the MOM system integrates with MES, which provides the input of which products are ready when. Integration with financial or customer systems links purchase orders, while integration with the logistics system allows you to schedule the pickup.
Ultimately, just because you can make a part doesn’t mean you should make a part. The MOM system ties together different silos of data to prevent poor decision-making, like making parts without an order or scheduling a machine without enough raw material available.
MES vs MOM: How Manufacturers Are Using Them Today
Most companies rely on MES systems to keep up with the fast pace of manufacturing. And while MOM adoption is growing, many manufacturers are still just dipping their toes, as these systems tend to be more complex to integrate.
For some, it’s still an open question of how these systems will pay off in terms of ROI. In fact, there are entire industries devoted to helping manufacturers achieve value from these systems, which hold the potential to drive further advances in Industry 4.0.
Benefits of Implementing MES and MOM Systems
Implementing MES and MOM systems offers many benefits to manufacturers, helping them build leaner production systems with less waste and higher profitability. Some of the biggest benefits of implementing these systems include:
- Improved efficiency: MES and MOM systems provide real-time data to streamline processes and accelerate production, reduce downtime, and optimize resource allocation.
- Enhanced quality control: MES allows manufacturers to track products through every phase of production to prevent defects, ensuring processes are followed so mishaps don’t happen in the first place. MOM goes a step further by integrating quality management with supply chain and inventory data to improve product quality overall.
- Lower costs: MES and MOM systems both help reduce costs by minimizing waste and defects, allowing teams to optimize production schedules while reducing manual labor.
- Increased flexibility: A robust MES allows manufacturers to adjust production schedules based on real-time demand—a core component of Lean manufacturing strategies. MOM, on the other hand, makes it easier to adapt to changes across all operations, whether it’s refining processes or responding to supply chain challenges.
- Regulatory compliance: Industries like pharmaceuticals, aerospace, and food manufacturing must comply with strict regulatory requirements. With MOM systems, companies can integrate plant floor checks into daily routines and monitor them at a high level for potential areas of noncompliance.
- Data-driven decision-making: MES and MOM systems collect vast troves of data that manufacturers can use to make more informed decisions and improve their processes.
MES, MOM, and Industry 4.0
Industry 4.0, hailed as the Fourth Industrial Revolution, centers on integrating advanced technologies like the Internet of things (IoT), big data, and AI into manufacturing processes. MES and MOM systems also have a critical role to play in the visibility and control of operations, acting as centralized hubs for managing the vast amounts of data generated on the plant floor.
Below are some examples of how MES and MOM are pushing the boundaries of what’s possible in Industry 4.0 to revolutionize manufacturing:
- Data from IoT sensors sent to the MES provides insights into machine performance and enables predictive maintenance to reduce costly downtime
- MOM integrates supply chain and plant floor data to help predict demand and respond to changes in the market
- Companies can use MES and MOM systems to build digital twins for testing different scenarios without disrupting production
- Mounted computers on forklifts tell operators precisely where to go and in what order to load boxes, based on information from the MOM system
- MOM system integration lets automatically guided vehicles (AGVs) know when work cells are depleted so they can bring fresh materials to the production line
Why Verification is Essential to MES and MOM Success
Even if you’ve implemented these systems to automate your process and minimize the chance of problems, there’s still the question of whether they’re actually operating the way you expect, day in and day out. That’s where verification is essential, using plant floor audits and inspections to root out otherwise hidden sources of variation and risk, like:
- Whether the work area is orderly, and free of hazards and unsafe conditions
- Whether operators are following work instructions
- Whether machine settings are correct
As manufacturers continue the long process of generating value from MOM tools, many are using specialized quality solutions like audit and inspection software to drive faster processing time and continuous improvements. Cloud-based software like EASE can be implemented relatively quickly compared with other Industry 4.0 applications, with manufacturers seeing real-life results such as:
- 50% reduction in quality costs
- 73% lower internal defects
- Higher customer quality ratings
As companies advance along their digitization journey, these software platforms can be integrated with the larger manufacturing ecosystem using open application programming interfaces (APIs).
MES and MOM are both important parts of Industry 4.0 technology, but they refer to two distinct aspects of optimizing operations. While MES is used by large enterprises and small businesses alike, MOM is a more complex system that can take time to implement and achieve value.
Cloud-based quality tools like audit and inspection software can help bridge the gap. These tools ensure systems and processes are working as intended on the plant floor, and offer the ability to quickly correct potential failure points before a defect occurs.