OSHA SVEP: What Manufacturers & Employers Need to Know
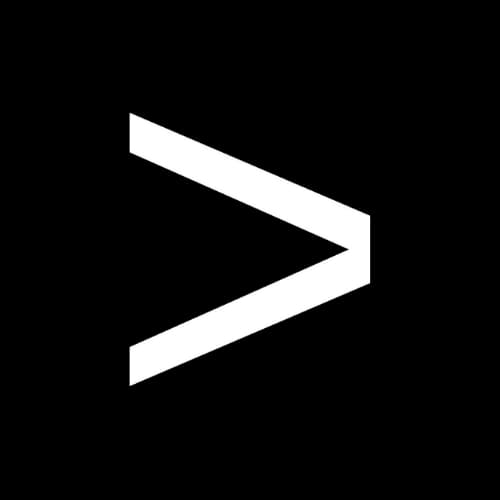
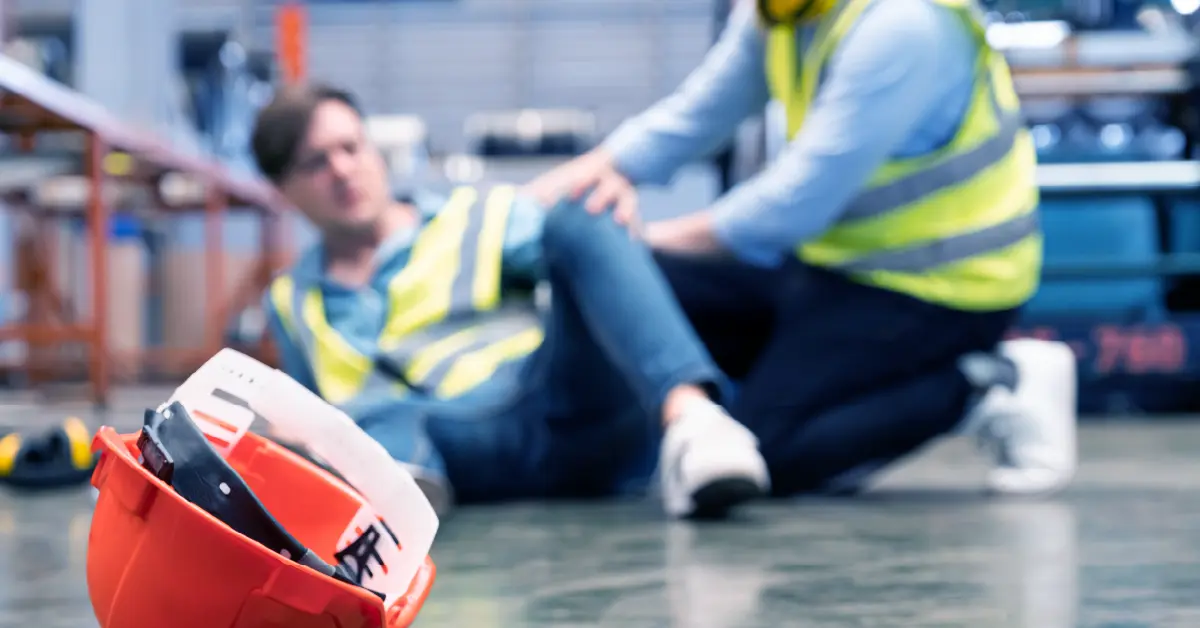
Employers that don’t address workplace safety hazards now face heightened enforcement thanks to recent expansion of the U.S. Occupational Safety and Health Administration (OSHA) Severe Violator Enforcement Program (SVEP) criteria.
The move follows years of criticism of the program’s onerous requirements, a sign that OSHA is doubling down on its increasingly strict approach to dealing with careless violators, including those who may qualify for SVEP even if none of the criteria are met.
Below, we’ll look at what the OSHA SVEP is and what the program changes mean for manufacturers. We’ll also explore how companies can avoid being placed in the SVEP, and why frequent plant floor checks are vital to safety vigilance.
Download a free whitepaper to learn Why and How Digital Safety Inspections Help Companies Work Safer
What Is the OSHA Severe Violator Enforcement Program?
OSHA’s Severe Violator Enforcement Program was created to place more stringent enforcement on employers that repeatedly and willfully violate occupational safety and health regulations.
Under SVEP, employers that have demonstrated indifference to occupational health and safety and have a history of significant violations are placed on a public log, where removal takes years and requires meeting numerous demands.
The OSH Act mandates that an employer must ensure the safety of its workers, and the SVEP enforces compliance by monitoring companies’ adherence to OSH act obligations.
What are the Criteria for Placement in the SVEP?
Previously, the SVEP focused on high-emphasis hazards and highly dangerous chemical hazards. Under the expanded criteria, it now covers all OSHA standards. An employer who demonstrates indifference to their OSH act obligations (or willfully violates them) may be hit with a SVEP case if an inspection meets any one of the following criteria:
- A fatality or catastrophe inspection with at least one willful or repeat violation, or a failure-to-abate violation based on a serious violation related to a fatality or an incident with three or more hospitalizations
- An inspection with at least two willful or repeat violations or failure-to-abate notices based on high-gravity serious violations, or any combination of these
- All egregious enforcement actions and citations
Note also that companies with multiple facilities are particularly at risk of repeat violations, e.g., if two separate sites receive lockout/tagout violations. In addition, OSHA has directed regional offices not to group citations, meaning failure to train employees could result in separate citations for each employee not trained properly.
What Are the Consequences of SVEP Placement?
The SVEP allows the administration to take more aggressive enforcement action against violators it says ignore their obligations under the law, aiming to deter violators with severe consequences such as:
- Publicly naming the company on OSHA’s website, which may lead to reputational damage that can result in lost business opportunities.
- Subjecting violators to more frequent and detailed follow-up inspections (even across multiple sites)
- Revealing details of violations in OSHA press releases
- Requiring violators to submit quarterly OSHA injury logs
Equally concerning for companies is the fact that it could mean losing significant revenue from customers that won’t work with companies on the SVEP public log.
Is SVEP Removal Possible?
Once you’re in the SVEP, you can’t be removed from the SVEP log until at least three years after an acceptable abatement verification from OSHA.
This requires employers to:
- Abate all SVEP-related hazards
- Pay all penalties
- Complete all settlement provisions
- Have no additional serious citations of occupational safety and health hazards from the SVEP inspection, or any related establishments
- Have one follow-up or referral inspection by OSHA
According to OSHA, the only way to reduce the SVEP term to less than three years from the date is if the employer agrees to an enhanced settlement agreement with OSHA. Settlement agreements may require the employer to:
- Implement a safety management system within two years covering the seven elements detailed in OSHA’s Recommended Practices for Safety and Health Programs, as well as how the establishment will evaluate and improve its effectiveness
- Have OSHA review and evaluate the safety management system
- Undergo third-party verification subject to OSHA approval for program implementation
Workplace Safety Prevention and Vigilance
While some companies may look at fighting citations, ensuring compliance in the first place is a better strategy. A system of frequent safety inspections play several key roles here, by:
- Providing ongoing checks of known safety issues to prevent incidents, injuries and compliance violations
- Addressing several elements of OSHA’s recommended practices for safety and health management programs
- Demonstrating a commitment to meeting compliance obligations, including verifying training effectiveness
One critical consideration here is the need to follow up on action items from inspections, as failure to do so could be grounds for a willful violation and potentially lead to a notice based on a serious violation.
Companies that have received violations in the past in particular shouldn’t waste time enacting a program of frequent safety checks to avoid repeat failures and failure-to-abate citations.
How to Be Proactive With Occupational Safety and Health Administration
Safety inspection software can help companies develop and implement a safety program, avoid OSHA violations, and, most importantly, eliminate hazards—all while making inspection resources and programs easier to manage.
By establishing a safety and health management system, employers can quickly implement frequent inspections across multiple facilities, proactively identify hazards and report on findings and trends. Just as important, this software helps track and follow up on action items, which helps to minimize OSHA inspection findings.
OSHA’s SVEP comes with serious consequences, especially when OSHA finds at least two repeated violations. It’s not hard to see how small problems can lead to years-long consequences (practices that are effective on purpose). Daily safety checks and ensuring you close the loop on hazards are critical to avoiding compliance issues, and building a stronger safety culture for all employees.