What is OEE in Manufacturing?
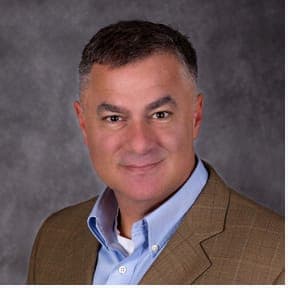

Research by Deloitte reveals that unplanned downtime costs manufacturers a full $50 billion every year, with poor maintenance strategies reducing a site’s productive capacity almost 20%.
Maintenance inefficiency, too, is a hidden yet significant driver of costs, with inefficient plants wasting as much as $300 million annually according to Efficient Plant magazine.
When equipment isn’t running, or when it’s not running at optimal conditions, that adds up to lost productive time, lost profits, delayed shipments and ultimately, dissatisfied customers.
It’s for these reasons and more that the concept of overall equipment effectiveness (OEE) was first developed, and why it remains a key metric for plants looking to improve efficiency.
So what defines a “good” OEE, and how can you improve this metric in your facility? This article explores these ideas, as well as topics such as:
- What goes into the OEE calculation
- The Six Big Losses and how they affect OEE in manufacturing
- Benefits of monitoring OEE and how to improve it
- Pitfalls and mistakes to watch out for when tracking OEE metrics
Download your free Cost of Quality eBook to learn about the hidden truth behind your ultimate quality metric
OEE Definition
Overall equipment effectiveness (OEE) is defined as a machine’s total productivity compared to its total capacity. OEE is calculated using three key variables:
- Availability rate, which is a function of equipment downtime
- Performance rate, which is reduced by slower cycle times
- Quality rate, which is a function of the number of defective parts produced
A perfect OEE of 100% would indicate that machines are running at 100% of their planned production time at an ideal cycle time with zero defects.
How to Calculate OEE
Manufacturers can calculate OEE for a single machine, a group of machines or even across an entire plant. The standard interval of time for measuring OEE is typically a single shift or day. However, OEE can also be measured for a single hour or part run.
The OEE calculation itself is relatively straightforward:
Below, we break down how to calculate each variable.
Calculating Availability Rate
Availability rate shows the proportion of planned production time a machine or plant is actually running.
For example, let’s imagine your planned production time is eight hours a day minus one 30-minute break for lunch, and you have to stop the line due to missing parts for 45 minutes. Breaking this down into seconds, your availability rate would calculate out to:
7.5 hours = 27,000 seconds
0.75 hours = 2,700 seconds
Calculating Performance Rate
Your performance rate shows how fast a machine operates as compared to its ideal speed based on the following equation:
In this scenario, let’s say you produce 200 parts in a day on a machine whose ideal cycle time is two minutes (120 seconds) per part. Your performance rate would then be:
Calculating Quality Rate
Quality rate is a simple calculation based on the number of good parts manufactured as a proportion of total units produced, like so:
Let’s imagine you produce 200 parts with 33 defects. Using this equation, your quality rate is:
Final OEE Calculation
Using the variables calculated above, the machine’s OEE is calculated via simple multiplication:
Improve Production Quality with Layered Process Audits and Maintain High Manufacturing Standards
Notice how the availability rate and performance rate are nearly perfect, and yet the final OEE calculation sits at 74.1%. This highlights how, because OEE involves multiplying percentages or proportions, small changes in a single variable can have a significant impact on OEE.
OEE, TPM and the Six Big Losses
OEE is closely related to Total Productive Maintenance (TPM), a strategy introduced by Seiichi Nakajima in 1969 at Japan Nippon Denso, now part of Toyota.
Called the father of TPM, Nakajima was part of the post-World War II quality revolution in Japan. TPM applies many of the same principles found in Total Quality Management (TQM) and the Toyota Production System (TPS) to eliminating waste and inefficiencies associated with equipment.
Nakajima’s famous book Introduction to TPM centres on how to maximize the effectiveness of equipment in the manufacturing process, defining what is called the Six Big Losses that impact OEE.
Availability loss |
|
Performance loss |
|
Quality loss |
|
By categorizing the most common types of manufacturing losses, OEE provides a window into where these losses are affecting overall productivity. Thus, it is through analyzing the individual variables of OEE that manufacturers can identify specific actions for improving machine or plant performance.
Availability Loss
Availability loss is caused by any planned or unplanned stops during the time equipment is scheduled to be running.
Unplanned stops include those caused by:
- Machine breakdowns
- Tooling failure
- Reactive maintenance
- Delays related to upstream or downstream equipment
- Lack of available operators or materials
Planned stops are typically related to machine setup in lean manufacturing, including:
- Tooling or machine changeovers
- Equipment adjustments
- Machine warmup time
- Scheduled maintenance
Performance Loss
Performance loss is a function of two variables: minor stoppages or machine idling and reduced operating cycle times.
Compared with the types of stops described above, minor stops typically last under a few minutes and are resolved without involving maintenance. Causes may include:
- Jammed material or misfeeds
- Incorrect machine settings
- Machine sensor issues
- Equipment cleaning
One common challenge here in terms of measuring OEE is accurately tracking minor stoppages. Often, these minor stoppages may happen on a timescale of seconds and aren’t even noticed by the operator.
Reduced operating cycle time occurs when a piece of equipment doesn’t meet its ideal cycle time, even if the operation is running. This means fewer parts produced and can be caused by factors such as:
- Machine or tooling condition
- Startup and shutdown
- Material quality issues
- Inexperienced operators
Quality Loss
Quality loss is a direct function of the number of defective parts produced over the measured interval of time. This includes both scrap and rework, because even rework causes a loss in productivity, affecting the time that is truly productive.
Scrap and rework can be caused by startup rejects that happen right after changeover or during warmup, as well as production rejects once equipment is warmed up. Quality loss may be caused by:
- Operator error
- Incorrect machine settings
- Extended warmup times
Benefits of Monitoring OEE
Measuring and monitoring OEE as a manufacturing KPI offers several benefits, including:
- Continuous improvement: Improving OEE requires analyzing your processes for bottlenecks that impact overall productivity. Tracking OEE helps plants achieve their continuous improvement goals and helps identify new opportunities for improvement.
- Eliminating waste: OEE strategies help identify areas for improvement in terms of where the Six Big Losses might be affecting plant performance. Monitoring OEE can provide early signals of impending equipment issues that can lead to costly downtime. The Six Big Losses are closely related to types of waste in Lean, so working to improve OEE can also positively impact Lean initiatives in the plant.
- Increasing profitability: If a plant is able to produce even 10% more parts on a shift, this can mean a substantial boost in profits as well as increased equipment ROI. Monitoring OEE can also provide early signals of impending equipment issues that can lead to costly downtime.
- Boosting productivity: Measuring OEE over time for a given machine, department or plant can help show you what’s working, what’s not and when you need to step in to increase productivity.
OEE Isn’t the Whole Story
It’s vital to note that OEE is a summary metric and is not actionable on its own. Furthermore, availability, performance and quality must all be generally balanced—and equally important in your operations—for OEE to be a valuable metric.
Why is this important? For starters, as we mentioned earlier, small changes in one variable will have a big impact on the final OEE calculation. Furthermore, in situations where one variable must take priority over the others, increasing OEE may actually run counter to your goals.
Let’s imagine, for instance, that you’re willing to tolerate a few more startup rejects to increase availability on an expensive piece of equipment where downtime is simply too costly. Focusing on OEE here might point you towards going slower to improve quality, but this would come at a cost.
In some situations, OEE optimization can even be dangerous, such as if you’re manufacturing safety-critical parts such as EV battery temperature sensors. Here, quality must take priority over other measures of effectiveness.
OEE vs. Total Effective Equipment Performance (TEEP)
Total effective equipment performance (TEEP) is a metric that’s closely related to OEE. TEEP is also used to measure equipment effectiveness, with one key difference from OEE.
Rather than looking at just planned production time that equipment is productive, TEEP takes into account all potential operating time. This includes scheduled maintenance, changeovers or other planned downtime.
Why is the distinction important?
OEE is often used to measure the productivity of a single machine. TEEP, on the other hand, can provide insight into productivity for the entire production line. Where there’s a gap between OEE and TEEP, this should raise questions about the source of this disparity.
Common Mistakes in Tracking OEE
Monitoring and measuring OEE over time can help improve manufacturing productivity and identify areas where the hidden factory may be at work. That said, there are several pitfalls in tracking OEE that manufacturers should be aware of:
- Identifying the ideal cycle time: It’s not uncommon for plants to set their ideal cycle time too low to account for factors like aging machinery or material issues. However, this mistake will make OEE look higher than it is, obscuring losses that underly equipment issues that need to be fixed.
- Setting unrealistic goals: Some companies hear 80% OEE as world-class and immediately make that their target. The problem is that this can set you up for failure, and it won’t motivate your team if you’re starting at 40% OEE, for example. Focus on incremental progress, not the absolute result.
- Excluding downtime: You may want to exclude certain times from your OEE calculation such as shift changes, short stops or times when there aren’t operators to work the equipment. This can distort your OEE calculation, and the more you include, the better you’ll be able to identify losses holding back performance.
- Taking an isolated view: Viewing OEE in isolation often means overlooking other factors that would indicate OEE is not the right metric to use. OEE is most valuable when viewed in tandem with other metrics like cycle time, scrap rate and first-pass yield.
Benchmarking Your OEE
If you’re just getting started measuring OEE, you may be wondering what qualifies as a “good” OEE. The answer may vary by company. What’s more, it may not even be the right metric to track, as discussed earlier.
For general purposes, industry experts would consider an OEE of 80% or above as world-class. Conversely, anything 50% or less would be considered low.
OEE | Classification |
≤ 50% | Low |
50-80% | Typical |
≥ 80% | World-Class |
Striving to hit an arbitrary target may not be useful, especially if you’re just starting out with measuring OEE. That said, it can be a useful benchmark for:
- Comparing OEE to similar machines
- Measuring OEE for a machine across different shifts
- Comparing OEE across different plants
Drilling down into availability, performance and quality at the plant level, for instance, might point to where you need to improve maintenance, job setups or process adherence.
At the division level, you might look at OEE to compare plants to see how individual sites compare to one another. Within a group of 10 plants, for example, you might identify three lagging plants and decide to investigate further to get them to a higher level of productivity.
OEE as a Baseline
OEE can also be useful as a baseline to track over time, whether on individual machines, production lines or plants. Using OEE as an indicator in this way can help plants:
- Find hidden sources of waste
- Improve productivity of machines
- Proactively identify equipment issues with declining performance
Strategies for Improving OEE
Improving OEE requires drilling down into availability, performance and quality to identify where the Six Big Losses are impacting operations. Below, we discuss some strategies for finding and addressing these losses.
How to Improve Availability Rate
Several common problems can impact machine availability, with maintenance issues being the most obvious. Preventive and predictive maintenance strategies are essential to avoiding unplanned downtime, and should be a key priority given that more than half of manufacturers still rely on reactive maintenance.
Setup and changeover times are also a primary driver of availability issues. Modest reductions in setup times can equate to hundreds of shifts over the course of the year, with more products rolling off the line and less overtime burden for workers.
One Lean tool used to reduce changeover time is single-minute exchange of die (SMED). SMED focuses on reducing changeover times to single digits by:
- Converting as many internal changeover steps, which can only be done when the equipment isn’t running, to external steps that can be completed while the machine is running
- Streamlining remaining internal changeover steps, for example by standardizing parts or implementing 5S strategies to ensure efficient use of the workspace
Last but not least, material and operator availability will have a significant influence on machine availability. In terms of materials, this can mean 20 people are left standing around for 10 minutes or more while the work cell must shut down to wait for one little clip on a front-end module. In terms of operators, something as simple as someone leaving the production line to use the restroom could mean missing a cycle.
While it may be tempting to blame these types of issues on people, manufacturers need to look at the deeper root causes of these problems by looking at whether:
- You have sufficient processes in place for requesting materials
- You need to implement new systems or technologies to prevent work cells from running out of materials
- Whether you need to cross-train workers on different machines to provide relief for operators as needed
How to Improve Performance Rate
Several factors can cause minor stoppages and reduced speed that are contributors to performance loss. Machines running at suboptimal conditions is one example. For example, if a machine is leaking hydraulic fluid or is running air pressure at 40 psi rather than 60 psi, this can have an impact on performance rate.
These problems highlight the need to stick to preventive maintenance schedules in order to meet ideal cycle times. If you’re using predictive maintenance tools, degradation in performance rate can indicate that you need to increase maintenance frequency so that the machine runs as it’s supposed to.
It’s not just machines that plants need to look at when assessing issues with performance loss. Tooling condition issues can also slow down the process, particularly when they require operators to rework parts. If a damaged tool creates a burr or flash on a part that needs to be removed, for example, this can mean an increase in cycle time that pushes down performance rate.
Finally, adherence to standard work has a significant effect on performance rate. If takt time means you need to produce a part every two minutes, but it actually takes an additional 15 seconds due to someone adding a step, this will have an impact on OEE.
Many of these issues can be identified with a program of frequent plant floor audits to verify items such as whether:
- Operators are performing preventive maintenance tasks
- Tools are in good condition and performing as expected
- Operators are following standard work instructions
- Unexpected issues are arising in the process that slow down cycle time
How to Improve Quality Rate
As manufacturers strive to hit production quotas and shipping deadlines, quality can sometimes take a backseat. What OEE recognizes, however, is how poor quality affects overall productivity, where plants are wasting time and resources producing bad parts.
The main issue manufacturers should be concerned about when it comes to improving quality rate is process adherence. Defects can happen anytime:
- Operators don’t follow work instructions
- The process itself varies, whether due to machine setup, condition or use
- Corrective actions aren’t held in place, and people revert to previous processes
Here again, plant floor verification is essential to ensuring that plant floor operations follow documented standards. Plant floor audits and inspections allow you to spot-check critical steps, machine settings and other process inputs. They also allow you to periodically check in on corrective actions that have been implemented, helping identify areas of non-conformance while reinforcing their importance to operators.
How to Apply the Theory of Constraints to OEE
The Theory of Constraints is a continuous improvement philosophy that focuses on identifying bottlenecks that constrain the entire system as a whole. The idea is that if you can eliminate these bottlenecks, the flow throughout the rest of the system will improve accordingly.
This theory provides some important direction as to where to start measuring OEE, and that is at the constraint step.
To identify the constraint, manufacturers must analyze different factors to find which machines or processes are limiting the production line’s overall throughput or efficiency. Activities to help plants do it include:
- Throughput analysis: Which machines or processes have the lowest throughput compared with others on the production line?
- Bottleneck observation: Where does inventory tend to accumulate? Slower processing speeds or increased stoppages may be at play.
- Downtime analysis: Equipment that has frequent breakdowns, changeovers or maintenance needs may be a constraint on the process.
- Cycle time analysis: Looking at each machine’s cycle time can provide important clues into equipment that may be slowing down the process.
- Capacity planning: Comparing real-life performance of machines against their designed capacity can help identify where equipment is operating at sub-optimal conditions.
Using Plant Floor Software to Improve OEE
Manufacturers can use plant floor software in a variety of ways to improve OEE scores. Strategies here include using audits and inspections to identify areas where the Six Big Losses may be impacting performance, accelerating issue resolution and connecting workers to additional support.
Plant Floor Audits and Inspections
Conducting regular plant floor audits and inspections can help show you where the Six Big Losses are hurting productivity, specifically by verifying that:
- Preventive maintenance tasks are performed
- Machines are running correctly
- Tooling is in good condition
- Operators are following standard work instructions
- Corrective actions are held in place
Accelerating Issue Resolution
When a problem is identified on the plant floor, it’s imperative to have a way to quickly resolve it. Plant floor inspection software makes it easy to log issues in the system and get tasks routed to the right people.
For example, if a tool needs replacement or servicing, this can be documented and communicated to the parties responsible for maintaining equipment. Fixing the issue faster can have a significant effect on the performance score, especially if your plant has several stations where rework is happening as a result of tooling issues.
Connected worker solutions that make it easy for operators to get the help or resources they need can help improve OEE by reducing stoppages. The ability to request additional materials, relief or even ask questions helps keep the line running more smoothly to increase uptime as a whole.
OEE is an important metric for measuring manufacturing efficiency that can provide insight into common causes of productivity losses. By digging into availability, performance and quality losses, plants can identify practical actions to improve plant productivity and thus profitability. Achieving meaningful increases in OEE comes down to careful analysis, and a commitment to eliminating hidden sources of waste associated with machines.