Poka Yoke in Manufacturing: Essential Principles
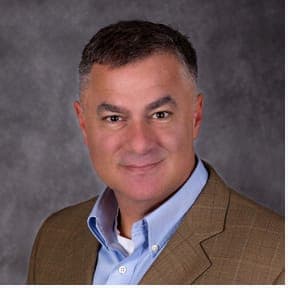
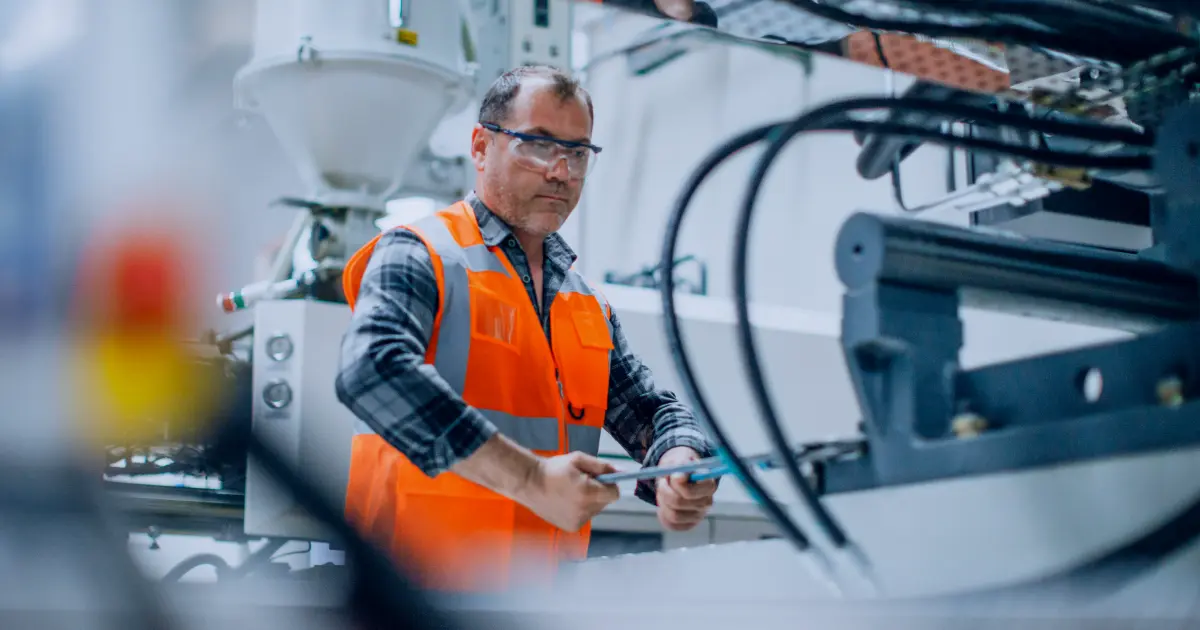
While we might not notice them, there are many devices in everyday life that protect us from our own mistakes. A collision alert goes off in your car, warning that you’re about to rear-end the vehicle in front of you, then applies the brakes automatically if you don’t slow down. A hedge trimmer cuts off power when material gets jammed in the blade to prevent kickback. An overflow drain ensures you don’t accidentally flood your house if you leave the bathtub faucet on.
These are examples of what would be described as a poka yoke in manufacturing to prevent defective products. In other words, what poka yokes do is to build safeguards into processes or products to prevent defects or safety incidents. To see how to apply poka yoke in your plant, this article looks at:
- The basic principles of poka yoke
- Different types of poka yoke systems
- Poka yoke implementation tips
Learn how much quality may be costing you with our free eBook on Cost of Quality: The Hidden Truth About Your Ultimate Quality Metric
What Is Poka Yoke in Manufacturing?
Poka yoke is a Japanese term that translates to “error-proofing.” Poka yoke in manufacturing refers to a mechanism used in the process to avoid errors and mistakes. Poka yoke was a concept first introduced by Shigeo Shingo in the 1960s, as part of the Toyota Production System.
Error-Proofing vs. Mistake-Proofing
At The Luminous Group, we think of poka yoke in manufacturing as falling into two distinct categories: error-proofing and mistake-proofing, both of which contribute to continuous improvement.
When you error-proof something, it is impossible to do it incorrectly. An example from safety is using dual palm buttons to activate machinery in very fast operations, which ensures operators can’t get their hands caught in equipment.
When you mistake-proof something, it means the operator can’t pass the mistake onto the next station. For instance, imagine a process that requires operators to place parts under a machine vision camera that detects defects before advancing the part to the next station.
Error-proofing is more effective than mistake-proofing because it is inherently focused on prevention rather than detection or mitigation. Below, we discuss different types of both error-proofing (prevention) and mistake-proofing (detection) poka yoke.
Error-Proofing Poka Yoke Principles
Error-proofing poka yokes to prevent errors utilize one of four principles:
- Elimination: With elimination, the goal is to eliminate errors by removing the step or part altogether. Version tracking in many software programs eliminates the possibility of losing a template used by many people if someone makes changes to the template and saves over the original, showcasing a type of poka-yoke in digital workflows.
- Prevention: An example of prevention would be a round part that can be loaded upside down or right side up. The product is designed so that orientation doesn’t matter, meaning that an operator literally can’t load it incorrectly.
- Replacement: Replacement focuses on redesigning products so that operators can’t forget a piece or orient it incorrectly. If you have a two-piece stamping and you replace it with a one-piece casting, the operator can never forget a piece or orient it incorrectly. This is essentially what Tesla is aiming to do with its gigacasting system, where an entire vehicle’s rail system is cast as a single piece, rather than using a welded frame.
- Facilitation: Facilitation is about making it easier, faster and safer for people to do their jobs. An example here would be replacing a gate that must be opened and closed with a light curtain.
Mistake-Proofing Poka Yoke Principles
Mistake-proofing poka yoke systems focus on two key principles: detection and mitigation.
From a detection perspective, mistake-proofing poka yoke devices or steps should make it easy to identify whether or not a step was performed correctly.
Imagine, for instance, a process that involves putting a black rubber stopper on a black part, making it difficult to see if the rubber stopper is assembled. By replacing it with a white stopper, it becomes immediately evident if the rubber stopper isn’t on the part.
Mitigation, on the other hand, is about reducing the impact of potential defects.
For example, consider a work station involving robotic fastening of multiple screws. A poka yoke here could be a vision detection system to check that all screws are present, highlighting the position of any missing screws so the next operator can add them.
Download free comprehensive safety inspection checklist template to enhance workplace safety and streamline your inspections!
Poka Yoke Devices and Methods
Poka yoke devices fall into two categories: control-based devices for error-proofing or prevention, and warning-based devices for mistake-proofing or detection.
Control-based devices identify the problem and stop the process immediately. Warning-based devices signal the problem to the operator without necessarily shutting down the process.
Both control-based and warning-based devices can apply three distinct methods for error-proofing or mistake-proofing, which are part of a comprehensive poka-yoke method:
- Contact method: This method identifies deviations using mechanisms that involve direct contact with other parts. For example, imagine a round part that must be oriented to 12:00. By placing a small slot on the round part and a key in the correct position of the part it touches, it ensures the part can’t be oriented incorrectly.
- Fixed-value method: Fixed-value methods often involve measurement devices such as scales or counters to prevent or identify nonconformances in the manufacturing process.
- Motion-step method: Motion-step methods focus on ensuring operators perform the right steps in the correct sequence. For example, a device may count the number of motions executed, such that a part is clamped until the operator makes torque six times when driving in the screws.
Poka Yoke Starts with Design
The earlier you can implement poka-yoke, the more valuable it is to your operation, and it significantly reduces human error. That’s because the less value that has been added to the part when you identify the defect, the less complex and costly it is to fix the problem.
Manufacturers should look at poka yokes beginning at the design stage, specifically when they are conducting a failure modes and effects analysis (FMEA) or process FMEA (PFMEA). Here poka yokes can be applied as prevention and detection controls for various failure modes to prevent known causes of defects or issues.
If misorientation of a part is an issue, for example, your prevention control could be to add an orientation feature on the part so that operators know exactly how to load it.
Put Poka Yokes Before Your Constraint Steps
There’s another important theory that goes into where to implement poka yoke that relates to constraints or bottlenecks in your process.
The idea is that if you do have a bottleneck in your process, a poka yoke is more useful upstream of the constraint rather than downstream. This ensures you’re only doing good work in the constraint process step, and not wasting productive capacity at that step on bad parts.
For instance, imagine a plant with a metal stamping press that can produce 360 pieces per hour. The next step downstream, welding, can only produce 100 pieces each hour in the production process. Ideally, your poka yoke would be placed on the stamping press before parts make it to welding because you can barely make enough welded parts as it is.
The Role of Verification in Poka Yoke
Once you’ve gone through the effort of planning and designing a poka-yoke system and you’ve seen it working on day one, how do you ensure that it’s still working on day two in a lean manufacturing environment?
One common strategy here is using what’s called a red rabbit, where you run a known defective part through the machine to see if the poka yoke detects the error. Incorporating red rabbit tests into plant floor checks such as layered process audits can help verify poka yoke systems are working on an ongoing basis.
For example, a layered process audit question to verify a poka yoke might state:
Demonstrate the use of the red rabbit and verify that the machine knocks out the part as part of the quality control procedure.
Here you’re verifying not just that the poka yoke system works as expected, but also that the operator knows how to use the red rabbit.
Poka Yoke Digitization
Poka yoke systems have become increasingly digitized alongside the proliferation of IoT sensors in the manufacturing environment. Examples include:
- Machine sensors that detect when a part does not meet specifications
- Pick light systems that ensure the operator chooses the correct parts in the correct order
- Light curtains that shut down the process when a person is inside a hazardous area when equipment is running
While technology has undoubtedly opened up new avenues for poka yoke, one concept we encourage manufacturers to keep in mind is “creativity before capital”. Because the fact is, anybody can spend a ton of money on poka yoke systems, but understanding the benefits of poka-yoke in manufacturing is crucial. So, the question is, can you be creative and find inexpensive solutions that are just as effective?
One recent client had planned to spend a large amount of money to install and mount several cameras inside a machine to detect a specific quality defect. Upon deeper investigation, we determined at least three of the internal cameras could be replaced with simple sensors on a related position on the part exterior.
Poka yoke is an important strategy for preventing, detecting and mitigating defects, acting as a key safeguard against manufacturing errors and mistakes. The key is to implement them as early in the process as possible, using poka-yoke techniques to prevent waste downstream. Rather than relying on complex technology that can easily break down, manufacturers should prioritize poka yoke systems that are physical, durable and reliable, backed by ongoing verification that they are working.