OEE KPIs: What Manufacturers Need to Know
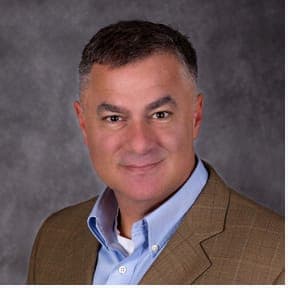
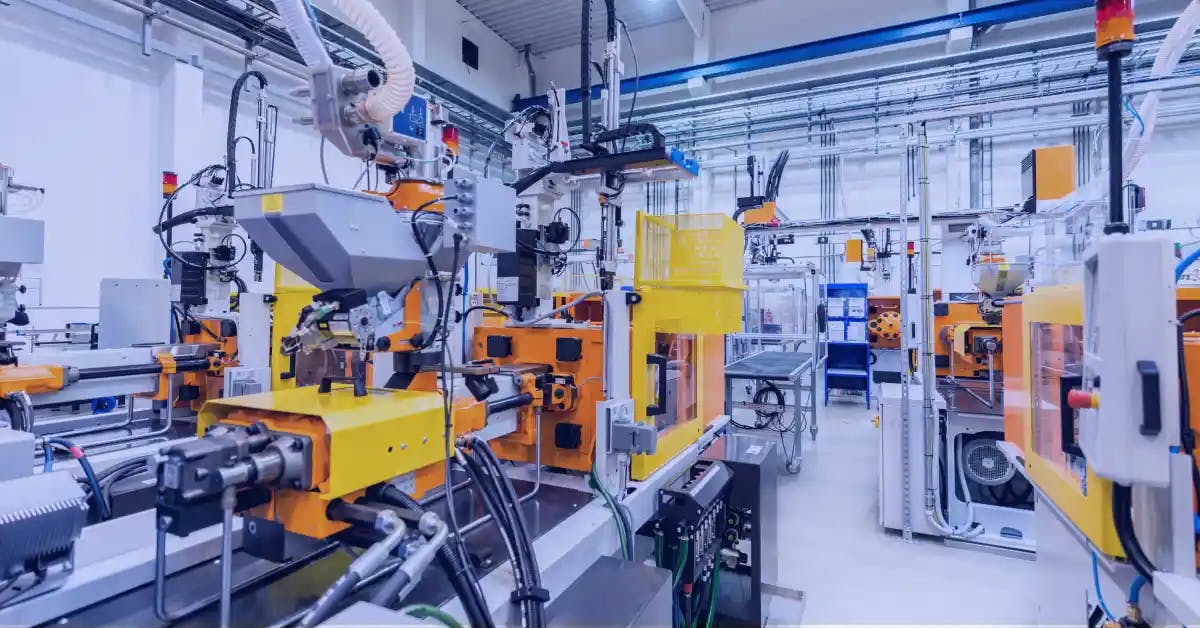
Overall equipment effectiveness key performance indicators (OEE KPIs) are important measures to track for plants looking to maximize productivity and quality. However, improving them comes with significant challenges, and isn’t always as straightforward as it seems.
At The Luminous Group, we recommend a balanced approach to tracking OEE, viewing it in your plant’s unique context to ensure you’re prioritizing the right goals. Let’s look at the components used to calculate OEE, what you can do to improve each component and, just as important when it’s not the right metric to use!
Download your free Root Cause Analysis 101 Guidebook to learn about top tools for finding the root cause of manufacturing issues
What Is OEE?
Overall equipment effectiveness (OEE) describes the total productivity of a machine relative to its capacity, based on three key variables:
- Availability
- Performance
- Quality
An OEE of 100% indicates perfect production processes, with machines always running at their ideal cycle time and producing zero defects.
OEE and the Six Big Losses
Availability, performance and quality are all impacted by the Six Big Losses in Lean Manufacturing. Thus, tracking OEE KPIs allows plants to identify where these losses are impacting productivity.
Availability loss |
|
Performance loss |
|
Quality loss |
|
How OEE Is Calculated
OEE calculation is determined using the following equation:
Now let’s look at each variable in more detail, with examples.
Availability Rate
Availability rate describes the percentage of planned production time a machine runs using the following equation:
Let’s say planned production time for a machine is 7 hours (25,200 seconds) a day, and you lose one hour (3,600 seconds) to a breakdown. Availability would then be:
Performance Rate
Performance rate describes how fast a machine runs compared to its optimum speed, using the equation below:
Let’s say you manufacture 100 parts per day on a machine with an ideal cycle time of three minutes (180 seconds) per part. Performance is then calculated as follows:
Quality Rate
Quality rate describes the percentage of good units produced using the following equation:
Thus, if you produce 100 parts with nine defects, your quality rate would be:
OEE Calculation
Based on the factors above, your OEE calculation would be:
Track non-conformances, make sure corrective actions get closed, and leverage real-time data to drive continuous improvement!
Improving Performance Rate
Common sticking points in improving performance rate are:
- Maintenance
- Standard work instruction adherence
- Tooling condition
Maintenance and Performance Rate
Plants may mistakenly believe that they can improve OEE KPIs by delaying maintenance to keep machines running. What often happens is that the machine may stay running, but at suboptimal conditions, meaning you don’t meet your ideal cycle time.
Keeping up with preventive maintenance is key, while those using predictive maintenance can use degradation in performance rate as an indicator to change maintenance frequency.
Standard Work and Performance Rate
Let’s say your plant has quoted a part at 60 seconds, but in actuality, it takes 66 seconds to produce one part. One way to approach the issue is with a Fishbone diagram exercise, looking at the 6Ms of process control. One critical factor here is adherence to standard work instructions, using layered process audits as verification. Connected worker software can also help by providing guided procedure checklists to keep the process moving at the desired pace.
Tooling Condition
Tooling condition is a hidden factor that causes slowdowns due to rework. For instance, a damaged tool might create a burr that needs rework, slowing down cycle time. Injection molding is another example, where a damaged tool creating flash on a part may require a slower injection speed.
Improving Quality Rate
Some of the biggest challenges in improving quality are:
- Standard work instruction adherence
- Process adherence
- Problem-solving implementation
Standard Work and Process Adherence
Any time operators aren’t following standard work instructions (or aren’t following them all the time), you run the risk of defects. The same is true for any variations in the process itself due to machine setup or use, for example:
- Running parts too hot, which causes them to warp
- Variation in a plating process that causes variance in plating thickness
- Variation in weld speed that affects the percentage of good parts
Daily verification of standard work, such as layered process audits, helps avoid these problems and ensures adherence to standards. Connected worker tools also provide visibility into process adherence, so that manufacturers can see what is—or is not—happening on the plant floor.
Problem-Solving Implementation
If you implement a corrective action but don’t hold the solution in place, there’s a high likelihood that operators will fall back on old habits. Related to process adherence, using verification to ensure corrective actions are sustained is essential to quality. Connected worker solutions that allow you to track nonconformances in real time are also critical, making it easier to spot problems before they cause downstream issues like defects and complaints.
Optimizing OEE Isn’t Always the Answer
OEE isn’t meaningful unless availability, performance and quality all have equal value and are roughly balanced since small changes in one variable can distort OEE. What’s more, focusing exclusively on optimizing OEE can lead you down the wrong path.
Examples include:
- Reducing setup time: Running larger lots can increase availability by decreasing the number of setups performed, however this also ties up capital and floor space while potentially increasing scrap—the very opposite of Lean best practices.
- Dealing with high-cost defects: If you’re producing diamond-encrusted tools, for instance, defects will cost you far more than downtime.
- Using high-tech/high-capital equipment: In this case, availability takes priority over other factors as downtime comes at a premium. If you have a multi-axis, multi-laser cutting machine that needs to be up and running, availability needs to be weighted higher than performance and quality.
- Producing safety-related parts: Quality is paramount when safety-related parts like airbags or temperature sensors on EV batteries are concerned. In these cases, trying to optimize OEE can be downright dangerous.
The key takeaway here: OEE is not the manufacturing metric to use all the time. It is a summary metric, and not always descriptive of what you’re trying to achieve.
OEE Dashboards and Metrics Tracking
An OEE dashboard can help you track OEE KPIs at the plant and machine level, using tools like PowerBI or Tableau to put the metrics in context. Pulling data from solutions like layered process audit software, for instance, can help spot trends affecting OEE like when a work cell has a high frequency of process conditions out of standard.
Ultimately, OEE is an important metric for understanding how well your machines are running compared to their capacity. That said, it can’t be used in a vacuum and isn’t always the right metric to focus on. For many, the key is drilling down into the OEE components, focusing on them individually to bring them into balance before measuring OEE at a high level.
Streamline your production with expert insights on Layered Process Audits. Improve your OEE KPIs and ensure quality. Download the guide now for best practices and digital strategies!
Using OEE to Identify Areas for Improvement
The example above highlights the use of OEE as a manufacturing KPI. After all, if a machine is only effective 55% of the time, that means 45% of the time, it isn’t running as effectively as it could be. Clearly, there is room for improvement.
Looking at the individual variables of OEE provides important clues about where to start enhancing equipment utilization:
- Availability: Why did the machine break down? Were there any signs of an impending breakdown, and were all scheduled maintenance tasks performed?
- Performance: Why were only 100 parts produced, when in theory the ideal cycle time would allow the machine to produce 140 parts daily?
- Quality: Did the nine defects result from a process or machine issue? Or did they result from operators not following standard work?
Using OEE as a Benchmark and a Baseline
Manufacturers can use OEE as a benchmark to evaluate the performance of a machine, including by comparing it to:
- Industry standards
- Other similar equipment
- OEE on different shifts
Tracking OEE over time also provides a baseline when your goal is to eliminate waste and improve the productivity of machines.
So what is a good OEE? As a rule of thumb, our team considers an OEE score of 80% as world-class, while 50% or less would be considered low. Below we examine some common challenges and potential solutions for improving each of the factors that go into OEE.
Improving Availability Rate
Some of the biggest factors affecting the availability rate are:
- Maintenance issues
- Setup time
- Material availability
- Operator availability
How Maintenance Affects Availability
Reactive maintenance, also called breakdown maintenance, is a significant driver of unplanned downtime and reduced availability. Instead of waiting for machines to break down, While most manufacturers have implemented preventive or predictive maintenance capabilities to prevent unplanned downtime, some issues that can impact effectiveness include:
- Lost issue reports and overdue maintenance requests
- Pencil-whipped autonomous or operator-driven maintenance checklists
- Lack of access to support materials and troubleshooting guides
Setup Time
Setup time should be evaluated whenever availability rate is an issue. One strategy here for improving availability is a single-minute exchange of die (SMED), a Lean tool for reducing changeover time to single digits, or less than 10 minutes.
SMED focuses on making as many changeovers as possible external setups, which operators can perform while the equipment is running. Other steps are subsequently streamlined to reduce the number of overall steps to complete changeovers as quickly as possible.
In one recent project, for example, The Luminous Group used SMED to help a plant reduce setup time by 13 minutes, which equates to 180 shifts in the plant over a year’s time. The result was more products rolling off the line with much less required overtime, an excess of which can hurt employee morale.
Material Availability
Material availability within a plant is a common issue that can constrain machine availability. Consider an example where an entire production line must shut down for 20 minutes just because a forklift driver forgot to pick up a clip needed for an automotive instrument panel.
It’s situations like these that are driving plants to adopt connected worker solutions, which enable bidirectional communication in real-time to minimize downtime, including material availability issues.
Operator Availability
Any time an operator leaves the line—even just to use the restroom—you run the risk of not loading the machine in time and missing a cycle.
Often this comes down to discipline, but in some cases, you need to look deeper. Did the operator leave because they needed more materials? Was there nobody who could step in to relieve them?
Again, these are areas where connected worker software can help bridge the gap. Dynamic training and worker guidance can help train operators faster on a wider number of machines, allowing for more flexible use of staff resources.